Yükselticisiz sfero dökümün gerçekleştirilmesi için koşullar
1 Sfero dökme demirin katılaşma özellikleri
Küresel dökme demir ve gri dökme demirin farklı katılaştırma yöntemleri, küresel grafit ve pul grafitin farklı büyüme yöntemlerinden kaynaklanır.
Ötektik altı gri demirde, grafit, birincil östenitin kenarında çökelmeye başlar. Grafit levhanın iki tarafı ostenit ile çevrilidir ve kalınlaştırmak için ostenitten grafiti emer. Grafit levhanın ucu sıvı içindedir. Grafiti emerek büyür.
Küresel dökme demirde, grafit küresel olduğu için, grafit topları yağıştan sonra etrafındaki grafiti emmeye başlar. Çevreleyen sıvı katı ostenite dönüşür ve w(C) miktarındaki azalma nedeniyle grafit topları çevreler; Östenit ile çevrili, östenitten emilebilen tek karbon nispeten sınırlıdır, sıvıdaki karbon ise katı içinden grafit topuna yavaşça yayılır ve östenit ile çevrili olmak büyümesini sınırlar; bu nedenle küresel dökme demirin karbon eşdeğeri gri dökme demirden çok daha yüksek olmasına rağmen, küresel dökme demirin grafitizasyonu daha zordur, bu nedenle katılaşma büzülmesini telafi etmek için yeterli grafitleşme genişlemesi yoktur; bu nedenle, sfero dökme demir büzülmeye eğilimlidir.
Ayrıca grafit küreyi saran ostenit tabakasının kalınlığı genellikle grafit kürenin çapının 1.4 katıdır. Yani, grafit bilye ne kadar büyükse, ostenit tabakası o kadar kalındır ve sıvıdaki karbonun ostenit yoluyla grafit küreye geçmesi o kadar zor olur. Harika [1].
Düşük silikonlu sfero dökümün beyaz ağza eğilimli olmasının temel nedeni aynı zamanda sfero dökümün katılaştırma yöntemidir. Yukarıda bahsedildiği gibi, sfero dökümün grafitizasyonunun zorluğundan dolayı, grafitleşme tarafından üretilen kalıba salınacak yeterli kristalleşme gizli ısısı yoktur, bu da aşırı soğuma derecesini arttırır ve grafitin çökelmek için zamanı yoktur. sementit. Ek olarak, küresel grafitli dökme demir, aşırı soğumaya son derece eğilimli faktörlerden biri olan hızlı bir büyüme ve düşüşe sahiptir [1].
2 Yükseltici döküm olmadan sfero döküm için koşullar
Sfero döküm parçalar için kolonsuz döküm elde etmenin daha zor olduğunu sfero dökümün katılaşma özelliklerinden görmek zor değildir. Yazar, üretimde uzun yıllara dayanan pratik deneyimime dayanarak, sfero dökümün kolonsuz döküm işlemini gerçekleştirebilmesi için gerekli koşullar hakkında bazı genellemeler ve özetler yapmış ve burada meslektaşları ile paylaşmıştır.
2.1 Erimiş demir bileşiminin seçimi
2.1.1 Karbon eşdeğeri (CE)
Aynı koşullar altında, küçük grafitin erimiş demirde çözülmesi kolaydır ve büyümesi kolay değildir; Grafit büyüdükçe, grafitin büyüme hızı da daha hızlı hale gelir, bu nedenle ötektik katılaşmayı teşvik etmek için erimiş demirde ötektikten önce birincil grafit üretilir Grafitleşme çok avantajlıdır. Ötektik üstü bileşime sahip erimiş demir bu tür koşulları karşılayabilir, ancak aşırı yüksek CE değeri ötektik katılaşmadan önce grafitin büyümesine neden olur ve belirli bir boyuta büyüdüğünde grafit yüzmeye başlar ve grafit yüzer kusurlarına neden olur. Bu zamanda, grafitleşmenin neden olduğu hacim genişlemesi, yalnızca erimiş demir seviyesinin yükselmesine neden olur, bu sadece dökümün beslenmesi için anlamsız değildir, aynı zamanda grafit sıvı haldeyken büyük miktarda karbon emdiği için. ötektik katılaştığında erimiş demirin katılaşmasına neden olur. Ortamdaki düşük w(C) miktarı yeterli ötektik grafit üretemez ve ötektik katılaşmanın neden olduğu büzülmeyi dengeleyemez. Uygulama, CE değerini %4.30 ile %4.50 arasında kontrol edebilmenin ideal olduğunu kanıtlamıştır.
