Binek Araç Motorunun Alüminyum Alaşımlı Silindir Kafası için Düşük Basınçlı Döküm Teknolojisi
Maliyet ve mekanik özelliklerin kapsamlı bir şekilde değerlendirilmesine dayalı olarak, alüminyum alaşımı uygulamasının genişletilmesi şu anda binek otomobillerin ağırlığını azaltmanın ve yakıt tüketimini azaltmanın ana yoludur. Örneğin, motor silindir kapağı artık tamamen alüminyum alaşımdan yapılmıştır. Alüminyum alaşımlı silindir kapakları için birçok üretim yöntemi olmasına rağmen, ana üretim süreçleri metal kalıba döküm ve düşük basınçlı dökümdür. Bunlar arasında Avrupa ve Çin daha çok metal kalıp kullanırken, Japonya ve Amerika Birleşik Devletleri daha çok düşük basınçlı döküm kullanıyor.
Yerçekimi metal kalıp dökümü ile karşılaştırıldığında, düşük basınçlı döküm, basınç altında doldurma ve kristal katılaşma nedeniyle iyi şekillendirme kalitesi ve yüksek işlem verimi avantajlarına sahiptir, ancak karmaşık şekillere ve yüksek performans gereksinimlerine sahip silindir kafası dökümleri için karmaşık işlemler vardır, Kontrol gerektirir ileri teknik zorluklar. Bu nedenle, bu makale, düşük basınçlı döküm işleminin teknik avantajlarından tam anlamıyla yararlanmak ve yüksek kaliteli silindir kafası dökümleri üretmek için alüminyum alaşımlı silindir kapaklarının düşük basınçlı döküm teknolojisine ve parametre kontrolünün kilit noktalarına odaklanmaktadır. .
Silindir kapağının düşük basınçlı döküm işleminin kilit noktaları
2.1 Kapı sistemi örneği
Silindir kapağının düşük basınçlı döküm proses planı genellikle bir yükseltici boru ve çok ağırlıklı bölmenin bir şekli olan çoklu kapılar şeklindedir. Örneğin, dört silindirli silindir kafası, iki temsili geçiş sistemine sahiptir, yani, yanma odasının yanına iki veya dört kapı yerleştirilmiştir. Şekil 2, iki kapı işleminin şematik bir diyagramıdır. Bu şema bir kalıp veya iki kalıp için uygundur.
2.2 Alaşımlı malzemeler ve eritme
Alüminyum alaşımlı silindir kapağının malzemesi genellikle ZL105 ve 107 gibi AI-Si-Cu serisi alaşımları seçer. Uzama ve korozyon direnci gerekiyorsa, ZL101 ve ZL104 de kullanılabilir. Yüksek kaliteli erimiş metal elde etmek için, standart işlem, Ar gazı döndürmeli üfleme rafine etme ve modifiye için Sr ekleme ve taneleri rafine etmek için AJ-Ti-B kullanmalıdır.
2.3 Dökme işlemi
2.3.1 Kalıp bakımı
Kalıbın düzenli olarak temizlenmesi ve bakımı, yüksek kaliteli silindir kafası dökümlerinin istikrarlı üretimi ve kalıbın hizmet ömrünün uzatılması için çok önemlidir. Genellikle her 500-700 adet üretildikten sonra kalıp bakımı yapılmalıdır. Ana içerik, kalıbı sökmek, boşluğun yüzey kaplamasını yumuşak bir fırça ile temizlemek ve ejektör çubuğu ile egzoz deliği arasındaki boşluğa giren alüminyum talaşları ve kaplama parçacıklarını çıkarmaktır. , Döküm şeklinin kalitesini, düzgün fırlatma ve pürüzsüz egzozu sağlamak için.
2.3.2 Kaplama
Dökmeden önce kalıp yaklaşık 200°C'ye ısıtılır ve üzerine boya püskürtülür. Silindir kapağının şekli karmaşıktır, bu nedenle farklı kısımlardaki farklı boya kalınlıklarına özel dikkat gösterilmelidir. Genel parçaların kaplama kalınlığı 0.1 --- 0.2 mm arasında kontrol edilir: hassas gereksinimler yüksektir. Örneğin yanma odasının yüzeyi O.OSmn kalınlığında ince parçacıklarla kaplanmalıdır. Yavaş katılaşması gereken kapılar, yükselticiler, iç raylar ve diğer yerler için daha kalın, genellikle yaklaşık 0.5-1 mm olabilir.
