Hassas dökümlerin boyutsal kararlılığını etkileyen çeşitli faktörler
Hassas dökümlerin boyutsal doğruluğunu sürekli iyileştirmek ve büyük ebatlardan kaynaklanan atık ürünleri azaltmak, yurtiçi ve yurtdışındaki hassas döküm işçileri tarafından her zaman takip edilen ana hedeflerden biri olmuştur.
1. Hassas dökümlerin boyutsal kararlılığı
1. Mum modelin boyutsal kararlılığı ve etkileyen faktörler
Çoğu durumda, dökümün boyutu dalgalandığında mum kalıbının boyutu büyük ölçüde dalgalanır ve birkaç istisna vardır. Genel olarak, mum kalıbının boyut dalgalanması, dökümün boyut dalgalanmasının %10 ila %70'ini oluşturur.
Kalıplama işlemi parametreleri, mum kalıbının boyutsal kararlılığı üzerinde belirleyici bir etkiye sahiptir. Ana faktörler aşağıdaki gibidir:
(1) Mum presleme sıcaklığı
Farklı kalıplama malzemeleri, mum presleme sıcaklığının etkisiyle farklı performanslara sahiptir. Mum bazlı kalıplama malzemeleri kullanıldığında, mum presleme sıcaklığı mum kalıbın boyutsal stabilitesinin etkisine karşı çok hassasken reçine bazlı kalıplama malzemelerinin etkisi daha az olur.
(2) Enjeksiyon basıncı
Basınç küçük olduğunda, basınç arttığında mum kalıbının büzülme oranı önemli ölçüde azalır. Bununla birlikte, basınç belirli bir dereceye kadar (≥1.6MPa) arttırıldıktan sonra, basıncın mum kalıbının boyutu üzerinde neredeyse hiçbir etkisi yoktur. Yabancı test sonuçlarının genellikle "basıncın mum kalıbının boyutuyla hiçbir ilgisi olmadığı" sonucuna varması şaşırtıcı değildir, ancak birçok yerli şirketin izlenimi tamamen aynı değildir.
(3) Akış hızı
Kalıp malzemesinin akış hızı aşağıdaki iki yolla değiştirilebilir, ancak mum kalıbının boyutu üzerindeki etki aynı değildir:
· Mum presinin akış hızı ayarını değiştirerek, bu yöntemin mum kalıbının büzülmesi üzerinde çok az etkisi vardır. Bununla birlikte, karmaşık şekilli ince duvarlı parçaların veya maçalı mum kalıpların dolgusu ve yüzey kalitesi üzerinde önemli bir etkisi vardır.
· Bu yöntem, mum enjeksiyon portunun kesit alanını değiştirerek büyük bir etkiye sahiptir, çünkü mum enjeksiyon portunun kesit alanını arttırmak sadece mum presleme sıcaklığını düşürmekle kalmaz, aynı zamanda katılaşmayı da uzatır. kalıp malzemesinin mum enjeksiyon portunda kalma süresi, böylece mum kalıbı sıkıştırması artar Büzülme derecesi ve yüzey büzülmesi azalır.
(4) Enjeksiyon süresi
Burada sözde enjeksiyon süresi, doldurma, sıkıştırma ve bakım için üç zaman periyodunu içerir. Doldurma süresi, kalıplama malzemesinin kalıplama boşluğunu doldurma süresini ifade eder; sıkıştırma, kalıplamanın doldurulmasından mum enjeksiyon memesinin kapanmasına kadar geçen süreyi ifade eder; ve tutma, mum enjeksiyon memesinin kapanmasından kalıbın çıkarılmasına kadar geçen süreyi ifade eder.
Enjeksiyon süresinin mum kalıbının büzülme hızı üzerinde önemli bir etkisi vardır. Bunun nedeni, enjeksiyon süresinin arttırılmasıyla boşluğa daha fazla kalıp malzemesinin sıkıştırılabilmesi ve mum kalıbının daha fazla sıkıştırılması ve böylece büzülme oranını düşürmesidir. Balmumu modelinin ağırlığı, uzun sıkıştırma süresi ile artar. Sıkıştırma süresi uygun olmalıdır. Sıkıştırma süresi çok uzunsa, mum enjeksiyon portundaki kalıp malzemesi tamamen katılaşmıştır ve sıkıştırma çalışmayacaktır. Şekil 4'ten ayrıca enjeksiyon süresi kısa olduğunda (15-25s), mum presleme sıcaklığının arttığı ve büzülme oranının arttığı görülebilir; ancak enjeksiyon süresi 25-35 saniyeye uzatıldığında (doldurma süresinin sabit kaldığı varsayımı altında, asıl olan sıkıştırma süresini uzatmaktır) Mum presleme sıcaklığının etkisi küçülür; enjeksiyon süresi 35 saniyeden fazla arttığında ise tam tersi bir durum oluşacaktır yani mum presleme sıcaklığı arttıkça mum kalıbı küçülme oranı düşecektir. Bu fenomen, kalıp malzemesi sıcaklığının arttırılması ve sıkıştırma süresinin uzatılmasının mum kalıbı sıkıştırma derecesinin artmasıyla aynı etkiye sahip olması olarak açıklanabilir.
