Alüminyum-Magnezyum Alaşımlı Döküm Kalıbının Isıl İşlem Süreci Tartışması
Sertleştirme işleminin ve yüzey güçlendirme işleminin kullanılması, kalıbın performansını ve ömrünü artırmak için önemli bir üretim yoludur. Alüminyum-magnezyum alaşımlı kalıp döküm kalıplarının çalışma koşulları ve performans gereksinimlerine göre, bu makale kalıbın özelliklerini analiz eder. ısıl işlem ve yaygın işlemler ayrıntılı olarak incelenir ve ısıl işlem işlem özelliklerinin makul bir formülasyonunun kalıp yüzey sertliğini, aşınma direncini, çekirdek mukavemetini ve tokluğunu sağlayabileceğine ve metal sıvı korozyonunu önleyebileceğine işaret eder. Kalıba yapışmak, hurda oranını etkili bir şekilde azaltabilir ve kalıbın hizmet ömrünü önemli ölçüde artırabilir.
Alüminyum-magnezyum alaşımları, düşük yoğunlukları ve yüksek mukavemetleri nedeniyle giderek daha yaygın olarak kullanılmaktadır. Bunlar arasında, gelişmiş bir kesme işlemi olarak alüminyum-magnezyum alaşımlı kalıp döküm teknolojisi, yüksek üretim verimliliği, hammadde tasarrufu, üretim maliyetlerini düşürme, iyi ürün performansı ve yüksek hassasiyet özelliklerine sahiptir. , Ağırlıklı olarak elektronik, otomobil, motor, ev aletleri ve diğer endüstrilerde kullanılan, bazı yüksek performanslı, yüksek hassasiyetli, yüksek tokluğa sahip yüksek kaliteli alüminyum-magnezyum alaşımlı ürünler de büyük uçaklara, gemilere ve diğer endüstrilere göreceli olarak uygulanmıştır. yüksek teknik gereksinimler.
Alüminyum-magnezyum alaşımlı pres döküm kalıplarının çalışma koşulları ve performans gereksinimleri
Alüminyum-magnezyum alaşımlı kalıp döküm kalıbı, bir kalıp döküm makinesinde alüminyum-magnezyum alaşımlı dökümlerin kalıp dökümü için kullanılan bir kalıplama kalıbıdır. Alüminyum alaşımının erime noktası 600~750 ℃ ve magnezyum alaşımının erime noktası 600~700 ℃'dir. Çalışma yüzeyi sıcaklığı genellikle 500~600 ℃'ye kadar çıkabilir. Boşluk, mandrel ve nozülün yüzeylerinin tümü şiddetli sıcaklık dalgalanmalarına maruz kalır ve kalıbın yüzeyi termal yorulma çatlaklarına eğilimlidir. Ek olarak, alüminyum-magnezyum alaşımının, kalıp döküm üretiminin sürekli çalışmasını etkileyen kalıp döküm işlemi sırasında kalıbın yüzeyine yapışması kolaydır. Sıvı alüminyum-magnezyum alaşımı, kalıbın yüzeyinde güçlü bir erozyon etkisine sahiptir. Bu nedenle, alüminyum-magnezyum alaşımlı kalıp döküm kalıpları üretmek için, kalıp malzemesinin yüksek tavlama stabilitesine ve yaklaşık 600°C'de soğuk ve ısı yorulmasına karşı dayanıklı olması ve yüksek sıcaklığa, yüksek basınca, yüksek hıza karşı iyi bir dirence sahip olması gerekir. ve sıvı alüminyum-magnezyum alaşımlarının yüksek erozyon direnci. Kalıbın mukavemeti ve tokluğu ve aynı zamanda, kalıp malzemesinin potansiyelinden yararlanmak ve kalıbın hizmet ömrünü artırmak için doğru ısıl işlem gereklidir. Şu anda, kalıp imalatında yaygın olarak kullanılan alüminyum-magnezyum alaşımlı kalıp döküm çelikleri şunları içerir: 3Cr2W8V çelik, 4Cr5MoSiV1 çelik, 4Cr3Mo3SiV çelik, 4Cr5MoSiV çelik ve yeni çelik türleri 4Cr5Mo2MnSiV1 çelik ve 3Cr3Mo3VNb çelik.
Alüminyum-magnezyum alaşımlı kalıp döküm kalıbının üretim süreci rotası
Alüminyum-magnezyum alaşımlı kalıp döküm kalıbının üretim süreci: körleme → dövme → küreselleştirme tavlama → işleme → söndürme, tavlama → onarım, taşlama, parlatma → nitrürleme (nitrokarbürleme) → montaj ve kullanımdır.
