Yaş kum sisteminin stabilitesi nasıl sağlanır?
I.Giriş
Üretim koşullarındaki ve ortamdaki değişiklikler nedeniyle, dökümün diğer parametreleri de kaçınılmaz olarak değişecektir. Kalıplama kumu işlemi zamanında ayarlanmazsa, kum sistemi kararsız olacak ve bu da sonunda dökümün ve hatta hurdanın daha zor temizlenmesine yol açacaktır;
Bu şekilde, kum sistemini stabilize etmek için orijinal kalıplama kumu işlemini ayarlamak gerekir; Kalıp kumunun malzeme bileşimi esas olarak eski kum, ham kum, bentonit ve katkı maddelerinden oluşur. Kalıplama kumunun %95'inden fazlası eski kum olduğundan ve eski kum, dökümün farklı kum-demir oranı ve maça kumunun farklı karışım miktarı gibi faktörlerden etkilendiğinden, çok büyük dalgalanmalara neden olur. malzeme bileşimi. Bu nedenle, kalıp kumunun bileşimini kontrol etmek için, kum karıştırma sırasında eklenen bentonit, katkı maddeleri ve ham kum miktarını belirlemek için kalıp kumundaki etkin bentonit içeriği, etkin katkı içeriği ve çamur içeriğinin incelenmesi gerekir.
Bu makale, yazarın şirketinin dökümhanesinin gerçek üretim sürecinde nasıl kök saldığını kısaca tanıtacaktır.
Parametrelerin değişimine göre, kum sisteminin stabilitesini sağlamak için kalıplama kumu işlemi ayarlanır.
2. Kalıp kumunun temel parametrelerinin tanımı:
1. Etkin bentonit içeriği: Etkin bentonit (aktif) içeriği, bentonitin içinde bulunan ve metilen mavisi ve diğer boyaları absorbe edebilen montmorillonit mineralinin özelliklerine göre belirlenir; 5.00g kalıplama kumunun %0.20 konsantrasyonlu reaktif saf metilen mavisi solüsyonu [mL] ile titrasyonuna atıfta bulunur; bentonitin standart eğri formülüne göre dönüştürülmüş (%)
2. Etkin katkı dozajı: Kalıp kumu katkılarının gaz oluşumu ile karşılaştırılır ve aşağıdaki formül kullanılarak hesaplanır; yani, 1.00°C'de [mL] 900g kalıplama kumunun gaz oluşumu eksi kalıplama kumundaki aktifleştirilmiş bentonitin gaz gelişimi (hesaplamadan önce ölçülen ortalama miktar) Ardından 1g katkı gazı hacmi (%) ile karşılaştırın.
3. Çamur içeriği: GB/T9442-1998 ulusal standardına göre, çapı 20μm'den küçük olan ince toz parçacıkları çamur olarak tanımlanır. Çamur genellikle yıkama yöntemi ile uzaklaştırılır [2].
4. Kalıp kumu parçacık boyutu: AFS inceliğinde ifade edilir, yani kum parçacıklarının ortalama boyutu, hayali elek işaretine göre yansıtılır [3];
5. AFS incelik hesaplama yöntemi: American Institute of Foundry tarafından belirlenen AFS incelik ölçüm prosedürleri ve hesaplama yöntemleri aşağıdaki gibidir:
①. Önce ölçülecek yaklaşık 50 g kum örneğini tartın, çamuru yıkayın, kurutun ve ardından eleyin.
②. Her elekte kalan kum parçacıklarının kalitesini tartın ve kaydedin;
③. Her elekte kalan kum parçacıklarının toplam kum numunesi miktarına oranını hesaplayın;
④. Her elekte kalan kum parçacıklarının yüzdesini, her bir elek için "AFS incelik çarpanı" ile çarpın;
⑤. Toplamı bulmak için her elek numarası için yukarıdaki ürünleri ekleyin:
⑥. AFS inceliğini elde etmek için, madde 5'te elde edilen toplamı, madde 3'teki her bir elek üzerinde kalan kum yüzdelerinin toplamına bölün.
