Kalite Hatalarının Söndürülmesi ve Kontrol Ansiklopedisi
Su verme işleminden sonra çelik parçaların mukavemeti, sertliği ve aşınma direnci iyileştirilebilir, ancak su verme sırasında iş parçasının orijinal boyutu veya şekli istenmeyen değişikliklere uğrayacaktır. Bu değişiklik, ürün kalitesini etkileyen, azaltan veya önleyen bir kusur haline gelecektir. Bu kusurlar, her şeyden önce, söndürme ile hangi kusurların üretileceğini, oluşum nedenlerinin neler olduğunu bilmeli ve bunlara uygun çözümler bulmalıyız. Su verme kalite kusurları ve kontrolü aşağıdaki yönlerden açıklanmaktadır.
1. Söndürme bozulması
Söndürme distorsiyonu türleri hacim distorsiyonu ve şekil distorsiyonu olmak üzere iki kategoriye ayrılabilir.
Söndürmeden önce ve sonra çeşitli yapıların özgül hacimlerindeki fark, hacim değişikliğinin ana nedenidir. Sırayla martensit → beynit → perlit → östenitin özgül hacmi azalır. Orijinal yapısı perlit olan iş parçası martensite su verilerek hacmi şişer. Kuruluşta çok miktarda kalıntı östenit varsa, hacmi küçültebilir. Hacmin düzgün genişlemesinin neden olduğu hacimsel değişiklikler için sadece özellikle yüksek hassasiyete sahip iş parçaları dikkate alınır.
Plaka ve çubuğun bükülmesi, iç deliğin genişlemesi ve daralması ve delik aralığının değişmesi gibi iş parçasının her bir parçasının göreli konumundaki veya boyutundaki değişiklikler topluca şekil bozulması olarak adlandırılır. Bozulma nedenleri aşağıdaki gibidir:
- (1) Isıtma sıcaklığı eşit değildir, oluşan termal stres bozulmaya neden olur veya iş parçası makul olmayan bir şekilde fırına yerleştirilir ve sürünme bozulması genellikle yüksek sıcaklıklarda kendi ağırlığından kaynaklanır.
- (2) Isıtma sırasında, ısıtma sıcaklığı arttıkça çeliğin akma dayanımı azalır. İş parçasının içindeki artık gerilim (soğuk deformasyon gerilimi, kaynak gerilimi, işleme gerilimi vb.) yüksek sıcaklıkta akma dayanımına ulaştığında, iş parçasının düzensiz plastik deformasyonu şekil bozulmasına ve artık gerilim gevşemesine neden olur.
- (3) Su verme ve soğutma sırasında farklı zamanlarda oluşan termal stres ve organizasyonel stres, iş parçasının lokal plastik deformasyonuna neden olur. Karmaşık şekillere sahip iş parçaları için, yapılarının özelliği nedeniyle, söndürme sırasında ısıtma ve soğutma hızları farklıdır, bu da deforme olma eğilimini arttırır.
2. Söndürme distorsiyonunu azaltmanın yolları ve yöntemleri
- (1) Makul bir ısıl işlem sürecinin kullanılması bozulmayı etkili bir şekilde azaltabilir. Söndürme ısıtma sıcaklığını düşürmek gibi; iş parçasının yavaş ısınması veya ön ısıtılması; statik ısıtma yöntemi, son derece ince ve son derece ince iş parçaları, tuz banyosu manyetik karıştırmanın iş parçası üzerindeki etkisini azaltmak için, kapalı ısıtma kullanılabilir; kesit boyutu küçüktür İş parçası için, çekirdek mukavemeti yüksek değilse hızlı ısıtma kullanın; iş parçasını makul bir şekilde toplayın ve asın; işin şekline göre makul bir su verme yöntemi kullanın; hiyerarşik söndürme veya östemperleme kullanın; iş parçasının şekil özelliklerine ve deformasyon yasalarına göre, Söndürmeden önce, su verme işleminden sonra bozulmayı dengelemek için iş parçasını ters yönde yapay olarak deforme edin.
