Alüminyum Alaşımlı Kabuk Döküm Kalıplarının Tasarım Detayı
Bu makale ilk olarak alüminyum alaşımlı kabuğun yapısını ve kalıp döküm sürecini analiz eder ve alüminyum alaşımlı kabuk kalıp döküm kalıbının tasarımını tamamlamak için UG yazılımını kullanır. Uygulama ile kanıtlanmış, tasarlanan kalıp döküm makul, elde edilen dökümün yüzeyi pürüzsüz ve temiz ve ürün kalitesi gereksinimleri karşılıyor.
Alüminyum alaşımlı arka kabuğun kalıp döküm parçalarının yapısının ve sürecinin analizi
- 1.1 Döküm yapısı Şekil 1'den görülebilir ki, arka kabuk doldurma kapağı döküm yapısı nispeten basittir, döküm duvar kalınlığı temelde tekdüzedir, iki döküm deliği vardır, ancak döküm deliğinin duvarı biraz daha kalın olduğundan, sıcaktır. Noktaların görünmesi kolaydır, Döküm parçaların genel duvar kalınlığı nispeten tekdüzedir. Duvar kalınlığını seçerken çeşitli faktörler göz önünde bulundurulmalıdır: kalıp döküm yapısı, malzeme özellikleri ve tasarlanan kalıp döküm işlemi. Sadece ince duvarlı veya tek tip duvar kalınlıkları tüm yönleri karşılayabilir. talep etmek.
- 1.2 Dökümün dış kenarının minimum duvar kalınlığı. İyi döküm şekillendirme koşulları, belirli bir dış kenar duvar kalınlığı gerektirir. Kenar duvar kalınlığı s ile derinlik h arasındaki ilişki s≥(1/4~1/3)hmm'dir. h<4.5 mm olduğunda, s≥1.5 mm.
- 1.3 Döküm malzemesi Döküm malzemesi, döküm alüminyum alaşımıdır, kalite YZAlSi9Cu4, çekme mukavemeti 240MPa, Brinell sertliği 85HBS ve ortalama büzülme oranı %0.6'dır. Seçilen alaşım, iyi döküm özellikleri sağlar ve özellikle basınçlı döküm için uygundur.
- 1.4 Döküm fileto yarıçapı Erimiş metal akışının daha düzgün ve gazı daha kolay boşaltmasını sağlamak için yapı, dökme filetolar kullanacak şekilde tasarlanmıştır ve yapının keskin köşelerini değiştirmek için filetoların kullanılması da çatlakları önleyebilir. Tasarlanan yapının yuvarlatılmış köşelerinin yarıçapı, yapının duvar kalınlığına bağlıdır ve aralık genellikle 0.5 ila 1 mm'dir.
- 1.5 Çekim açısı, birçok faktörün kapsamlı bir şekilde dikkate alınmasıyla seçilmelidir: döküm geometrisi (derinlik, duvar kalınlığı, boşluk veya maça yüzeyi), pürüzlülük, işleme tane yönü, vb. Yukarıdaki faktörler dikkate alınarak, kabuk kalıptan çıkarma eğiminin tasarımı döküm: dış yüzeyde α=30' ve iç yüzeyde β=1°.
Döküm proses parametre tasarımı
2.1 Pres döküm makinesi seçimi Bir pres döküm makinesi seçerken, önce sıkıştırma kuvveti belirlenmelidir. Sıkıştırma kuvvetinin iki işlevi vardır: biri, ayırma yüzeyini kilitleme amacına ulaşmak için karşı basıncı dengelemek için kullanılır; diğeri ise hedef boyutsal doğruluğa ulaşma amacına ulaşmak için erimiş metalin sıçramasını önlemektir. Tasarlanan dökümde kısmi genleşme kuvveti yoktur, çünkü bu kalıbın yan maça çekmesi yoktur (kalıp dökümünde yan delikler ve alttan kesikler yoktur). Bu nedenle, F kilidi ≥ KF ana=1.25×1288.352=1610.44kN. Yukarıdaki hesaplamaya göre, sıkıştırma kuvvetinin değeri ve dökümün ağırlığı elde edilir. Bu iki ana faktöre göre, döküm makinesi seçilir ve son seçilen model: yatay soğuk oda döküm makinesi (2500kN)——— J1125 tipi, ana parametreler:
- ①Maksimum metal dökme hacmi———3.2Kg,
- ②Kalıp kalınlığı————250~650mm,
- ③Hareketli kalıp oturma plakası stroku————400mm,
- ④Enjeksiyon kuvveti—— —143~280kN.
