Basınçlı Döküm Nedir? Kalıp Döküm İşlemi Nedir?
Yüksek basınçlı döküm, modern metal işleme teknolojisinde hızla gelişen, daha az kesimli ve kesimsiz özel bir döküm yöntemidir. Erimiş metalin yüksek basınç ve yüksek hızda bir kalıba doldurulup, yüksek basınç altında kristalleştirilip katılaştırılarak bir döküm elde edilmesi işlemidir. Yüksek basınç ve yüksek hız, yüksek basınçlı dökümün ana özellikleridir. Yaygın olarak kullanılan basınç onlarca megapaskaldır, doldurma hızı (iç kapı hızı) yaklaşık 16-80 m/s'dir ve erimiş metalin kalıp boşluğunu doldurma süresi son derece kısadır, yaklaşık 0.01-0.2 saniyedir. Bu yöntemle üretilen ürünler, yüksek üretim verimliliği, basit prosedürler, daha yüksek tolerans seviyeleri, iyi yüzey pürüzlülüğü ve yüksek mekanik mukavemet avantajlarına sahip olduğundan, birçok işleme prosedürü ve ekipmanından tasarruf edebilir, hammadde tasarrufu sağlayabilir, vb. , böylece döküm sektörünün önemli bir parçası haline gelmiştir.
Döküm İşleminin Ana İşlem Parametreleri
1. Pres Döküm İşlemine Giriş
- C: Kalıp döküm işlemi, kalıp döküm makinesi, kalıp döküm kalıbı ve kalıp döküm alaşımının üç unsurunun organik kombinasyonunun bir işlemidir.
- B: Kalıp döküm sırasında boşluğu metal doldurma işlemi, basınç, hız, sıcaklık ve zaman gibi işlem faktörlerini dinamik olarak dengeleme işlemidir.
- C: Bu süreç faktörleri hem birbirini kısıtlamakta hem de birbirini tamamlamaktadır. Beklenen sonuçlar ancak bu faktörleri koordineli hale getirmek için doğru bir şekilde seçip ayarlayarak elde edilebilir. Kalıp döküm işleminde sadece döküm yapısının işlenebilirliği değil, aynı zamanda kalıbın gelişmiş doğası da elde edilebilir. Döküm makinesinin performansı ve yapısı mükemmel, döküm alaşım seçiminin uyarlanabilirliği ve eritme işleminin standardizasyonu. Basınç, hız ve zamanın döküm kalitesi üzerindeki önemli etkisine daha fazla dikkat edilmelidir.
2. Basınç
Basınçlı döküm işlemini diğer döküm yöntemlerinden ayıran en önemli özellik basıncın varlığıdır. Basınç, dökümlerin kompakt yapı ve net anahat elde etmesini sağlayan faktördür; basınç, enjeksiyon kuvveti ve özgül basınç olarak ifade edilebilir.
2.1 Enjeksiyon kuvveti
Enjeksiyon kuvveti, enjeksiyon mekanizmasındaki enjeksiyon pistonunun hareketini iten kuvvettir. döküm makine. Enjeksiyon kuvveti, döküm makinesinin işlevini yansıtan ana parametredir. Enjeksiyon kuvvetinin boyutu, enjeksiyon silindirinin kesit alanı ve enjeksiyon odasındaki çalışma sıvısının basıncı ile belirlenir. Enjeksiyon kuvvetinin formülü aşağıdaki gibidir: F basıncı = P sıvı XA silindiri
2.2 Özgül Basınç
Basınç odasındaki erimiş metalin birim alandaki basıncına özgül basınç denir. Spesifik basınç, enjeksiyon kuvvetinin basınç odasının kesit alanına oranıdır. Hesaplama formülü şu şekildedir: P oranı = P enjeksiyon / A odası
Spesifik basınç, doldurma işleminin her aşamasında erimiş metalin gerçek kuvvetinin ifade yöntemidir ve doldurmanın her aşamasında ve metal farklı kesitlerden akarken erimiş metalin kuvveti kavramını yansıtır. alanlar. Doldurma sırasındaki özgül basınca, doldurmaya özgü basınç veya enjeksiyona özgü basınç denir. Takviye aşamasındaki spesifik basınca takviye spesifik basıncı denir. İki spesifik basıncın büyüklükleri de enjeksiyon kuvvetine göre belirlenir.