- (2) Makul tasarım parçaları. Örneğin, kesit eşitsizliğinden kaçınmak için iş parçasının şekli simetrik olmalıdır, böylece eşit olmayan soğutmanın neden olduğu bozulmayı azaltır; yivin genleşmesini veya büzülmesini azaltmak için, yivli iş parçası veya kolayca bozulan açılış iş parçası, su verme işleminden önce kapalı bir yapıya dönüştürülmelidir, örneğin çentikte nervürleri artırın ve su verdikten sonra kesin; boşluk büzülmesini azaltmak için proses delikleri düzenleyin; karmaşık parçalar birleşik bir yapıyı benimser, yani karmaşık bir iş parçası birkaç basit parçaya bölünür ve daha sonra sırasıyla mikro-bozuklaştırılır ve söndürülür ve daha sonra monte edilir; doğru Çelik kullanılır. Yüksek hassasiyetli ve düşük ısıl işlem distorsiyonuna sahip takımlar için mikro distorsiyonlu çelik kullanılabilir ve yüksek hassasiyetli plastik kalıplar için önceden sertleştirilmiş çelik de kullanılabilir.
- (3) Makul dövme ve ön ısıl işlem. Şiddetli karbür ayrışması ve bantlı yapı, söndürme distorsiyonunu anizotropik veya düzensiz hale getirir. Dövme yoluyla karbür dağılımını iyileştirmek, yalnızca bozulmayı azaltmakla kalmaz, aynı zamanda iş parçasının hizmet ömrünü de iyileştirir.
3. Bozulmanın düzeltilmesi
Isıl işlem sonrası parçaların bozulması için soğuk pres doğrultma, sıcak nokta doğrultma, sıcak doğrultma, tavlama doğrultma, karşı saldırı doğrultma, büzülme işlemi vb. kullanılabilir.
Soğuk presle doğrultma, plastik deformasyona neden olmak için bükülmüş iş parçasının en yüksek noktasına dış kuvvet uygulamaktır. Bu yöntem, sertliği 35HRC'den az olan şaft iş parçaları için uygundur; sıcak nokta doğrultma, dışbükey parçayı bir oksiasetilen alevi ile ısıtmak ve daha sonra ısıtılmış parçayı termal stres etkisi altında küçültmek için hızlı bir şekilde soğutmak için su veya yağ kullanmaktır. Bu yöntem, sertliği 35-40HRC'den fazla olan iş parçaları için uygundur; sıcak doğrultma, iş parçasını Ms sıcaklığına yakın bir şekilde söndürmek iken, östenitin iyi plastisitesini ve plastisitesini kullanın. Faz değişimi süperplastisitesi, distorsiyonun düzeltilmesini sağlar; temperleme düzeltmesi, iş parçasına dış kuvvet uygulamak ve ardından temperleme yapmaktır, temperleme sıcaklığı 300 ℃'den yüksektir; karşı saldırı düzleştirme, iş parçasının küçük bir alanını oluşturmak için girintiye sürekli olarak çelik bir çekiçle vurmaktır Plastik deformasyon; Büzülme işlemi, şişmiş iş parçasını kırmızı olacak şekilde 600-700 ℃'ye söndürdükten sonra ısıtmaktır. Deliğe su girmesini önlemek için iş parçasının her iki ucunu kapatmak için iki ince plaka kullanılır ve hızlı soğutma için iş parçası hızla suya atılır. Delik küçülür ve bir veya daha fazla tekrarlanan işlemden sonra şişmiş delik düzeltilebilir.
4. Söndürme çatlaması
Su verme çatlaması, malzemenin kırılma mukavemetini aşan ısıl işlem stresinin neden olduğu bir çatlama olgusudur. Çatlaklar, çatlak üzerinde soğutma yağı veya tuzlu su izleri, oksidasyon rengi ve çatlağın her iki tarafında dekarburizasyon olmaksızın seri olarak aralıklı olarak dağılmıştır. Çatlakların söndürülmesinin nedenleri ve nedenleri şunlardır:
- (1) Malzeme yönetimi kaotiktir ve yüksek karbonlu çelik veya yüksek karbonlu alaşımlı çelik yanlışlıkla düşük ve orta karbonlu çelik olarak kullanılır ve suyla söndürme kullanılır.
- (2) Yanlış soğutma. Ms sıcaklığının altındaki hızlı soğutma, yüksek doku stresi nedeniyle çatlamaya neden olacaktır. Su-yağ ikili-orta söndürme gibi, suda kalma süresi uzundur ve söndürme yağı çok fazla su içerir.
- (3) Sertleştirilmemiş iş parçasının çekirdek sertliği 36~45HRC olduğunda, sertleştirilmiş tabaka ile sertleştirilmemiş tabakanın birleşme yerinde su verme çatlakları oluşur. Çekirdek sertliği 36HRC'den azdır ve bağlantıdaki çekme mukavemeti azalır. Çekirdek sertliği 45HRC'den büyüktür, bu da martensit bir yapı olduğunu, tepe çekme geriliminin azaldığını ve çatlama eğiliminin azaldığını gösterir.
