Pelet performansını artırmak için "Alkali" ve "Magnezyum"
Oksitlenmiş peletler iyi mekanik mukavemete ve metalurjik özelliklere sahiptir ve yüksek fırın demir üretimi için vazgeçilmez yüksek kaliteli bir dolgu haline gelmiştir. Ancak, yerel manyetit konsantresi arzının olmaması, birçok yerel çelik tesisinin oksit peletleri üretmek için ithal hematiti kullanmasına neden oldu. Manyetit peletlerle karşılaştırıldığında, hematit peletleri yüksek kavurma sıcaklığına ve dar bir aralığa (1300 ℃ ~ 1350 ℃) sahiptir ve peletlerin basınç dayanımı düşüktür. Ek olarak, asidik hematit peletleri zayıf metalurjik özelliklere sahiptir. Bunlar arasında, spekülerit önemli bir hematit tipine aittir ve peletlerin kavurma performansı ve metalurjik özellikleri, sıradan hematit peletlerinden daha kötüdür.
Araştırmacılar, yüksek mukavemetli oksitlenmiş peletler üretmek için hematitin nasıl kullanılacağına dair birçok araştırma yaptılar. Çalışmalar, oksitlenmiş peletler hazırlamak için hematite manyetit eklenmesinin ön ısıtma kavurma sıcaklığını etkili bir şekilde azaltabileceğini ve önceden ısıtılmış kavurma peletlerinin basınç dayanımını artırabileceğini göstermiştir; Fluxed hematit peletleri üretmek için flux eklemek de bir çözümdür.
Yerli pelet fabrikaları genellikle yüksek mukavemetli pelet üretmek için hematit ve manyetit kullanır, ancak hematit oranı arttıkça manyetit eklemenin etkisi büyük ölçüde zayıflar. Akı peletleri üretmek için CaO akısının eklenmesi, daha düşük bir sıcaklıkta daha yüksek mekanik mukavemet ve daha iyi indirgenebilirlik sağlayabilir, ancak yüksek sıcaklıkta yeniden akış performansı zayıftır ve indirgeme genişlemesi ciddidir. İlk çalışmalar, peletlere MgO eklenmesinin, azalma genleşme oranını azaltabileceğini ve yüksek sıcaklıkta yeniden akış performansını iyileştirebileceğini göstermiştir.
Şu anda, alkalinite ve MgO içeriğinin speküler peletlerin mukavemeti ve metalurjik özellikleri üzerindeki etkisi, özellikle alkalinite ve MgO'nun peletlerin metalurjik özellikleri üzerindeki etkisi hakkında nispeten az sayıda rapor bulunmaktadır. Bu nedenle, alkalinite ve MgO içeriğinin spekülerit peletlerin mukavemeti ve metalurjik özellikleri üzerindeki etkilerini inceleyen bu makale, pelet kavurmayı geliştirmek ve yüksek fırın demir yapımını güçlendirmek için önemli teorik değere sahiptir.
Hammadde özellikleri ve araştırma yöntemleri
Bu deneyde kullanılan hammaddeler Brezilya speküleriti, bentonit, kireçtaşı ve manyezittir. Brezilya speküleriti, kireçtaşı ve manyezit partikül boyutunda nispeten kaba olduğundan, laboratuvarda bir bilyalı değirmen ile pelet üretimi için gerekli olan partikül boyutuna ve spesifik yüzey alanına öğütülürler. Spiegelite, yüksek demir derecesine, daha az gang mineraline ve diğer zararlı safsızlıklara sahiptir ve yüksek kaliteli bir pelet hammaddesidir. Kireçtaşı ve manyezit, düşük SiO2 içeriğine ve birkaç diğer zararlı yabancı maddeye sahiptir. Bunlar yüksek kaliteli kalsiyum-magnezyum flukslarıdır.
Testte kullanılan bağlayıcı yüksek kaliteli sodyum bazlı bentonittir ve göstergeler şu şekildedir: montmorillonit içeriği %92.76, şişme hacmi 20mL/g, 2 saatte su emme oranı %342 ve -0.074mm içeriği %100'e ulaşır.
