Rulet Döküm Parçalarının Döküm Süreci
Orta ve ağır plakalı soğutma yatağının haddeleme plakasının döküm işlemi ve malzemesi üzerine yapılan araştırmalarla, çoklu metal reçine kum maça yığınları ile rulet demir dökümleri yapmak için yeni bir yöntem incelenmiştir. Yöntemin basit süreci, yüksek üretkenliği, yüksek döküm kapsamlı performansı ve iyi yüzey kalitesi vardır.
Rulet Döküm Parçaları Döküm İşleminin Güncel Durumu
Rulet dökme demir parçalar, çapı yüksekliğinden çok daha büyük olan bir döküm tipini ifade eder. Genel olarak, ara mil deliğinin işleme gereksinimleri nispeten yüksektir, göbek ve jant daha kalındır ve ispitteki duvar incedir, bu da kolayca eşit olmayan sıcaklık ve büyük sıcaklık farkına neden olur. Hub ve jant iki sıcak noktadır. Döküm işlemi makul değilse, döküm, büzülme boşluğuna, büzülme gözenekliliğine ve çatlak kusurlarına eğilimlidir. Şu anda, çoğu yerli üretici sıradan kil kum kalıplama, tek parça döküm, teğetsel kapı enjeksiyonu ve merkezde soğutulmuş demir ile birlikte kullanılan besleyici besleme veya döküm yöntemlerini kullanarak rulet dökümleri üretmektedir. Bu yöntem geniş yer kaplar, proses verimi, verim ve üretim verimliliği düşüktür ve dökümün yüzey kalitesi kötüdür.
Rulet tipi demir dökümler-soğutma yatağı silindirlerinin (5700 adetten fazla) üretim görevini aldıktan sonra, çözülmesi gereken ilk sorun, döküm işleminin araştırılmasıdır. İşlemin basit olması gerekir, böylece döküme aşina olmayan işçiler çalışabilir. Kalıplama ve dökme alanının küçültülmesi ve mevcut üretim koşulları altında üretim ihtiyaçlarının karşılanması gerekmektedir. Döküm sürecini incelerken yine malzeme sorunlarıyla karşılaştık. Yapılan rulo levha çok kırılgandı ve üretimde hiç kullanılamadı. Döküm prosesi ve döküm malzemesinin araştırılması ile rulet döküm parçalar için yeni bir döküm prosesi türü araştırılmış ve kaliteli merdaneler üretilmiştir.
Ana Araştırma İçerikleri ve Temel Teknolojiler
1. Malzeme araştırması
Silindir plakası, soğutma yatağı ekipmanının temel bileşenlerinden biridir. İyi yüzey kalitesi ve yüksek ısı direnci gerektirir. Dökme demirin ısı direnci, esas olarak, yüksek sıcaklık oksidasyon direncine (yani, dökme demirin yüzeyinde oluşan oksit filmin Koruyucu etkiye sahip olup olmadığına) ve dökme demirin büyümesine (yani, boyutun geri döndürülemez genişlemesine) bağlıdır. yüksek sıcaklıklarda çalışan dökme demir parçalar). Bu iki özellik, dökme demirin kimyasal bileşimi ile yakından ilgilidir. Demir dökümlerin mukavemeti ve darbe direnci esas olarak alaşım elementlerinin sayısına bağlıdır, bu nedenle dökümlerin malzemesinin incelenmesi çok önemli bir konu haline gelir. Bu nedenle, malzeme üzerinde araştırma yaptık ve sadece dökümün ısı direncini iyileştirmekle kalmayıp aynı zamanda dökümün mekanik özelliklerini de sağlayan makul bir kimyasal bileşim seçimi yaptık. Silindirin orijinal tasarım malzemesi RQTSi5'tir ve kimyasal bileşimi (%) şöyledir: wC = %2.30 ~ %2.89, wSi = %4 ~ %5, wMn = %5.5 ~ %0.50, wP = %0.77 ~ %0.06, wS=%0.09~%0.062, wCr=0.089%~0.38. Mekanik