Hurda Temperli Sfero Döküm Eritme Süreci
Sfero dökme demirin geleneksel üretim sürecinde, genellikle bileşenler için yaklaşık %10 karbon hurdası kullanılır. Bu makale yalnızca, bir indüksiyon ocağında sfero döküm üretiminde kullanılan karbon hurda oranı artırıldıktan sonra üretim sürecinde özellikle dikkat edilmesi gereken bazı konuları ele almaktadır. Üretim pratiğine göre yazar, meslektaşlarının referansı için kendi görüşlerini ortaya koymaktadır.
şarj seçimi
(1) Hurda Çelik
Sfero demir üretiminde kullanılan hurda, karbon hurdası olmalıdır. Krom gibi grafitleşmeyi engelleyen elementler içermemelidir. Küreselleşmeyi önleyici alaşım elementleri içermemelidir. Hurda çelik topakları, fırına düz olarak yerleştirilebilen kalın pullar şeklinde yaklaşık %30 olmalıdır.
(2) Yeniden karbonlaştırıcı
- ① Yüksek kaliteli kok. Kükürt içeriği düşük olmalı, yumrululuk 60-80 mm'dir ve yüksek mukavemete sahiptir. Yakıldıktan sonra ezilemez.
- ②Harcanmış elektrot bloğu. Erimiş demiri kesmeyi kolaylaştırmak için belirli bir uzunluğa sahip olmak en iyisidir.
(3) Dökme Demir
Esas olarak erimiş demirin karbon içeriğini ayarlamak için kullanılır. wC>%4 ile yüksek karbonlu düşük kükürtlü pik demir kullanmayı umuyoruz. Pik demirdeki silikon içeriği uygun şekilde daha yüksektir ve sfero döküm demir üretimi daha az ferrosilikon olabilir.
(4) küreselleştirme
Küreselleştirici ajan ve aşılayıcı geleneksel tekniklere göre kullanılır ve her fabrikanın gerçek koşullarına göre belirlenir.
osmerus
Eritme işlemi: Kok bloğu + hurda çelik → elektrot bloğu → sıcaklık artışı → kok bloğunu ve elektrot bloğunu çekin → numune alın ve karbon içeriğini analiz edin → pik demir → geri malzeme → numune alın ve Si, Mn'yi analiz edin → sıcaklık artışı → ferromangan + ferrosilikon → deşarj →Aşılama + küreselleştirme → dökme.
Eritme işlemi sırasında alınacak önlemler şunlardır:
- Kok bloğu fırının altına monte edilmiştir, amaç kok bloğunun erimiş demirde daha uzun bir ıslatma süresi yaratmaktır. Kok blok miktarı hurdanın yaklaşık %5'i kadardır. Hurdanın yaklaşık %50'si eritilir ve kok, kalın pul hurda ile kaplanmalıdır. Yüksek kaliteli sfero döküm elde etmek için daha faydalı olan, daha düşük kükürt içeriğine sahip bir yeniden karbonlaştırıcı olarak fırın tabanına kurulacak kok yerine 60-80 mm'lik atık elektrot bloklarını kullanmak da mümkündür.
- Kullanılan hurda çeliğin oranı esas olarak karbon artışının verimliliği ile belirlenir. Sfero dökme demir üretmek için bu yöntemi kullanmaya başlayan üreticiler için yaklaşık %30 daha iyidir. Karbon artış verimliliğini artırdıktan sonra, hurda çelik oranını kademeli olarak artırın. Hurda çeliğin aşırı kullanımı, eğer karbon artış verimi yüksek değilse, nihai ürünün karbon silikon eşdeğerini etkileyecektir.
- Hurda çelik eritildikten sonra, fırındaki sıcaklığı uygun şekilde artırmak ve karbon verimliliğini artırmak için elektrot çubuğunu yerleştirin. Bununla birlikte, fırın sıcaklığı çok yüksektir, bu da güç tüketimini arttırır ve ayrıca fırın astarına zarar verir.
- Karbon içeriğinin yeterince yüksek olduğu tahmin edildikten sonra, kok bloğunu ve elektrot çubuğunu çıkarın ve karbon içeriğini örnekleyin ve analiz edin.