(5) Kalıplama sıcaklığı ve mum presleme ekipmanı
Kalıplama sıcaklığı yüksektir, mum kalıbı yavaş soğur ve büzülme hızı artar. Bunun nedeni, mum kalıbın kalıp çıkarılmadan önce hala sıkıştırmalı kalıplamada olması ve büzülmenin sınırlı olması, ancak kalıp çıkarıldıktan sonra büzülmekte serbest hale gelmesidir. Bu nedenle, kalıp serbest bırakıldığında mum kalıbı sıcaklığı yüksekse, nihai büzülme oranı büyük olacak ve bunun tersi durumda büzülme oranı küçük olacaktır.
Aynı şekilde, mum presinin soğutma sistemi mum kalıbının boyutu üzerinde yaklaşık %0.3'lük bir etkiye sahip olabilir.
Son olarak, mum bazlı kalıp malzemeleri kullanıldığında mum pastanın katı, sıvı ve gazdan oluşan üç fazlı bir birlikte var olma sistemi olduğunu vurgulamakta fayda var. Üç faz arasındaki hacim oranı, mum kalıbının boyutu üzerinde büyük bir etkiye sahiptir. Bu üçü arasındaki orantısal ilişki fiili üretimde kontrol edilemez, bu da mum bazlı kalıplama malzemeleri kullanan mumlu kalıpların zayıf boyutsal stabilitesinin önemli bir nedenidir.
2. Kabuk malzemesinin ve kabuk yapım sürecinin dökümlerin boyutsal kararlılığı üzerindeki etkisi
Kalıp kabuğunun dökümün boyutu üzerindeki etkisi, esas olarak, kalıp kabuğunun ateşleme sırasında termal genleşmesi ve termal deformasyonu (yüksek sıcaklık sürünmesi) ve kalıp kabuğunun soğuma büzülmesi üzerindeki kısıtlamasından (tıkanması) kaynaklanır. döküm.
(1) Kabuğun termal genleşmesi
Esas olarak kabuk malzemesine bağlıdır. Farklı refrakter malzemelerin farklı genleşme oranları vardır. Yaygın olarak kullanılan refrakterler arasında, erimiş silika en düşük genleşme hızına sahiptir, bunu alüminyum silikat takip eder ve silika en büyük ve düzensizdir. Testten sonra, alüminyum silikat kabuğun oda sıcaklığından 1000 ℃'ye kadar ısıtılabileceği, kabuğun yaklaşık %0.25 genleşme üretebileceği ve bu da döküm boyutunun genel büzülmesinin küçük bir bölümünü oluşturduğu belirlendi. Bu nedenle, bu tür refrakter malzemeler kullanılırsa, kabuk Daha iyi boyutsal stabiliteye sahiptir, örneğin erimiş silika gibi şüphesiz daha iyi olacaktır. Bununla birlikte, silika kullanılırsa, kabuğun boyutu büyük ölçüde dalgalanır.
(2) Termal deformasyon (yüksek sıcaklık sürünmesi)
Örneğin, bağlayıcı olarak su camı kullanan bir kabuk, 1000°C'nin üzerindeki yüksek sıcaklıklarda, silika sol ve etil silikat kabuklarınkinden önemli ölçüde daha büyük bir sürünme derecesine sahiptir. Kaynaşmış korindonun kendisinin yüksek refrakterliğe sahip olmasına rağmen, sodyum oksit gibi safsızlıkların varlığı nedeniyle, 1000 ℃'den yüksek kabuk ateşleme sıcaklığı da sürünmeye neden olabilir ve bu da zayıf boyutsal stabiliteye neden olabilir.
(3) Kalıp kabuğunun dökümün büzülmesi üzerindeki kısıtlaması—kalıp kabuğunun geri çekilmesi ve çökebilirliği Bu aynı zamanda esas olarak kalıp kabuğunun malzemesine de bağlıdır.
