Toz Metalurjisi (P/M) Parçalarının Kesim İşleme
Otomotiv güç sistemleri için parça üretmek için toz metalurjisi (P/M) işleminin kullanımı büyümeye devam ediyor. P/M prosesi ile üretilen parçaların birçok önemli ve benzersiz avantajı vardır. Bu kısımlarda kasıtlı olarak bırakılan kalıntı gözenekli yapı, kendi kendini yağlama ve ses yalıtımı için iyidir. Geleneksel döküm işlemi ile üretilmesi zor veya imkansız olan karmaşık alaşımlar, P/M teknolojisi kullanılarak üretilebilmektedir. Bu teknolojiyle üretilen parçaların genellikle çok az işleme kapasitesi vardır veya hiç yoktur, bu da onları daha ucuza ve malzemede daha az atık haline getirir. Ne yazık ki, bu özelliklerin çekiciliğinin arkasında P/M parçaların işlenmesi zordur.
P/M endüstrisinin orijinal amaçlarından biri tüm işlemeyi ortadan kaldırmak olsa da, bu hedefe henüz ulaşılamamıştır. Çoğu parça yalnızca "son şekle yakın" olabilir ve yine de biraz bitirmeye ihtiyaç duyar.
Bununla birlikte, döküm ve dövme ile karşılaştırıldığında, P / M parçalarından çıkarılması gereken az miktarda malzeme tipik bir aşınmaya dayanıklı malzemedir.
Gözenekli yapı, p/M parçaların geniş bir kullanım alanına sahip olmasını sağlayan özelliklerden biridir ancak gözenekli yapı nedeniyle takım ömrü de zarar görecektir. Gözenekli yapı yağı ve sesi depolayabilir, ancak mikro aralıklı kesmeye de yol açar. Delikten katı parçacıklara ileri geri hareket ederken, takım ucu sürekli olarak darbe alır, bu da çok küçük yorulma kırılma deformasyonuna ve kesme kenarı boyunca ince kenar çökmesine neden olabilir. Daha da kötüsü, parçacıklar genellikle çok serttir. Ölçülen malzemenin makro sertliği 20 ile 35 derece arasında olsa bile bileşenin partikül boyutu 60 derece kadar yüksektir. Bu sert parçacıklar şiddetli ve hızlı kenar aşınmasına neden olur. Birçok p/M parçası ısıl işlem görebilir ve ısıl işlemden sonra malzemenin sertliği ve mukavemeti daha yüksektir. Son olarak sinterleme ve ısıl işlem teknolojisi ve kullanılan gazlar nedeniyle malzemenin yüzeyi sert ve aşınmaya dayanıklı oksitler ve/veya karbürler içerecektir.
P / M parçalarının performansı
İşlenebilirlik dahil olmak üzere P / M parçaların özelliklerinin çoğu, yalnızca alaşımın kimyasal bileşimi ile değil, aynı zamanda gözenekli yapının gözeneklilik seviyesi ile de ilgilidir. Birçok yapısal parçanın gözenekliliği %15 ~ %20'ye kadardır. Filtrasyon cihazı olarak kullanılan parçaların gözenekliliği %50 kadar yüksek olabilir. Serinin diğer ucunda, dövme veya kalça parçaların gözenekliliği sadece %1 veya daha azdır. Bu malzemeler, daha yüksek mukavemet seviyelerine ulaşabildikleri için otomotiv ve uçak uygulamalarında özellikle önem kazanmaktadır.
P/M alaşımının çekme mukavemeti, tokluğu ve sünekliği yoğunluğun artmasıyla artacaktır ve gözeneklilik takım ucuna zararlı olduğu için işlenebilirlik de iyileştirilebilir.
Gözeneklilik seviyesinin artması, parçaların ses yalıtım performansını iyileştirebilir. Standart parçalardaki sönüm salınımı, takım tezgahları, klima üfleme boruları ve pnömatik aletler için çok önemli olan P/M parçalarında önemli ölçüde azaltılmıştır. Kendinden yağlamalı dişliler için de yüksek gözeneklilik gereklidir.