Alüminyum-magnezyum alaşımlı kalıp döküm kalıbının güçlendirilmesi ve sertleştirilmesi işlemi
Alüminyum-magnezyum alaşımlı kalıp döküm kalıbının sertleştirme işlemi, kalıbın gerekli yapısını ve performansını elde etmek için çeliğin yapısını değiştirmektir. Isıl işlem, ısıl işlem proses özelliklerini belirlemek için kalıp malzemesine, kalıp şekline, boyutuna ve karmaşıklığına dayanmalıdır.
3.1 Ön ısıl işlem
Kalıp döküm kalıbının ön ısıl işlemi üç işlemi benimseyebilir: sürekli tavlama, izotermal tavlama ve su verme ve tavlama ısıl işlemi. Amaç, çeliğin mukavemetini ve tokluğunu iyileştirmek için son ısıl işlemden önce üniform bir yapı ve dispers karbür elde etmektir. Sürekli tavlama işlemi nispeten basittir ve daha iyi taneli bir perlit yapısı da elde edilebilir. Karmaşık şekillere ve yüksek gereksinimlere sahip kalıp döküm kalıpları için, daha ideal bir granüler perlit yapı elde etmek için izotermal tavlama kullanılabilir.
3.2 Söndürme ve ön ısıtma
Döküm kalıp çeliği çoğunlukla düşük termal iletkenliğe sahip yüksek alaşımlı çeliktir. Ön ısıtma önlemleri genellikle söndürme ve ısıtma sırasında alınır. Ön ısıtma sayısı ve sıcaklık, kalıp çeliğinin bileşimine ve kalıp deformasyon gereksinimlerine bağlıdır. Düşük su verme sıcaklığı, basit şekil ve düşük deformasyon gereksinimleri olan kalıplar için, su verme ve çatlama olmadan ısıtma sırasında bir ön ısıtma (800~850 ℃) gereklidir. Daha yüksek sıcaklıkta su verme, karmaşık şekiller ve yüksek deformasyon gereksinimleri olan kalıplar için ikincil ön ısıtma (600-650°C, 800-850°C) gereklidir. Amaç, ısıtma işlemi sırasında oluşan stresi azaltmak ve aynı zamanda kalıbın genel yapısını tek tip hale getirmektir.
3.3 Söndürme ısıtması
Döküm kalıbının söndürme ısıtma sıcaklığı, her bir çelik sınıfının söndürme ısıtma özelliklerine göre uygulanabilir. Örneğin, 3Cr2W8V çeliğinin su verme sıcaklığı 1050~1150℃ ve H13 çeliğinin su verme sıcaklığı 1020~1100℃'dir. İki çeliğin su verme sıcaklığının arttırılması, kalıp döküm kalıbının yüksek sıcaklık dayanımını ve termal yorulma direncini artırabilir, ancak bu, kalıbın deformasyonunu artıracaktır. Tuz banyosu fırınında ısıtırken, kalıp yüzeyinde oksidatif dekarburizasyondan kaçınmak için deoksidasyonu iyi olan bir baryum klorür tuz banyosu kullanılmalı ve deoksidasyon sıklıkla yapılmalıdır. Kutu tipi bir rezistans fırınında ısıtırken koruyucu bir atmosfer benimsenmelidir; veya paketlemeden sonra genel bir kutu tipi rezistans fırınında ısıtma. Karbürlerin tam çözünmesini sağlamak, düzgün östenit elde etmek ve iyi bir yüksek sıcaklık performansı elde etmek için, kalıp döküm kalıplarının su verme ve ısıtma tutma süresi uygun şekilde uzatılmalıdır. Genel olarak, tuz banyosu fırınındaki ısıtma tutma katsayısı 0.8-1.0 dak/mm'dir.
3.4 Söndürme soğutması
Yağda su verme hızı hızlıdır ve iyi performans elde edilebilir ancak deformasyon ve çatlama eğilimi büyüktür. Genellikle basit şekillere ve düşük deformasyon gereksinimlerine sahip yağ soğutmalı kalıp döküm kalıpları kullanılır; karmaşık şekillere ve yüksek deformasyon gereksinimlerine sahip kalıp döküm kalıpları için, kalıp deformasyonunu ve çatlamayı önlemek için hiyerarşik su verme kullanılmalıdır. Söndürme soğutması, bir vakum direnci fırınında söndürme deformasyonunu, ısıtmayı ve söndürmeyi azaltmak için mümkün olduğunca yavaş olmalıdır, soğutma, gazla söndürme olarak kabul edilebilir. Tuz banyosunda ısıtma ve su verme ve soğutma sırasında derecelendirmeli su verme uygulanabilir. Kalıp su verildiğinde ve soğutulduğunda, genellikle 150-200°C'ye soğutulur ve daha sonra ıslandıktan hemen sonra temperlenir. Oda sıcaklığına soğumasına izin verilmez.