- (4) En tehlikeli söndürme çatlağı boyutuna sahip iş parçası, söndürme çatlaklarına eğilimlidir. İş parçası tamamen söndürüldüğünde, söndürme çatlaklarının en tehlikeli boyutu vardır, çapı: Suda söndürme sırasında 8-15 mm; Yağda söndürürken 25-40mm. Boyut, en tehlikeli söndürme çatlama boyutundan daha küçük olduğunda, çekirdek ve yüzey arasındaki sıcaklık farkı küçüktür, sertleştirme kuvveti küçüktür ve çatlaması kolay değildir. Aksine artar, ancak çekme gerilmesi tepe noktası yüzeyden çok uzaktadır ve bunun yerine su verme çatlama eğilimi azalır.
- (5) Şiddetli yüzey dekarburizasyonu, ağ çatlakları oluşturmak kolaydır. Karbonsuz tabakanın martenziti küçük bir özgül hacme sahiptir ve çekme gerilimi altında ağ çatlakları oluşturmaya yatkındır.
- (6) Daha küçük iç çaplara sahip derin delikli iş parçaları için, iç yüzey dış yüzeyden çok daha az soğutulur ve artık termal gerilim küçüktür. Artık çekme gerilimi dış yüzeyden daha büyüktür ve iç duvarda paralel uzunlamasına çatlaklar oluşturmak kolaydır.
- (7) Söndürme ısıtma sıcaklığı çok yüksektir, bu da kristal tanelerin kabalaşmasına, tane sınırlarının zayıflamasına, çeliğin kırılganlığının azalmasına ve söndürme sırasında kolay çatlamaya neden olur.
- (8) Tekrarlanan söndürmeden önce ara tavlama olmadan, aşırı ısınma eğilimi yüksektir, önceki maddenin söndürme stresi tamamen ortadan kaldırılamaz ve tekrarlanan ısıtmanın neden olduğu yüzey karbonsuzlaşması, söndürme çatlamasını teşvik edecektir.
- (9) Büyük kesitli yüksek alaşımlı çelik iş parçaları, su verme ve ısıtma sırasında önceden ısıtılmaz veya çok hızlı ısıtılmaz ve ısıtma sırasında termal stres veya yapısal stres artar ve çatlamaya neden olur.
- (10) Düşük kaliteli yüksek karbonlu çelik küreselleştirme tavlaması gibi zayıf orijinal yapı, yapısı yüksek termal eğilime sahip katmanlı veya noktalı perlittir; tane irileşmesi, yüksek martensit içeriği ve yüksek su verme çatlama eğilimi.
- (11) Hammadde mikro çatlakları, metalik olmayan inklüzyonlar ve şiddetli karbür ayrışması, su verme çatlamasını artırma eğilimindedir. Örneğin, metalik olmayan safsızlıklar veya şiddetli karbürler, haddeleme yönü boyunca bir şerit oluşturur. Mekanik özelliklerin anizotropisi nedeniyle, enine özellikleri, boyuna özelliklerinden %30 ila %50 daha düşüktür. Metal kapanımlarının veya karbürlerin dağılım yönü boyuna çatlaklardır.
- (12) Dövme çatlakları su verme sırasında genişler. Esnek fırında söndürme ve ısıtma sırasında, çatlamış kırılma yüzeyi siyah oksit ölçeğine sahiptir ve çatlağın her iki tarafında dekarbürize bir tabaka vardır.
- (13) Aşırı yanan çatlaklar. Çatlaklar çoğunlukla ağ şeklindedir ve tane sınırları oksitlenir ve erir.
- (14) Sertleşebilirliği düşük olan çelikler için, kenetlendiğinde ve pense ile su verildiğinde, kenetlenen kısım yavaşça su verir ve martenzitik olmayan bir yapıya sahiptir. Çeneler, sertleştirilmiş tabaka ile sertleştirilmemiş tabakanın birleştiği yerde bulunur ve çekme gerilimi Büyük ve çatlaması kolaydır.
- (15) Yüksek hız çeliği ve yüksek krom çeliği aşamalı olarak su verilir ve iş parçası oda sıcaklığına soğutulmaz ve temizlemeye isteklidir (Ms'nin altındaki hızlı soğuma nedeniyle) çatlamaya neden olur.