İşlemedeki zorluklar
P / M endüstrisinin sürekli gelişiminin hedeflerinden biri işlemeyi ortadan kaldırmak olsa da ve P / M sürecinin ana cazibe merkezlerinden biri sadece az miktarda işlemeye ihtiyaç duyulmasına rağmen, birçok parçanın elde edilmesi için hala son işlemeye ihtiyacı vardır. daha yüksek doğruluk veya daha iyi yüzey kalitesi. Ne yazık ki, bu parçaların işlenmesi son derece zordur. Karşılaşılan sorunların çoğu poroziteden kaynaklanmaktadır. Gözeneklilik, kesme kenarının mikro yorulmasına yol açar. Keskin uçlu sürekli içeri ve dışarı kesiyor. Parçacıklar ve delikler arasında geçer. Tekrarlanan küçük darbeler kesici kenarda küçük çatlaklara yol açar.
Bu yorulma çatlakları kesici kenar çökene kadar büyür. Bu tür mikro ufalanma kenarı genellikle çok küçüktür ve genellikle normal aşındırıcı aşınma gösterir.
Gözeneklilik ayrıca P/M parçaların ısıl iletkenliğini azaltır, bu da kesici kenarda yüksek sıcaklık ile sonuçlanır ve krater aşınmasına ve deformasyona neden olur. Dahili olarak bağlı gözenekli yapı, kesme sıvısının kesme alanından boşaltılması için bir yol sağlar. Bu, özellikle delmede sıcak çatlaklara veya deformasyona neden olabilir.
İç gözenekli yapının neden olduğu yüzey alanı artışı da ısıl işlem sırasında oksidasyona ve/veya karbonlaşmaya neden olur. Daha önce belirtildiği gibi, bu oksitler ve karbürler serttir ve aşınmaya dayanıklıdır.
Gözenekli yapı, son derece önemli olan parça sertlik okumasının başarısızlığını da verir. Bir P / M parçasının makro sertliği kasıtlı olarak ölçüldüğünde, delik sertliği faktörünü içerir. Gözenekli yapı, yapının çökmesine neden olur ve nispeten yumuşak kısımlarda yanlış izlenim verir. Parçacıklar çok daha serttir. Yukarıda açıklandığı gibi, fark dramatiktir.
PM parçalarında kapanımların varlığı da dezavantajlıdır. Talaşlı imalat sırasında bu parçacıklar yüzeyden yukarı çekilecek ve parçanın takımın önüne sürtüldüğünde yüzeyinde çizik veya çizik oluşacaktır. Bu kapanımlar genellikle büyüktür ve parçanın yüzeyinde görünür delikler bırakır.
Karbon içeriğinin farkı, işlenebilirliğin tutarsızlığına yol açar. Örneğin, fc0208 alaşımının karbon içeriği %0.6 ila %0.9 arasında değişmektedir. %0.9 karbon içeriğine sahip bir malzeme partisi nispeten zordur ve bu da takım ömrünün kısa olmasına neden olur. %0.6 karbon içeriğine sahip diğer malzeme grubu, mükemmel takım ömrüne sahiptir. Her iki alaşım da izin verilen aralıktadır.
Nihai işleme problemi, P/M parçası üzerinde meydana gelen kesme tipi ile ilgilidir. Parça nihai şekle yakın olduğu için kesme derinliği genellikle çok sığdır. Bu, serbest bir kesme kenarı gerektirir. Kesici kenarda talaş birikmesi genellikle mikro talaş oluşumuna yol açar.
Işleme teknolojisi
Bu sorunların üstesinden gelmek için çeşitli teknolojiler (sektöre özgü) uygulanmaktadır. Yüzey gözenekli yapısı genellikle sızma ile kapatılır. Ek serbest kesim genellikle gereklidir. Son zamanlarda, ısıl işlem sırasında toz temizliğini artırmak ve oksitleri ve karbürleri azaltmak için tasarlanmış gelişmiş toz üretim teknikleri kullanılmıştır.