Özetle, refrakter malzemeler, kabuğun dökümün boyut dalgalanması üzerindeki etkisinde önemli bir rol oynar, ancak bağlayıcının rolü göz ardı edilemez. Buna karşılık, kabuk yapma sürecinin etkisi küçüktür.
3. Dökümlerin eşit olmayan soğumasının neden olduğu stresin boyutsal kararlılık üzerindeki etkisi
Dökümün her bir parçasının (yolluk sistemi dahil) soğuma hızı farklıdır, bu da termal stres oluşturan ve dökümü deforme ederek boyutsal kararlılığı etkiler. Bu genellikle gerçek üretimde karşılaşılan bir durumdur. Dökümlerin soğuma hızını azaltmak ve yolluk kombinasyonunu iyileştirmek etkili önleyici tedbirlerdir.
2. Doğruluk-kalıp büzülme oranını iyileştirmenin anahtarı doğru şekilde atanır
Yukarıda bahsedilen "boyutsal kararlılık", "boyutsal doğruluk" ve "hassasiyet (hassasiyet)"den farklıdır. Boyutsal kararlılık (yani kesinlik), boyutsal dalgalanma veya dağılım derecesini yansıtan boyutsal tutarlılık ile eş anlamlıdır ve genellikle standart sapma σ ile ölçülür. Boyutsal kararsızlığın ana nedeni, rastgele bir hata olan gevşek süreç kontrolüdür. Doğruluk, birçok ölçülen değerin aritmetik ortalamasının, döküm üzerinde belirli bir boyut için nominal boyuttan, yani ortalama sapmanın boyutundan sapma derecesini ifade eder. Hassas döküm için, zayıf boyutsal doğruluğun ana nedeni, genellikle kalıbın tekrar tekrar onarılmasıyla ayarlanan sistematik bir hata olan profil tasarımı sırasında büzülme oranının yanlış atanmasıdır. Boyutsal doğruluk (hassasiyet) yukarıdaki ikisinin birleşimidir. Bu nedenle, dökümlerin boyutsal doğruluğunu iyileştirmek ve ürün boyutu toleransları sorununu çözmek için, boyutsal dalgalanmaları azaltmak için sadece süreç sıkı bir şekilde kontrol edilmemeli, aynı zamanda profil tasarlanırken dökümün her boyutunun büzülme oranı da doğru şekilde atanmalıdır. .
Hassas dökümlerin nihai toplam büzülmesinin mum kalıbı, alaşım büzülmesi ve az miktarda kabuk genişlemesinin bir kombinasyonu olduğu iyi bilinmektedir. Kabuk yaklaşık %0.25 oranında şişer ve etkisi sınırlıdır. Alaşımın doğrusal büzülme oranı genellikle mum kalıbınınkinden daha büyük olmasına rağmen, mum presleme işleminin neden olduğu boyutsal dalgalanma daha büyük bir etkiye sahiptir. Kalıp onarım maliyetini azaltmak ve döküm boyutundaki dalgalanmayı azaltmak için mum kalıbının büzülme oranını kontrol etmek çok önemlidir.
1. Balmumu kalıp büzülmesi
Mum kalıbının büzülmesi, mum kalıbının boyutu tamamen stabilize edildikten sonra ölçülmelidir. Bunun nedeni, mum kalıbın büzülmesinin kalıp çıkarıldıktan sonra tamamen durmamasıdır. Mum kalıbın boyutu bazen kalıp çıkarıldıktan sadece birkaç gün sonra sabitlenir. Bununla birlikte, kalıp malzemesinin büzülmesinin çoğu, temel olarak kalıp çıkarıldıktan sonra bir ila birkaç saat içinde tamamlanır. Balmumu kalıp büzülme oranı esas olarak aşağıdaki etkileyen faktörlere sahiptir:
(1) Kalıp malzemesinin türü;
(2) Balmumu modelinin kesit boyutu;
Mum kalıbının kesit boyutunun büzülme oranı üzerinde önemli bir etkiye sahip olduğunu vurgulamakta fayda var. Örneğin, farklı kalınlıklarda mum kalıpları preslerken tipik bir doldurulmamış kalıp malzemesinin büzülme oranı. Mum kalıbının kesitinin kalınlığı genellikle 13 mm'yi geçmemelidir. Kalınlık 13 mm'den fazla olduğunda, özellikle dolgu olmayan kalıp malzemeleri için önemli olan büzülmeyi azaltma amacına ulaşmak için soğuk mum blokları veya metal göbekler kullanılarak duvar kalınlığı azaltılabilir.