Deneysel araştırma, harmanlama, karıştırma, yeşil bilye hazırlama, yeşil bilye kurutma, kuru bilye ön ısıtma kavurma ve kavurma pelet performans testini içerir. Bitmiş peletlerin SiO2 içeriği, ince öğütülmüş kuvars kumu eklenerek %3.0-%3.1 oranında kontrol edilir. Bitmiş peletlerin alkalinite ve MgO içeriği, kireçtaşı ve manyezit eklenerek ve alkalinite ve MgO içeriğindeki değişikliklerin basınç dayanımı, indirgeme derecesi, indirgeme genleşmesi, düşük sıcaklıkta indirgeme toz haline getirilmesi ve yüksek sıcaklıkta yumuşak erime üzerindeki etkileri ayarlanır. kavrulmuş peletlerin özellikleri araştırılmıştır. Etkilemek.
Test sonuçları ve etki analizi
"Alkalinite ve MgO içeriğinin basınç dayanımı ve gözeneklilik üzerindeki etkisi." Peletlerin basınç dayanımı, taşıma ve depolama işlemi sırasında ve indirgeme fırınında peletlerin dayanabileceği basıncı yansıtan önemli bir göstergedir. Büyük yüksek fırınlar, peletlerin basınç dayanımının 2500 N/parça'dan fazla olmasını gerektirir.
Doğal MgO içeriği altında, peletlerin basınç dayanımı önce alkalinitedeki artışla artar. Alkalinite 0.2'ye yükseldiğinde, peletlerin basınç dayanımı 2400 N/parça doğal alkaliniteden 3,500 N/parçaya yükselir; 0.4'e ulaştıktan sonra, peletlerin basınç dayanımı artık artmaz. Bunun nedeni, kalsiyum ferrit ve kalsiyum silikat gibi CaO, Fe2O3 ve SiO2'nin alkalinitesindeki artıştır. Uygun sıvı faz, hematitin yeniden kristalleşmesine yardımcı olur, ancak çok fazla sıvı faz, peletlerin basınç dayanımının iyileştirilmesine yardımcı olmaz. Doğal alkalilik altında, MgO içeriğinin artmasıyla peletlerin basınç dayanımı azalır. Bunun nedeni, peletlerin ön ısıtması ve kavrulması sırasında manyezitin ayrışarak peletlerin gözenekliliğini arttırmasıdır.
Alkalinite ve MgO, aynı MgO içeriği altında birlikte çalıştığında, alkaliliğin kalsine edilmiş peletlerin basınç mukavemeti üzerindeki etkisi, temel olarak alkaliliğin, doğal MgO içeriği altındaki peletlerin basınç mukavemeti üzerindeki etkisi ile aynıdır, yani, peletlerin basınç dayanımı. Dayanım önce alkalinitenin artmasıyla artar. Alkalinite belirli bir değere ulaştıktan sonra, peletlerin basınç dayanımı artık önemli ölçüde artmaz; aynı alkalinite altında, MgO içeriğinin artmasıyla peletlerin basınç dayanımı azalır, bu da MgO içeriğinden kaynaklanır. sıvı fazın oluşumu üzerinde belirli bir engelleyici etkiye sahip olan gang minerallerinin erime noktası. Test sonuçları, alkalilik 0.2'nin üzerinde olduğunda, farklı alkalilik ve MgO içeriğine sahip spekülerit peletlerin basınç dayanımının 2500 N/parça'dan fazla olabileceğini göstermektedir.
Akı miktarı arttıkça, ön ısıtma kavurma sırasında akı ayrışmasının bıraktığı gözenekler de artar. Flux ilavesi sadece peletlerin kimyasal bileşimini ve mineral bileşimini etkilemekle kalmaz, aynı zamanda peletlerin yapısını ve gözenekliliğini de etkiler. Bu, peletlerin basınç dayanımını ve metalurjik özelliklerini bir dereceye kadar etkileyecektir.
Alkalinite ve MgO içeriğinin indirgenme derecesine etkisi. İndirgeme derecesi (RI), yüksek fırının indirgeme bölgesindeki sıcaklık ve atmosfer koşulları altında demir cevherinden oksijeni uzaklaştırma eğilimini ve zorluğunu değerlendirmek için önemli bir göstergedir. Demir cevherinin indirgenme derecesini etkileyen faktörler arasında parçacık boyutu, gözeneklilik, mineral bileşimi ve yapısı ve gang mineral bileşimi bulunur.