- Analiz sonuçlarına göre, eklenen pik demir miktarını ve kullanılan geri dönüştürülmüş sfero demir miktarını hesaplayın.
- Silisyum içeriğinin tahminine dayalı olarak, toplam erimiş demir miktarının yenilenmiş malzeme ile yapılıp yapılamayacağını belirleyin.
- Yeniden ısıtılan malzeme eritildikten sonra bir numune alın ve Si, Mn ve diğer alaşım elementlerinin içeriğini analiz edin.
- Erimiş demirin sıcaklığını uygun şekilde artırın, analiz sonuçlarına göre alaşım elementlerini tamamlayın ve fırın fırın sıcaklığına ulaşmadan önce ferrosilikon ekleyin.
- Ferrosilikon erimiş halde eritilir ve hemen fırından çıkarılır.
- Küreselleştirme, aşılama ve dökme her zamanki gibi gerçekleştirilir.
Kompozisyon ayarlama hesaplaması
Hepimizin bildiği gibi, sfero dökümün mekanik özellikleri esas olarak kimyasal bileşime, soğutma hızına (dökme sfero döküm olarak) ve ısıl işlem sürecine bağlıdır. Kimyasal bileşim iç nedendir, köktür ve değişkendir, neredeyse her fırın farklıdır. Bu nedenle kimyasal bileşenlerin tespitinin güçlendirilmesi ve dikkatli ayarlamaların yapılması gerekli olup, “sabit oranlı üretim” benimsenmesi uygun değildir. Kimyasal bileşimde karbon eşdeğeri özellikle önemlidir. Özellikle, ana yük olarak hurda çelik kullanılarak üretilen sfero dökme demir, karbon artışının verimliliğini kontrol etmek zor olduğundan ve karbon eşdeğeri büyük ölçüde dalgalandığından, karbon eşdeğerinin ayarlanmasına özel dikkat gösterilmelidir.
- Eklenen pik demir miktarını hesaplayın. Karbon içeriğinin analizine göre eklenen pik demir miktarını hesaplayın. Aslında, sfero dökme demirin karbon eşdeğerini, hem pik demirin hem de hurda çeliğin oluşturduğu eriyiğin karbon eşdeğerinin sfero döküm için gereken karbon eşdeğerine ulaşması için ayarlamaktır. Eklenen pik demir miktarı = eklenen hurda × (sfero döküm demirin gerekli karbon içeriği-karbon içeriğinin analizi) / (pik demirin karbon içeriği-sfero döküm demirin gerekli karbon içeriği)
- Eklenen geri dönüştürülmüş sünek demir miktarının hesaplanması Geri dönüştürülmüş sünek demirin karbon eşdeğeri temelde normaldir ve eklenen miktar büyük değildir. Bu nedenle, tekrar ısıtılmış demir ilave edildikten sonra, tüm fırındaki erimiş demirin karbon içeriği kalifiye olur. Fırına eklenen sfero döküm miktarı = toplam şarj miktarı - hurda çelik miktarı - pik miktarı demir eklendi
- Silikon içeriğinin tahmini Hesaplama formülü aşağıdaki gibidir: Silikon içeriği ≈ ((hurda çelik + pik demir + sfero dökme demir ilave miktarı) × silikon içeriği / toplam yük] × %100 ≤ orijinal erimiş demirin izin verilen silikon içeriği Tahmini silikon içerik çok yüksekse, az miktarda geri dönüştürülmüş sünek demir ekleyin ve toplam şarjı telafi etmek için 9:1 oranında aynı miktarda pik demir ve hurda kullanın.
- Ferrosilikon İlavesinin Hesaplanması Hesaplama formülü şu şekildedir: Eklenen ferrosilikon miktarı = [toplam şarj miktarı × (aşılama ile artan sfero demirin gerekli silikon muhtevası - sferoidleşme ile arttırılan silikon muhtevası - silikon muhtevasının analizi)] / ferrosilisyumun silikon içeriği
- Eklenen manganez ve diğer alaşım elementlerinin miktarı şu şekilde hesaplanır: Eklenen alaşımlı demir miktarı = toplam yük miktarı × (sfero-analiz içeriğinin gerekli alaşım içeriği)/alaşımlı demirdeki alaşım elementi içeriği Yanma kaybı değil Yukarıdaki hesaplamalara dahil edilmiştir.