Not: 1. Suda çözünür kalıp malzemesinin büzülme oranı yaklaşık %0.25'tir;
2. Çözünebilir çekirdekler, seramik çekirdekler veya kuvars cam tüpler kullanıldığında, çekirdek ile temas halinde olan mum kalıbında doğrusal bir büzülme olmaz;
(3) Çekirdek türleri
Mum kalıbının boşluk boyutu, hiç şüphesiz, çekirdeğin şekli ile tutarlıdır. Bu nedenle maça kullanımı, mum kalıbının boşluğunun boyutsal doğruluğunu geliştirmenin bir yolu haline geldi.
2. Alaşım büzülmesi
Alaşım büzülmesi esas olarak aşağıdaki faktörlere bağlıdır:
· Döküm alaşım tipi ve kimyasal bileşimi;
· Döküm geometrisi (kısıtlama durumu ve kesit boyutu dahil);
· Döküm sıcaklığı, kabuk sıcaklığı, döküm soğutma hızı vb. gibi döküm parametreleri;
· Seramik çekirdekler, kuvars cam tüpler vb.
Dökme sıcaklığı, kabuk sıcaklığı, döküm soğutma hızı ve diğer proses parametreleri genellikle üretim prosesi sırasında standart proses kartları tarafından sıkı bir şekilde kontrol edildiğinden, bunun neden olduğu boyut dalgalanmaları farklı üretim partileri arasında büyük değildir. Dökme sıcaklığı, proses spesifikasyonunun gerektirdiği aralığı aşsa bile, döküm boyutunun dalgalanması genellikle büyük değildir. Mum kalıbına benzer şekilde, dökümün kesit boyutu ve kalıp kabuğunun kısıtlamaları, alaşımın büzülmesini etkileyen ana faktörlerdir. Deneyimler, tamamen sınırlandırılmış boyutun büzülme oranının, serbest büzülme oranının %85 ila %89'u olduğunu göstermektedir; yarı kısıtlı boyut %94 ila %95'tir.
3. Ölçüm için ilk numune partisinin minimum sayısı
Yukarıda listelenen büzülme oranı, gerçek büzülme oranı değil, geçmiş deneyimlere dayanan ampirik verilerdir. Kalıpları bu verilere göre tasarlayın ve üretin, onarım kaçınılmazdır. Onarımların doğruluğunu ve başarı oranını artırmak ve onarım sayısını azaltmak için önemli bir bağlantı, yeterli sayıda deneme döküm numunesinin boyutunu dikkatlice kontrol etmektir. Ürettiğimiz dökümlerin boyutları tam olarak aynı olamayacağından, yalnızca ölçülen numune sayısı yeterince büyük olduğunda, elde edilen ortalama değer gerçek aritmetik ortalamaya yakın olabilir. Buradan, minimum ölçüm numunesi sayısının, üretim sürecinin ürün boyutu tutarlılığını kontrol etme (Process Capability) işlem kapasitesi ile doğrudan ilişkili olduğunu görmek zor değildir. Dökümler tamamen aynı boyutta ise, test edilmesi için yalnızca bir numune gerekir; Tersine, döküm boyutu büyük ölçüde dalgalanıyorsa,
Daha doğru büzülme verileri elde etmek için çok sayıda numuneyi ölçmek gerekir. Daha önce belirtildiği gibi, üretim sürecinin boyutu kontrol etme yeteneği, bu süreç tarafından üretilen döküm boyutunun 6σ'si ile temsil edilebilir. Çoğu yatırım dökümhanesinin mevcut teknolojik seviyesinden, Hp çoğunlukla 0.5'in üzerindedir, bu nedenle ilk ölçüm numunesi partisi genellikle en az 11 numune gerektirir.
