Alüminyum-Magnezyum Alaşımlı Döküm Kalıbının Ömrünü Artıracak Önlemler
Önemli bir işleme ekipmanı olarak, alüminyum-magnezyum alaşımlı pres döküm kalıpları, şirketin ürün kalitesi ve ekonomik faydaları üzerinde doğrudan bir etkiye sahiptir. Kalıp malzemesi ve ısıl işlem teknolojisi, alüminyum-magnezyum alaşımlı kalıp döküm kalıplarının ömrünü etkileyen ana faktörlerdir. Bu makale, alüminyum-magnezyum alaşımlı kalıp döküm kalıplarının ana arıza modlarını analiz eder, tipik kalıp çeliklerini ve yaygın ısıl işlem yöntemlerini kısaca tanıtır ve makul bir kalıp malzemesi seçiminin ve ısıl işlem işlemlerinin, kalıbın termal stabilitesini, sertleşebilirliğini önemli ölçüde iyileştirebileceğine işaret eder. , aşınma direnci ve termal kararlılık. Yorulma ve ısıl iletkenlik gibi özellikler kalıbın kullanım ömrünü uzatır.
Alüminyum-Magnezyum Alaşımlı Döküm Kalıbının Arıza Modu
Alüminyum-magnezyum alaşımlı kalıp döküm kalıbı, bir kalıp döküm makinesinde alüminyum-magnezyum alaşımlı dökümlerin kalıp dökümü için kullanılan bir şekillendirme kalıbıdır. Çalışma sırasında boşluğun yüzey sıcaklığı yaklaşık 600 ℃'ye ulaşabilir ve erimiş alüminyum-magnezyum alaşımlı sıvının çelik malzemelere yapışması kolaydır. Kalıp boşluğuna sık sık yapışma önleyici kaplama uygulanması, boşluğun yüzey sıcaklığında ciddi dalgalanmalara neden olur. Ana arıza modları kalıp yapışması, erozyon, termal yorulma ve aşınmadır. Kalıp boşluğu yapısı karmaşık olduğunda ve stres konsantrasyonu olduğunda, termal yük ve mekanik yükün birleşik etkisi altında kalıp da kırılacak ve başarısız olacaktır.
1.1 Yapışkan Kalıp
Alüminyum-magnezyum alaşımlı parçalar ve kalıp yüzeyi, düzgün olmayan yüzey nedeniyle hareket ettiğinde, bazı temas noktalarının yerel stresi, bağlanacak malzemenin akma mukavemetini aşar ve yapıştırılan bağlantılar kesilir ve kırılır ve çekilir, kalıbın yüzey malzemesi İş parçasına aktarılır veya düşer.
1.2 Erozyon
Kalıp yüzeyi nispi hareket için alüminyum-magnezyum alaşımlı sıvı ile temas ettiğinde, sıvı ve kalıp arasındaki temasta oluşan kabarcık patlar ve ani darbe ve yüksek sıcaklık üreterek kalıp yüzeyinin küçük çukurlar ve çukurlar oluşturmasına neden olur. Alüminyum-magnezyum alaşımlı sıvı ve küçük katı parçacıklar yüksek hızda düşer ve kalıbın yüzeyini art arda etkiler, yerel malzeme kaybına neden olur ve metal yüzeyinde çukurlar ve çukurlar oluşturur. Tekrarlanan eylem altında, kalıbın yüzeyinde yorulma çatlakları oluşacak ve hatta yerel kırılmalar meydana gelecektir.
1.3 Termal Yorulma
Kalıbın yüzeyi, yorulmaya ve çatlaklara neden olmak için tekrar tekrar ısıtma ve soğutmaya tabi tutulur. Alüminyum-magnezyum alaşımlı kalıp döküm kalıbının çatlamasının ana nedeni, döküm sıcaklığı ile kalıbın ön ısıtma sıcaklığı arasındaki farktır. Sıcaklık farkı ne kadar büyük olursa, soğutma hızı o kadar hızlı olur, termal yorulma çatlakları o kadar kolay olur. İkincisi, ısıl döngü hızı, kalıbın ısıl işlem süreci ve Yüzey işlemi de yakından ilişkilidir.
1.4 Aşınma
Kalıp yüzeyi ile yüksek sıcaklıkta işlenmiş alüminyum-magnezyum alaşımlı parçalar arasındaki sürtünme yağlanamadığından ve yüksek sıcaklıktaki iş parçaları oksitlendiğinden, kalıp boşluğunun yüzeyi temperlenir ve yumuşatılır ve düşük sertlik aşınmayı arttırır. Şiddetli aşınma, kalıbın nitelikli ürünleri işlemesini engeller. Emeklilik geçersiz.