3. Uyum planı:
Fabrikanın kullandığı kum karıştırma ekipmanı DISA kum değirmeni ve kalıplama ekipmanı KW statik basınçlı kalıplama hattıdır; yarım yıllık veri istatistiklerini kullanarak, kalıplama kumu sistemi için aşağıdaki planlar formüle edilmiştir:
1. İstatistikler:
① Kalıplama sunucusunun ayar değerine göre her kutuya eklenen kalıplama kumu miktarını belirleyin ve her kutu dökümün ağırlığına ve dökme ağırlığına göre her kutu dökümün kum-demir oranını hesaplayın sistem ve dökümde kullanılan maça kumu miktarı;
②Deşarj edilen atık kum miktarı ile maça kumu ve yardımcı malzemelerin kullanımına ilişkin istatistikler
③ Kalıp kumu sisteminin toz giderme istatistikleri
2. Kum ayarı:
① Üretim durumuna göre, iki veya daha fazla gün boyunca bir döküm sürekli olarak üretildiğinde, eklenen kalıp kumu aksesuarları (bentonit, katkı maddeleri) sabitlenecek ve etkili kalıp kumu miktarındaki değişiklikler sayılacaktır, ve daha sonra diğer dökümlerin sürekli üretimi sırasında kademeli olarak doğrulanır Kum/demir oranı ile eklenen miktar arasındaki ilişki;
② Kalıplama kumu parçacık boyutunun ayarlanması: kalıp kumunun AFS'si olduğunda, 50/100 elek medyan değerine (50/100 elek silika kumu, ortalama inceliğin medyan değeri 50 [4]) göre ayarlayın. 50'den küçük veya eşit, 70/140 ince kum veya 140/70 daha ince yeni kum eklenerek değirmen başına 30kg-60kg eklenir ve partikül büyüklüğündeki değişim analiz edilir.
③ Kalıplama kumunun çamur içeriğinin ayarlanması: günlük toz giderme istatistikleri aracılığıyla kalıplama kumu sisteminin çamur içeriğinin değişimini analiz edin;
Dördüncüsü, özel ayarlama süreci:
1. Döküm kumu/demir oranı istatistikleri:
(Not: X2B1 silindir gövdesi entegre kum maça ile döküldüğü için kalıp kumunu yakmaz, bu nedenle dökümün dış kalıp kumunun ağırlığı "0" olarak hesaplanır)
2. Etkili miktarı dökümün kum-demir oranına göre ayarlayın. 56D silindir bloğunun kum-demir oranı 6.57'dir. Yukarıdaki dökümler arasında kum-demir oranı silindir bloğu dökümleri arasında en yüksek olanıdır. Bu nedenle 56D silindir bloğu önce test edilir:
56D art arda üç gün boyunca üretildiğinde, katkı miktarı 22 kg/değirmen ve kil katkı miktarı 33 kg/değirmen; etkin katkı maddesi miktarı %4.55'ten %5.03'e yükseldi; etkili kil miktarı %6.56'dan %7'ye yükseldi; yaklaşık %0.5'lik bir artış; 56D silindir üretildiğinde, eklenen miktarın kum sisteminin denge değerinden daha yüksek olacak şekilde ayarlanması gerektiği anlamına gelir;
Yukarıdaki veri analizi ile eklenen yardımcı malzeme miktarı aşağıdaki gibi ayarlanır:
1) Silindir yeniden üretildiğinde, katkı miktarı 19kg/değirmen olarak ayarlanır ve kil katkı miktarı 26kg/değirmen olduğunda, ardışık üç gün için veri istatistikleri, etkin katkı miktarının %4.36'dan %4.29'a değiştiğini göstermektedir. ; efektif kil miktarı %4.36'dan %4.29'a değiştirilmiştir. %7.22, %7.11 olur; etkin miktar %0.1 oranında dalgalanır; bu nedenle, süreç ayarlama planı makuldür ve kalıplama kumu sisteminin dengesini sağlayabilir;
2) Benzer şekilde diğer dökümlere eklenen yardımcı malzeme miktarı ile efektif miktar arasındaki ilişki deneysel veri analizi ve teori ile hesaplanır; farklı dökümleri yeniden üretirken, eklenen yardımcı malzemelerin uygun miktarını ayarlayın.