2.2 Kalıp döküm basıncı Kalıp döküm basıncı, kalıp döküm işlemindeki ana parametrelerden biridir. Bu nedenle, sıvı metalin basınç değişimi sırasındaki basınç değişimini kavramak büyük önem taşımaktadır. kalıp döküm ve kalıp döküm işleminin her aşamasında basıncı makul bir şekilde kontrol etmek için:
- ① Nitelikli dökümler elde edin—— —Yoğun organizasyon, net anahat;
- ②Özgül enjeksiyon basıncının ilk hesaplaması — Seçilen enjeksiyon kuvvetine göre hesaplayın. Spesifik enjeksiyon basıncı ayrıca kalıp boşluğu alanı, dökümün duvar kalınlığı, erimiş metal süreci ve diğer faktörlerle de ilgilidir. Tasarlanan kalıbın spesifik parametreleri ve başlangıç değeri birleştirilerek, bu kalıp döküm kalıbının enjeksiyon spesifik basıncı son olarak 90MPa'ya ayarlanır.
2.3 Döküm hızı Döküm hızı seçiminin iki yönü vardır: enjeksiyon hızı seçimi ve doldurma hızı seçimi. Dökümün iç ve dış kalitesini ve kontur tanımını doğrudan belirleyen iki hızın seçimi çok önemlidir. Dolum hızı seçilirken dikkate alınması gereken faktörler:
- ①Döküm boyutu,
- ②Döküm yapısının karmaşıklığı,
- ③Döküm için seçilen alaşımın cinsi,
- ④Enjeksiyon basıncı seviyesi.
Özel seçenekler:
- ①Doldurulması daha kolay olan dökümler --- basit duvar kalınlığına veya daha yüksek iç kalite gereksinimlerine sahip dökümler, şunları seçin: düşük hız, yüksek özgül basınç, büyük kapı;
- ②Hızlı doldurma gereklidir --- karmaşık ince duvarlı veya Daha yüksek yüzey kalitesi gereksinimleri olan dökümler için şunu seçin: yüksek hız, yüksek özgül basınç. Kapsamlı değerlendirme, bu döküm parçasının belirli özelliklerine göre yapı nispeten basittir, orta hızı seçin, aralık 20 ~ 90m/s'dir.
2.4 Kalıp döküm süresi, gerekli sürenin üç bölümünden oluşan kalıp döküm süresini belirler: doldurma süresi, tutma süresi ve basınçlı döküm parçasının kalıp döküm kalıbında kaldığı süre. Bu sonucu elde etmek için birkaç faktör bir araya geldi: basınç, hız, sıcaklık, erimiş metal özellikleri, ayrıca döküm yapısı (esas olarak duvar kalınlığı ve hacmi) ve kalıp yapısı (özellikle yolluk sistemi ve tahliye sistemi) ve diğer faktörler. Doldurma süresi çoğunlukla 0.01 ile 0.2 sn arasındadır. Uzunluk, dökümün boyutuna ve yapının karmaşıklığına göre belirlenir: basit bir yapıya ve büyük bir hacme sahip bir döküm, nispeten uzun bir doldurma süresi gerektirir; daha karmaşık bir yapıya ve daha küçük et kalınlığına sahip bir döküm, kısa bir süre gerektirir. Pratik testlerden sonra, doldurma süresi, bu yazıda tasarlanan orta ve küçük alüminyum alaşımlı dökümler için makul olan yaklaşık 0.2 s'ye ayarlanır. Tutma basıncı süresinin işlevi şudur: enjeksiyon zımbası, katılaşmamış metale basınç uygulamak için yeterli zamana sahiptir, böylece kristalizasyon işlemi basınç altında gerçekleştirilebilir, bu da beslemeyi arttırır ve başarılı bir şekilde yoğun bir yapı elde eder. Süreyi etkileyen faktörler: seçilen alaşımın erime noktası, kristalleşme sıcaklık aralığı ve dökümün et kalınlığı. Yüksek erime noktalı, geniş aralıklı ve geniş duvar kalınlığına sahip dökümler, 2~3sn gibi uzun bir süre gerektirir; Belirlenen süre çok kısa olduğunda büzülme meydana gelir ancak bekletme süresi uzarsa önemli bir etkisi olmaz. 