üç. Ölçüm sistemi analizi
Ürün boyutu problemlerini analiz ederken ve çözerken kullanılan ölçüm sisteminin doğruluğuna ve güvenilirliğine dikkat etmeliyiz. Ölçüm aletlerinin ve ekipmanlarının kendilerinin sık sık kalibrasyonlarına ek olarak, ölçüm hatalarını en aza indirmek de önemlidir. Ölçüm sistemi (operatör ve çalıştırma yöntemi dahil) büyük bir hataya sahipse, yalnızca reddedilenler nitelikli ürün olarak değerlendirilemez, aynı zamanda birçok nitelikli ürün de reddedilmiş olarak değerlendirilebilir, her ikisi de büyük kazalara veya gereksiz ekonomik duruma neden olabilir. kayıplar. Bir ölçüm sisteminin belirli bir ölçüm görevi için uygun olup olmadığını belirlemenin en kolay yolu, tekrarlanabilirlik ve tekrarlanabilirlik yeterlilik testleri yapmaktır. Sözde tekrarlanabilirlik, aynı denetçinin aynı parçayı incelemek ve sonuçların tutarlılığını elde etmek için aynı aleti (veya ekipmanı) ve yöntemi kullanması anlamına gelir. Tekrarlanabilirlik, aynı parçayı kontrol etmek için farklı enstrümanlar kullanan farklı operatörler tarafından elde edilen sonuçların tutarlılığını ifade eder. Amerikan Otomotiv Endüstrisi Eylem Grubu (Otomotiv Endüstrisi Eylem Grubu), ölçülen döküm boyutu dalgalanmalarının standart sapması içindeki tekrarlanabilirlik ve yeniden üretilebilirlik Ar-Ge'sinin entegre standart sapması yüzdesinin, ölçüm sisteminin standart olarak aşağıdakileri karşılaması için ≤%30 olduğunu şart koşar. gereksinimler [5]. Bazı büyük boyutlu ve karmaşık şekilli dökümlerin ölçümünde, tüm ölçüm sistemleri bu gereksinimi karşılayamaz. Kalıpları ölçerken izin verilen ölçüm hatası, genellikle 1/3 olmak üzere daha küçük olmalıdır.
dört. Kalıp yapısı ve işleme seviyesi
Kalıp yapısının ve işleme kalitesinin mum kalıbının boyutu ve geometrisi üzerinde önemli bir etkiye sahip olduğu iyi bilinmektedir. Örneğin, konumlandırma ve sıkıştırma mekanizmasının doğru ve güvenilir olup olmadığı, hareketli parçaların (hareketli bloklar, cıvatalar vb. gibi) eşleşen açıklığının uygun olup olmadığı, çizim yönteminin dökümlerin boyutsal doğruluğunu sağlamak için faydalı olup olmadığı. , vb. Söylemeye gerek yok, önemli sayıda yerli hassas döküm tesisi için, kalıp tasarımı ve üretim seviyesinin hala acilen iyileştirilmesi gerekiyor.
Beşler. sonuç olarak
Yukarıdaki analizden, hassas dökümlerin boyutsal doğruluğunu iyileştirmenin, hassas döküm üretim sürecinin tüm yönlerini içeren sistematik bir proje olduğunu görmek zor değildir. Ana noktalar aşağıdaki gibi özetlenebilir:
1) Kalıplama süreci parametrelerini, özellikle de dökümün boyutu üzerinde önemli bir etkisi olan parametreleri kesinlikle kontrol edin.
2) Uygun kabuk malzemesini seçin.
3) Büzülme atamasının doğruluğunu artırmak için büzülme ile ilgili verileri istatistiksel ilkelere uygun doğru bir yöntemle toplayın, sayın ve analiz edin.
4) Tekrarlanabilirlik ve tekrar üretilebilirlik hatalarının belirtilen gereksinimleri karşıladığından emin olmak için ölçüm sistemini (ekipman, muayene personeli ve teknoloji dahil) sık sık izleyin.
5) Kalıp tasarım ve imalat düzeyini sürekli iyileştirmek.
6) Döküm düzeltme ve stabilizasyon ısıl işlemi gibi önlemler birçok durumda hala vazgeçilmezdir.
Lütfen yeniden basım için bu makalenin kaynağını ve adresini saklayın: Hassas dökümlerin boyutsal kararlılığını etkileyen çeşitli faktörler
Minhe Basınçlı Döküm Şirketi kaliteli ve yüksek performanslı Döküm Parçaları üretmeye ve sağlamaya adamıştır (metal döküm parça yelpazesi esas olarak şunları içerir: İnce Duvarlı Döküm,Sıcak Kamara Basınçlı Döküm,Soğuk Oda Döküm), Yuvarlak Servis (Döküm Servisi,Cnc İşleme,Kalıp yapımı,Yüzey İşleme).Herhangi bir özel Alüminyum döküm, magnezyum veya Zamak/çinko döküm ve diğer döküm gereksinimleri bizimle iletişime geçebilirsiniz.