2.1.2 Silikon (Si)
Genellikle Fe-C-Si alaşımlarında Si'nin grafitleştirici bir element olduğuna ve yüksek miktarda w (Si)'nin grafitleşme genişlemesine faydalı olduğuna ve büzülme boşluklarının oluşumunu azaltabileceğine inanılır. Si'nin ötektik katılaşma grafitleşmesini engellediğini çok az kişi biliyor. Bu nedenle parçalanmış grafitin beslenmesi veya oluşumunun engellenmesi açısından ne olursa olsun aşılamanın güçlendirilmesi gibi önlemlerle beyaz ağız önlenebildiği sürece w(Si) miktarı mümkün olduğunca azaltılmalıdır.
2.1.3 Karbon (C)
Makul CE değeri koşulu altında, w(C) miktarını mümkün olduğu kadar artırın. Gerçekler, sfero dökümün w(C) içeriğinin %3.60~3.70 oranında kontrol edildiğini ve dökümün en düşük büzülme oranına sahip olduğunu kanıtlamıştır.
2.1.4 Kükürt (S)
S, grafitin küreselleşmesini engelleyen ana unsurdur. Küreselleştirmenin temel amacı S'yi uzaklaştırmaktır. Ancak sfero dökme demirin hızlı büyümesi ve azalması, düşük w(S) miktarı ile doğrudan ilişkilidir; bu nedenle, uygun miktarda w(S) gereklidir. w(S) miktarı yaklaşık %0.015'te kontrol edilebilir ve MgS'nin çekirdeklenme etkisi, grafit kürelerinin sayısını artırmak ve düşüşü azaltmak için grafit çekirdek parçacıklarını artırmak için kullanılabilir [2].
2.1.5 Magnezyum (Mg)
Mg ayrıca grafitleşmeyi engelleyen bir elementtir, bu nedenle küreselleşme oranının %90'ın üzerine çıkabileceği varsayımı altında Mg mümkün olduğunca düşük olmalıdır. Orijinal erimiş demir w(O) ve w(S)'nin yüksek olmaması koşuluyla, kalan w(Mg) içeriği %0.03~0.04 arasında kontrol edilebilir en ideal olanıdır.
2.1.6 Diğer unsurlar
Mn, P, Cr ve grafitleşmeyi engelleyen diğer elementler mümkün olduğunca düşüktür.
Ti gibi eser elementlerin etkisine dikkat edin. w(Ti) miktarı düşük olduğunda grafitleşmeyi kuvvetle destekleyen bir elementtir. Aynı zamanda Ti, karbürleri oluşturan bir element ve küreselleşmeyi etkileyen ve vermiküler grafit üretimini teşvik eden bir elementtir. Bu nedenle, w (Ti) miktarı ne kadar düşükse, o kadar iyidir. Yazarın şirketi bir zamanlar çok olgun, yükseltici olmayan bir döküm sürecine sahipti. Geçici hammadde sıkıntısı nedeniyle, aw(Ti) içeriği %0.1 olan pik demir kullanıldı. Üretilen dökümlerin sadece yüzey büzülmesi değil, aynı zamanda işlendikten sonra içlerinde konsantre tipler de ortaya çıktı. Büzülme.
Kısacası, saf hammaddeler, sfero dökümün kendi kendini besleme kabiliyetini geliştirmek için faydalıdır.
2.2 Dökme sıcaklığı
Deneyler, sfero dökümün 1 350 ℃ ila 1500 ℃ arasındaki dökme sıcaklığının, dökümün büzülme hacmi üzerinde belirgin bir etkisi olmadığını, ancak büzülme boşluğunun morfolojisinin kademeli olarak konsantre tipten dağınık tipe geçtiğini göstermiştir. Grafit topların boyutu, dökme sıcaklığının artmasıyla kademeli olarak artar ve grafit topların sayısı giderek azalır. Bu nedenle, çok düşük bir döküm sıcaklığı talep etmeye gerek yoktur. Kalıp, erimiş demirin statik basıncına dayanacak kadar güçlü olduğu sürece, dökme sıcaklığı daha yüksek olabilir. Erimiş demir ötektik katılaşma sırasında aşırı soğuma derecesini azaltmak için kalıbı ısıtmak için kullanılır, böylece grafitizasyonun devam etmesi için yeterli zaman olur. Ancak kalıptaki erimiş demirin sıcaklık farkını en aza indirmek için döküm hızı mümkün olduğunca hızlı olmalıdır [3].