1~2s genel tutma süresi aralığıdır. Bu tasarımdaki dökümün ortalama et kalınlığı 3 mm'dir. Yapısı ve alaşım özellikleri göz önünde bulundurularak bekletme süresi olarak 3s seçilmiştir. 2.5 Kalıp döküm sıcaklığı Nitelikli dökümler sağlamak için ana proses parametreleri – erimiş metalin döküm sıcaklığı ve kalıbın çalışma sıcaklığı. Bunu etkileyen birçok faktör vardır: dökümün yapısı, et kalınlığı, doldurma basıncı, hız ve alaşım türleri. Döküm sıcaklığının makul bir aralıkta stabil olmasını ve iyi doldurma koşulları sağlamasını sağlamak için yukarıdaki parametreleri kapsamlı bir şekilde göz önünde bulundurmak gerekir. Dökme sıcaklığı makul bir aralıkta değilse, ürünün kalitesi düşecek ve hatta niteliksiz olacaktır:
①Aşırı dökme sıcaklığı — soğutma sırasında aşırı büzülmeye neden olur, ürün çatlaklara, daha büyük tanelere ve zayıf mekanik Performansa eğilimlidir ve hatta kalıba yapışmasına neden olur, kalıp ömrünü kısaltır;
② Çok düşük dökme sıcaklığı, soğuk bariyer, yüzey deseni ve yetersiz dökme gibi kusurlara neden olur. Kaliteli döküm elde etmek için döküm sıcaklığının yanı sıra basınç, döküm kalıbı sıcaklığı, dolum hızı ve döküm için seçilen alaşım da aynı zamanda dikkate alınmalıdır. Kalıp döküm parçalar alüminyum-silikon alaşımından yapılmıştır. Akışkanlığına ve kalıp özelliklerine göre, kalıp döküm sıcaklığı olarak 620℃ seçilir.
Arka kabuğun döküm kalıp dökümünün yapı tasarımı
3.1 Ayırma Yüzeyinin Belirlenmesi Parça basit bir yapıya sahiptir. Ayrım yüzeyi seçimi ilkesine göre, Şekil 2'de gösterildiği gibi en büyük izdüşüm kesiti seçilmelidir.
3.2 Yolluk sisteminin tasarımı Yolluk sistemi dört bölümden oluşur:
- ① düz koşucu
- ② yatay koşucu
- ③ iç kapı,
- ④ soğuk sümüklü böcek deliği.
Özel tasarım:
- ①İntegral basınç odası——basınç odası ve yolluk burcunun bağlantı yöntemi;
- ②Koşucunun kesit şekli——düz yamuk;
- ③İç kapı——halka şeklindeki yan kapı;
- ④Yan dökme Ağız-dökümün ayırma yüzeyinde düzenlenmiş;
- ⑤ Dört boşluklu bir kalıp, Şekil 3 özel yapıyı göstermektedir.
3.3 Taşma tankı ve egzoz sisteminin tasarımı Taşma tankının yapısal tasarımı yapılır ve çeşitli faktörlerin kapsamlı bir şekilde dikkate alınmasıyla seçilen enine kesit şekli yamuktur (Şekil 4). Makul bir yapı aşağıdaki işlevlere sahiptir:
- ①Kalıbın termal dengesini iyileştirin-sıcaklığı kalıbın her yerinde ayarlayın, akış izlerini, soğuk bariyerleri ve dökümlerin yetersiz dökülmesini, büzülme boşluklarını, büzülme gözenekliliğini ve girdap sıkışmasını azaltın;
- ② boşaltma Boşluktaki gaz, egzoz oluğu ile hızla tükenir;
- ③soğuk kirli metal sıvının depolanması-boya kalıntısı ve gaz karışımı.
3.4 Ejeksiyon sisteminin tasarımı Kalıp döküm işleminde, tam bir şekillendirme döngüsü tamamlandıktan sonra, kalıp döküm parçasını almak için kalıbın açılması gerekir ve sarılı kalıp döküm parçası, kalıbın yan tarafında bulunacaktır. çıkarılması gereken yumruk. Bu görev, gerçekleştirmek için ek bir tür üst parça mekanizması gerektirir. Ejektör sistemi, kalıp yapısı tasarımında önemli bir yere sahiptir. Ejektör sisteminin üç ana parçası vardır:
- ① çıkarmak,
- ② sıfırla
- ③ rehber. Bu kalıp seti, döküm ve ladin fırlatma için kullanılan iki ejektör fırlatma mekanizmasını benimser. İtici pimlerin çapları sırasıyla 6 mm ve 8 mm'dir.