3. Kum boyutunu ayarlamak için 70/140 mesh yeni kum ve 140/70 yeni kum kullanın (prototip kumun çamur içeriği %11.42'dir):
① 16 Ocak'tan 21 Ocak'a kadar, beş günde toplam 4257 kum öğütme süresi, yaklaşık 4257*3/900=14 kez; her döngünün parçacık boyutu yaklaşık 0.26 (öğütme başına) değişir; bu nedenle 16 Ocak'taki kalıp kumu AFS değeri 49.15'tir; 16 Ocak'tan itibaren, parçacık boyutunu ayarlamak için beş gün sürekli 70/140 yeni kum ilavesi, değirmen başına 60 kg, 21 Ocak'ta kalıplama kumunun AFS değeri 52.84'tür;
② 25 Ocak - 27 Ocak tarihleri arasında üç günde toplam 2165 kum öğütme süresi, yaklaşık 2165*3/900=7 devir; her döngünün tane boyutu yaklaşık olarak 0.22 (öğütme başına) değişir; bu nedenle, 24 Ocak kumu AFS =52.44, kalıplama kumunun parçacık boyutu 52-53'e ulaştığında, sürekli 70/140 yeni kum ilavesinin kum sistemi AFS üzerinde çok az etkisi vardır; 26 Ocak'tan itibaren, ayarlamak için arka arkaya üç gün boyunca 140/70 yeni kum eklenir ve her öğütme için 60 kg eklenir, 1 28'inde, kumun AFS'si 54'tür.
(Not: ①FAW kurumsal standardı, 70/140 kuvars kumu eleme oranının 70,100,140 ≥%80, bunun 70,100 eleme ≥%60; 140/70 kuvars kumu 70,100,140 eleme oranı ≥%80, bunun 100,140 eleme oranı ≥60 % ②Her bir öğütme hacmi 3 ton olup, sistem kum hacmi 900 ton olarak tahmin edilmektedir)
4. Ardışık üç ay için çamur içeriği ve toz giderme karşılaştırması:
Şubat-Mart ayları arasında kuzeydeki soğuk iklim nedeniyle, soğuk toz giderme boru hattındaki toz, sıcak toz uzaklaştırıldıktan sonra yoğunlaşacak ve katılaşacaktır. Boru hattı zamanında temizlenmezse sık sık tıkanmalar meydana gelecek ve günlük deşarj 4 ila 8 ton arasında değişecektir. Kum sisteminin çamur içeriği büyük ölçüde dalgalanır. Bu süre zarfında, toz giderme kapasitesini artırmanın ve çamur içeriğini azaltmanın tek yolu, toz giderme ekipmanının hava hacmini artırmak ve boruları taramaktır;
Nisan ayına girdikten sonra, sıcaklık kademeli olarak arttı, toz yoğuşması ve katılaşma olgusu artık ortaya çıkmadı, toz giderme miktarı kademeli olarak stabilize edildi, günde ortalama 7-8 ton deşarja ulaştı ve çamur içeriğinin dalgalanma aralığı azaldı;
Kalıplama kumu sisteminin çamur içeriği, yeni kum ilave edilerek veya yardımcı malzeme ilavesi azaltılarak da azaltılabilir. Bu iki yöntemin dezavantajları test sonucunda açıklanacaktır.
5. Test sonucu
1. Etkili kum aksesuar miktarını ayarlayın
Bentonit kristalleri ısıtma ile belirli bir dereceye kadar zarar görür ve su ilave edildikten ve karıştırıldıktan sonra ıslak bağlanma mukavemeti açıkça azalacaktır. Daha yüksek sıcaklıkta ve daha uzun süre ısıtıldıktan sonra, bentonitin kristal yapısı tamamen bozulur ve kohezyon kuvveti olmaksızın "ölü kil" haline gelir. Artan döküm kalınlığı, düşük kum-demir oranı, yüksek döküm sıcaklığı ve uzun soğuma süresi bentonitin yanma kaybını arttırır.
Kalıplama kumundaki etkili kömür tozunun yeterli olup olmadığına karar vermenin en doğrudan yolu, döküm yüzeyinin düzgünlüğünü ve kum yapışmasının olup olmadığını gözlemlemektir. Eski kumdaki kömürün bir kısmı dökülen erimiş metalin ısısı nedeniyle yanar ve yeniden doldurulması gerekir. Öte yandan, etkili toz haline getirilmiş kömür seviyesine ulaşmak için taze kum, karışık maça kumu ve bentonit gibi yeni eklenen malzemelerin de eklenmesi gerekmektedir. Kum karıştırma sırasında eklenen toplam toz haline getirilmiş kömür miktarı, yanma kaybının ve ilave ilave miktarın toplamıdır. (Etkili kömür tozu metindeki etkin katkı maddesine eşdeğerdir)
2. Kum boyutunun ayarlanması:
Yüksek basınçlı kalıplama kumunun parçacık boyutu genellikle 50/140 iken reçine kumu maçalarının parçacık boyutu çoğunlukla 50/100 veya daha kabadır. Maça kumunun aşırı karıştırılması, tüm eski ıslak kumun irileşmesini etkileyecek, bu da kumun geçirgenliğini artıracak ve dökümün yüzeyini pürüzlendirecektir.