- (16) Hızlı soğutma ve ısıtma nedeniyle kriyojenik işlem tarafından oluşturulan termal stres ve yapısal stres nispeten büyüktür ve düşük sıcaklıktaki malzemenin kırılgan mukavemeti düşüktür, bu da söndürme çatlaması üretmesi kolaydır.
- (17) Söndürmeden sonra zamanla temperlenmezse, iş parçasının içindeki mikro çatlaklar, söndürme geriliminin etkisi altında makro çatlaklar oluşturmak üzere genişler.
5. Söndürme çatlamasını önlemek için önlemler
- (1) İş parçasının yapısını iyileştirin. Kesitte üniform olmaya çalışın ve gerilim konsantrasyonunun neden olduğu çatlamayı önlemek için açık olmayan delikleri ve keskin köşeleri en aza indirmek için farklı kesitlerde yuvarlak geçişler olmalıdır.
- (2) Makul bir şekilde çeliği seçin. Karmaşık şekilli ve kırılması kolay iş parçası, yüksek sertleşebilirliğe sahip alaşımlı çelikten yapılmalıdır, böylece yavaş soğutma hızına sahip su verme ortamı, su verme stresini azaltmak için kullanılabilir.
- (3) Hammaddeler, mikro çatlaklardan ve metalik olmayan inklüzyonların ve karbürlerin ciddi şekilde ayrılmasını önlemelidir.
- (4) Normalleştirme ve tavlama yapı kusurlarını önlemek için ön ısıl işlem doğru şekilde yapılmalıdır.
- (5) Isıtma parametrelerini doğru seçin.
- (6) Su verme ortamının ve su verme yönteminin makul seçimi.
- (7) İş parçasının keskin köşeler, ince duvarlar, delikler vb. gibi kolayca çatlayan kısımlarını kısmen bandajlayın.
- (8) Su verme işleminden sonra, kolayca çatlayan iş parçası zamanla veya sıcaklıkla temperlenmelidir.
6. Yetersiz sertlik
Su verme sonrası iş parçasının yüzey sertliği, kullanılan çeliğin su verme sertlik değerinden düşüktür ve buna yetersiz sertlik denir.
Yetersiz Söndürme Sertliğinin Nedenleri
- Ortamın soğutma kapasitesi zayıftır ve iş parçasının yüzeyi ferrit ve troostit gibi martensitik olmayan yapılara sahiptir.
- Söndürme ısıtma sıcaklığı düşüktür veya ön soğutma süresi uzundur, söndürme soğutma hızı düşüktür ve martensitik olmayan yapı görünür.
- Ötektoid altı çeliğin yetersiz ısıtılması, çözünmemiş ferrit içerir
- Karbon çeliği veya düşük alaşımlı çelik, su-yağ ikili ortamı ile su verildiğinde, suda kalma süresi yetersizdir veya parçalar sudan kaldırıldıktan sonra havada kalma süresi çok uzundur.
- Çeliğin sertleşebilirliği zayıftır ve çalışma bölümünün boyutu büyük değildir ve sertleştirilemez.
- Yüksek karbonlu yüksek alaşımlı çelik, yüksek su verme sıcaklığına ve aşırı düzeyde tutulan östenite sahiptir
- İzotermal süre çok uzun, östenitin stabilize olmasına neden oluyor
- Yüzey dekarburizasyonu
- Nitrat veya alkali banyosundaki nem içeriği çok küçüktür ve aşama soğutması sırasında troostit gibi martensit olmayan maddeler oluşur.
- Alaşım elementleri içten oksitlenir, yüzey sertleşebilirliği azalır ve iç yapı martensit iken troostit gibi martensit olmayanlar ortaya çıkar.
Kontrol önlemleri
- Daha hızlı soğutma ile söndürme ortamı kullanın; söndürme ısıtma sıcaklığını uygun şekilde artırın
- Normal söndürme ısıtma sıcaklığının sağlanması öncülüğünde; ön soğutma süresini azaltın
- Isıtma sıcaklığını, nemlendirme süresini ve fırın sıcaklığı homojenliğini kesinlikle kontrol edin
- Parçaların suda kalma süresini ve çalışma özelliklerini sıkı bir şekilde kontrol edin
- Sertleşebilirliği iyi olan çelik kullanın
- Söndürme ısıtma sıcaklığını azaltın veya kriyojenik tedaviyi benimseyin
- Sınıflandırmayı veya izotermal zamanı kesinlikle kontrol edin
- Kontrol edilebilir atmosfer ısıtması veya diğer karbonsuzlaştırma önleyici önlemleri kullanın
- Tuz banyosu ve alkali banyosundaki nemi kesinlikle kontrol edin
- Fırın atmosferindeki oksitleyici bileşenlerin içeriğini azaltın; hızlı soğutma hızına sahip söndürme ortamını seçin.