Çünkü sfero döküm endüksiyon ocağında eritilir ve elementler fazla yanmaz ve demir de bir miktar yakılır. Özel durumlarla karşılaşırsanız yanmaya dikkat etmelisiniz.
Kompozisyon ayarlama uygulama örneği:
- Perlitik sünek demir QT1-800 üretmek için 2 tonluk endüksiyonlu elektrikli fırın kullanıldığında, döküm ağırlığı 1000 kg'dır.
- "Kontrol kimyasal bileşimi: wC=%3.5, wSi=%2.5, wMn=%0.5, wP<%0.07, wS<%0.02, wMg=%0.03~%0.06, wRE=%0.02~%0.04.
- Yeniden karbonlamadan sonra, fırındaki "hurda erimiş çeliğin" karbon içeriği %2.5'tir.
- Eklenen pik demir miktarı = 300 × (%3.5-%2.5) / (%4-3.5) = 600 (kg)
- Fırında kullanılan sfero döküm miktarı = 1000-300-600=100 (kg)
- Tahmini silikon içeriği = (300×0.3%+600×1.8%+100×2.5%)×%100=1.42
- Nodulizerin silikon içeriği %0.6 ve aşılayıcının silikon içeriği %0.4 ise, orijinal erimiş demirin silikon içeriği, tahmini silikon içeriğinden daha yüksek olan %1.5 olmalıdır. Bunun için karbon eşdeğerini ayarlamak için Z18 dökme demir kullanılabilir ve toplam şarj miktarını telafi etmek için yeniden pişirilmiş sfero kullanılabilir.
- Fırın serbest bırakılmadan önce silikon içeriği %1.38 ve manganez içeriği %0.15'tir.
- Ferrosilikon eklenen miktar = [1000 (%2.5-%0.6-%0.4-%1.38)] / %75 = 1.6kg
- Ferromangan eklenen miktar = [1000 (%0.5-%0.15)] / %65 = 5.4kg
4. son sözler
İndüksiyonlu elektrikli fırın üretiminde, QT800-2 üretmek için hurda çelik kullanıyoruz, mukavemet 800~1000MPa'dır ve uzama %4'ten fazladır.
Şu anda piyasada çok fazla hurda çelik var, pik demir pahalı ve yüksek kaliteli pik demir daha da kıt. Bu nedenle, sfero dökme demir üretim görevleri olan üreticilerin, sfero dökme demir üretmek için yukarıda belirtilen varsayıma ve "çeliğin demirin yerini alması"na başvurabileceğini öneriyoruz.
Lütfen yeniden basım için bu makalenin kaynağını ve adresini saklayın:Hurda Temperli Sfero Döküm Eritme Süreci
Minhe Basınçlı Döküm Şirketi kaliteli ve yüksek performanslı Döküm Parçaları üretmeye ve sağlamaya adamıştır (metal döküm parça yelpazesi esas olarak şunları içerir: İnce Duvarlı Döküm,Sıcak Kamara Basınçlı Döküm,Soğuk Oda Döküm), Yuvarlak Servis (Döküm Servisi,Cnc İşleme,Kalıp yapımı,Yüzey İşleme).Herhangi bir özel Alüminyum döküm, magnezyum veya Zamak/çinko döküm ve diğer döküm gereksinimleri bizimle iletişime geçebilirsiniz.
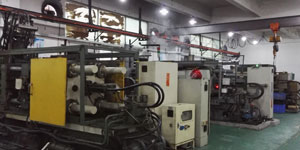
ISO9001 ve TS 16949 kontrolünde, tüm işlemler yüzlerce gelişmiş basınçlı döküm makinesi, 5 eksenli makine ve blasterlerden Ultra Sonic yıkama makinelerine kadar diğer tesisler aracılığıyla gerçekleştirilir. Müşterinin tasarımını gerçeğe dönüştürmek için deneyimli mühendisler, operatörler ve müfettişlerden oluşan ekip.