1.5 Mola
Alüminyum-magnezyum alaşımlı kalıp döküm kalıbının çalışma sırasında büyük çatlaklara veya kısmi ayrılmalara sahip olması ve normal hizmet kabiliyetini kaybetmesi olgusuna kırılma hatası denir. Kalıp kırılması genellikle lokal parçalar olarak kendini gösterir veya kalıbın tamamı birkaç parçaya bölünür.
Alüminyum Magnezyum Alaşımlı Döküm Kalıp Çelik Seçimi
Kalıp malzemesinin türü, kimyasal bileşim, metalografik yapı, sertlik, tokluk, hipoploid yapı ve diğer kapsamlı faktörler, alüminyum-magnezyum alaşımlı kalıp döküm kalıplarının başarısız olmasının önemli nedenleridir. Kötü çalışma koşulları, alüminyum-magnezyum alaşımlı kalıp döküm kalıplarının yüksek olmasını gerektirir. Temperleme önleyici stabilite ve soğuk ve ısı yorgunluğuna karşı direnç performansı, yüksek sıcaklığa, yüksek basınca ve yüksek hızlı sıvı alüminyum-magnezyum alaşımı erozyon kabiliyetine karşı iyi bir dirence sahiptir ve yüksek mukavemet ve tokluk.
2.1 3Cr2W8V (H21) çelik
Daha fazla tungsten, krom ve vanadyum elementleri içeren, yüksek sertleşebilirliğe, tavlama kararlılığına ve termal dayanıma sahiptir. Yüksek taşıma kapasiteli, yüksek ısıl dayanımlı ve yüksek tavlama kararlılığına sahip pres döküm kalıpları için uygundur.
2.2 4Cr5MoSiV1 (H13) çelik
Soğuğa ve ısıya karşı yüksek tokluğa ve dirence sahiptir ve termal yorulma çatlakları üretmek kolay değildir. Termal yorulma çatlakları görünse bile, bunlar ince ve kısadır ve genişlemeleri kolay değildir. Kullanmadan önce ön ısıtmaya gerek yoktur ve musluk suyu ile soğutulabilir. Termal güç.
2.3 4Cr5Mo2MnSiV1 (Y10) çelik
Yaklaşık %2 kütle fraksiyonuna sahip molibden eklenir, termal kararlılığı iyileştirmek için vanadyum ve çamur gibi elementlerle desteklenir ve matrisin gücünü artırmak için uygun miktarlarda silikon ve manganez eklenir, iyi termal yorulma performansı ve dirençle birlikte matrisin mukavemetini arttırır. erimiş metal korozyonu.
2.4 4Cr5MoSiV (H11) Çelik
Tungsten sıcak iş kalıp çeliğine aittir. Orta sıcaklık koşullarında iyi tokluğa, iyi termal mukavemete, termal yorulma performansına ve belirli aşınma direncine sahiptir. Daha düşük östenitleme sıcaklık koşulları altında hava ile söndürülür ve ısıl işleme tabi tutulur. Deformasyon küçüktür, hava ile söndürme sırasında oksit ölçeği üretme eğilimi küçüktür ve erimiş alüminyumun erozyon etkisine direnebilir.
2.5 3Cr3Mo3VNb (HM3) Çelik
Temperleme direncini ve termal mukavemeti artırmak için düşük karbon içeriği koşulu altında iz element Nb ekleyen yeni bir yüksek mukavemetli ve tokluğa sahip sıcak dövme kalıp çeliği, belirgin bir tavlama ikincil sertleştirme etkisine sahiptir ve etkili bir şekilde kalıbın üstesinden gelebilir Erken başarısızlık nedeniyle termal aşınma, termal yorulma, termal çatlama vb.
2.6 4Cr3Mo3SiV (H10) Çelik
500 ~ 600 ℃ çalışma sıcaklığında daha yüksek sertliğe, ısı direncine ve aşınma direncine sahiptir ve çok iyi sertleşebilirlik ve yüksek tokluğa sahiptir, tavlama direnci ve termal stabilite H13 çeliğinden daha yüksektir, darbe tokluğu Sertlik ve kırılma tokluğu bundan daha yüksektir 3Cr2W8V çelikten. Temperleme sıcaklığı 260℃'yi aştığında, çeliğin sertliği H13 çeliğinden daha yüksektir. Alüminyum-magnezyum alaşımlı döküm kalıpların performansını artırmak ve kalıbın hizmet ömrünü uzatmak için yüksek mukavemetli ve tok kalıp malzemelerinin kullanılması çok önemli bir önlemdir. Örneğin, belirli bir kalıp doğrudan 3Cr2W8V çeliği ile işlenir. Boyutlar φ180x85mm, sertlik gereksinimi 42~46HRC, üretimde ve kullanımda sadece 249 pres döküm yapılabilir,
900 adet. Daha sonra 4Cr3Mo3SiV'den yapılmış ve servis ömrü 1000.000 parçaya çıkarılmıştır.