Kapalı yüzeyli gözenekli yapı, metal (genellikle bakır) veya polimer infiltrasyonu ile sağlanır. Sızıntının bir yağlayıcı görevi gördüğü tahmin edilmektedir. Deneysel verilerin çoğu, gerçek avantajın yüzeydeki gözenekli yapının kapatılmasında ve böylece kesici kenarın mikro yorgunluğunun önlenmesinde yattığını göstermektedir. Tırlamanın azaltılması takım ömrünü ve yüzey kalitesini iyileştirir. Sızdırmanın en dramatik kullanımı, gözenekli yapı kapatıldığında takım ömründe %200'lük bir artış gösterir.
MNS, s, MoS2, MgSiO3 ve BN gibi katkı maddelerinin takım ömrünü arttırdığı bilinmektedir. Bu katkı maddeleri, talaşların iş parçasından ayrılmasını kolaylaştırarak, talaşları kırarak, talaş oluşumunu önleyerek ve kesici kenarı yağlayarak işlenebilirliği artırır. Katkı maddelerinin miktarını artırmak işlenebilirliği iyileştirebilir, ancak mukavemeti ve tokluğu azaltabilir.
Sinterleme ve ısıl işlem fırın gazını kontrol etmek için toz atomizasyon teknolojisi, inklüzyonların ve yüzey oksit karbürlerinin oluşumunu en aza indiren temiz toz ve parçalar üretmeyi mümkün kılar.
Takım malzemesi
P / M endüstrisinde en yaygın olarak kullanılan takımlar, iyi yüzey kalitesi koşulu altında aşınmaya dayanıklı, kenar çatlamaya dayanıklı ve talaşsız olan malzemelerdir. Bu özellikler, özellikle P / M parçaları için herhangi bir işleme işlemi için kullanışlıdır. Bu kategoriye dahil edilen alet malzemeleri, kübik bor nitrür (CBN) aletler, kaplanmamış ve kaplanmış sermetler ve iyileştirilmiş kaplanmış sinterlenmiş sinterlenmiş karbürlerdir.
CBN takımları, yüksek sertlikleri ve aşınma direnci nedeniyle çekicidir. Bu alet, Rockwell sertliği 45 ve üzeri olan çelik ve dökme demirlerin işlenmesinde uzun yıllardır kullanılmaktadır. Ancak, P/M alaşımının benzersiz özellikleri ve mikrosertlik ile makrosertlik arasındaki önemli fark nedeniyle, CBN takımları Rockwell sertliği 25 olan P/M parçalar için kullanılabilir. Anahtar parametre parçacıkların sertliğidir. Parçacıkların sertliği Rockwell 50 dereceyi aştığında, makro sertlik değerinden bağımsız olarak CBN takımları kullanılabilir. Bu araçların bariz sınırlaması, dayanıklılıklarının olmamasıdır. Aralıklı kesme veya yüksek gözeneklilik durumunda, negatif pah kırma ve ağır honlama dahil kenar takviyesi gereklidir. Honlanmış keskin uçlu ile basit hafif kesim yapılabilir.
Etkili olan birkaç CBN materyali vardır. En iyi tokluğa sahip malzeme esas olarak tüm CBN'den oluşur. Mükemmel tokluğa sahiptirler, bu nedenle kaba işleme için kullanılabilirler. Sınırlamaları genellikle yüzey kalitesi ile ilgilidir. Büyük ölçüde aleti oluşturan bireysel CBN parçacıkları tarafından belirlenir. Parçacıklar kesici kenardan düştüğünde iş parçası malzemesinin yüzeyini etkileyecektir. Ancak, ince parçacık aracının bir parçacıktan düşmesi o kadar ciddi değildir.