2.3 Basıncın Rolü ve Etkisi
- A: Doldurma özgül basıncı, metal sıvı akışının gerekli iç kapı hızına ulaşabilmesi için, kapı sistemindeki ve boşluktaki akış direncinin, özellikle iç kapıdaki direncin üstesinden gelmek içindir.
- B: Takviye basıncı ve özgül basınç, katılaşmış metal üzerindeki basıncı ve bu sırada oluşan şişkinlik kuvvetini belirler. Spesifik basıncın dökümün mekanik özellikleri üzerindeki etkisi: artan spesifik basınç, ince kristaller ve artan ince taneli tabakalar İyileştirilmiş doldurma özellikleri, iyileştirilmiş yüzey kalitesi, azaltılmış gözenek etkileri ve iyileştirilmiş çekme mukavemeti nedeniyle daha kalın.
- C: Doldurma koşulları üzerindeki etki: Alaşım eriyiği boşluğu yüksek özgül basınç altında doldurur, alaşım sıcaklığı yükselir ve akışkanlık iyileşir, bu da döküm kalitesinin iyileştirilmesi için faydalıdır.
3. hız
Kalıp döküm işlemi sırasında, enjeksiyon hızı doğrudan basınçtan etkilenir ve basınçla birlikte dökümün iç kalitesi, yüzey gereksinimleri ve kontur netliğinde önemli bir rol oynar. Basınç, hızın temel hız gösterimi olup iki türe ayrılır: zımba hızı ve giriş hızı.
3.1 Yumruk hızı ile cinsel ilişki hızı arasındaki ilişki
Süreklilik ilkesine göre, aynı zamanda, V1 hızında F1 basınç odasının kesit alanı ile alaşım sıvısından akan metal akışının hacmi, alaşım sıvısının hacmine eşit olmalıdır. F2 kesit alanı ile iç kapıdan akan V2 hızında F1 odası V1 atış = F2 içinde ve V2 içinde. Bu nedenle, enjeksiyon çekicinin enjeksiyon hızı ne kadar yüksek olursa, kapıdan akan metal o kadar yüksek olur.
3.2 Enjeksiyon hızı
- C: Enjeksiyon hızı iki seviyeye ayrılmıştır. Birinci seviye enjeksiyon hızına yavaş enjeksiyon hızı da denir. Bu hız seviyesi, zımbanın ilk hareketinden zımbanın odadaki erimiş metali iç kapıya göndermesine kadar olan hareket hızını ifade eder. Bu aşamada alaşım sıvısının sıcaklığını çok fazla düşürmemek aynı zamanda basınç odasındaki gazı da gidermeye yardımcı olmak ilkesiyle basınç odasının içindeki erimiş metal ile basınç odasının doldurulması gerekmektedir.
- B: İkincil enjeksiyon hızına hızlı enjeksiyon hızı da denir. Bu hız, kalıp döküm makinesinin özelliklerine göre belirlenir. Pres döküm makinesi tarafından verilen maksimum enjeksiyon hızı genellikle 4-5 m/s aralığındadır.
3.3 Hızlı Enjeksiyon Hızının Rolü ve Etkisi
Hızlı enjeksiyon hızının alaşımların mekanik özellikleri üzerindeki etkisi ve etkisi, enjeksiyon hızını arttırmak, kinetik enerjiyi ısı enerjisine dönüştürmek, alaşım eriyiğinin akışkanlığını iyileştirmek, akış işaretleri, soğuk bariyerler gibi kusurları ortadan kaldırmaya yardımcı olmak ve mekanik özellikleri iyileştirmek ve yüzey kalitesi, Ancak hız çok hızlı olduğunda, alaşım eriyiği puslu olacak ve gazla karışacak, bu da ciddi sıkışmaya ve mekanik özelliklerin bozulmasına neden olacaktır.