Sistemdeki tasarım limit cihazları:
- ① sınır bloğu,
- ② mekanizmanın sıfırlama doğruluğunu iyileştirmek ve mekanizma bileşenlerinin hareketi sırasında strokun sınırı aşmasını önlemek için sıfırlama kolu.
3.5 Oluşturulan parçanın boyutunun hesaplanması
3.5.1 Boşluk ve çekirdek boyutu:
3.5.2 Merkez mesafesini ve konum boyutunu hesaplayın: burada: L-oluşturma parçasının merkez mesafesi ve konumun ortalama boyutu (mm); L-kalıp döküm merkezi mesafesinin ortalama boyutu ve konumu (mm).
3.6 Soğutma sisteminin tasarımı, yüksek kaliteli dökümler ve uzun kalıp ömrü elde etmek için verimli ve kontrolü kolay bir kalıp soğutma yöntemi - su soğutması seçer. Su soğutmanın soğutma etkisi, boşlukta düzenlenen soğutma kanalının düzenine bağlıdır:
- ①En yüksek sıcaklık,
- ②Isı daha yoğundur,
- ③Kalıp altında,
- ④Operatörün karşısındaki taraf. Su dağıtım hortumunun montaj kolaylığını arttırmak için su kanalının dış çapının geometrik boyutlarının birleştirilmesi gerekmektedir. Yapısal düzenlemesi Şekil 5'te gösterilmiştir.
3.7 Basınçlı Döküm Kalıbının Genel Montaj Çizimi Arka kabuk kapağının basınçlı döküm kalıbının genel montaj çizimini yapın (Şekil 6). Kalıp döküm kalıbı iki parçadan oluşur: sabit kalıp ve hareketli kalıp. Sabit kalıp sabittir ve sabit kalıp plakası üzerinde bulunur. Hareketli kalıp, takipçi plaka ile birlikte hareket eder ve takipçi kalıp sabit plakası üzerinde bulunur. Hareketli kalıbın hareketli kalıba göre hareketi ile kalıp kapanır ve açılır.
① Kalıp sıkıştırma: ikisi bir boşluk oluşturacak şekilde kapatılır ve boşluk, bir geçit sistemi kullanılarak yüksek basınç altında erimiş metal ile doldurulur; ② kalıp açma: basınç korunduktan sonra ikisi ayrılır ve ejeksiyon mekanizması ürünleri boşluktan çıkarma görevini tamamlar.
Bu makale, arka kapak parçalarını modellemek için UG yazılımını kullanır ve arka kapak parçalarının süreç analizini, döküm süreç parametrelerini ve kalıp yapısı tasarımını tamamlar. Boşluk, aşağıdaki faktörlerle sınırlıdır: üretim, proses ve üretim Verimliliği vb. Yukarıdaki faktörler kapsamlı bir şekilde göz önüne alındığında, daha makul bir tek kalıplı dört boşluklu yerleşim olarak belirlenir. Pratik üretim, 90MPa'lık kalıp döküm spesifik basıncının seçildiğini, kalıp döküm hızının 20-90m/s aralığında seçildiğini, döküm süresinin 0.2s olduğunu, tutma süresinin 3s olduğunu ve kalıp dökümünün seçildiğini göstermektedir. 620℃ sıcaklık, ortaya çıkan arka kabuk havasız kapak Pürüzsüz bir yüzeye sahiptir ve ürün kalitesi gereksinimlerini karşılar.
Lütfen yeniden basım için bu makalenin kaynağını ve adresini saklayın: Alüminyum Alaşımlı Kabuk Döküm Kalıplarının Tasarım Detayı
Minhe Basınçlı Döküm Şirketi kaliteli ve yüksek performanslı Döküm Parçaları üretmeye ve sağlamaya adamıştır (metal döküm parça yelpazesi esas olarak şunları içerir: İnce Duvarlı Döküm,Sıcak Kamara Basınçlı Döküm,Soğuk Oda Döküm), Yuvarlak Servis (Döküm Servisi,Cnc İşleme,Kalıp yapımı,Yüzey İşleme).Herhangi bir özel Alüminyum döküm, magnezyum veya Zamak/çinko döküm ve diğer döküm gereksinimleri bizimle iletişime geçebilirsiniz.
