Matkap ve Nikelin 4Cr5Mo2V Pres Döküm Kalıp Çeliğinin Termal Hasar Direnci Üzerindeki Etkisi
4Cr5 Mo2V, yaygın olarak kullanılan bir kalıp döküm kalıp çeliğidir. Kalıp döküm alüminyum alaşımı sürecinde, erimiş alüminyumun aşınması ve yapışması nedeniyle, kalıp, termal yorulma ve termal eriyik kaybı gibi termal hasara uğrayacak ve bu da sertliğinde bir azalmaya ve hatta erken arızaya neden olacaktır.
Nikel veya kuruluk, alüminyum alaşımlı kalıp döküm kalıplarının termal hasar direncini iyileştirip iyileştirmediğini incelemek için, %4 Ni ve %5 Co (kütle oranı) içeren 2Cr4 Mo5V çelik ve 2Cr1Mo1V çelik test blokları hazırlanmış ve daha sonra kakılmıştır. söndürme ve temperleme. Döküm kalıbının sabit kalıbında, 12°C sıcaklığa sahip ADC800 alüminyum alaşımı daha sonra 200 ila 1,000 kez kalıp dökümü yapıldı ve test bloğunun makro morfolojisi ve yüzey sertliği incelendi.
Sonuçlar, alüminyum alaşımın 1,000 kez kalıp dökümünden sonra, 4Cr5Mo2V çelik test bloğunun alüminyuma en şiddetli şekilde yapıştığını ve çok az ağ benzeri çatlak ürettiğini gösteriyor; Ni içeren çelik test bloğu alüminyuma hafifçe yapışmış ve Co içeren çelik test bloğu en az alüminyuma yapışmıştır, bu da %1 Co 4Cr5Mo2V çelik içeriğinin döküm alüminyum alaşımlarına karşı en iyi termal hasar direncine sahip olduğunu gösterir. Ayrıca, alüminyum alaşımın kalıp dökümünden önceki sertliğe kıyasla, 1,000 kez kalıp dökümden sonra, 4Cr5Mo2V çelik, nikel içeren ve kuru içeren 4Cr5Mo2V çelik numunelerin yüzey sertliği 2.8, 1.8 ve 1.4 HRC azaldı, yani, çoklu kalıp döküm alüminyum alaşımları. Nikel içeren ve kuru 4Cr5Mo2V çeliğinin yüzey sertliği üzerindeki olumsuz etki, alüminyum sıvı erozyon direncini iyileştirmek için faydalı olan Co ve Ni'nin katı çözelti güçlendirme etkisi ile ilgili olan 4Cr5Mo2V çeliğinden daha azdır. kalıp ve kalıbı termal hasara karşı daha az duyarlı hale getirin.
Alüminyum alaşımlı kalıp döküm, karmaşık bir yüksek sıcaklık ve yüksek basınç işlemidir. Alüminyum alaşımlı kalıp döküm kalıplarının termal hasar (termal yorulma ve termal kayıp dahil) performansını etkileyen birçok faktör vardır. Bunlar arasında, sıcak iş kalıp çeliğinin bileşimi özellikle önemlidir.
Normal şartlar altında, çatlama ve plastik deformasyon nedeniyle döküm kalıbının arızalanması önlenebilir. Kalıp çatlaması genellikle kazara mekanik aşırı yüklenmeden veya termal aşırı yüklenmeden kaynaklanır ve ciddi stres konsantrasyonuna neden olur. Kalıp döküm kalıplarının erken termal yorulma çatlaması ve kaynak kaybı (yüzey termal hasarı) ana arıza modlarıdır ve ikisi genellikle birbirini etkiler. 4Cr5Mo2V çelik, iyi aşınma direnci ve plastik deformasyon direnci ile yaygın olarak kullanılan bir sıcak iş kalıp çeliğidir. Matkap ve nikel, çeliğin mukavemetini ve sertliğini etkili bir şekilde artırabilen ve termal hasara direnme üzerinde belirli bir etkiye sahip olan yaygın olarak kullanılan alaşım elementleridir. Bu nedenle, 4Cr5Mo2V çeliği, %4 Ni ve %5 Co içeren 2Cr1Mo1V (kütle oranı, aşağıda aynı) incelenmiştir. Çeliğin erimiş alüminyum hasarına karşı direnci, fiili üretimi yönlendirmek için büyük önem taşımaktadır.