3.4 İç Kapı Hızı
Erimiş metal iç kapıya girdiğinde ve boşluğa girdiğinde lineer hıza iç kapı hızı denir; iç kapı hızının olağan aralığı 15-70 m/s'dir. İç kapının hızı, dökümün mekanik özellikleri üzerinde büyük bir etkiye sahiptir. İç kapının hızı çok düşükse, dökümün gücü azalır; hız artar, güç artar; hız çok yüksek ve güç azalır.
4. Sıcaklık
Basınçlı döküm işleminde, doldurma işleminin termal durumunda ve işlemin verimliliğinde sıcaklık önemli bir rol oynar. Dökümde belirtilen sıcaklık, döküm, sıcaklık ve kalıp sıcaklığını ifade eder. Sıcaklık kontrolü, iyi dökümler elde etmek için önemli bir endüstriyel faktördür. Erimiş metalin dökme sıcaklığı, basınç odasından boşluğa girdiğinde ortalama sıcaklığı ifade eder. Doldurma odasındaki erimiş metalin sıcaklığını ölçmek uygun olmadığı için genellikle bekletme fırınının sıcaklığı olarak ifade edilir.
4.1 Dökme Sıcaklığının Rolü ve Etkisi
Alaşım sıcaklığının dökümlerin mekanik özellikleri üzerindeki etkisi. Alaşım sıcaklığı arttıkça. Mekanik performans arttı, ancak belirli bir sınırdan sonra performans düşüyor, ana nedenler:
- A: Alaşımdaki gazın çözünürlüğü sıcaklık arttıkça artar. Gaz alaşımda çözünmesine rağmen, mekanik özellikleri etkileyen kalıp döküm işlemi sırasında çökelmek zordur.
- B: Alaşım sıcaklığının artmasıyla demir içeriği artar, bu da akışkanlığı, kaba kristalleri azaltır ve performansı düşürür
- C: Alüminyum ve magnezyum alaşımları artan sıcaklık, oksitleyici inklüzyonlar ve alaşımın özelliklerinin bozulması ile daha fazla oksitlenir.
4.2 Kalıp Sıcaklığının Rolü ve Etkisi
Kalıp döküm işlemi sırasında kalıp belirli bir sıcaklığa ihtiyaç duyar. Kalıbın sıcaklığı, üretim verimliliğini artırmada ve yüksek kaliteli dökümler elde etmede önemli bir rol oynayan basınçlı döküm işleminde bir diğer önemli faktördür.
Doldurma işlemi sırasında, kalıp sıcaklığının metal sıvı sıcaklığı, viskozite, akışkanlık, doldurma süresi, doğrudan doldurma akış durumu vb. üzerinde büyük etkisi vardır. Kalıp sıcaklığı çok düşük olduğunda, yüzey tabakası yoğunlaşır ve yüksek hız sıvı akışı tekrar kırılır ve bir yüzey tabakası ile sonuçlanır Kusurlar, kalıplama sıcaklığı çok yüksek olsa bile, dökümün pürüzsüz bir yüzeyini elde etmek faydalı olsa da, büzülmesi ve çökmesi kolaydır
Kalıp sıcaklığı, alaşım eriyiğinin soğuma hızı, kristal durumu ve büzülme gerilimi üzerinde önemli bir etkiye sahiptir.
Kalıp sıcaklığı çok düşükse, büzülme gerilimi artacak ve döküm çatlamaya meyilli olacaktır.
Kalıp sıcaklığının kalıp ömrü üzerinde büyük etkisi vardır. Yoğun sıcaklık değişiklikleri karmaşık bir stres durumu oluşturur ve sık stres değişiklikleri erken çatlaklara neden olur.
Kalıp sıcaklığı, dökümün boyutsal tolerans seviyesi üzerinde bir etkiye sahiptir. Kalıp sıcaklığı sabit ise, dökümün boyutsal küçülmesi de kararlıdır ve boyutsal tolerans seviyesi de iyileşir.
5. zaman
Kalıp döküm işlemindeki "zaman", doldurma süresi, basınç oluşturma süresi, basınç tutma süresi ve kalıp tutma süresidir. Bu "zamanlar", basınç, hız ve sıcaklığın üç faktörünün yanı sıra erimiş metalin fiziksel özellikleridir. , Döküm yapısı (özellikle et kalınlığı), kalıp yapısı (özellikle döküm sistemi ve taşma sistemi) ve diğer kapsamlı sonuçlar.