2.3 Soğuk demir
Yazarın soğuk demir kullanma deneyimine ve yukarıdaki teorik analize dayanarak, soğuk demirin büzülme kusurlarını ortadan kaldırabileceği iddiası doğru değildir. Bir yandan, soğuk demirin (delikli parçalar gibi) yerel kullanımı, büzülme boşluğunu ortadan kaldırmak yerine yalnızca aktarabilir; Öte yandan, soğuk demirin geniş bir alanda kullanılması, beslemeyi azaltma veya yükseltici olmaması etkisini sağlayabilir. Soğuk demir yerine kalıp mukavemetini bilinçsizce arttırmak sıvı veya ötektik katılaşma büzülmesini azaltır. Aslında soğuk demir çok fazla kullanılırsa grafit topun büyümesini ve grafitleşme derecesini etkiler, tam tersine çekmeyi şiddetlendirir.
2.4 Kalıp mukavemeti ve sertliği
Sfero döküm çoğunlukla ötektik veya ötektik üstü bileşimi seçtiğinden, erimiş demirin kalıptaki ötektik sıcaklığa soğuması daha uzun zaman alır, yani kalıbın hidrostatik basıncı ötektik bileşimin basıncından daha uzundur. Gri dökme demir daha uzunsa, kalıp basınç deformasyonuna daha yatkındır. Grafitleşme genleşmesinin neden olduğu hacim artışı, sıvı büzülmesi + katılaşma büzülmesi + kalıp deformasyon hacmini dengeleyemediğinde büzülme boşlukları kaçınılmazdır. Bu nedenle, yeterli kalıp rijitliği ve basınç dayanımı, kolonsuz dökümün gerçekleştirilmesi için önemli koşullardır. Yükselticisiz dökümü gerçekleştirmek için birçok kum kaplı demir döküm işlemi bu teorinin kanıtıdır.
2.5 Aşılama tedavisi
Güçlü aşılayıcı ve anında gecikmeli aşılama işlemi, erimiş demire yalnızca büyük miktarda çekirdek parçacıkları vermekle kalmaz, aynı zamanda aşılamanın azalmasını da önler ve ötektik katılaşma sırasında sfero dökümün yeterli grafit küresine sahip olmasını sağlayabilir; büyük ve küçük grafit topları azaltır Sıvıdaki C'nin grafit çekirdeğe olan aktarım mesafesi, grafitleşme hızını hızlandırır. Kısa sürede, büyük miktarda ötektik katılaşma, daha gizli kristalleşme ısısını serbest bırakabilir, aşırı soğutma derecesini azaltabilir ve beyaz ağızların oluşumunu önleyebilir, aynı zamanda grafitleşme genişlemesini güçlendirebilir. Böylece. Sfero dökümün kendi kendini besleme kabiliyetini geliştirmek için güçlü aşılama şarttır.
2.6 Sıvı demir filtrasyonu
Erimiş demir süzüldükten sonra, bazı oksitlenmiş inklüzyonlar süzülür, böylece erimiş demirin mikro akışkanlığı artar ve mikroskobik büzülme olasılığı azaltılabilir.
2.7 Döküm modülü
Döküm halinde perlitik sfero dökümün grafitleşmeyi engelleyen elementler eklemesi gerektiğinden, bu grafitleşme derecesini etkileyecek ve dökümlerin kendi kendini beslemesinin gerçekleşmesi üzerinde belirli bir etkisi olacaktır. Bu nedenle, veri girişleri vardır. Yükselticisiz döküm, QT500'ün altındaki sünek grafitler için uygundur. dökme demir. Ayrıca dökümün şekline ve boyutuna göre belirlenen modül en az 3.1 cm olmalıdır.
50 mm'den daha az kalınlığa sahip plaka dökümlerinin yükselticisiz dökümünün elde edilmesinin zor olduğunu belirtmekte fayda var.
QT500'ün üzerindeki sfero dökme demir için kolonsuz döküm işleminin gerçekleştirilme koşulunun, modülünün 3.6 cm'den büyük olması gerektiği bilgisi de vardır.
Lütfen yeniden basım için bu makalenin kaynağını ve adresini saklayın: Yükselticisiz sfero dökümün gerçekleştirilmesi için koşullar
Minhe Basınçlı Döküm Şirketi kaliteli ve yüksek performanslı Döküm Parçaları üretmeye ve sağlamaya adamıştır (metal döküm parça yelpazesi esas olarak şunları içerir: İnce Duvarlı Döküm,Sıcak Kamara Basınçlı Döküm,Soğuk Oda Döküm), Yuvarlak Servis (Döküm Servisi,Cnc İşleme,Kalıp yapımı,Yüzey İşleme).Herhangi bir özel Alüminyum döküm, magnezyum veya Zamak/çinko döküm ve diğer döküm gereksinimleri bizimle iletişime geçebilirsiniz.