Bununla birlikte, ağızdan önce döküm kalıp çeliğinin termal hasarını incelemeye yönelik yöntemlerin çoğu, ısıtma ve soğutmayı simüle etmektir. Kalıp çelik numunesi, erimiş alüminyumla doğrudan temas etmez ve kalıp çelik numunesinin doğrudan endüksiyonla ısıtılması gibi erimiş alüminyumun temizleme etkisini içermez. -A. Bu yazıda, ADC12 alüminyum alaşımının kalıp döküm testini gerçekleştirmek için üç bileşenli kalıp çeliği test blokları hazırlanmış ve kalıp döküm kalıbına gömülmüştür. Erimiş alüminyumun hasar performansı.
1.Test Materyalleri ve Yöntemleri
1.1 Test Malzemeleri
4Cr5Mo2V çeliğinin, %4 Ni içeren 5Cr2Mo1V çeliğinin (bundan sonra 4Cr5Mo2V + Ni çeliği olarak anılacaktır) ve %4 Co içeren 5Cr2 Mo1V çeliğinin (bundan sonra 4Cr5Mo2V + Co çeliği olarak anılacaktır) kimyasal bileşimi Tablo 1'de gösterilmiştir. ADC12 ile döküm Alüminyum alaşımının kimyasal bileşimi Tablo 2'de gösterilmektedir.
Tablo 1 İncelenen döküm kalıp çeliklerinin kimyasal bileşimleri (kütle oranı) % | |||||||
Malzeme | C | Cr | Mo | V | Co | Ni | Si |
4Cr5Mo2V çelik | 0.39 | 4.65 | 2. 21 | 0.46 | - | - | 0. 23 |
4Cr5Mo2V+Ni çelik | 0.38 | 4.72 | 2.34 | 0. 51 | - | 1.02 | 0. 21 |
4Cr5Mo2V+Co çelik | 0.41 | 4.67 | 2.40 | 0.48 | 1.03 | - | 0. 24 |
Tablo 2 ADC12 Alüminyum Alaşımının Kimyasal Bileşimi % | |||||||||
Eleman | Cu | Mg | Mn | Fe | Si | Zn | Ti | Pb | Sn |
Kalite Puanı | 1.74 | 0.22 | 0.16 | 0.76 | 10.70 | 0.87 | 0.064 | 0.035 | 0. 010 |
1.2 Test Yöntemi
Tavlanmış 4Cr5Mo2V çeliği, 4Cr5Mo2V + Ni çeliği ve 4Cr5Mo2V + Co çeliği, Şekil 1'de gösterildiği gibi test blokları halinde işlendi. Vakumla su verme işleminden sonra, sertliği yaklaşık 47 HRC olan iki kez temperlendiler ve oksit tortusunu gidermek için ince bir şekilde öğütüldüler.
Test bloğunun grup numarası, sabit kalıbın oluğuna gömülüdür ve döküm alüminyum alaşımının boşluğu, Şekil 2'de gösterildiği gibi hareketli kalıpta ayarlanır. 500 tonluk yatay soğuk odalı bir kalıp döküm makinesi. ve ADC12 alüminyum alaşımlı levhanın kalıp döküm testi için kendinden tasarlanmış bir kalıp kullanıldı ve alüminyum alaşımı yeniden kullanıldı. Testi hızlandırmak için erimiş alüminyumun sıcaklığı 800°C daha yüksektir (genellikle, ADC12 alüminyum alaşımının döküm sıcaklığı (650 120)°C'dir). Erimiş alüminyumun sıcaklığı 800 ℃ olduğundan Fe-A1 intermetalik bileşiğin erime noktasına ulaşmaz, sonuçta ortaya çıkan bileşik düştükten sonra erimiş alüminyumda safsızlıklar olarak bulunacaktır. Erimiş alüminyumun tekrar tekrar kullanılması, safsızlıkların artmasına ve alüminyumun güçlendirilmesine neden olacaktır. Sıvının ovma etkisi, böylece testi hızlandırır.
Döküm testinden sonra, test bloğunun yüzeyindeki alüminyum yapışma olgusunu gözlemlemek için bir stereo mikroskop kullanıldı; alüminyum yapışma derecesini ve test bloğunun yüzeyinde çatlak olup olmadığını daha fazla gözlemlemek için bir ultra-alan derinliği mikroskobu kullanıldı.