Doğal alkalilik ve doğal MgO içeriğine sahip asidik peletlerin indirgenme derecesi düşüktür, sadece %62.22'dir. MgO içeriğinin artmasıyla indirgeme derecesi artar. MgO içeriği %3.0 olduğunda, peletlerin indirgeme derecesi %68'e ulaşabilir; MgO içeriği alkaliniteyi arttırdığında, spekülerit peletlerin indirgeme derecesi büyük ölçüde iyileşir. Alkalinite 1.2'ye yükseldiğinde, peletlerin indirgenme derecesi %72.82'ye yükselir. Bunun nedeni, kireçtaşı ilavesinin peletlerin gözenekliliğini arttırması ve aynı zamanda CaO'nun Fe2O3 ile reaksiyona girerek kolayca indirgenmiş kalsiyum ferrit oluşturmasıdır.
Alkalinite ve MgO birlikte hareket ettiğinde, aynı alkalinite altında, MgO içeriğinin artmasıyla mirrorit peletlerinin indirgenme derecesi artar; aynı MgO içeriği altında, alkalinitenin artmasıyla indirgenme derecesi artar.
Alkalinite 1.2'ye ulaştığında ve MgO içeriği %3.0'a yükseldiğinde, peletlerin indirgenme derecesi %76.94 kadar yüksektir. Bunun nedeni, manyezitin peletlerin ön ısıtması ve kavrulması sırasında peletlerin gözenekliliğini de arttırması ve MgO'nun cüruf fazının ve yüzen gövdenin erime noktasını artırabilmesi, böylece indirgeme işlemi sırasında erimenin kolay olmamasıdır. ve peletlerin gözenekleri erimez. Malzeme, gaz difüzyonuna elverişli olan yüksek gözenekliliği korumak için doldurulur.
Alkalinite ve MgO içeriğinin indirgeme genleşmesine etkisi.
Doğal MgO içeriği altında, spekülerit peletlerin indirgeme genleşme hızı önce artar ve sonra azalır ve alkalinite 0.4 ile 0.6 arasında maksimum değere ulaşır ve maksimum değer %32 kadar yüksektir.
Bunun nedeni, peletlere eklenen CaO'nun küçük bir kısmının Fe2O3 ile reaksiyona girerek kalsiyum ferrit üretmesi ve çoğunun cüruf fazına girmesidir. İndirgenmediğinde, cüruf fazına CaO-SiO2 ikili sistemi hakimdir. Alkalinite 0.4 ile 0.6 arasında olduğunda, yani cüruf fazındaki SiO2 içeriği, kalsiyum metasilikat (CaOSiO62.5) ve SiO70'nin ikili ötektik nokta bileşiminin aralığı olan %2 ile %2 arasındadır ve düşük sıcaklık ötektik noktası 1436℃'dir, ancak indirgeme koşulları altında, bu cüruf fazı FeO ilavesi nedeniyle CaO-SiO2-FeO üçlü cüruf sistemi haline gelir. Bu cüruf sisteminde CaO ve SiO2 oranı değişmeden kalır. Cüruf fazının erime noktası, FeO içeriğinin artmasıyla keskin bir şekilde artar. Saf üçlü cüruf sisteminde, 1093℃ kadar düşük olabilir ve düşük erime noktalı cüruf fazı, peletlerin azalmasını ve genişlemesini daha da kötüleştirecektir.
Doğal alkalinite altında, peletlerin azalma genleşme hızı, MgO içeriğinin artmasıyla biraz azalır, ancak açık değildir. Bunun nedeni, SiO1700 içeriği %2 olduğunda 90℃ erime noktasına sahip doğal alkalilik ve doğal MgO pelet cüruf fazıdır. MgO ilavesiyle, cüruf fazına MgO-SiO2 ikili sistemi hakimdir, ancak düşük sıcaklıktaki ötektik sıcaklığı da düşük ötektik sıcaklığa sahiptir. 1543°C. Alkalinite ve MgO birlikte çalıştığında, alkaliliğin peletlerin genleşme hızındaki azalma üzerindeki etkisi, aynı MgO içeriği altındaki doğal MgO içeriği ile temelde aynıdır. MgO eklendiğinde, cüruf fazının erime noktası, MgO'nun cüruf fazına eritilmesiyle artar. Aynı zamanda cüruf fazının erime noktası da cüruf fazında MgO tarafından arttırılır.