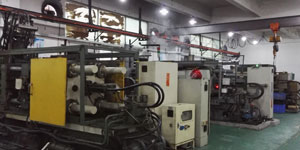
ISO9001 ve TS 16949 kontrolünde, tüm işlemler yüzlerce gelişmiş basınçlı döküm makinesi, 5 eksenli makine ve blasterlerden Ultra Sonic yıkama makinelerine kadar diğer tesisler aracılığıyla gerçekleştirilir. Müşterinin tasarımını gerçeğe dönüştürmek için deneyimli mühendisler, operatörler ve müfettişlerden oluşan ekip.
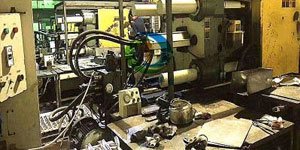
Dökümlerin sözleşmeli üreticisi. Yetenekler, 0.15 lbs'den başlayan soğuk oda alüminyum döküm parçaları içerir. 6 lbs'ye kadar, hızlı değişim kurulumu ve işleme. Katma değerli hizmetler arasında polisaj, titreşim, çapak alma, kumlama, boyama, kaplama, kaplama, montaj ve kalıplama yer alır. Çalışılan malzemeler arasında 360, 380, 383 ve 413 gibi alaşımlar bulunur.
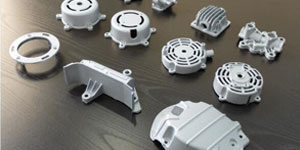
Çinko pres döküm tasarım yardımı/eşzamanlı mühendislik hizmetleri. Hassas çinko dökümlerin özel üreticisi. Minyatür dökümler, yüksek basınçlı dökümler, çok kızaklı kalıp dökümleri, geleneksel kalıp dökümleri, birim kalıp ve bağımsız kalıp dökümleri ve boşluklu sızdırmaz dökümler üretilebilir. Dökümler, +/- 24 inç toleransta 0.0005 inç'e kadar uzunluk ve genişliklerde üretilebilir.
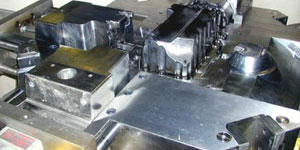
ISO 9001: 2015 sertifikalı döküm magnezyum üreticisi, Yetenekler arasında 200 ton sıcak odaya ve 3000 ton soğuk odaya kadar yüksek basınçlı magnezyum kalıp dökümü, takım tasarımı, cilalama, kalıplama, işleme, toz ve sıvı boyama, CMM özelliklerine sahip tam kalite güvencesi bulunur , montaj, paketleme ve teslimat.
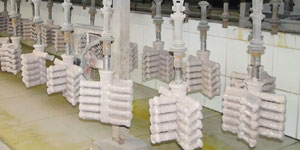
ITAF16949 sertifikalı. Ek Döküm Hizmeti Dahil yatırım dökümleri,kum dökümü,Yerçekimi Döküm, Kayıp Köpük Döküm,Savurma döküm,Vakumlu Döküm,Kalıcı Kalıp Döküm,.Yetenekler arasında EDI, mühendislik yardımı, katı modelleme ve ikincil işleme yer alır.
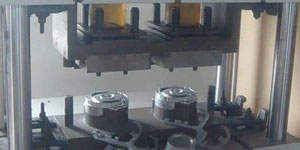
Döküm Endüstrileri Arabalar, Bisikletler, Uçaklar, Müzik aletleri, Deniz Araçları, Optik cihazlar, Sensörler, Modeller, Elektronik cihazlar, Muhafazalar, Saatler, Makineler, Motorlar, Mobilya, Mücevher, Jigler, Telekom, Aydınlatma, Tıbbi cihazlar, Fotoğraf cihazları, Robotlar, Heykeller, Ses ekipmanları, Spor ekipmanları, Aletler, Oyuncaklar ve daha fazlası.
Bundan sonra ne yapmanıza yardımcı olabiliriz?
∇ Ana Sayfaya Git Çin Döküm
→Döküm Parçaları-Ne yaptığımızı öğren.
→ Hakkında İlgili İpuçları Pres Döküm Hizmetleri
By Minghe Döküm Üreticisi |Kategoriler: Faydalı Makaleler |Malzeme Etiketler: Alüminyum Döküm, Çinko Döküm, Magnezyum Döküm, Titanyum Döküm, Paslanmaz Çelik Döküm, Pirinç Döküm,Bronz Döküm,Döküm Videosu,Tarihçe,Alüminyum Döküm |Yorumlar Kapalı