Alüminyum-Magnezyum Alaşımlı Kalıp Döküm Kalıbı İçin Isıl İşlem Prosesinin Seçimi
Alüminyum-magnezyum alaşımlı kalıp döküm kalıbının ısıl işlemi, kalıp çeliğinin yapısını değiştirmek, böylece kalıbın gerekli yapı ve performansı elde edebilmesi ve kalıbın hizmet ömrünü uzatabilmesidir. Isıl işlem proses özellikleri, kalıp malzemesine, kalıp şekline, boyutuna ve karmaşıklığına göre belirlenmelidir.
3.1 Ön Isıl İşlem
Kalıp döküm kalıbının ön ısıl işlemi üç işlemi benimseyebilir: sürekli tavlama, izotermal tavlama ve su verme ve tavlama ısıl işlemi. Amaç, çeliğin mukavemetini ve tokluğunu iyileştirmek için son ısıl işlemden önce üniform bir yapı ve dispers karbür elde etmektir. Sürekli tavlama işlemi nispeten basittir ve daha iyi taneli bir perlit yapısı da elde edilebilir. Karmaşık şekillere ve yüksek gereksinimlere sahip kalıp döküm kalıpları için, daha ideal bir granüler perlit yapı elde etmek için izotermal tavlama kullanılabilir.
3.2 Söndürme ve Ön Isıtma
Döküm kalıp çeliği çoğunlukla düşük termal iletkenliğe sahip yüksek alaşımlı çeliktir. Ön ısıtma önlemleri genellikle söndürme ve ısıtma sırasında alınır. Ön ısıtma sayısı ve sıcaklık, kalıp çeliğinin bileşimine ve kalıp deformasyon gereksinimlerine bağlıdır. Düşük su verme sıcaklığına, basit şekle ve düşük deformasyon gereksinimlerine sahip kalıplar için, su verme ısıtması sırasında çatlama olmadan bir ön ısıtma (800℃~850℃) yapılmalıdır. Daha yüksek sıcaklıkta su verme, karmaşık şekiller ve yüksek deformasyon gereksinimleri olan kalıplar için ikincil ön ısıtma (600 ila 650°C, 800 ila 850°C) gereklidir. Amaç, ısıtma işlemi sırasında oluşan stresi azaltmak ve aynı zamanda kalıbın genel yapısını tek tip hale getirmektir.
3.3 Söndürme Isıtma
Döküm kalıbının söndürme ısıtma sıcaklığı, her bir çelik sınıfının söndürme ısıtma özelliklerine göre uygulanabilir. Örneğin, 3Cr2W8V çeliğinin su verme sıcaklığı 1050~1150℃ ve H13 çeliğinin su verme sıcaklığı 1020~1100℃'dir. Karbürlerin tam çözünmesini sağlamak, düzgün östenit elde etmek ve iyi bir yüksek sıcaklık performansı elde etmek için, basınçlı döküm kalıplarının su verme ve ısıtma tutma süresi uygun şekilde uzatılmalıdır. Genel olarak, tuz banyosu fırınındaki ısıtma tutma katsayısı 0.8 ~ 1.0dak/mm'dir.
3.4 Söndürme ve Soğutma
Yağda su verme hızı hızlıdır ve iyi performans elde edilebilir ancak deformasyon ve çatlama eğilimi büyüktür. Genel olarak, basit şekillere ve düşük deformasyon gereksinimlerine sahip kalıp döküm kalıpları için yağ soğutması kullanılır; karmaşık şekillere ve yüksek deformasyon gereksinimlerine sahip kalıp döküm kalıpları için, kalıp deformasyonunu ve çatlamayı önlemek için hiyerarşik su verme kullanılmalıdır. Söndürme soğutması, bir vakum direnci fırınında söndürme deformasyonunu, ısıtmayı ve söndürmeyi azaltmak için mümkün olduğunca yavaş olmalıdır, soğutma, gazla söndürme olarak kabul edilebilir. Tuz banyosunda ısıtma ve su verme ve soğutma sırasında derecelendirmeli su verme uygulanabilir. Kalıp sulandırılıp soğutulduğunda, ıslatıldıktan ve 150~200℃'ye soğutulduktan hemen sonra temperlenmelidir ve oda sıcaklığına soğumasına izin verilmemelidir.