Bu nedenle, aynı alkalilik altında, MgO içeriğinin arttırılması, indirgeme genişlemesini azaltabilir.
Oksitlenmiş peletlerdeki hematitin hacim genişlemesi, manyetit ve floatite indirgenir. Bu genişleme esas olarak hematit manyetite indirgendiğinde kristal yapının değişmesinden kaynaklanır. Peletlerin azalma genleşme hızı, gang bileşimi ve cüruf fazının hematit parçacıklarının indirgenmesiyle oluşturulan strese dayanma yeteneği ile ilgilidir.
Yüksek erime noktalı cüruf fazının indirgeme işlemi sırasında eritilmesi kolay değildir ve yüksek mukavemeti korumak, peletlerin azalma genleşme oranını etkili bir şekilde sınırlayabilirken, düşük erime noktalı cüruf fazı, peletlerin redüksiyon genişlemesini kötüleştirecektir.
Peletlerin %20'nin altındaki azalma genleşme oranı, normal genleşme aralığına aittir ve speküler peletlerin alkalinitesi, 0.2'den az veya 1.0'a eşit veya daha büyük bir aralıkta kontrol edilmelidir.
Ancak genel olarak endüstriyel üretimde peletlerin küçülme genleşme hızının %15'in altında kontrol edilmesi gerekmektedir. %3.0~%3.1 SiO2 içeren doğal alkaliniteye sahip spekülerit peletler için, indirgeme genişleme oranı %15'ten azdır ve indirgeme derecesi sadece %62.2'dir. Alkaliniteyi artırarak indirgeme derecesini iyileştirirken, alkaliniteyi sadece artış derecesi 1.0'a ve MgO içeriği %3.0'a veya alkalinite 1.2'ye ve MgO içeriği ≥1.0% olduğunda azaltmak gerekir, indirgeme genişlemesi olabilir oranı %15'in altında olmalıdır.
Alkalinite ve MgO içeriğinin düşük sıcaklıkta indirgeme pulverizasyonuna etkisi. Düşük sıcaklıkta indirgeme pulverizasyonu (RDI), peletlerin yüksek fırının üst kısmında veya 400°C ila 600°C sıcaklık aralığında doğrudan indirgeme şaftlı fırının üst kısmında indirgendiğinde toz üretme eğilimini yansıtır. Düşük sıcaklıktaki azalma ve pulverizasyonun ana nedeni, hematitin manyetite indirgenmesi sırasında kristal yapının dönüştürülmesinden kaynaklanan hacim genişlemesi ve kafes distorsiyonudur.
Peletler önceden ısıtıldığında ve kavrulduğunda oluşan üç ana bağlama yöntemi vardır:
Demir oksit yeniden kristalleştirme, silikat bağı ve ferrit bağı.
Bunlar arasında, hematit yeniden kristalleşme bağı en yaygın ve en güçlü olanıdır, ancak hematit indirgeme koşulları altında son derece kararsızdır, hematit manyetite indirgendiğinde silikat bağlama fazı korunabilir. Değişiklik.
Bu nedenle, aynalı topakların düşük sıcaklıktaki indirgeme ve toz haline getirilmesini azaltmak için bir akı ekleyerek bu tek biçimli dağılımı arttırmak ve düşük sıcaklıktaki indirgeme koşulları altında stabil bir bağlanma fazını korumak mümkündür.
Doğal alkalinite ve doğal MgO içeriğine sahip peletler, daha az silikat bağlama fazı ile esas olarak hematit katı faz difüzyon konsolidasyonudur. Bu nedenle, düşük sıcaklık azaltma sırasında daha fazla toz üretilir ve RDI-3.15mm değeri 12.75'e kadar çıkar. %. Doğal MgO içeriği altında, alkalinite 0.2'ye yükseldi ve pelet düşük sıcaklıkta azaltma pulverizasyon oranı RDI-3.15mm değeri hızla 0.52'ye düştü; alkalinite artmaya devam etti ve RDI-3.15mm değeri temel olarak yaklaşık %0.5'te tutuldu. Bunun nedeni, CaO ilavesinin, peletlerin, ön ısıtma ve kalsinasyon sırasında düşük sıcaklıktaki indirgeme sırasında stabil olan daha fazla silikat sıvı fazı oluşturmasını sağlaması ve böylece peletlerin düşük sıcaklıkta azaltılmasını ve toz haline getirilmesini azaltma amacına ulaşmasıdır.