2.3.3 Filtre
Filtrenin yerleştirilmesinin amacı, yükseltici tüpteki oksit safsızlıklarının boşluğa girmesini ve laminer dolgu oluşturmasını önlemektir. Ucuz ve etkili galvanizli metal ağ kullanılabilir, telin çapı .4--0.6mm, 1214 ağdır.
2.3.4 Sıcaklık
Erimiş alüminyumun sıcaklığı, silindir kapağının iç kusurları ve görünüm kalitesi üzerinde büyük bir etkiye sahiptir. Dökme derecesi 680-730 aralığında olmalı ve gerçek çalışmadaki sıcaklık sapması 20°C içinde kontrol edilmelidir.
Düşük basınçlı dökümün özelliği, iyi sıralı katılaşma elde etmektir. Bundan sonra, düşük basınçlı dökümde raporun sıcaklığının ılımlı olmasını kontrol etmek önemlidir. İdeal kalıp sıcaklık dağılımı, kapıdan üst kalıba kademeli olarak düşürülür ve her parçanın spesifik yüzey kontrol aralığı elde edilecek şekilde değiştirilir. Yukarıda belirtilen sıcaklık alanı ve silindir kafası dökümlerinin performansının iyileştirilmesi ve üretim döngüsünün kısaltılması, üst kalıp ve yan kalıp üzerinde uygulanmalıdır. sakin ol. Genellikle çok kanallı ayarlar kullanılarak su soğutmalı ve hava soğutmalı olarak ikiye ayrılır, her kanal bağımsız olarak otomatik olarak kontrol edilir (akış ve basınç). Su soğutma, kalıp içinde yüksek sıcaklıktaki buharlaşmanın neden olduğu zayıf su akışı sorununu çözmek için basınçlı besleme su pompası kullanır ve hava soğutması için basınçlı hava kullanılır.
Silindir kapağı birden fazla kapıya sahip olduğundan, iki kapı arasındaki kısa mesafe, kapılar arasındaki döküm parçasının sıcaklığının yükselmesine neden olacak ve kapı ve bu parçanın katılaşma sırası tersine dönecektir. Bu nedenle, gerekli sıcaklık gradyanını elde etmek için bu kısımda yerel cebri soğutma ayarlanmalıdır.
Kalıp ömrü ve güvenliği göz önüne alındığında, dolaylı soğutma ana soğutma yöntemi olmalıdır ve yerel dökümlerin kalınlığının büyük olduğu durumlarda doğrudan soğutma kullanılabilir. Soğutma yoğunluğu için iki yöntem vardır: zaman kontrolü ve sıcaklık kontrolü. Zaman kontrolü, geçen su veya havanın zamanını kontrol etmektir. Bu yöntem basit ve uygulanması kolaydır, ancak doğruluğu yüksek değildir. Sıcaklık kontrolü, soğutma konumunda bir termokupl kurmaktır ve PC, termokupl tarafından ölçülen sıcaklığa göre soğutma suyunu veya havayı açar veya kapatır. Kontrol doğruluğu nispeten yüksektir.
Son yıllarda, katılaşma sayısal simülasyon teknolojisinin gelişimi, silindir kapaklarının düşük basınçlı döküm işleminin optimizasyonu için iyi bir referans sağlamıştır. Farklı koşullar altında katılaşma testi sonuçlarını tam olarak kavrayabilir, döküm işleminin kontrolünü güçlendirebilir ve dökümlerin kalitesini sağlayabilir.
2.3.5 Basınçlandırma süresi
Kapının doldurulmasından katılaşmasına kadar geçen süre, sıcaklıktan büyük ölçüde etkilenen pres süresi olarak adlandırılır. Stabil üretim koşullarında, basınçlandırma süresi silindir kapağının ağırlığına göre değişse de genellikle 2-8dk'da kontrol edilir. Üretim verimliliğinin artırılması açısından tek kalıp, iki parça, iki aşamalı basınçlandırma gibi yöntemler süreyi kısaltmak için kullanılabilir.
2.3.6 Kalıp bırakma süresi
Basınçlandırma süresi gibi, sıcaklıktaki değişikliklerden dolayı değişir. Zaman kısa olduğunda, dökümün deforme olması kolaydır; zaman çok uzun olduğunda, dökümün kalıba sıkışması kolaydır ve çıkarılamaz. Bu nedenle, genellikle basınçlandırma süresinin yaklaşık 1/3'ünde kontrol edilir. Dökümün soğuma hızını arttırmak için kalıp çekilirken önce kalıp ayırma direnci düşük olan yan kalıp, belli bir süre soğuduktan sonra üst kalıp açılabilir.