2.Test Sonuçları ve Analizi
2. 1 Test Bloğunun Yüzey Morfolojisi
2.1.1 Yüzey Yapıştırma Alüminyum
Şekil 3, basınçlı döküm olmadan ve 600,1000 kez pres dökümden sonra üç çelik test bloğunun yüzey morfolojisini göstermektedir. Şekil 3'te (b, e, h) 600 kez pres dökümden sonra 4Cr5Mo2V çelik test bloğunun en ciddi alüminyum yapışmasına sahip olduğu görülebilir.
4Cr5Mo2V + Co çelik test bloğu en az alüminyuma yapışır. Şekil 3 (c, f, i), üç test bloğunun yüzeyindeki alüminyum yapışmasının 1,000 kez pres dökümden sonra arttığını göstermektedir. 4Cr5Mo2V çelik test bloğunun yüzeyi belirgin alüminyum yapışmasına sahipken, diğer iki test bloğu hafif alüminyum yapışmasına sahiptir. 4Cr5Mo2V + Co çelik testi Alüminyum yığını en az ve tek tiptir, bu da elmas içeren 4Cr5Mo2V çeliğinin sıvı alüminyum hasarına karşı en iyi dirence sahip olduğunu, 4Cr5Mo2V çeliğinin ise en kötü olduğunu gösterir. Matkap ve nikel elemanlarının eklenmesi, kalıp çeliği 9-10'un yüksek sıcaklık sertliğini stabilize etmek için faydalıdır ve erimiş alüminyum ile tekrarlanan temas sırasında yüzeyin "yumuşaması" kolay değildir, bu nedenle sıvı alüminyum erozyon direnci daha iyidir ve alüminyum yapışması daha iyidir. hafiftir. Döküm testi sırasında, erimiş alüminyum test bloğu ile temas etmek için boşluğa girer ve test bloğunun düzensiz yapısı, işleme kusuru alanı ve diğer yerel alanlar alüminyuma hafifçe yapışacaktır. Alüminyum bağlı alandaki alüminyum, Fe oluşturmak üzere çelik ile reaksiyona girecektir.} Al kırılgan ara bileşik, bu, yüksek basınçlı alüminyum sıvının ovma altında kırılıp soyularak kalıp yüzeyinde çukurlara neden olur ve daha fazlası alüminyum sıvının ovma altında ciddi alüminyum yapıştırma.
2.1.2 Yüzey Çatlakları
Şekil 4, 4Cr5Mo2V çelik, 4Cr5Mo2V + Ni çelik ve 4Cr5Mo2V + Co çelik numunelerinin 1,000 kez pres dökümden sonra süper alan morfolojisi derinliğini göstermektedir. Şekil 4(a)'dan, 4 Cry Mot V çelik test bloğunun yüzeyinde neredeyse net bir şekilde dağılmış az sayıda mikro çatlak olduğu görülebilir. Yapıştırılan alüminyum ve erimiş alüminyum, Fe.} Al bileşikleri oluşturmak üzere çelikle reaksiyona girer. Fe.} Al'nin termal genleşme katsayısı matrisinkinden farklıdır, bu da yapıştırılan alüminyum ve Fe.} Al ve bileşiklerde çok az miktarda mikro çatlaklara neden olur. Erimiş alüminyumun ovma etkisi mikro çatlakların yayılmasına neden olur ve erimiş alüminyum çatlağa nüfuz eder ve ayrıca Fe2Al bileşikleri oluşturmak için matris ile reaksiyona girer. Müteakip tekrarlanan kalıp döküm işleminde, test bloğunun yüzeyindeki Fe.} Al bileşikleri, çukurlar oluşturmak üzere sıyrılır. Dekapaj ve ultrasonik temizlemeden sonra, test bloğunun yüzeyi, ağ benzeri alüminyum sıvı temizleme özelliklerine benzer göründü. Şekil 4 (b, c), 4Cr5Mo2V + Co çelik ve 4Cr5Mo2V + Ni çelik test bloklarında çatlak olmadığını gösterir, bu da %1 matkap veya molibden ilavesinin yalnızca alüminyumun yüzey yapışmasını azaltmakla kalmayıp aynı zamanda azaltabileceğini gösterir. Kalıbın çatlama eğilimi ve alüminyum direncini artırır Sıvı hasarı performansı. Nikel ve elmas karbür oluşturucu olmayan elementlerin eklenmesi, kalıbın yüksek sıcaklıktaki sertliğini iyileştirebilir ve elmas ayrıca tavlama işlemi sırasında molibden karbürün dağılmasını ve çökelmesini teşvik edebilir ve çökelme sertleştirme etkisini 'z-} geliştirebilir. 3. Ling Qian ve arkadaşlarının araştırması. döküm kalıp çeliğine östenit stabilize edici elementlerin eklenmesinin stres konsantrasyonunu azaltabileceğini göstermiştir. Hem matkap hem de nikel, ostenit bölgesini genişleten elementlerdir, bu nedenle 4Cr5Mo2V + Ni çelik ve 4Cr5Mo2V + Co çelik basınçlı döküm kalıp yüzeyleri çatlamaya meyilli değildir.