3.5 Temperleme
Kalıp döküm kalıbının sertliği, temperleme ile elde edilir ve kalıp döküm kalıbı boşluğunun sertliği, kalıbın sıcak ve soğuk yorulma ömrünü doğrudan etkiler. Farklı malzemeler, farklı su verme sıcaklığı ve tavlama sıcaklığı da farklıdır. Örneğin, 3Cr2W8V çelik alüminyum-magnezyum alaşımlı kalıp döküm kalıbının sertliği genellikle 42~48HRC'dir ve tavlama sıcaklığı genellikle 560~620 ℃ arasında seçilir, ancak yüksek sıcaklıkta su verme kullanılıyorsa, tavlama sıcaklığı aşağıdaki kadar yüksektir. 670℃. 1150°C'de su verme ve 650°C'de tavlama sonrası sertlik 45HRC'dir; 1050°C'de su verme ve 650°C'de temperleme sonrası sertlik ise 35HRC'dir. H13 çelik alüminyum-magnezyum alaşımlı kalıp döküm kalıbının sertliğinin 44~50HRC olması gerekir. H13 çeliğinin ikincil sertleşme zirvesi, 500°C'de temperleme sırasında ortaya çıkar, ancak zirvenin boyutu, söndürme sıcaklığı ile ilgilidir. Temperleme sıcaklığı genellikle 560~620℃'dir. Temperleme 2 ila 3 kez yapılmalıdır. İlk tavlamanın sıcaklığı daha düşük olabilir. İlk temperlemeden sonra sertlik değerini ölçün. Sertlik gereksinimine ulaşılırsa, sertliğin düşmesini önlemek için tavlama sıcaklığı 20-30 ℃ düşürülmelidir. Sertlik çok yüksekse, yüksek sertliğe göre sertlik gereksinimini karşılamak için tavlama sıcaklığını uygun şekilde ayarlayın. Üçüncü tavlama tokluğu iyileştirmektir, tavlama sıcaklığı ikinciden daha yüksek olmalıdır.
İkincil tavlama sıcaklığı 30~50 ℃ daha düşüktür. Temperleme ve bekletme süresi, su verme sırasında oluşan stresi ortadan kaldırmak ve kalıp çatlaklarının oluşumunu azaltmak için yeterli olmalıdır. Her tavlama için bekletme süresi 2 saattir ve büyük kalıplar için bekletme süresi uygun şekilde uzatılır. Söndürmeden sonra döküm kalıbının yüksek termal stresi ve mikro yapı stresi nedeniyle, kalıp genellikle 150-200°C'ye soğutulduktan hemen sonra temperlenir.
Alüminyum-magnezyum alaşımlı kalıp döküm kalıbının yüzey güçlendirme işlemi
Su verme ve tavlamadan sonra alüminyum-magnezyum alaşımlı kalıp döküm kalıbının yüzey sertliği çok yüksek değildir. Çekirdek parça hala yeterli mukavemet ve tokluğu korurken kalıbın yüzeyinde yüksek sertlik ve aşınma direnci elde etmek ve alüminyum-magnezyum alaşımlı kalıp döküm kalıbının yapışma önleyici performansını iyileştirmek için yüzey nitrürleme veya nitrürleme kalıp üzerinde yapılabilir. Karbürizasyon tedavisi.
4.1 Nitrürleme işlemi
Nitrürleme, yüzey tabakasındaki azot konsantrasyonunu artırmak için çeliğin yüzeyini nitrürleme işlemidir. Nitrürlemenin amacı, kalıp parçalarının deformasyonunu azaltmak, alüminyum-magnezyum alaşımlı kalıp döküm kalıplarının yüzey sertliğini, aşınma direncini, yorulma mukavemetini ve tutukluk direncini iyileştirmek, kalıbın atmosfere ve aşırı ısıtılmış buhara karşı korozyon direncini iyileştirmektir. ve tavlama ve yumuşamaya karşı direnci arttırın. Çentik hassasiyeti. Katı nitrürleme, sıvı nitrürleme ve gaz nitrürleme yaygın nitrürleme yöntemleridir. İyon nitrürleme, vakum nitrürleme, elektrolitik nitrürleme ve yüksek frekanslı nitrürleme gibi yeni teknolojiler, nitrürleme döngüsünü büyük ölçüde kısaltabilir, yüksek kaliteli bir nitrürleme katmanı elde edebilir ve işletmelerin ekonomik verimliliğini artırabilir, bu nedenle üretimde yaygın olarak kullanılırlar.