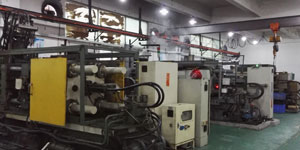
ISO9001 ve TS 16949 kontrolünde, tüm işlemler yüzlerce gelişmiş basınçlı döküm makinesi, 5 eksenli makine ve blasterlerden Ultra Sonic yıkama makinelerine kadar diğer tesisler aracılığıyla gerçekleştirilir. Müşterinin tasarımını gerçeğe dönüştürmek için deneyimli mühendisler, operatörler ve müfettişlerden oluşan ekip.
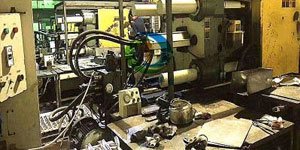
Dökümlerin sözleşmeli üreticisi. Yetenekler, 0.15 lbs'den başlayan soğuk oda alüminyum döküm parçaları içerir. 6 lbs'ye kadar, hızlı değişim kurulumu ve işleme. Katma değerli hizmetler arasında polisaj, titreşim, çapak alma, kumlama, boyama, kaplama, kaplama, montaj ve kalıplama yer alır. Çalışılan malzemeler arasında 360, 380, 383 ve 413 gibi alaşımlar bulunur.
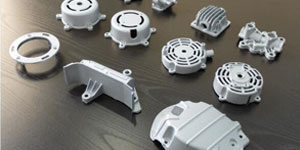
Çinko pres döküm tasarım yardımı/eşzamanlı mühendislik hizmetleri. Hassas çinko dökümlerin özel üreticisi. Minyatür dökümler, yüksek basınçlı dökümler, çok kızaklı kalıp dökümleri, geleneksel kalıp dökümleri, birim kalıp ve bağımsız kalıp dökümleri ve boşluklu sızdırmaz dökümler üretilebilir. Dökümler, +/- 24 inç toleransta 0.0005 inç'e kadar uzunluk ve genişliklerde üretilebilir.
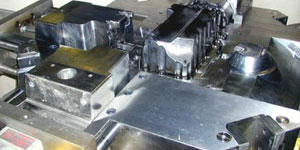
ISO 9001: 2015 sertifikalı döküm magnezyum üreticisi, Yetenekler arasında 200 ton sıcak odaya ve 3000 ton soğuk odaya kadar yüksek basınçlı magnezyum kalıp dökümü, takım tasarımı, cilalama, kalıplama, işleme, toz ve sıvı boyama, CMM özelliklerine sahip tam kalite güvencesi bulunur , montaj, paketleme ve teslimat.
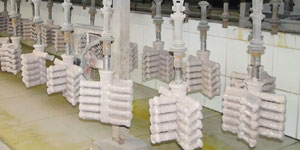
ITAF16949 sertifikalı. Ek Döküm Hizmeti Dahil yatırım dökümleri,kum dökümü,Yerçekimi Döküm, Kayıp Köpük Döküm,Savurma döküm,Vakumlu Döküm,Kalıcı Kalıp Döküm,.Yetenekler arasında EDI, mühendislik yardımı, katı modelleme ve ikincil işleme yer alır.
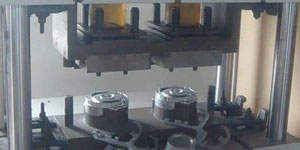
Döküm Endüstrileri Arabalar, Bisikletler, Uçaklar, Müzik aletleri, Deniz Araçları, Optik cihazlar, Sensörler, Modeller, Elektronik cihazlar, Muhafazalar, Saatler, Makineler, Motorlar, Mobilya, Mücevher, Jigler, Telekom, Aydınlatma, Tıbbi cihazlar, Fotoğraf cihazları, Robotlar, Heykeller, Ses ekipmanları, Spor ekipmanları, Aletler, Oyuncaklar ve daha fazlası.
Bundan sonra ne yapmanıza yardımcı olabiliriz?
∇ Ana Sayfaya Git Çin Döküm
→Döküm Parçaları-Ne yaptığımızı öğren.
→ Hakkında İlgili İpuçları Pres Döküm Hizmetleri
By Minghe Döküm Üreticisi |Kategoriler: Faydalı Makaleler |Malzeme Etiketler: Alüminyum Döküm, Çinko Döküm, Magnezyum Döküm, Titanyum Döküm, Paslanmaz Çelik Döküm, Pirinç Döküm,Bronz Döküm,Döküm Videosu,Tarihçe,Alüminyum Döküm |Yorumlar Kapalı