Gerçek kalıp döküm işleminde erimiş alüminyum kalıba karşı çok güçlüdür. Fe-A1 faz diyagramına göre, çelik ve erimiş alüminyumun reaksiyonu ile oluşan Fe-Al intermetalik bileşikleri, çoğunlukla kırılgan olan FeAlz, Fez A15, FeA13 vb.'dir. Alüminyum alaşımının Al açısından zengin fazı, matristen ayrılın ve erimiş alüminyumun ovma altında erimiş alüminyuma girin, kalıbın yüzeyinde çukurlar bırakın. Alüminyum alaşımının bir kısmı ve kalıp çukurlarının kombinasyonu nispeten güçlüdür ve düşmez ve ayrıca Fe Al bileşikleri oluşturur. Alüminyum, Fe.} Al ve oraya yapışan bileşikler soğutma sırasında mikro çatlaklara eğilimlidir. Kalıp döküm levhası daha az sıvı alüminyuma sahiptir, bu nedenle daha hızlı katılaşır ve kalıp ile sıvı alüminyum arasındaki reaksiyon daha yavaştır. Bu nedenle, Fe ve Al'ın reaksiyonu nedeniyle test bloğunun yüzeyinde daha az çukur bulunur ve alüminyum sıvısının erozyonu ile daha fazla yapışkan alüminyum üretilir.
2. 2 Yüzey Sertliği
Tablo 3, farklı kalıp döküm zamanlarından sonra üç kalıp çeliği test bloğunun yüzey sertliğinin ortalama değeridir. Tablo 3'teki veriler, üç tür test bloğunun yüzey sertliğinin hepsinin biraz azaldığını göstermektedir. Döküm kalıplarının sayısı arttıkça, test bloğunun tekrarlanan temperlenmesine eşdeğerdir, bu nedenle sertlik azalır. 1,000 kez kalıp dökümden sonra, 4Cr5Mo2V + Co çelik test bloğunun sertliği 1.4 HRC olan en küçük düşüşe sahiptir; 4Cr5Mo2V çelik test bloğu en belirgin düşüşe sahiptir.
Açıkçası, 2 HRC düştü; 8Cr4Mo5V + Ni çelik test bloğunun yüzey sertliği 2 HRC düştü. Kararlı kalıp sertliği, alüminyum yapışmasını azaltmak için faydalıdır, yani kalıp dökümünün termal hasarına direnmek faydalıdır.
Tablo 3 Farklı zamanlar için kalıp dökümden sonra test bloklarının yüzey sertliği % | ||||||
Malzeme | Kalıp Döküm Yok | 200 Times | 400 Times | 600 Times | 800 Times | 1000 Times |
4Cr5Mo2V çelik | 48.6 | 48.4 | 48.1 | 47.2 | 46.9 | 45.8 |
4Cr5Mo2V+Ni çelik | 47.5 | 47.4 | 47.2 | 46.8 | 46.9 | 46.1 |
4Cr5Mo2V+Co çelik | 47.7 | 47.5 | 47.1 | 46.5 | 46.2 | 45.9 |
Kalıp çeliğinin uzun bir süre temperlenmesinden sonra martensit ayrışır ve ikincil karbürler daha kaba hale gelir, bu da yüzey sertliğinde bir azalmaya neden olur. Hem matkap hem de nikel, çelik katı çözeltisinin '5 ila' 8'i güçlendirmesini sağlamak için Fe atomlarının yerini alabilen karbür oluşturucu olmayan elementlerdir, böylece kalıp daha yüksek yüksek sıcaklık mukavemetine sahip olur ve tekrarlanan hızlı ısıtma ve soğutmadan sonra daha yüksek sertliği korur. Çin Döküm Birliği, su verilmiş ve temperlenmiş Cr-Mo-V-Ni çeliğinde element dağılımını inceledi ve temperleme işlemi sırasında Ni elementlerinin karbürler etrafında zenginleşeceğini ve böylece ferrit etrafındaki karbon atomlarını engellediğini buldu. karbürler Karbürlerin sürekli difüzyonu, karbür kabalaşmasının aktivasyon enerjisini arttırır, karbürlerin büyümesini engeller, böylece nikel içeren 4Cr5Mo2V çeliğinin sertlik düşüşünü azaltır ve erimiş alüminyum hasarına karşı direncini artırır.