Doğal alkalinite altında, MgO içeriğinin artması, peletlerin düşük sıcaklıkta indirgemesi ve toz haline getirme oranı, RDI-3.15mm, tümü %3.0'ın altına düşer. Alkalinite ve MgO birlikte çalıştığında, düşük sıcaklıkta indirgeme pulverizasyonunda peletlerin RDI-3.15mm değeri düşüktür. RDI-3.15mm, alkalilikteki artışla azalır ve MgO içeriğindeki artışla hafifçe artar. Bunun nedeni MgO Sıvı fazda silikat oluşumunu engelleyebilir.
Alkalinite ve MgO içeriğinin yeniden akış özelliklerine etkisi. Peletlerin ergitme özellikleri, yüksek fırının alt kısmındaki yumuşak ergitme bölgesinde pelet oluşumunu ve yumuşak ergitme bölgesindeki performansını yansıtabilir. Yükün yeniden akış özellikleri, yüksek fırının çalışması üzerinde daha büyük bir etkiye sahiptir. Peletlerin yumuşama sıcaklığı düşüktür ve yeniden akış aralığı geniştir ve yüksek fırının alt kısmındaki yeniden akış bölgesinin hava geçirgenliği zayıflayacaktır, bu da indirgeyici gazın ve şarjın konveksiyonuna elverişli değildir ve azaltma sürecini ciddi şekilde etkiler.
Doğal alkali ve doğal MgO içeriğine sahip asit peletleri 1009°C'de yumuşamaya başlar ve damlama sıcaklığı 1272°C'dir. Doğal MgO içeriği ile alkalinite 1.2'ye yükselir, peletlerin yumuşama sıcaklığı 1034°C'ye yükselir, yumuşama aralığı ve yumuşama aralığı daralır ve damlama sıcaklığı da 1299°C'ye yükselir. Alkalinite 1.2 olduğunda, MgO içeriğinin arttırılması, yumuşama başlangıç sıcaklığını ve damlama sıcaklığını artırabilir. MgO içeriği %1.0 olduğunda, pelet yumuşatma sıcaklığı 1072°C'ye yükselecek, damlama sıcaklığı 1319°C'ye ulaşacak, MgO içeriği artmaya devam edecek ve pelet yumuşatma sıcaklığı artmayacak Daha fazla artışla, damlama sıcaklığı arttı .
Peletlerin yeniden akış özellikleri, esas olarak, indirgeme sırasında üretilen fusterit ve cüruf gibi düşük erime noktalı sıvı fazlardan etkilenir. Asit peletlerinin zayıf yüksek sıcaklıkta yeniden akış özellikleri, esas olarak, indirgeme işlemi sırasında FeO bakımından zengin olivin cüruf fazının düşük erime noktasından kaynaklanır ve MgO ilavesi, cüruf fazının erime noktasını artırabilir. Yüksek erime noktasına sahip katı bir çözeltinin oluşumu, peletlerin yüksek sıcaklıkta yeniden akış özelliklerinin geliştirilmesinde de rol oynayacaktır.
Lütfen yeniden basım için bu makalenin kaynağını ve adresini saklayın: Pelet performansını artırmak için "Alkali" ve "Magnezyum"
Minhe Basınçlı Döküm Şirketi kaliteli ve yüksek performanslı Döküm Parçaları üretmeye ve sağlamaya adamıştır (metal döküm parça yelpazesi esas olarak şunları içerir: İnce Duvarlı Döküm,Sıcak Kamara Basınçlı Döküm,Soğuk Oda Döküm), Yuvarlak Servis (Döküm Servisi,Cnc İşleme,Kalıp yapımı,Yüzey İşleme).Herhangi bir özel Alüminyum döküm, magnezyum veya Zamak/çinko döküm ve diğer döküm gereksinimleri bizimle iletişime geçebilirsiniz.