4.2 Nitrokarbürleme
Nitrokarbürleme, amonyak artı alkol sıvıları (metanol, etanol) ve üre, formil yapıştırıcı ve trietanol yapıştırıcı gibi birlikte nüfuz eden ortamlardır. Termal bozunma reaksiyonu, alüminyum-magnezyum alaşımları tarafından kalıpla dökülen aktif nitrojen ve karbon atomlarını üretmek için belirli bir sıcaklıkta gerçekleşir. Kalıp yüzeyi emildikten sonra, nitrojen bazlı bir nitrokarbürizasyon tabakası elde etmek için kalıp yüzey tabakasına yayılır ve nüfuz eder, böylece kalıp daha yüksek yüzey sertliği, yorulma direnci, aşınma direnci ve korozyon direnci elde eder. Nitrokarbürleme yöntemleri sıvı ve gaz yöntemlerini içerir ve üretimde kullanılan yöntemlerin çoğu gaz nitrokarbürlemedir. H13 çelik alüminyum alaşımlı kalıp döküm kalıbı, yüksek sıcaklık tuz banyosu fırınında 550 ℃ × 40 dakika ve 850 ℃ × 40 dakika ön ısıl işlemin iki aşamasında ısıtılır, 1030 ℃'de söndürülür, 600 ℃'de temperlenir ve daha sonra tabi tutulur. 580 ℃'de gaz nitrokarbürleme ısıl işlemine. Sertlik 900HV'nin üzerindedir, matris sertliği 46 ~ 48HRC'dir, kalıbın aşınma direnci, yorulma direnci ve korozyon direnci önemli ölçüde iyileştirilmiştir ve ömrünü etkili bir şekilde artıran yapışma, soyulma, çizik ve korozyon yoktur. kalıba dökmek.
Sonuç
Önemli bir işleme ekipmanı olarak, alüminyum-magnezyum alaşımlı kalıp döküm kalıpları, şirketin ürün kalitesi ve ekonomik faydaları üzerinde doğrudan bir etkiye sahiptir. Araştırma ve istatistikler, uygun olmayan ısıl işlem sürecinden kaynaklanan kalıp arızalarının toplam arızaların yaklaşık %50'sini oluşturduğunu göstermektedir. Bu nedenle, güçlendirme ve toklaştırma işleminin ve yüzey güçlendirme işleminin makul seçimi ve ısıl işlem proses özelliklerinin sıkı kontrolü, kalıp performansını ve ömrünü iyileştirmenin önemli yollarıdır. Alüminyum-magnezyum alaşımlı kalıp döküm kalıplarının üretiminde, kalıp çalışma koşullarına göre arıza nedenlerini analiz etmek ve incelemek ve kalıp yüzey sertliğini, aşınma direncini, çekirdek mukavemetini ve tokluğunu sağlamak, metali önlemek için ısıl işlem süreçlerini makul bir şekilde formüle etmek gerekir. sıvı korozyon ve kalıp yapışması ve reddetme oranını etkili bir şekilde azaltır, kalıbın hizmet ömrünü önemli ölçüde artırır.
Lütfen yeniden basım için bu makalenin kaynağını ve adresini saklayın: Alüminyum-Magnezyum Alaşımlı Döküm Kalıbının Isıl İşlem Süreci Tartışması
Minhe Basınçlı Döküm Şirketi kaliteli ve yüksek performanslı Döküm Parçaları üretmeye ve sağlamaya adamıştır (metal döküm parça yelpazesi esas olarak şunları içerir: İnce Duvarlı Döküm,Sıcak Kamara Basınçlı Döküm,Soğuk Oda Döküm), Yuvarlak Servis (Döküm Servisi,Cnc İşleme,Kalıp yapımı,Yüzey İşleme).Herhangi bir özel Alüminyum döküm, magnezyum veya Zamak/çinko döküm ve diğer döküm gereksinimleri bizimle iletişime geçebilirsiniz.