2.3.7 Basınç eğrisi
Basınçlandırma basıncı, erimiş metalin sıvı doldurma performansını ve besleme etkisini doğrudan etkiler ve basınçlandırma eğrisi, düşük basınçlı döküm proses kontrolünün önemli bir parçasıdır. Basınçlandırma basıncı aşağıdaki formülle hesaplanabilir:
P=γx(1+S/A) x ΔH x 10-2
Yukarıdaki formülde, P-basıncı (MPa), γ-alüminyum sıvı özgül ağırlığı (2.4-2.5), ΔH-alüminyum sıvı yükselme yüksekliği (m), S-kaldırma borusu kesit alanı (m2), A-boşluk çaprazı -kesit alanı ( m2)o
Yükselticinin besleme basıncı genellikle yaklaşık 0.005-0.01MPa'dır. Yüksek basıncın etkisi iyi olsa da, basınç 0.01 Mpa'yı geçerse boyanın soyulmasına neden olur, alüminyum sıvı kalıp havalandırmasını tıkar ve kum çekirdeğine nüfuz eder. Döküm işlemi sırasında kum çekirdeğin yanması sonucu oluşan gazı zamanında boşaltmak çok gereklidir, ancak silindir kapağında kullanılan kum çekirdeği karmaşık bir yapıya sahip olduğundan ve en büyük sayı olduğundan büyük bir sayı ayarlamak zordur. kalıptaki havalandırma deliklerinden. Bu sırada, besleyicinin besleyici basıncını üst sınıra yakın bir düzeye çıkarmak, gazın döküme karışmasını etkili bir şekilde önleyebilir.
Narenciye mağarasındaki sıvı seviyesinin değişmesi, basınç eğrisinin tekrarlanabilirliğini etkiler, bu nedenle narenciye felaketindeki basınç otomatik olarak telafi edilmelidir. Silindir kapağı dökümleri için sensörler, basınç eğrisinin sıfır noktasını I81 doğru şekilde kontrol edecek şekilde ayarlanabilir.
Ayrıca, yükseltici borunun alt ucu ile turuncu koltuk değneğinin altı arasındaki aralık çok kısaysa, çözüm kolayca türbülanslı akış üretecektir. Bu nedenle, çözeltinin kullanımını etkilemeden, yükseltici borunun alt ucu ile turuncu tencerenin tabanı arasındaki mesafe yaklaşık 200 mm'dir.
Döküm kusurları ve karşı önlemler
Tablo 1, düşük basınçlı dökümün genel kusurlarını ve alınması gereken önlemleri listeler. Silindir kapağı gibi karmaşık bir parça için çeşitli parametrelerin dalgalanması dökümün kalitesini etkileyebilir. Bu nedenle, çeşitli kusur nedenlerini açıklığa kavuşturmak için süreç planı, şablon tasarımı, döküm işlemi vb. gibi çeşitli yönlerde ayrıntılı analiz ve araştırma yapmak ve bu temelde ilgili önlemleri almak gerekir.
Sonuç
Şimdiye kadar, alüminyum alaşımlı silindir kafaları, düşük basınçlı döküm için uygun olan birkaç sınırlı otomobil parçasından biridir. Bu nedenle, alüminyum alaşımlı silindir kafalarında yerli düşük basınçlı döküm teknolojisinin üretimini ve uygulamasını genişletmek için yüksek üretim hızı ve iyi iç kalite avantajlarına tam anlamıyla sahip olurlar. Ülkemin otomobil teknolojisinin hızlı gelişimine uyum sağlamak.
Lütfen yeniden basım için bu makalenin kaynağını ve adresini saklayın: Binek Araç Motorunun Alüminyum Alaşımlı Silindir Kafası için Düşük Basınçlı Döküm Teknolojisi
Minhe Basınçlı Döküm Şirketi kaliteli ve yüksek performanslı Döküm Parçaları üretmeye ve sağlamaya adamıştır (metal döküm parça yelpazesi esas olarak şunları içerir: İnce Duvarlı Döküm,Sıcak Kamara Basınçlı Döküm,Soğuk Oda Döküm), Yuvarlak Servis (Döküm Servisi,Cnc İşleme,Kalıp yapımı,Yüzey İşleme).Herhangi bir özel Alüminyum döküm, magnezyum veya Zamak/çinko döküm ve diğer döküm gereksinimleri bizimle iletişime geçebilirsiniz.