3.5 Temperleme
Kalıp döküm kalıbının sertliği, temperleme ile elde edilir ve kalıp döküm kalıbı boşluğunun sertliği, kalıbın sıcak ve soğuk yorulma ömrünü doğrudan etkiler. Farklı malzemeler, farklı su verme sıcaklığı ve tavlama sıcaklığı da farklıdır. Örneğin, 3Cr2W8V çelik alüminyum-magnezyum alaşımlı kalıp döküm kalıbının sertliği genellikle 42 ~ 48HRC'dir ve tavlama sıcaklığı genellikle 560 ~ 620 ℃ arasında seçilir, ancak yüksek sıcaklıkta su verme kullanılıyorsa, tavlama sıcaklığı kadar yüksektir. 670 ℃. 1150°C'de su verme ve 650°C'de temperleme sonrası sertlik 45HRC'dir; 1050°C'de su verme ve 650°C'de temperleme sonrası sertlik ise 35HRC'dir.
3.6 Yüzey Güçlendirme İşlemi
Döküm kalıbı su verildikten ve temperlendikten sonra yüzey sertliği çok yüksek değildir. Çekirdek kısım hala yeterli mukavemet ve tokluğu korurken, kalıp döküm kalıbının yüzeyinde yüksek sertlik ve aşınma direnci elde etmek ve alüminyum-magnezyum alaşımlı kalıp döküm kalıbının yapışma önleyici performansını iyileştirmek için, yüzey döküm kalıbı üzerinde nitrürleme yapılabilir. Veya nitrokarbürleme işlemi. Sertleştirme işleminin ve yüzey güçlendirme işleminin kullanılması, kalıbın performansını ve ömrünü iyileştirmenin önemli bir yoludur. Örneğin, H13 kalıp döküm kalıbının nitrokarbürleme ısıl işlem ortamı, amonyak gazı + etanoldür ve işlem 580 ℃ x 4.5 saattir. 1030°C'de su verme ve 600°C ve 580 gaz nitrokarbürleme ısıl işleminde temperlemeden sonra, kalıbın yüzey sertliği 900HV'nin üzerindedir, matris sertliği 46~48HRC'dir ve kalıbın aşınma direnci, yorulma direnci ve korozyon direnci büyük ölçüde iyileştirilir. .
Sonuç
Alüminyum-magnezyum alaşımlı kalıp döküm kalıplarının üretiminde, kalıbın çalışma koşullarına göre arıza nedenlerini analiz etmek ve incelemek, kalıp malzemesini doğru seçmek ve kalıbı sağlamak için makul bir ısıl işlem süreci formüle etmek gerekir. yüzey sertliği, aşınma direnci, çekirdek mukavemeti ve tokluğu ve metal sıvı korozyonunu ve kalıp yapışmasını önler. , Reddetme oranını etkili bir şekilde azaltın ve kalıbın hizmet ömrünü önemli ölçüde artırın. Üretim uygulaması, alüminyum-magnezyum alaşımlı kalıp döküm kalıbının etkili ve ekonomik bir sıcaklığa ön ısıtılmasının kalıp ve iş parçası arasındaki sıcaklık farkını azaltabileceğini, kalıp çatlaklarının oluşumunu azaltabileceğini, kalıbın hizmet ömrünü uzatabileceğini ve artırabileceğini kanıtlamıştır. üretkenlik. Elbette alüminyum-magnezyum alaşımlı döküm kalıpların kullanımı sırasında doğru kullanım, makul yönetim ve dikkatli bakım da kalıbın erken kırılma arızasını azaltmak ve kalıbın hizmet ömrünü artırmak için etkili önlemlerdir.
İlgili Sayfalar:kalıp imalatı
Lütfen yeniden basım için bu makalenin kaynağını ve adresini saklayın: Alüminyum-Magnezyum Alaşımlı Döküm Kalıbının Ömrünü Artıracak Önlemler
Minhe Basınçlı Döküm Şirketi kaliteli ve yüksek performanslı Döküm Parçaları üretmeye ve sağlamaya adamıştır (metal döküm parça yelpazesi esas olarak şunları içerir: İnce Duvarlı Döküm,Sıcak Kamara Basınçlı Döküm,Soğuk Oda Döküm), Yuvarlak Servis (Döküm Servisi,Cnc İşleme,Kalıp yapımı,Yüzey İşleme).Herhangi bir özel Alüminyum döküm, magnezyum veya Zamak/çinko döküm ve diğer döküm gereksinimleri bizimle iletişime geçebilirsiniz.