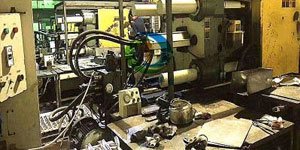
Dökümlerin sözleşmeli üreticisi. Yetenekler, 0.15 lbs'den başlayan soğuk oda alüminyum döküm parçaları içerir. 6 lbs'ye kadar, hızlı değişim kurulumu ve işleme. Katma değerli hizmetler arasında polisaj, titreşim, çapak alma, kumlama, boyama, kaplama, kaplama, montaj ve kalıplama yer alır. Çalışılan malzemeler arasında 360, 380, 383 ve 413 gibi alaşımlar bulunur.
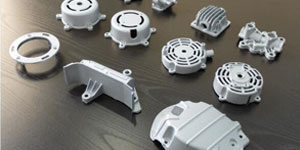
Çinko pres döküm tasarım yardımı/eşzamanlı mühendislik hizmetleri. Hassas çinko dökümlerin özel üreticisi. Minyatür dökümler, yüksek basınçlı dökümler, çok kızaklı kalıp dökümleri, geleneksel kalıp dökümleri, birim kalıp ve bağımsız kalıp dökümleri ve boşluklu sızdırmaz dökümler üretilebilir. Dökümler, +/- 24 inç toleransta 0.0005 inç'e kadar uzunluk ve genişliklerde üretilebilir.
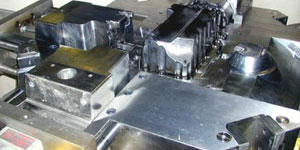
ISO 9001: 2015 sertifikalı döküm magnezyum üreticisi, Yetenekler arasında 200 ton sıcak odaya ve 3000 ton soğuk odaya kadar yüksek basınçlı magnezyum kalıp dökümü, takım tasarımı, cilalama, kalıplama, işleme, toz ve sıvı boyama, CMM özelliklerine sahip tam kalite güvencesi bulunur , montaj, paketleme ve teslimat.
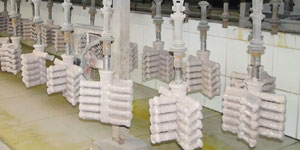
ITAF16949 sertifikalı. Ek Döküm Hizmeti Dahil yatırım dökümleri,kum dökümü,Yerçekimi Döküm, Kayıp Köpük Döküm,Savurma döküm,Vakumlu Döküm,Kalıcı Kalıp Döküm,.Yetenekler arasında EDI, mühendislik yardımı, katı modelleme ve ikincil işleme yer alır.
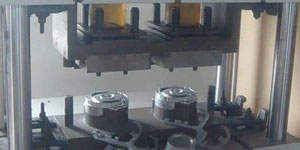
Döküm Endüstrileri Arabalar, Bisikletler, Uçaklar, Müzik aletleri, Deniz Araçları, Optik cihazlar, Sensörler, Modeller, Elektronik cihazlar, Muhafazalar, Saatler, Makineler, Motorlar, Mobilya, Mücevher, Jigler, Telekom, Aydınlatma, Tıbbi cihazlar, Fotoğraf cihazları, Robotlar, Heykeller, Ses ekipmanları, Spor ekipmanları, Aletler, Oyuncaklar ve daha fazlası.
Bundan sonra ne yapmanıza yardımcı olabiliriz?
∇ Ana Sayfaya Git Çin Döküm
→Döküm Parçaları-Ne yaptığımızı öğren.
→ Hakkında İlgili İpuçları Pres Döküm Hizmetleri
By Minghe Döküm Üreticisi |Kategoriler: Faydalı Makaleler |Malzeme Etiketler: Alüminyum Döküm, Çinko Döküm, Magnezyum Döküm, Titanyum Döküm, Paslanmaz Çelik Döküm, Pirinç Döküm,Bronz Döküm,Döküm Videosu,Tarihçe,Alüminyum Döküm |Yorumlar Kapalı