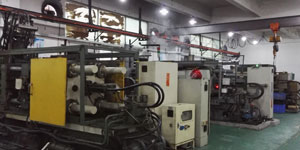
ISO9001 ve TS 16949 kontrolünde, tüm işlemler yüzlerce gelişmiş basınçlı döküm makinesi, 5 eksenli makine ve blasterlerden Ultra Sonic yıkama makinelerine kadar diğer tesisler aracılığıyla gerçekleştirilir. Müşterinin tasarımını gerçeğe dönüştürmek için deneyimli mühendisler, operatörler ve müfettişlerden oluşan ekip.
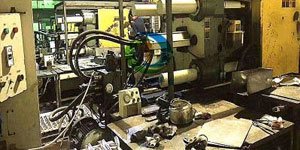
Dökümlerin sözleşmeli üreticisi. Yetenekler, 0.15 lbs'den başlayan soğuk oda alüminyum döküm parçaları içerir. 6 lbs'ye kadar, hızlı değişim kurulumu ve işleme. Katma değerli hizmetler arasında polisaj, titreşim, çapak alma, kumlama, boyama, kaplama, kaplama, montaj ve kalıplama yer alır. Çalışılan malzemeler arasında 360, 380, 383 ve 413 gibi alaşımlar bulunur.
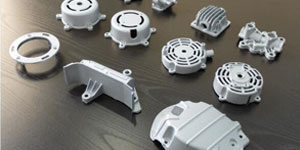
Çinko pres döküm tasarım yardımı/eşzamanlı mühendislik hizmetleri. Hassas çinko dökümlerin özel üreticisi. Minyatür dökümler, yüksek basınçlı dökümler, çok kızaklı kalıp dökümleri, geleneksel kalıp dökümleri, birim kalıp ve bağımsız kalıp dökümleri ve boşluklu sızdırmaz dökümler üretilebilir. Dökümler, +/- 24 inç toleransta 0.0005 inç'e kadar uzunluk ve genişliklerde üretilebilir.
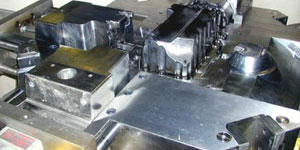
ISO 9001: 2015 sertifikalı döküm magnezyum üreticisi, Yetenekler arasında 200 ton sıcak odaya ve 3000 ton soğuk odaya kadar yüksek basınçlı magnezyum kalıp dökümü, takım tasarımı, cilalama, kalıplama, işleme, toz ve sıvı boyama, CMM özelliklerine sahip tam kalite güvencesi bulunur , montaj, paketleme ve teslimat.
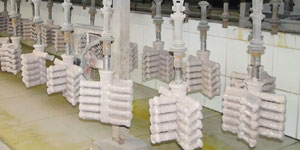
ITAF16949 sertifikalı. Ek Döküm Hizmeti Dahil yatırım dökümleri,kum dökümü,Yerçekimi Döküm, Kayıp Köpük Döküm,Savurma döküm,Vakumlu Döküm,Kalıcı Kalıp Döküm,.Yetenekler arasında EDI, mühendislik yardımı, katı modelleme ve ikincil işleme yer alır.
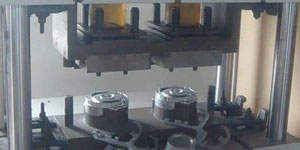
Döküm Endüstrileri Arabalar, Bisikletler, Uçaklar, Müzik aletleri, Deniz Araçları, Optik cihazlar, Sensörler, Modeller, Elektronik cihazlar, Muhafazalar, Saatler, Makineler, Motorlar, Mobilya, Mücevher, Jigler, Telekom, Aydınlatma, Tıbbi cihazlar, Fotoğraf cihazları, Robotlar, Heykeller, Ses ekipmanları, Spor ekipmanları, Aletler, Oyuncaklar ve daha fazlası.
Bundan sonra ne yapmanıza yardımcı olabiliriz?
∇ Ana Sayfaya Git Çin Döküm
→Döküm Parçaları-Ne yaptığımızı öğren.
→ Hakkında İlgili İpuçları Pres Döküm Hizmetleri
By Minghe Döküm Üreticisi |Kategoriler: Faydalı Makaleler |Malzeme Etiketler: Alüminyum Döküm, Çinko Döküm, Magnezyum Döküm, Titanyum Döküm, Paslanmaz Çelik Döküm, Pirinç Döküm,Bronz Döküm,Döküm Videosu,Tarihçe,Alüminyum Döküm |Yorumlar Kapalı