özellikleri aşağıdaki gibidir: çekme mukavemeti 0.49-140MPa, sertlik 220-160 HBW. Maksimum çalışma sıcaklığı 270~750℃'dir. Bu malzemenin yüksek silikon içeriği nedeniyle, dökme demirin kırılgan geçiş sıcaklığı artar. Bu nedenle döküm çok kırılgandır ve düzensiz et kalınlığına sahip kırılgan hassas parçaların üretimi için uygun değildir. Silindir plakası bu yapının dökümüne aittir. Sonuç olarak, üretim yeni başladı. O zamanlar, malzeme sorunlarından kaynaklanan birçok atık ürün vardı. Ayrıca, RQTSi900'in malzemesi kırılgan olduğundan ve verim düşük olduğundan, çoğu yerli üretici artık bu malzemeyi merdane yapmak için kullanmamaktadır. Yukarıdaki durum göz önüne alındığında, rulo levhaların toplu hurdaya ayrılmasını önlemek ve orta ve ağır levha projesinin sorunsuz bir şekilde başlamasını sağlamak için rulo levha üretimi için ortaya çıkan bir malzemenin deneme üretimi birinci öncelik haline geldi. Pek çok deney ve gösteri ile geliştirdiğimiz yeni malzemeyi kullanmaya karar verdik. Kimyasal bileşimi: wC=%5~%3.05, wSi=%3.51~%2.9, wMn=%3.5~%0.24, wP=%0.56~%0.05, wS=%0.09~%0.010, wMo=0.030~ %0.29. Mekanik özellikleri aşağıdaki gibidir: çekme mukavemeti 0.6~580MPa, uzama %695~%8, sertlik 18~210 HBW. Maksimum çalışma sıcaklığı 280~750℃'dir. Geliştirilen malzemelerin iyi özellikleri ve yüksek verim oranı nedeniyle kullanıcılar tarafından kabul görmüştür.
Malzeme belirlendikten sonra malzeme içerikleri, sferoidizasyon işlemi, aşılama ve aşılama işlemi, fırın önü kalite kontrol vs. ele alındı ve başarılı oldu. Silindirin mekanik özellikleri, dökme demir atölyesi tarihindeki en iyi seviyeye ulaştı. Seviye.
2. Eritme sürecindeki temel sorunların üstesinden gelmek
Kimyasal bileşim belirlendikten sonra yüksek kalitede erimiş demir elde etmek için makul bir eritme işlemi gereklidir. Isıya dayanıklı sfero dökümler için küreselleştirme işlemi özellikle önemlidir (yani aşılayıcı ve küreselleştirme işlemi seçimi). Dökümlerin mekanik özellikleri, küreselleştirme işlendiğinde de iyidir. Araştırma yoluyla uygun bir aşılayıcı seçtik ve makul bir küreselleştirme süreci geliştirdik, böylece erimiş demir iyi küreselleştirilebilir, bu da sadece dökümün gücünü arttırmakla kalmaz, aynı zamanda uzamasını da arttırır ve etkisi çok iyidir.
- Küreselleştirme maddesinin seçimi Küreselleştirme maddesinin kalitesi, küreselleştirme etkisini doğrudan etkiler ve erimiş demir ve dökümlerin kalitesini etkiler. Pek çok deney ve gösterim yoluyla, sonunda, küreselleştirme maddesinin ReMg5-8 hafif nadir toprağı benimsediğini, aşılayıcının 75SiFe'yi ve dökme demirin mukavemetini ve uzamasını önemli ölçüde artırabilen benzersiz uzun etkili aşılayıcıyı benimsediğini belirledik.
- Küreselleştirme Yüksek kaliteli dökümler elde etmek için aşılayıcıların seçimi ve küreselleştirme süreçleri de çok önemlidir. Temel sorunları çözerek, uygun bir aşılayıcı seçtik ve makul bir küreselleştirme işlemi formüle ettik, bu sadece dökümün mukavemetini arttırmakla kalmadı, aynı zamanda uzamasını da arttırdı ve etkisi çok iyiydi.