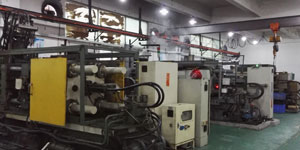
ISO9001 ve TS 16949 kontrolünde, tüm işlemler yüzlerce gelişmiş basınçlı döküm makinesi, 5 eksenli makine ve blasterlerden Ultra Sonic yıkama makinelerine kadar diğer tesisler aracılığıyla gerçekleştirilir. Müşterinin tasarımını gerçeğe dönüştürmek için deneyimli mühendisler, operatörler ve müfettişlerden oluşan ekip.
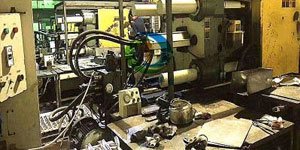
Dökümlerin sözleşmeli üreticisi. Yetenekler, 0.15 lbs'den başlayan soğuk oda alüminyum döküm parçaları içerir. 6 lbs'ye kadar, hızlı değişim kurulumu ve işleme. Katma değerli hizmetler arasında polisaj, titreşim, çapak alma, kumlama, boyama, kaplama, kaplama, montaj ve kalıplama yer alır. Çalışılan malzemeler arasında 360, 380, 383 ve 413 gibi alaşımlar bulunur.
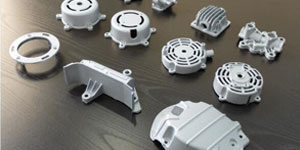
Çinko pres döküm tasarım yardımı/eşzamanlı mühendislik hizmetleri. Hassas çinko dökümlerin özel üreticisi. Minyatür dökümler, yüksek basınçlı dökümler, çok kızaklı kalıp dökümleri, geleneksel kalıp dökümleri, birim kalıp ve bağımsız kalıp dökümleri ve boşluklu sızdırmaz dökümler üretilebilir. Dökümler, +/- 24 inç toleransta 0.0005 inç'e kadar uzunluk ve genişliklerde üretilebilir.
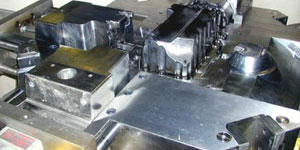
ISO 9001: 2015 sertifikalı döküm magnezyum üreticisi, Yetenekler arasında 200 ton sıcak odaya ve 3000 ton soğuk odaya kadar yüksek basınçlı magnezyum kalıp dökümü, takım tasarımı, cilalama, kalıplama, işleme, toz ve sıvı boyama, CMM özelliklerine sahip tam kalite güvencesi bulunur , montaj, paketleme ve teslimat.
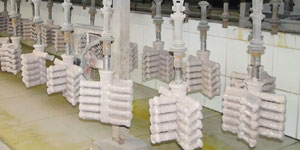
ITAF16949 sertifikalı. Ek Döküm Hizmeti Dahil yatırım dökümleri,kum dökümü,Yerçekimi Döküm, Kayıp Köpük Döküm,Savurma döküm,Vakumlu Döküm,Kalıcı Kalıp Döküm,.Yetenekler arasında EDI, mühendislik yardımı, katı modelleme ve ikincil işleme yer alır.
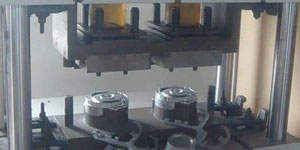
Döküm Endüstrileri Arabalar, Bisikletler, Uçaklar, Müzik aletleri, Deniz Araçları, Optik cihazlar, Sensörler, Modeller, Elektronik cihazlar, Muhafazalar, Saatler, Makineler, Motorlar, Mobilya, Mücevher, Jigler, Telekom, Aydınlatma, Tıbbi cihazlar, Fotoğraf cihazları, Robotlar, Heykeller, Ses ekipmanları, Spor ekipmanları, Aletler, Oyuncaklar ve daha fazlası.
Bundan sonra ne yapmanıza yardımcı olabiliriz?
∇ Ana Sayfaya Git Çin Döküm
→Döküm Parçaları-Ne yaptığımızı öğren.
→ Hakkında İlgili İpuçları Pres Döküm Hizmetleri
By Minghe Döküm Üreticisi |Kategoriler: Faydalı Makaleler |Malzeme Etiketler: Alüminyum Döküm, Çinko Döküm, Magnezyum Döküm, Titanyum Döküm, Paslanmaz Çelik Döküm, Pirinç Döküm,Bronz Döküm,Döküm Videosu,Tarihçe,Alüminyum Döküm |Yorumlar Kapalı