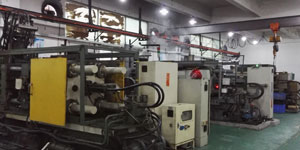
ISO9001 ve TS 16949 kontrolünde, tüm işlemler yüzlerce gelişmiş basınçlı döküm makinesi, 5 eksenli makine ve blasterlerden Ultra Sonic yıkama makinelerine kadar diğer tesisler aracılığıyla gerçekleştirilir. Müşterinin tasarımını gerçeğe dönüştürmek için deneyimli mühendisler, operatörler ve müfettişlerden oluşan ekip.
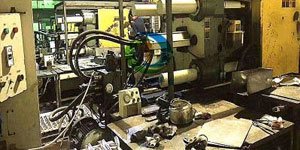
Dökümlerin sözleşmeli üreticisi. Yetenekler, 0.15 lbs'den başlayan soğuk oda alüminyum döküm parçaları içerir. 6 lbs'ye kadar, hızlı değişim kurulumu ve işleme. Katma değerli hizmetler arasında polisaj, titreşim, çapak alma, kumlama, boyama, kaplama, kaplama, montaj ve kalıplama yer alır. Çalışılan malzemeler arasında 360, 380, 383 ve 413 gibi alaşımlar bulunur.
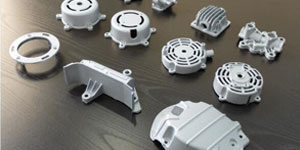
Çinko pres döküm tasarım yardımı/eşzamanlı mühendislik hizmetleri. Hassas çinko dökümlerin özel üreticisi. Minyatür dökümler, yüksek basınçlı dökümler, çok kızaklı kalıp dökümleri, geleneksel kalıp dökümleri, birim kalıp ve bağımsız kalıp dökümleri ve boşluklu sızdırmaz dökümler üretilebilir. Dökümler, +/- 24 inç toleransta 0.0005 inç'e kadar uzunluk ve genişliklerde üretilebilir.
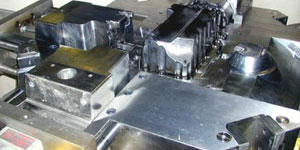
ISO 9001: 2015 sertifikalı döküm magnezyum üreticisi, Yetenekler arasında 200 ton sıcak odaya ve 3000 ton soğuk odaya kadar yüksek basınçlı magnezyum kalıp dökümü, takım tasarımı, cilalama, kalıplama, işleme, toz ve sıvı boyama, CMM özelliklerine sahip tam kalite güvencesi bulunur , montaj, paketleme ve teslimat.
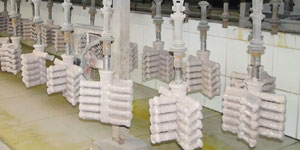
ITAF16949 sertifikalı. Ek Döküm Hizmeti Dahil yatırım dökümleri,kum dökümü,Yerçekimi Döküm, Kayıp Köpük Döküm,Savurma döküm,Vakumlu Döküm,Kalıcı Kalıp Döküm,.Yetenekler arasında EDI, mühendislik yardımı, katı modelleme ve ikincil işleme yer alır.
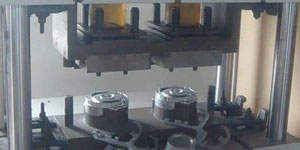
Döküm Endüstrileri Arabalar, Bisikletler, Uçaklar, Müzik aletleri, Deniz Araçları, Optik cihazlar, Sensörler, Modeller, Elektronik cihazlar, Muhafazalar, Saatler, Makineler, Motorlar, Mobilya, Mücevher, Jigler, Telekom, Aydınlatma, Tıbbi cihazlar, Fotoğraf cihazları, Robotlar, Heykeller, Ses ekipmanları, Spor ekipmanları, Aletler, Oyuncaklar ve daha fazlası.
Bundan sonra ne yapmanıza yardımcı olabiliriz?
∇ Ana Sayfaya Git Çin Döküm
→Döküm Parçaları-Ne yaptığımızı öğren.
→ Hakkında İlgili İpuçları Pres Döküm Hizmetleri
By Minghe Döküm Üreticisi |Kategoriler: Faydalı Makaleler |Malzeme Etiketler: Alüminyum Döküm, Çinko Döküm, Magnezyum Döküm, Titanyum Döküm, Paslanmaz Çelik Döküm, Pirinç Döküm,Bronz Döküm,Döküm Videosu,Tarihçe,Alüminyum Döküm |Yorumlar Kapalı