Kalıp kumunun partikül boyutunun kabalaşmasını önlemek için toz giderme sisteminden gelen partiküller eski kuma geri dönüştürülebilir. Veya ayarlamak için ince yeni kum ekleyin; dökümhanede belirtildiği gibi, kalıplama kumunun AFS'si yaklaşık 48'e ulaştığında, sürekli olarak 70/140 veya 140/70 yeni kum ekleyerek ayarlayın; bununla birlikte, dökümler kum sisteminin çekirdeğine kırıldığı için Kum miktarı zaten fazladır. Kalıp kumunun partikül boyutu dayanılmaz derecede irileştirilmemişse, sürekli olarak bu kadar büyük miktarda yeni kum eklenmesi tavsiye edilmez, aksi takdirde kalıp kumu sisteminin diğer performans göstergelerini (çamur içeriği, etkin miktar ve aşırı miktarda yeni kum nedeniyle mukavemet). ) üzerinde etkisi olan;
3. Çamur içeriğinin ayarlanması
Çamur içeriğinin artması kalıp kumunun geçirgenliğinin azalmasına neden olacak ve döküm işlemi sırasında "gaz patlaması" olgusu meydana gelecek ve patlama ve yapışkan kum nedeniyle döküm hurdaya çıkacaktır. Kalıp kumu sisteminin çamur içeriği çok yüksek olmamalıdır; yardımcı malzeme miktarı azaltılarak kum sisteminin çamur içeriği azaltılabilir, ancak etkin bentonit içeriğinin azaltılması kalıp kumunun mukavemetinin azalmasına neden olacak ve kumu kaldırma ve dayanma kabiliyeti azalacaktır; Etkin Azaltma dozu, kalıp kumunun kumun yapışma önleyici özelliğinin azalmasına neden olacaktır.
Çamur içeriğini ayarlamak için eklenen yeni kum miktarını artırırsanız, önce yeni eklenen çeşitli malzemelerin dökme kumda ne kadar çamur ürettiğini hesaplayın ve ardından çamur içeriğini yapmak için ne kadar ham kum eklenmesi gerektiğini hesaplayabilirsiniz. kalıplama kumu işlem Yönetmeliklerine uygundur.
Makalede bahsedildiği gibi, dökümhaneye eklenen her 0.1 kg yeni kum için çamur içeriği %30 oranında azaltılabilir; bununla birlikte, aşırı yeni kum ilavesi sadece maliyet israfına neden olmakla kalmayacak, aynı zamanda kalıp kumu sistemindeki kullanılmış kum oranını da azaltacak ve bu da kalıp kumunun performansını düşürecektir. , Kalıplama kumunun kalıplama kabiliyetini etkileyen kalıplama kumu ıraksar ve döküm işlemi sırasında kum yıkama fenomeni oluşur;
Bu nedenle yazar, kum sisteminin çamur içeriğinin toz giderme ekipmanı ayarlanarak kontrol edilebilmesinin en iyi seçim olduğuna inanmaktadır.
Sonuç olarak, stabilize kum sistemi, yüksek kaliteli dökümler üretebilmektir. Bu konsept sayesinde, üretim ihtiyaçlarını karşılamak için kalıplama kumu sürecini değişen üretim koşullarına göre sürekli olarak ayarlamalıyız.
Lütfen yeniden basım için bu makalenin kaynağını ve adresini saklayın: Yaş kum sisteminin stabilitesi nasıl sağlanır?
Minhe Basınçlı Döküm Şirketi kaliteli ve yüksek performanslı Döküm Parçaları üretmeye ve sağlamaya adamıştır (metal döküm parça yelpazesi esas olarak şunları içerir: İnce Duvarlı Döküm,Sıcak Kamara Basınçlı Döküm,Soğuk Oda Döküm), Yuvarlak Servis (Döküm Servisi,Cnc İşleme,Kalıp yapımı,Yüzey İşleme).Herhangi bir özel Alüminyum döküm, magnezyum veya Zamak/çinko döküm ve diğer döküm gereksinimleri bizimle iletişime geçebilirsiniz.