Genellikle kullanılan CBN malzemesi, yüksek CBN içeriğine ve orta parçacık boyutuna sahiptir. CBN bitirme bıçağı ince tanelidir ve CBN içeriği düşüktür. Hafif kesme ve yüzey kalitesi gerektiğinde veya işlenmekte olan alaşım özellikle sert olduğunda en etkilidirler.
Birçok kesme uygulamasında takım ömrü malzeme türünden bağımsızdır. Başka bir deyişle, herhangi bir CBN malzemesi benzer takım ömrüne ulaşabilir. Bu durumlarda, malzeme seçimi esas olarak her bir kesici kenarın en düşük maliyetine dayalıdır. Bir yuvarlak bıçak, bütün bir CBN üst yüzeyine sahiptir ve dört işlemeli CBN bıçağından daha ucuz olan dört veya daha fazla kesme kenarı sağlayabilir.
P/M parçaların sertliği Rockwell 35 dereceden düşük olduğunda ve partiküllerin sertliği aralık içinde olduğunda sermet genellikle seçeneklerden biridir. Sermetler çok serttir, talaş oluşumunu etkili bir şekilde önleyebilir ve yüksek hıza dayanabilir. Ek olarak, sermetler her zaman çelik ve paslanmaz çeliğin yüksek hızlı ve finiş işlemesi için kullanıldığından, genellikle şekillendirilmiş parçalara yakın ideal geometrik oluklara sahiptirler.
Günümüzün sermetleri, 11'e kadar alaşım elementi ile metalurjide karmaşıktır. Genellikle TiCN partiküllerinden ve Ni Mo yapıştırıcıdan sinterlenirler. TiCN, sermetlerin başarılı kullanımı için önemli olan sertlik, talaş oluşumu direnci ve kimyasal stabilite sağlar. Ek olarak, bu aletler genellikle yüksek bir yapışkan içeriğine sahiptir, bu da iyi tokluğa sahip oldukları anlamına gelir. Tek kelimeyle, P / M alaşımını etkili bir şekilde işlemenin tüm özelliklerine sahiptirler. Birkaç çeşit sermet etkilidir, tıpkı tungsten karbür sinterlenmiş sinterlenmiş karbür gibi, bağlayıcı içeriği ne kadar yüksek olursa, tokluk o kadar iyi olur.
Bilinen nispeten yeni bir gelişme, orta sıcaklıkta kimyasal buhar birikiminin (mtcvd) aynı zamanda P/M endüstrisi için bir avantaj sağlamasıdır. Mtcvd, geleneksel kimyasal buhar birikiminin (CVD) tüm aşınma direncini ve krater aşınma direncini korur, ancak aynı zamanda tokluğu nesnel olarak iyileştirir. Tokluğun artması esas olarak çatlakların azalmasından kaynaklanmaktadır. Kaplama, yüksek sıcaklıkta biriktirilir ve daha sonra fırında soğutulur. Tutarsız termal genleşme nedeniyle alet oda sıcaklığına ulaştığında kaplama çatlaklar içerir. Düz camdaki çiziklere benzer şekilde, bu çatlaklar kesici kenarın gücünü azaltır. mtcvd'nin daha düşük birikme sıcaklığı, daha düşük çatlak frekansına ve kesme kenarının daha iyi tokluğuna yol açar.
CVD kaplama ve mtcvd kaplamanın alt tabakası aynı özelliklere ve kenar kaplamaya sahip olduğunda, tokluklarının farkı gösterilebilir. Kenar tokluğunun gerekli olduğu uygulamalarda kullanıldığında mtcvd kaplamanın performansı CVD kaplamadan daha iyidir. Analiz yoluyla, gözenekli yapıya sahip P / M parçaları işlerken kenar tokluğu önemlidir. Mtcvd kaplama, CVD kaplamadan daha iyidir.
Fiziksel buhar biriktirme (PVD) kaplama, mtcvd veya CVD kaplamadan daha incedir ve aşınmaya daha az dayanıklıdır. Bununla birlikte, PVD kaplama, uygulamada önemli etkilere dayanabilir. PVD kaplama, kesme aşındırıcı aşınma olduğunda etkilidir, CBN ve sermetler çok kırılgandır ve mükemmel yüzey kalitesi gerektirir.