5.1 Dolum Süresi
Erimiş metalin basınç altında boşluğa girmesi için doldurulana kadar geçen süreye doldurma süresi denir. Galvanizli parçaların dolum süresi 0.02S, yakıt enjeksiyonlu parçaların dolum süresi ise 0.04S'dir.
5.2 Dolum Süresi
Takviye basıncı oluşturma süresi, boşluğun doldurulduğu andan başlayarak, takviye basıncı önceden belirlenmiş bir değere ulaşana kadar, yani enjeksiyona özgü basınç artışından, doldurma işlemindeki erimiş metalin takviye fazını ifade eder. Artış Basıncın oluşması için geçen süre
5.3 Bekletme Süresi
Erimiş metal boşluğu doldurduktan sonra, erimiş metalin takviye basıncının etkisi altında katılaştığı süreye tutma süresi denir. Tutma süresinin işlevi, enjeksiyon zımbasının basıncı, katılaşmamış kalan malzeme ve kapı kısmındaki katılaşmamış metal aracılığıyla boşluğa aktarmasını sağlamaktır, böylece katılaşmış metal, yoğun bir döküm elde etmek için basınç altında kristalleşecektir.
3. Döküm Tasarımı
Kusurlu ürünlerin oluşmasını temel olarak önlemek ve kalıp döküm parçalarının düşük maliyetle seri üretilmesini sağlamak için, kalıp döküm parçalarının tasarımı, kalıp döküm üretimine uygun olmalıdır. İyi bir kalıp döküm tasarımı, kalıbın ömrünü, üretimini ve üretim güvenilirliğini sağlayabilir. İyi bir verim oranı ile, aşağıda kalıp dökümlerin yapısından ve sürecinden tasarım ilkeleri ve gereksinimleri açıklanacaktır.
1. Tasarım yaparken iç içbükeyden kaçının ve yan maça çekme sayısını en aza indirin
2. Kalıp dökümlerinin et kalınlığının tasarımı
Kalıp dökümlerin et kalınlığı genellikle 2-5 mm'dir. Genellikle 7 mm veya daha fazla et kalınlığının iyi olmadığı kabul edilir, çünkü et kalınlığının artmasıyla mukavemeti azalır. Buna ek olarak, duvar kalınlığı tasarımı mümkün olduğunca eşit duvar kalınlığı ilkesini takip etmelidir, esas olarak yerel sıcak eklemler tarafından oluşturulan büzülme gerilimi ile farklı kalınlıklar arasındaki büyük farkın iç gözeneklere, deformasyona, çatlaklara ve diğer kusurlara neden olmasını önlemek için. .
3. Kalıp dökümün yuvarlak köşe tasarımı
Özel uyum gereksinimleri dışında, dökümün tüm parçaları yuvarlatılmış köşelerle tasarlanmalıdır. Yuvarlatılmış köşelerin işlevi, stres yoğunlaşmasını ve çatlamayı önlemek ve aynı zamanda kalıbın ömrünü uzatmaktır. Ek olarak, parçaların yüzey işleme gereksinimleri olduğunda yuvarlatılmış köşeler eşit şekilde kaplanabilir. Zemin.
4. Kalıp dökümün taslak açısının tasarımı
Taslak açısının rolü, ürünü sorunsuz bir şekilde kalıptan çıkarmak, parçaların sıkma kuvvetini azaltmak ve parçaların gerilmesini önlemektir. Döküm parçaların minimum eğimi aşağıdaki tabloda listelenmiştir ve izin veriliyorsa en büyük eğim alınmalıdır. , Genel aralık bir tarafta 1-3 derecedir.