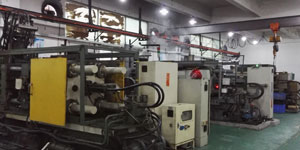
ISO9001 ve TS 16949 kontrolünde, tüm işlemler yüzlerce gelişmiş basınçlı döküm makinesi, 5 eksenli makine ve blasterlerden Ultra Sonic yıkama makinelerine kadar diğer tesisler aracılığıyla gerçekleştirilir. Müşterinin tasarımını gerçeğe dönüştürmek için deneyimli mühendisler, operatörler ve müfettişlerden oluşan ekip.
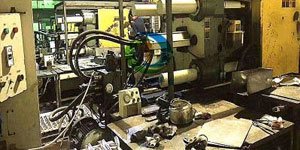
Dökümlerin sözleşmeli üreticisi. Yetenekler, 0.15 lbs'den başlayan soğuk oda alüminyum döküm parçaları içerir. 6 lbs'ye kadar, hızlı değişim kurulumu ve işleme. Katma değerli hizmetler arasında polisaj, titreşim, çapak alma, kumlama, boyama, kaplama, kaplama, montaj ve kalıplama yer alır. Çalışılan malzemeler arasında 360, 380, 383 ve 413 gibi alaşımlar bulunur.
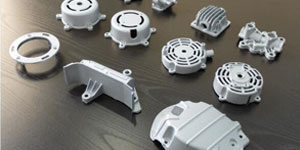
Çinko pres döküm tasarım yardımı/eşzamanlı mühendislik hizmetleri. Hassas çinko dökümlerin özel üreticisi. Minyatür dökümler, yüksek basınçlı dökümler, çok kızaklı kalıp dökümleri, geleneksel kalıp dökümleri, birim kalıp ve bağımsız kalıp dökümleri ve boşluklu sızdırmaz dökümler üretilebilir. Dökümler, +/- 24 inç toleransta 0.0005 inç'e kadar uzunluk ve genişliklerde üretilebilir.
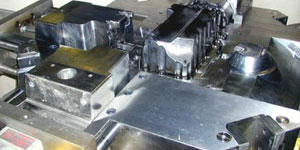
ISO 9001: 2015 sertifikalı döküm magnezyum üreticisi, Yetenekler arasında 200 ton sıcak odaya ve 3000 ton soğuk odaya kadar yüksek basınçlı magnezyum kalıp dökümü, takım tasarımı, cilalama, kalıplama, işleme, toz ve sıvı boyama, CMM özelliklerine sahip tam kalite güvencesi bulunur , montaj, paketleme ve teslimat.
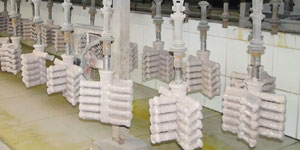
ITAF16949 sertifikalı. Ek Döküm Hizmeti Dahil yatırım dökümleri,kum dökümü,Yerçekimi Döküm, Kayıp Köpük Döküm,Savurma döküm,Vakumlu Döküm,Kalıcı Kalıp Döküm,.Yetenekler arasında EDI, mühendislik yardımı, katı modelleme ve ikincil işleme yer alır.
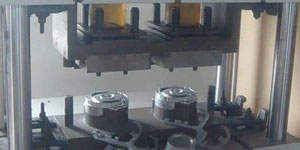
Döküm Endüstrileri Arabalar, Bisikletler, Uçaklar, Müzik aletleri, Deniz Araçları, Optik cihazlar, Sensörler, Modeller, Elektronik cihazlar, Muhafazalar, Saatler, Makineler, Motorlar, Mobilya, Mücevher, Jigler, Telekom, Aydınlatma, Tıbbi cihazlar, Fotoğraf cihazları, Robotlar, Heykeller, Ses ekipmanları, Spor ekipmanları, Aletler, Oyuncaklar ve daha fazlası.
Bundan sonra ne yapmanıza yardımcı olabiliriz?
∇ Ana Sayfaya Git Çin Döküm
→Döküm Parçaları-Ne yaptığımızı öğren.
→ Hakkında İlgili İpuçları Pres Döküm Hizmetleri
By Minghe Döküm Üreticisi |Kategoriler: Faydalı Makaleler |Malzeme Etiketler: Alüminyum Döküm, Çinko Döküm, Magnezyum Döküm, Titanyum Döküm, Paslanmaz Çelik Döküm, Pirinç Döküm,Bronz Döküm,Döküm Videosu,Tarihçe,Alüminyum Döküm |Yorumlar Kapalı