Küreselleştirme işlemi, iyice kurutulması gereken bir baraj torbası kullanır. Çeşitli alaşımlar önceden ısıtılmalıdır. Baraj torbasına aşağıdan yukarıya eklenen alaşımlar şunlardır: hafif nadir toprak alaşımı %1.8 → aşılayıcı %0.8 → örtü demir levhası veya demir tozu (erimiş demir sıcaklığına göre) → alkali yüzey %0.5. Demirin 2/3'ü akıtılır ve reaksiyon tamamlandıktan sonra demir tekrar gerekli miktarda akıtılır ve akışla birlikte %0.6 ferromolibden, %0.6 aşılayıcı ilave edilir ve cüruf çıkarılır.
3. Döküm sürecindeki temel sorunların üstesinden gelmek
Yüksek kaliteli bir proje oluşturmak için firmamız, merdanelerin yüzey kalitesi, boyutsal toleransları ve işleme hacmi için ulusal standartların üzerinde gereksinimler ortaya koymuştur. Ancak, silindirler büyük partilere ve sıkı programlara sahiptir. Programı kapmak için atölye bazı döküm teknikleri kullanmak zorunda kaldı. Tanıdık olmayan geçici işçiler, rulo diskleri işleminde son derece yüksek gereksinimleri ortaya koyan rulo diskleri üretir. Döküm süreci hakkında araştırma yaptık.
- Modelleme süreci araştırması Parçanın yapısından göbeğin daha kalın ve jant tellerinin daha ince olduğu görülebilir. Şu anda, çoğu yerli üretici, göbekte yükselticiler ve teğetsel kapılar ile sıradan kum tipi tek parça döküm kullanarak bu yapıya sahip dökümler üretmektedir. Bu proses ile proses verim oranı, bitmiş ürün oranı düşüktür ve üretim verimliliği de düşüktür. Tek parça döküm için normal kum kalıp kullanılıyorsa, 5,700 adet merdane üretiminin gereken süre içerisinde tamamlanması, her gün 144 adet merdane üretilmesi, 288 adet kum kutusu, 16 adet metal kalıp ve yeterli kalıplama ve döküm alanına sahip olması gerekmektedir. gerekli ve işçilik Kompleksi, döküme aşina olmayan ve üretim gereksinimlerini karşılayamayan işçiler için çalışamaz. Bu amaçla, karşılaştırma yoluyla metal reçine kum maça istifleme işlemini seçtik, yani, maça yapmak için metal maça kutu reçine kumu kullanılır ve daha sonra kum maça birlikte düşürülür ve dökme için kutu halkasına konur. Bu süreci benimseyerek üretim ihtiyaçlarını karşılamak için sadece 8 takım metal maça kutusuna ihtiyaç vardır. Her ladin 3 istif ile, her istif 8 parça ile dökülmekte ve bir alt plaka aynı anda 48 parça ile dökülmektedir. Ortak yolluk sisteminin kullanılması nedeniyle, döküm oranı yüksektir ve reçine kum kalıp dökümlerinin yüzey kalitesi iyidir.
- Takım tasarımı ve üretimi Proses belirlendikten sonra gerekli takımları tasarladık ve ürettik.
- Maça kumunun oranlanması, karıştırılması ve üretimi. Maça kumu hazırlama süreci, reçine kumu montajı maça istifleme sürecinin anahtarıdır. Üretimin başlangıcında, reçine ve kürleme maddesinin uygun olmayan oranı nedeniyle, kum çekirdeğin metal kalıptan çıkarılması zordu ve kum çekirdeğin yüzey kalitesi çok zayıftı. Oranın deneme üretimi sonunda reçine, kürleme maddesi ve ham kum oranını belirledi ve nitelikli kum maçaları üretti. Oran: 0.45~0.224mm (40/70 mesh) ovma kumu %100, reçine %1.8-%2'dir. ham kum ağırlığı ve kürleme maddesi reçinenin %30 - %50'sidir. Karıştırma: Reçine kumu karıştırmak için S2512C kum karıştırıcı kullanılır. Tartılan ham kumu kum karıştırıcıya ekleyin ve ardından kürleme maddesini ekleyin, 8-10 dakika karıştırmaya başlayın, ardından reçineyi ekleyin, karıştırın ve 8-10 dakika öğütün ve ardından kumu çıkarın. Kum çekirdeği üretimi: silin maça kutusunun iç yüzeyini üretimden önce temizleyin, bir ayırıcı madde uygulayın, maça yaparken kumu eşit şekilde dövün ve maça tamir ederken boyutun doğru olduğundan emin olun. Hazırlanan çekirdekler sırayla numaralandırılmıştır ve alkol bazlı grafit kullanılmıştır. Boyayı iki kez fırçalayın. Boya tutuşturulduktan sonra, kum çekirdeğinin yüzeyini düzgün bir şekilde cilalamak için kuru bir bez kullanın.