5. Kalıp döküm işleminin fırlatma pozisyonunun tasarımı
Döküm işleminde kalıp açıldıktan sonra ürün hareketli kalıba sarılır ve kalıbın ejektör pimi ile dışarı atılması gerekir. Bu nedenle, üründe ejektör pimini yerleştirmek için yeterli alana sahip olmalıdır. Döküm ürünün ejektör piminin çapı genellikle 5 mm'nin üzerinde ve 5 mm'nin altındadır. Genellikle üretim sırasında kırılır, bu nedenle tavsiye edilmez. Döküm ürünleri tasarlarken, yeterli fırlatma alanı ve konumu olup olmadığını göz önünde bulundurun. Özel şekilli yüksük kullanmaktan kaçının ve yuvarlak yüksük kullanın. Aynı zamanda yüksüğün ve duvarın konumuna dikkat edin. Yeterli mesafe, genellikle 3 mm'den büyük.
6. Kalıp dökümlerinin sonraki işlemlerinin tasarımını azaltın
Döküm parçalar yüksek boyutsal doğruluk sağlayabilir, bu nedenle çoğu yüzey ve parça mekanik işleme gerektirmez ve doğrudan monte edilip kullanılabilir. Aynı zamanda, aşağıdaki iki nedenden dolayı mekanik işleme desteklenmez. Birincisi, döküm yüzeyinin sert ve aşınmaya dayanıklı olması ve işlemden sonra kaybolmasıdır. Bu soğutulmuş tabaka, ikincisi, genellikle döküm içinde gözenekler olmasıdır. Dağınık küçük gözenekler kullanımı etkilemez. İşlemden sonra, gözenekler, görünüm ve kullanım işlevini etkilemek için maruz kalır. Mekanik işlem gerektiren özel gereksinimler olsa bile kullanılmalıdır. İşleme payını makul bir şekilde kontrol edin, işleme süresini ve hava deliklerini sızdırma olasılığını azaltın. Genel olarak, işleme payı 0.8'in altında kontrol edilir. Mekanik işlemeyi en aza indirmek için, parçaların montajını sağlamak için çizimin toleransını makul bir şekilde formüle etmek gerekir. Uygun olmayan tolerans aralığı sonraki işlemeyi artıracaktır. İkincisi, makul tasarım, parçaların büzülmesini ve deformasyonunu azaltır. Üçüncüsü, uç şeklindeki delikler için açılı montaj delikleri düşünülebilir.
7. Döküm tasarımında gömülü tasarım
Metal veya metal olmayan ekler, esas olarak yerel mukavemeti ve aşınma direncini artırmak veya oluşturulması zor iç boşluklar oluşturmak için kalıp döküm parçalarına dökülebilir. Ek parçanın metale gömülü olduğu kısım, dönmeyi ve eksenel hareketi önleyecek şekilde tasarlanmalıdır. Ek parçayı kalıba yerleştirmenin rahatlığını ve erimiş metalin etkisine dayanma kararlılığını göz önünde bulundurun.
5. Kalıp dökümlerin kalite problemlerini çözme durumları.
Kabuktan 100 yüzün işlenmesinde ışığı görmeme sorunu
1.1 Durum anketi
1.2 İşlemin ışığı görmemesinin nedeni
1.2.1 Kabuk işlerken, hareketli kalıp yüzeyini işlemek için önce B1, B2 ve B3 uç yüzlerini referans yüzey olarak kullanın ve ardından statik kalıp yüzeyini işlemek için referans yüzey olarak işlenmiş hareketli kalıp yüzeyini kullanın. Görünmeyen kısım ölçüldükten sonra, hareketli kalıp yüzeyinin işlendikten sonra bir eğim olduğu bulunur (aşağıdaki şekilde gösterildiği gibi). Normal işlenmiş parça ile karşılaştırıldığında, görünmeyen parçanın hareketli kalıp yüzeyi lokal olarak 1 mm daha fazla işlenir. İşlem sırasında B2 referans düzleminin uygun olmayan şekilde sıkıştırılmasından veya referans düzleminin deformasyonundan kaynaklanır.
1.3. B2 referans deliğinin deformasyon nedenleri
1.3.1 Kısmi tip çapak kalınlığı, B2 referans deliğinin uç yüzünün daha yüksek olmasına neden olur. Görünmez B2 parçasının duvar kalınlığı 8 mm'dir ve normal işlenmiş B parçasının iki duvar kalınlığı aynıdır. Duvarın kalınlığı çok az değişir. B2 referans deliğinin uç yüzeyinin artmasının nedeni çapak kalınlığı değildir.