Çin Döküm Birliği, %1 Ni içeren ve Ni içermeyen kalıp çeliğinin termal kararlılığını ve mikroyapı değişikliklerini inceledi ve termal kararlılık testinin sonraki aşamasında nikelin kalıp çeliğinin sertliğini yavaşlatacağını ve böylece çelik daha iyi termal olarak kararlı Seks. Delme, ostenit faz bölgesini genişleten bir unsurdur. 4Cr5Mo2V çeliğine matkap eklemek, östenitleme işlemi sırasında karbürlerin çözünmesini teşvik edebilir, östenitin karbon içeriğini artırabilir ve östenitin stabilitesini artırabilir, böylece tutulan östenit miktarını artırabilir. temperleme işlemi sırasında molibden karbürün dağılmasını ve çökelmesini teşvik eder ve çökelme sertleştirme etkisini z'-1 arttırır.
Nikel ve matkabın matris üzerindeki güçlendirici etkisi, erimiş alüminyumun tekrar tekrar yıkanmasından sonra kalıp çelik test bloğunun hala daha yüksek bir yüzey sertliğine sahip olmasını sağlar, böylece erozyona karşı daha dirençli olur, bu da test bloğunun direncini arttırmada faydalıdır. erimiş alüminyumun zararına. Test bloğunun yüzey sertliği ve alüminyum yapışma derecesi de gösterir (bkz. Şekil 3, Tablo 3): Delinmiş 4Cr5 Mo2V çelik test bloğu, 1,000 kez kalıp dökümden sonra en az yüzey çukuruna ve alüminyum yapışmasına sahiptir, yani, alüminyum sıvı hasarına karşı direnç en iyisidir. Bu nedenle, çeliğe %1 Co eklenmesinin güçlendirme etkisi, her ikisi de kalıp çeliğinin anti-alüminyum hasar performansını iyileştirmeye elverişli olan %1 Ni eklemekten daha fazladır.
3.Conclusion
- Alüminyum alaşımı 1 kez pres dökümünden sonra, matkaplı 000Cr4 Mo5V çelik numunesi en az alüminyumu ve 2Cr4Mo5V çelik numunesi en fazla alüminyumu yapıştırır, yani matkaplı 2Cr4 Mo5V çeliği en iyi termal hasar direncine sahiptir.
- Alüminyum alaşımı 1,000 kez pres dökümünden sonra, 4Cr5Mo2V çelik, 4Cr5Mo2V +Ni çelik ve 4Cr5Mo2V + Co çelik numunelerin yüzey sertliği 2.8, 1.8 ve 1.4 HRC azaldı, yani nikel veya matkap ilavesi Termal hasar direncini önemli ölçüde artırabilir 4Cr5Mo2V döküm kalıp çeliğinden.
Lütfen yeniden basım için bu makalenin kaynağını ve adresini saklayın: Matkap ve Nikelin 4Cr5Mo2V Pres Döküm Kalıp Çeliğinin Termal Hasar Direnci Üzerindeki Etkisi
Minhe Basınçlı Döküm Şirketi kaliteli ve yüksek performanslı Döküm Parçaları üretmeye ve sağlamaya adamıştır (metal döküm parça yelpazesi esas olarak şunları içerir: İnce Duvarlı Döküm,Sıcak Kamara Basınçlı Döküm,Soğuk Oda Döküm), Yuvarlak Servis (Döküm Servisi,Cnc İşleme,Kalıp yapımı,Yüzey İşleme).Herhangi bir özel Alüminyum döküm, magnezyum veya Zamak/çinko döküm ve diğer döküm gereksinimleri bizimle iletişime geçebilirsiniz.