- Döküm sistemi seçimi Döküm sisteminin boyutu, dökümlerin kalitesini doğrudan etkiler. Döküm sisteminin alanı çok küçük ise yetersiz döküm ve soğuk bariyerler gibi kusurlar kolaylıkla oluşur. Çok büyükse, dökümlerden temizlemek zordur. Döküm sfero dökümden yapılmıştır. Üretime ilk başladığımızda şaftın başına 4 adet iç kızak kurduk. Sonuç olarak, kapının temizlenmesi nedeniyle silindir diski genellikle hurdaya ayrıldı. Daha sonra dökümlerin şekil ve ağırlıklarına göre deneyler yaparak makul bir yolluk sistemi seçtik ve kaliteli dökümler ürettik. Grafitleşme genişlemesinden ve kendi kendine besleme özelliklerinden tam olarak yararlanıyoruz ve yükseltici olmayan bir besleme döküm yöntemini benimsiyoruz. Her silindirin başında sadece iki adet 80mm×40mm düz kapı açılır. Bu dökme sistemi yalnızca erimiş demirden tasarruf sağlamakla kalmaz, aynı zamanda dökme yükselticinin temizlenmesi için gereken çalışma saatlerini de azaltır ve dökümün yüzey kalitesi de iyidir.
- İstifleme merdanelerinin sayısının belirlenmesi İstif döküm teknolojisi kullanılarak, her seferinde dökülen dökümlerin sayısı, dökümlerin kalitesini doğrudan etkiler. Çok fazla döküm, yetersiz besleme nedeniyle deliklerin büzülmesine eğilimlidir. Çok az döküm, iş gücü verimliliği ve proses verimi çok düşük. Araştırma ekibi deneme üretimine başladığında kaliteyi sağlamak için istif başına sadece 6 adet dökülmüştür. Sürekli üretim tecrübesi birikimimizle, dikkatli hesaplamalarımıza göre artık istif başına 8 adet ve 3 istif başına bir ladin döküyoruz. Sonuç olarak, sadece dökümlerin kalitesini garanti etmekle kalmaz, aynı zamanda işgücü verimliliğini de artırır.
- Dökme sıcaklığı seçimi. Döküm sıcaklığı yüksek olan dökümler gözeneklilik ve büzülme gibi kusurlara eğilimliyken, döküm sıcaklığı çok düşük olduğundan yetersiz döküm ve yüzeyde demir çekirdekleri gibi kusurlara neden olmaz. Deneyler yoluyla 1280~1300 makul bir dökme sıcaklığı belirledik. ℃, nitelikli dökümler üretin.
- Boks zamanının kontrolü. Boks çok erken yapılırsa dökümlerin deforme olması kolaydır ve daha sonra dökmeyi etkiler. Dökümlerin boyutuna ve miktarına göre vuruş süresini 6 saat olarak belirledik.
Kalite Kontrolü
Üretilen silindirlerin kalitesini sağlamak için sıkı bir denetim sistemi kurduk: her silindir, döküm testi için bir test bloğu ile bağlanmalıdır ve test bloğunun mekanik özellikleri, metalografik yapısı ve kimyasal bileşimi %100 test edilir. . Kalifiye olmayanlar fabrikadan çıkmayacak.