1.3.2 Kalıp üzerindeki B1, B2 ve B3 deliklerinin maçaları sabitlendi ve maça geri çekilmesi bulunmadı. Çekirdek geri çekilme sorunu ortadan kaldırılabilir.
1 B3 deliğindeki tümsek deformasyona neden olur. İade edilen hatalı parçayı inceleyin. B2 deliğinde ciddi tümsekler var ve bu yeni bir tümsek değil. Tümsek, B2 deliğindeki deformasyonun ana nedenidir.
1.4 Sonuç
Sonuç: Çarpışma nedeniyle, B2 deliği statik kalıp tarafına deforme olur, bu da hareketli kalıp yüzeyi işlendiğinde B2'yi daha yüksek yapar. Hareketli kalıp yüzeyi bir eğime işlenir ve yerel işleme 1 mm daha fazladır; Statik kalıp yüzeyi işlenirken, hareketli kalıp yüzeyi referans düzlemi olarak kullanılır, Hareketli kalıbın çoklu işlem pozisyonuna karşılık gelen statik kalıp parçasının işlem miktarı yoktur, bu da statik kalıp tarafı işleminin görünmez olmasına neden olur.
1.5 İyileştirme önlemleri
1.5.1 Parçaları kalıp döküm atölyesine ve temizleme atölyesine yerleştirirken, bunları dikkatli bir şekilde yerleştirin ve dökümlerin çarpmasını önlemek için düzgün bir şekilde yerleştirin ve süreci kesinlikle takip edin. Her bir döküm katmanının arasına iki kat karton koyun. Depolama ve nakliye departmanı. Devir sırasında forkliftin parçalara çarpmasını önleyin, uygun olmayan çatallı taşıma yöntemleri ve aşırı taşıma hızı nedeniyle parçaların çarpmasını önleyin.
1.5.2 Çok kalın ayırma çapaklarını önlemek için ayırma çapaklarını zamanında temizleyin.
2.2 Sebep analizi
2.2.1 Lishell'in 701# deliğinde gözeneklerin göründüğü parçanın delik çapı q26'dır, işlemden sonraki delik çapı p27.9'dur, işleme payı 0.95 mm'dir, işleme payı büyüktür ve gözenekler kolaydır görünmek.
2.3 Sonuç
Sonuç: 701# çekirdek sıcaklığı çok yüksek, derin boşlukta ve egzoz zayıf ve işleme payı çok büyük, bu da 701# deliğin işlemden sonra gözeneklere eğilimli olmasına neden oluyor.
2.4 İyileştirme önlemleri
2.4.1 Çekirdek sıcaklığını azaltmak için 701# deliğine su eklemek üzere tasarlanmış teknik departman; kalıp çizimini değiştirin, egzoz etkisini güçlendirmek için 701# deliğine bir taşma oluğu ekleyin; çekirdek çizimini değiştirin ve 701# delik işleme payını değiştirin 0.9 mm'den 0.7 mm'ye düşürüldü.
Lütfen yeniden basım için bu makalenin kaynağını ve adresini saklayın: Basınçlı Döküm Nedir? Kalıp Döküm İşlemi Nedir?
Minhe Basınçlı Döküm Şirketi kaliteli ve yüksek performanslı Döküm Parçaları üretmeye ve sağlamaya adamıştır (metal döküm parça yelpazesi esas olarak şunları içerir: İnce Duvarlı Döküm,Sıcak Kamara Basınçlı Döküm,Soğuk Oda Döküm), Yuvarlak Servis (Döküm Servisi,Cnc İşleme,Kalıp yapımı,Yüzey İşleme).Herhangi bir özel Alüminyum döküm, magnezyum veya Zamak/çinko döküm ve diğer döküm gereksinimleri bizimle iletişime geçebilirsiniz.
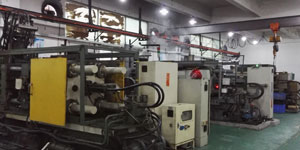
ISO9001 ve TS 16949 kontrolünde, tüm işlemler yüzlerce gelişmiş basınçlı döküm makinesi, 5 eksenli makine ve blasterlerden Ultra Sonic yıkama makinelerine kadar diğer tesisler aracılığıyla gerçekleştirilir. Müşterinin tasarımını gerçeğe dönüştürmek için deneyimli mühendisler, operatörler ve müfettişlerden oluşan ekip.