Örneğin, C-2 sinterlenmiş karbürün kesici kenarı fc0205'te 180 m/dak hat hızında ve 0.15 mm/devir besleme hızında işlenebilir. 20 parça işlendikten sonra talaş oluşumu mikro çökmeye neden olabilir. PVD titanyum nitrür (TIN) kaplama kullanıldığında talaş oluşumu kısıtlanır ve takım ömrü uzar. Bu test için kalay kaplama kullanıldığında, P/M parçaların abrasiv aşınma özelliklerinin TiCN kaplama ile daha etkili olması beklenir. TiCN, kalay ile hemen hemen aynı talaş birikimi direncine sahiptir, ancak kalaydan daha sert ve aşınmaya karşı daha dirençlidir.
Gözenekli yapı önemlidir ve fc0208 alaşımının işlenebilirliğini etkiler. Gözenekli yapı ve özellikler değiştiğinde, farklı alet malzemeleri karşılık gelen avantajlar sağlar. Yoğunluk düşük olduğunda (6.4g/cm3), makrosertlik düşüktür. Bu durumda mtcvd kaplamalı semente karbür en iyi takım ömrünü sağlar. Kesici kenarın mikro yorulması çok önemlidir ve kenar tokluğu çok önemlidir. Bu durumda, iyi bir tokluk sermet bıçağı maksimum takım ömrü sağlar.
Aynı alaşımı 6.8g/cm3 yoğunluğa sahip olarak üretirken, aşındırıcı aşınma kenar çatlamasından daha önemli hale gelir. Bu durumda mtcvd kaplama en iyi takım ömrünü sağlar. PVD kaplı semente karbür, iki tür aşırı sert parçayı test etmek için kullanılır ve kesme kenarına dokunduğunda kırılır.
Hız arttığında (doğrusal hız dakikada 300 metreden fazladır), sermetler ve hatta kaplanmış sermetler krater aşınmasına neden olur. Kaplamalı semente karbür, özellikle kaplamalı semente karbürün kesme kenarı tokluğu iyi olduğunda daha uygundur. Mtcvd kaplama, özellikle kobalt bakımından zengin alana sahip semente karbür için etkilidir.
Sermetler en çok tornalama ve delme işlemlerinde kullanılır. PVD kaplamalı semente karbürler, diş işleme için idealdir çünkü daha düşük hızlar ve birikmeye daha fazla dikkat edilmesi beklenebilir.
Lütfen yeniden basım için bu makalenin kaynağını ve adresini saklayın:Toz Metalurjisi (P/M) Parçalarının Kesim İşleme
Minghe Döküm Şirketi, kaliteli ve yüksek performanslı Döküm Parçaları üretmeye ve sağlamaya kendini adamıştır (metal döküm parça yelpazesi esas olarak şunları içerir: İnce Duvarlı Döküm,Sıcak Kamara Basınçlı Döküm,Soğuk Oda Döküm), Yuvarlak Servis (Döküm Servisi,Cnc İşleme,Kalıp yapımı,Yüzey İşleme).Herhangi bir özel Alüminyum döküm, magnezyum veya Zamak/çinko döküm ve diğer döküm gereksinimleri bizimle iletişime geçebilirsiniz.
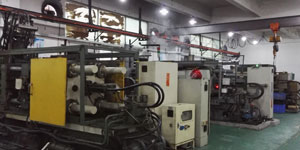
ISO9001 ve TS 16949 kontrolünde, tüm işlemler yüzlerce gelişmiş basınçlı döküm makinesi, 5 eksenli makine ve blasterlerden Ultra Sonic yıkama makinelerine kadar diğer tesisler aracılığıyla gerçekleştirilir. Müşterinin tasarımını gerçeğe dönüştürmek için deneyimli mühendisler, operatörler ve müfettişlerden oluşan ekip.