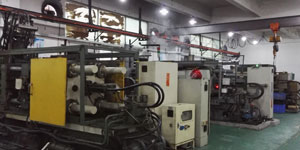
ISO9001 ve TS 16949 kontrolünde, tüm işlemler yüzlerce gelişmiş basınçlı döküm makinesi, 5 eksenli makine ve blasterlerden Ultra Sonic yıkama makinelerine kadar diğer tesisler aracılığıyla gerçekleştirilir. Müşterinin tasarımını gerçeğe dönüştürmek için deneyimli mühendisler, operatörler ve müfettişlerden oluşan ekip.
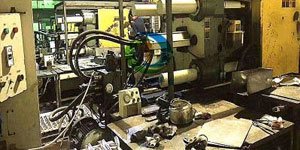
Dökümlerin sözleşmeli üreticisi. Yetenekler, 0.15 lbs'den başlayan soğuk oda alüminyum döküm parçaları içerir. 6 lbs'ye kadar, hızlı değişim kurulumu ve işleme. Katma değerli hizmetler arasında polisaj, titreşim, çapak alma, kumlama, boyama, kaplama, kaplama, montaj ve kalıplama yer alır. Çalışılan malzemeler arasında 360, 380, 383 ve 413 gibi alaşımlar bulunur.
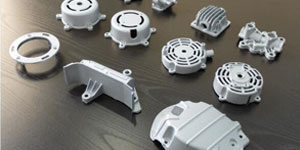
Çinko pres döküm tasarım yardımı/eşzamanlı mühendislik hizmetleri. Hassas çinko dökümlerin özel üreticisi. Minyatür dökümler, yüksek basınçlı dökümler, çok kızaklı kalıp dökümleri, geleneksel kalıp dökümleri, birim kalıp ve bağımsız kalıp dökümleri ve boşluklu sızdırmaz dökümler üretilebilir. Dökümler, +/- 24 inç toleransta 0.0005 inç'e kadar uzunluk ve genişliklerde üretilebilir.
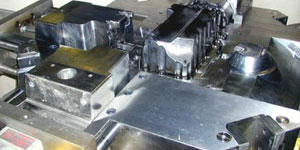
ISO 9001: 2015 sertifikalı döküm magnezyum üreticisi, Yetenekler arasında 200 ton sıcak odaya ve 3000 ton soğuk odaya kadar yüksek basınçlı magnezyum kalıp dökümü, takım tasarımı, cilalama, kalıplama, işleme, toz ve sıvı boyama, CMM özelliklerine sahip tam kalite güvencesi bulunur , montaj, paketleme ve teslimat.
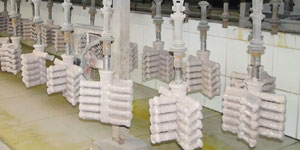
ITAF16949 sertifikalı. Ek Döküm Hizmeti Dahil yatırım dökümleri,kum dökümü,Yerçekimi Döküm, Kayıp Köpük Döküm,Savurma döküm,Vakumlu Döküm,Kalıcı Kalıp Döküm,.Yetenekler arasında EDI, mühendislik yardımı, katı modelleme ve ikincil işleme yer alır.
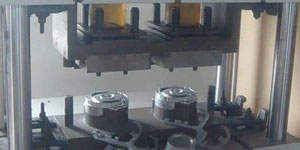
Döküm Endüstrileri Arabalar, Bisikletler, Uçaklar, Müzik aletleri, Deniz Araçları, Optik cihazlar, Sensörler, Modeller, Elektronik cihazlar, Muhafazalar, Saatler, Makineler, Motorlar, Mobilya, Mücevher, Jigler, Telekom, Aydınlatma, Tıbbi cihazlar, Fotoğraf cihazları, Robotlar, Heykeller, Ses ekipmanları, Spor ekipmanları, Aletler, Oyuncaklar ve daha fazlası.
Bundan sonra ne yapmanıza yardımcı olabiliriz?
∇ Ana Sayfaya Git Çin Döküm
→Döküm Parçaları-Ne yaptığımızı öğren.
→ Hakkında İlgili İpuçları Pres Döküm Hizmetleri
By Minghe Döküm Üreticisi |Kategoriler: Faydalı Makaleler |Malzeme Etiketler: Alüminyum Döküm, Çinko Döküm, Magnezyum Döküm, Titanyum Döküm, Paslanmaz Çelik Döküm, Pirinç Döküm,Bronz Döküm,Döküm Videosu,Tarihçe,Alüminyum Döküm |Yorumlar Kapalı