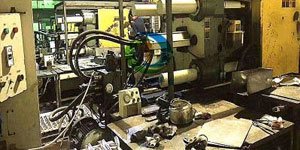
Dökümlerin sözleşmeli üreticisi. Yetenekler, 0.15 lbs'den başlayan soğuk oda alüminyum döküm parçaları içerir. 6 lbs'ye kadar, hızlı değişim kurulumu ve işleme. Katma değerli hizmetler arasında polisaj, titreşim, çapak alma, kumlama, boyama, kaplama, kaplama, montaj ve kalıplama yer alır. Çalışılan malzemeler arasında 360, 380, 383 ve 413 gibi alaşımlar bulunur.
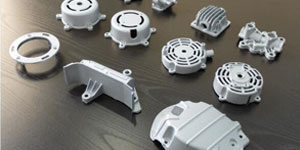
Çinko pres döküm tasarım yardımı/eşzamanlı mühendislik hizmetleri. Hassas çinko dökümlerin özel üreticisi. Minyatür dökümler, yüksek basınçlı dökümler, çok kızaklı kalıp dökümleri, geleneksel kalıp dökümleri, birim kalıp ve bağımsız kalıp dökümleri ve boşluklu sızdırmaz dökümler üretilebilir. Dökümler, +/- 24 inç toleransta 0.0005 inç'e kadar uzunluk ve genişliklerde üretilebilir.
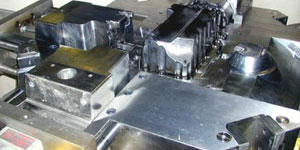
ISO 9001: 2015 sertifikalı döküm magnezyum üreticisi, Yetenekler arasında 200 ton sıcak odaya ve 3000 ton soğuk odaya kadar yüksek basınçlı magnezyum kalıp dökümü, takım tasarımı, cilalama, kalıplama, işleme, toz ve sıvı boyama, CMM özelliklerine sahip tam kalite güvencesi bulunur , montaj, paketleme ve teslimat.
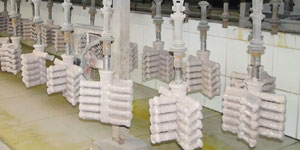
ITAF16949 sertifikalı. Ek Döküm Hizmeti Dahil yatırım dökümleri,kum dökümü,Yerçekimi Döküm, Kayıp Köpük Döküm,Savurma döküm,Vakumlu Döküm,Kalıcı Kalıp Döküm,.Yetenekler arasında EDI, mühendislik yardımı, katı modelleme ve ikincil işleme yer alır.
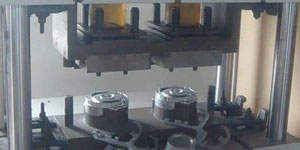
Döküm Endüstrileri Arabalar, Bisikletler, Uçaklar, Müzik aletleri, Deniz Araçları, Optik cihazlar, Sensörler, Modeller, Elektronik cihazlar, Muhafazalar, Saatler, Makineler, Motorlar, Mobilya, Mücevher, Jigler, Telekom, Aydınlatma, Tıbbi cihazlar, Fotoğraf cihazları, Robotlar, Heykeller, Ses ekipmanları, Spor ekipmanları, Aletler, Oyuncaklar ve daha fazlası.
Bundan sonra ne yapmanıza yardımcı olabiliriz?
∇ Ana Sayfaya Git Çin Döküm
→Döküm Parçaları-Ne yaptığımızı öğren.
→ Hakkında İlgili İpuçları Pres Döküm Hizmetleri
By Minghe Döküm Üreticisi |Kategoriler: Faydalı Makaleler |Malzeme Etiketler: Alüminyum Döküm, Çinko Döküm, Magnezyum Döküm, Titanyum Döküm, Paslanmaz Çelik Döküm, Pirinç Döküm,Bronz Döküm,Döküm Videosu,Tarihçe,Alüminyum Döküm |Yorumlar Kapalı