Üretim Etkisi
- Metal reçine kum çekirdek montajının çok gruplu istifleme işlemi ile geliştirilen silindir disk, yüksek mukavemete ve iyi yüzey kalitesine sahiptir. Çeşitli özellikleri orijinal tasarım malzemesinin çok ötesindedir ve kullanıcıların ihtiyaçlarını karşılar.
- Bu işlemi benimsedikten sonra, kumun demire oranı sadece 1.5:1'dir, bu da yerli ileri teknoloji seviyesinden (3~4.5):1 çok daha düşüktür, bu da çok fazla reçine kumu tasarrufu sağlar.
- İşlemin çalıştırılması basittir ve kalite garanti edilir. Dökme demir atölyesi ayrıca çok sayıda vasıfsız operatör kullanarak yüksek kaliteli silindirler üretti.
- Verimlilik iki kattan fazla artar, bu da yalnızca çalışma saatlerinden tasarruf sağlamakla kalmaz, aynı zamanda çok sayıda kum havuzu maliyetinden de tasarruf sağlar.
- Birden fazla silindir seti ortak bir dökme sistemi kullandığından ve hiçbir yükseltici gerekmediğinden, döküm verim oranı %95 kadar yüksektir, bu da sıradan işlem yöntemlerinin %70 işlem verim oranından çok daha yüksektir. Yolluk sisteminin küçük kesit alanı nedeniyle, yalnızca hafifçe çekiçleme ile temizlenebilir, bu da dökümleri kesmek ve yükselticileri dökmek için çalışma saatlerini büyük ölçüde azaltır.
Firmamız tarafından üretilen rulo sac orta ve kalın sac fabrikasında üretime alındığından beri sorunsuz çalışmakta, sorunsuz ve normal çalışmakta olup, soğuk yatak çizikleri, sac üzerinde darbeler veya sacda herhangi bir sapma olmamıştır. rulo levhanın kalitesi nedeniyle çelik levha. Verimlilik, fabrikamızın üretiminin normal çalışmasını garanti eder ve iyi ekonomik faydalar yaratır.
Sonuç
Merdane levhanın malzeme ve döküm prosesi üzerine yapılan araştırmalar sayesinde merdane levhanın döküm işini zamanında, nitelik ve nicelik olarak tamamlamış, şirketimizin orta ve ağır levha projesine sorunsuz bir başlangıç yapması için temel atmış bulunmaktayız. Bu işlemin yüksek verimliliği ve dökümlerin iyi yüzey kalitesi nedeniyle, soğutma yatağı merdanelerimizin tamamlanması temelinde, Lingang, Xianggang ve diğer üreticilerden 20,000'den fazla merdane üretim görevi üstlendik. Promosyon ve uygulama beklentileri geniş ve ekonomiktir. Faydaları çok önemlidir.
Lütfen yeniden basım için bu makalenin kaynağını ve adresini saklayın:Rulet Döküm Parçalarının Döküm Süreci
Minghe Döküm Şirketi, kaliteli ve yüksek performanslı Döküm Parçaları üretmeye ve sağlamaya kendini adamıştır (metal döküm parça yelpazesi esas olarak şunları içerir: İnce Duvarlı Döküm,Sıcak Kamara Basınçlı Döküm,Soğuk Oda Döküm), Yuvarlak Servis (Döküm Servisi,Cnc İşleme,Kalıp yapımı,Yüzey İşleme).Herhangi bir özel Alüminyum döküm, magnezyum veya Zamak/çinko döküm ve diğer döküm gereksinimleri bizimle iletişime geçebilirsiniz.
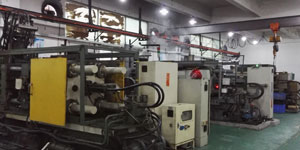
ISO9001 ve TS 16949 kontrolünde, tüm işlemler yüzlerce gelişmiş basınçlı döküm makinesi, 5 eksenli makine ve blasterlerden Ultra Sonic yıkama makinelerine kadar diğer tesisler aracılığıyla gerçekleştirilir. Müşterinin tasarımını gerçeğe dönüştürmek için deneyimli mühendisler, operatörler ve müfettişlerden oluşan ekip.