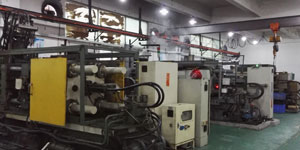
ISO9001 ve TS 16949 kontrolünde, tüm işlemler yüzlerce gelişmiş basınçlı döküm makinesi, 5 eksenli makine ve blasterlerden Ultra Sonic yıkama makinelerine kadar diğer tesisler aracılığıyla gerçekleştirilir. Müşterinin tasarımını gerçeğe dönüştürmek için deneyimli mühendisler, operatörler ve müfettişlerden oluşan ekip.
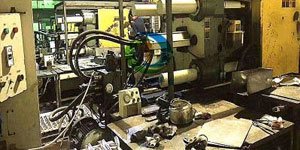
Dökümlerin sözleşmeli üreticisi. Yetenekler, 0.15 lbs'den başlayan soğuk oda alüminyum döküm parçaları içerir. 6 lbs'ye kadar, hızlı değişim kurulumu ve işleme. Katma değerli hizmetler arasında polisaj, titreşim, çapak alma, kumlama, boyama, kaplama, kaplama, montaj ve kalıplama yer alır. Çalışılan malzemeler arasında 360, 380, 383 ve 413 gibi alaşımlar bulunur.
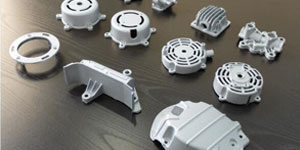
Çinko pres döküm tasarım yardımı/eşzamanlı mühendislik hizmetleri. Hassas çinko dökümlerin özel üreticisi. Minyatür dökümler, yüksek basınçlı dökümler, çok kızaklı kalıp dökümleri, geleneksel kalıp dökümleri, birim kalıp ve bağımsız kalıp dökümleri ve boşluklu sızdırmaz dökümler üretilebilir. Dökümler, +/- 24 inç toleransta 0.0005 inç'e kadar uzunluk ve genişliklerde üretilebilir.
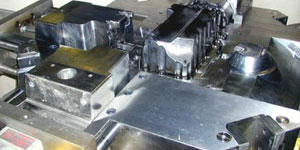
ISO 9001: 2015 sertifikalı döküm magnezyum üreticisi, Yetenekler arasında 200 ton sıcak odaya ve 3000 ton soğuk odaya kadar yüksek basınçlı magnezyum kalıp dökümü, takım tasarımı, cilalama, kalıplama, işleme, toz ve sıvı boyama, CMM özelliklerine sahip tam kalite güvencesi bulunur , montaj, paketleme ve teslimat.
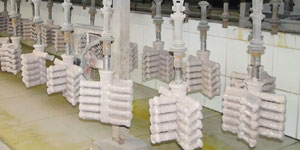
ITAF16949 sertifikalı. Ek Döküm Hizmeti Dahil yatırım dökümleri,kum dökümü,Yerçekimi Döküm, Kayıp Köpük Döküm,Savurma döküm,Vakumlu Döküm,Kalıcı Kalıp Döküm,.Yetenekler arasında EDI, mühendislik yardımı, katı modelleme ve ikincil işleme yer alır.
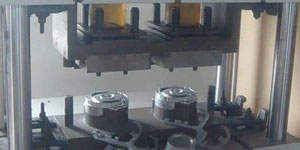
Döküm Endüstrileri Arabalar, Bisikletler, Uçaklar, Müzik aletleri, Deniz Araçları, Optik cihazlar, Sensörler, Modeller, Elektronik cihazlar, Muhafazalar, Saatler, Makineler, Motorlar, Mobilya, Mücevher, Jigler, Telekom, Aydınlatma, Tıbbi cihazlar, Fotoğraf cihazları, Robotlar, Heykeller, Ses ekipmanları, Spor ekipmanları, Aletler, Oyuncaklar ve daha fazlası.
Bundan sonra ne yapmanıza yardımcı olabiliriz?
∇ Ana Sayfaya Git Çin Döküm
→Döküm Parçaları-Ne yaptığımızı öğren.
→ Hakkında İlgili İpuçları Pres Döküm Hizmetleri
By Minghe Döküm Üreticisi |Kategoriler: Faydalı Makaleler |Malzeme Etiketler: Alüminyum Döküm, Çinko Döküm, Magnezyum Döküm, Titanyum Döküm, Paslanmaz Çelik Döküm, Pirinç Döküm,Bronz Döküm,Döküm Videosu,Tarihçe,Alüminyum Döküm |Yorumlar Kapalı