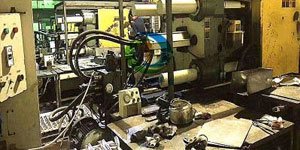
Dökümlerin sözleşmeli üreticisi. Yetenekler, 0.15 lbs'den başlayan soğuk oda alüminyum döküm parçaları içerir. 6 lbs'ye kadar, hızlı değişim kurulumu ve işleme. Katma değerli hizmetler arasında polisaj, titreşim, çapak alma, kumlama, boyama, kaplama, kaplama, montaj ve kalıplama yer alır. Çalışılan malzemeler arasında 360, 380, 383 ve 413 gibi alaşımlar bulunur.
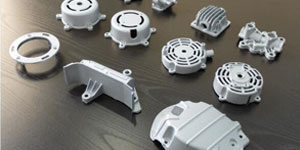
Çinko pres döküm tasarım yardımı/eşzamanlı mühendislik hizmetleri. Hassas çinko dökümlerin özel üreticisi. Minyatür dökümler, yüksek basınçlı dökümler, çok kızaklı kalıp dökümleri, geleneksel kalıp dökümleri, birim kalıp ve bağımsız kalıp dökümleri ve boşluklu sızdırmaz dökümler üretilebilir. Dökümler, +/- 24 inç toleransta 0.0005 inç'e kadar uzunluk ve genişliklerde üretilebilir.
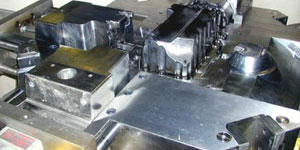
ISO 9001: 2015 sertifikalı döküm magnezyum üreticisi, Yetenekler arasında 200 ton sıcak odaya ve 3000 ton soğuk odaya kadar yüksek basınçlı magnezyum kalıp dökümü, takım tasarımı, cilalama, kalıplama, işleme, toz ve sıvı boyama, CMM özelliklerine sahip tam kalite güvencesi bulunur , montaj, paketleme ve teslimat.
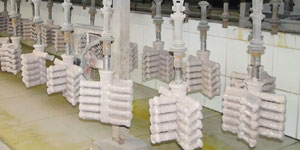
ITAF16949 sertifikalı. Ek Döküm Hizmeti Dahil yatırım dökümleri,kum dökümü,Yerçekimi Döküm, Kayıp Köpük Döküm,Savurma döküm,Vakumlu Döküm,Kalıcı Kalıp Döküm,.Yetenekler arasında EDI, mühendislik yardımı, katı modelleme ve ikincil işleme yer alır.
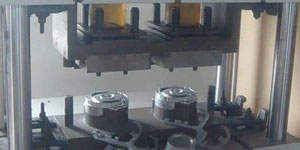
Döküm Endüstrileri Arabalar, Bisikletler, Uçaklar, Müzik aletleri, Deniz Araçları, Optik cihazlar, Sensörler, Modeller, Elektronik cihazlar, Muhafazalar, Saatler, Makineler, Motorlar, Mobilya, Mücevher, Jigler, Telekom, Aydınlatma, Tıbbi cihazlar, Fotoğraf cihazları, Robotlar, Heykeller, Ses ekipmanları, Spor ekipmanları, Aletler, Oyuncaklar ve daha fazlası.
Bundan sonra ne yapmanıza yardımcı olabiliriz?
∇ Ana Sayfaya Git Çin Döküm
→Döküm Parçaları-Ne yaptığımızı öğren.
→ Hakkında İlgili İpuçları Pres Döküm Hizmetleri
By Minghe Döküm Üreticisi |Kategoriler: Faydalı Makaleler |Malzeme Etiketler: Alüminyum Döküm, Çinko Döküm, Magnezyum Döküm, Titanyum Döküm, Paslanmaz Çelik Döküm, Pirinç Döküm,Bronz Döküm,Döküm Videosu,Tarihçe,Alüminyum Döküm |Yorumlar Kapalı