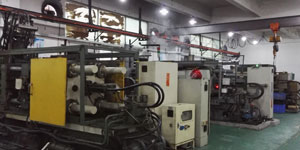
ISO9001 ve TS 16949 kontrolünde, tüm işlemler yüzlerce gelişmiş basınçlı döküm makinesi, 5 eksenli makine ve blasterlerden Ultra Sonic yıkama makinelerine kadar diğer tesisler aracılığıyla gerçekleştirilir. Müşterinin tasarımını gerçeğe dönüştürmek için deneyimli mühendisler, operatörler ve müfettişlerden oluşan ekip.
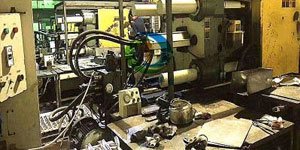
Dökümlerin sözleşmeli üreticisi. Yetenekler, 0.15 lbs'den başlayan soğuk oda alüminyum döküm parçaları içerir. 6 lbs'ye kadar, hızlı değişim kurulumu ve işleme. Katma değerli hizmetler arasında polisaj, titreşim, çapak alma, kumlama, boyama, kaplama, kaplama, montaj ve kalıplama yer alır. Çalışılan malzemeler arasında 360, 380, 383 ve 413 gibi alaşımlar bulunur.
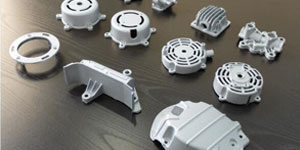
Çinko pres döküm tasarım yardımı/eşzamanlı mühendislik hizmetleri. Hassas çinko dökümlerin özel üreticisi. Minyatür dökümler, yüksek basınçlı dökümler, çok kızaklı kalıp dökümleri, geleneksel kalıp dökümleri, birim kalıp ve bağımsız kalıp dökümleri ve boşluklu sızdırmaz dökümler üretilebilir. Dökümler, +/- 24 inç toleransta 0.0005 inç'e kadar uzunluk ve genişliklerde üretilebilir.
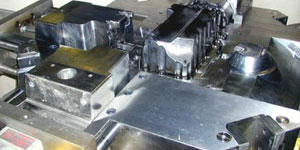
ISO 9001: 2015 sertifikalı döküm magnezyum üreticisi, Yetenekler arasında 200 ton sıcak odaya ve 3000 ton soğuk odaya kadar yüksek basınçlı magnezyum kalıp dökümü, takım tasarımı, cilalama, kalıplama, işleme, toz ve sıvı boyama, CMM özelliklerine sahip tam kalite güvencesi bulunur , montaj, paketleme ve teslimat.
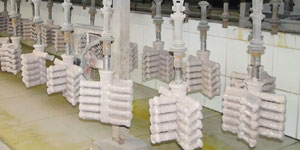
ITAF16949 sertifikalı. Ek Döküm Hizmeti Dahil yatırım dökümleri,kum dökümü,Yerçekimi Döküm, Kayıp Köpük Döküm,Savurma döküm,Vakumlu Döküm,Kalıcı Kalıp Döküm,.Yetenekler arasında EDI, mühendislik yardımı, katı modelleme ve ikincil işleme yer alır.
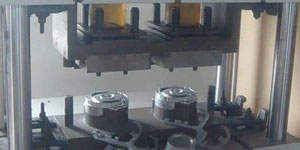
Döküm Endüstrileri Arabalar, Bisikletler, Uçaklar, Müzik aletleri, Deniz Araçları, Optik cihazlar, Sensörler, Modeller, Elektronik cihazlar, Muhafazalar, Saatler, Makineler, Motorlar, Mobilya, Mücevher, Jigler, Telekom, Aydınlatma, Tıbbi cihazlar, Fotoğraf cihazları, Robotlar, Heykeller, Ses ekipmanları, Spor ekipmanları, Aletler, Oyuncaklar ve daha fazlası.
Bundan sonra ne yapmanıza yardımcı olabiliriz?
∇ Ana Sayfaya Git Çin Döküm
→Döküm Parçaları-Ne yaptığımızı öğren.
→ Hakkında İlgili İpuçları Pres Döküm Hizmetleri
By Minghe Döküm Üreticisi |Kategoriler: Faydalı Makaleler |Malzeme Etiketler: Alüminyum Döküm, Çinko Döküm, Magnezyum Döküm, Titanyum Döküm, Paslanmaz Çelik Döküm, Pirinç Döküm,Bronz Döküm,Döküm Videosu,Tarihçe,Alüminyum Döküm |Yorumlar Kapalı