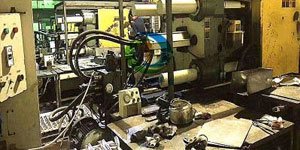
Dökümlerin sözleşmeli üreticisi. Yetenekler, 0.15 lbs'den başlayan soğuk oda alüminyum döküm parçaları içerir. 6 lbs'ye kadar, hızlı değişim kurulumu ve işleme. Katma değerli hizmetler arasında polisaj, titreşim, çapak alma, kumlama, boyama, kaplama, kaplama, montaj ve kalıplama yer alır. Çalışılan malzemeler arasında 360, 380, 383 ve 413 gibi alaşımlar bulunur.
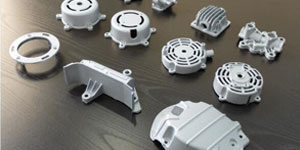
Çinko pres döküm tasarım yardımı/eşzamanlı mühendislik hizmetleri. Hassas çinko dökümlerin özel üreticisi. Minyatür dökümler, yüksek basınçlı dökümler, çok kızaklı kalıp dökümleri, geleneksel kalıp dökümleri, birim kalıp ve bağımsız kalıp dökümleri ve boşluklu sızdırmaz dökümler üretilebilir. Dökümler, +/- 24 inç toleransta 0.0005 inç'e kadar uzunluk ve genişliklerde üretilebilir.
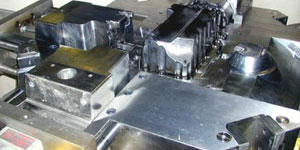
ISO 9001: 2015 sertifikalı döküm magnezyum üreticisi, Yetenekler arasında 200 ton sıcak odaya ve 3000 ton soğuk odaya kadar yüksek basınçlı magnezyum kalıp dökümü, takım tasarımı, cilalama, kalıplama, işleme, toz ve sıvı boyama, CMM özelliklerine sahip tam kalite güvencesi bulunur , montaj, paketleme ve teslimat.
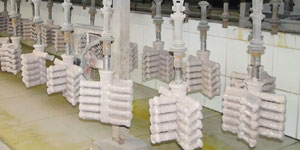
ITAF16949 sertifikalı. Ek Döküm Hizmeti Dahil yatırım dökümleri,kum dökümü,Yerçekimi Döküm, Kayıp Köpük Döküm,Savurma döküm,Vakumlu Döküm,Kalıcı Kalıp Döküm,.Yetenekler arasında EDI, mühendislik yardımı, katı modelleme ve ikincil işleme yer alır.
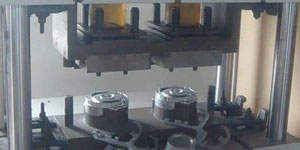
Döküm Endüstrileri Arabalar, Bisikletler, Uçaklar, Müzik aletleri, Deniz Araçları, Optik cihazlar, Sensörler, Modeller, Elektronik cihazlar, Muhafazalar, Saatler, Makineler, Motorlar, Mobilya, Mücevher, Jigler, Telekom, Aydınlatma, Tıbbi cihazlar, Fotoğraf cihazları, Robotlar, Heykeller, Ses ekipmanları, Spor ekipmanları, Aletler, Oyuncaklar ve daha fazlası.
Bundan sonra ne yapmanıza yardımcı olabiliriz?
∇ Ana Sayfaya Git Çin Döküm
→Döküm Parçaları-Ne yaptığımızı öğren.
→ Hakkında İlgili İpuçları Pres Döküm Hizmetleri
By Minghe Döküm Üreticisi |Kategoriler: Faydalı Makaleler |Malzeme Etiketler: Alüminyum Döküm, Çinko Döküm, Magnezyum Döküm, Titanyum Döküm, Paslanmaz Çelik Döküm, Pirinç Döküm,Bronz Döküm,Döküm Videosu,Tarihçe,Alüminyum Döküm |Yorumlar Kapalı