7. Yumuşak Noktalar
Söndürmeden sonra, iş parçası yüzeyinin yerel bölgesindeki düşük sertlik olgusuna yumuşak nokta denir. Karbon çeliği ve düşük alaşımlı çelik, genellikle zayıf sertleşebilirlik nedeniyle yumuşak noktayı söndürmeye eğilimlidir.
Yumuşak Noktaların Nedenleri
- Söndürme sırasında iş parçası yüzeyindeki kabarcıklar zamanında kırılmamış, bu da kabarcıklardaki soğuma hızının düşmesine ve martensit olmayan bir yapıya neden olmuştur.
- Çalışma yüzeyindeki yerel oksit ölçeği, pas lekeleri veya diğer ekler (boya) söndürme sırasında soyulmadığından soğutma hızı düşürüldü
- Orijinal yapı, ciddi bant benzeri yapı veya karbür segregasyonu ile tek tip değildir
Kontrol önlemleri
- Ortamın ve iş parçasının göreceli hareketini artırın; su sıcaklığını ve sudaki safsızlıkları kontrol edin
- Söndürmeden önce iş parçasının yüzeyini temizleyin
- Hammaddeler, yapıyı homojenleştirmek için dövülür ve önceden ısıtılır
8. Yüzey korozyonu
İş parçası su verildikten, asitlendikten veya kumlandıktan sonra yüzeyde, ortamın korozyonu ile oluşan, çukur adı verilen yoğun nokta benzeri çukurlar görülür. Çukurlar iş parçasının parlaklığını kaybetmesine neden olur ve yüzey kalitesini etkiler.
Çukur oluşumunun birçok nedeni vardır, ancak matrisin aşınmasını önlemek için tuz banyosundaki sülfat içeriğini azaltmak gibi çalışma sırasında bu kusuru azaltabiliriz; ayrıca nitrat sıcaklığının düşürülmesi; yüksek sıcaklıkta söndürme ısıtma iş parçası önceden soğutulur Daha sonra nitratın ayrışmasını önlemek için çözeltiye koyun; yüksek sıcaklık lokal olarak ısıtıldığında, ısıtılmayan kısım, çukur korozyonunu önlemek için katı bir tuz kabuğuyla kaplamak için tuza batırılır.
Lütfen yeniden basım için bu makalenin kaynağını ve adresini saklayın:Kalite Hatalarının Söndürülmesi ve Kontrol Ansiklopedisi
Minhe Basınçlı Döküm Şirketi kaliteli ve yüksek performanslı Döküm Parçaları üretmeye ve sağlamaya adamıştır (metal döküm parça yelpazesi esas olarak şunları içerir: İnce Duvarlı Döküm,Sıcak Kamara Basınçlı Döküm,Soğuk Oda Döküm), Yuvarlak Servis (Döküm Servisi,Cnc İşleme,Kalıp yapımı,Yüzey İşleme).Herhangi bir özel Alüminyum döküm, magnezyum veya Zamak/çinko döküm ve diğer döküm gereksinimleri bizimle iletişime geçebilirsiniz.
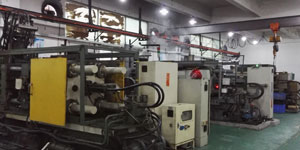
ISO9001 ve TS 16949 kontrolünde, tüm işlemler yüzlerce gelişmiş basınçlı döküm makinesi, 5 eksenli makine ve blasterlerden Ultra Sonic yıkama makinelerine kadar diğer tesisler aracılığıyla gerçekleştirilir. Müşterinin tasarımını gerçeğe dönüştürmek için deneyimli mühendisler, operatörler ve müfettişlerden oluşan ekip.
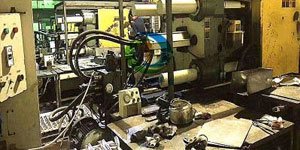
Dökümlerin sözleşmeli üreticisi. Yetenekler, 0.15 lbs'den başlayan soğuk oda alüminyum döküm parçaları içerir. 6 lbs'ye kadar, hızlı değişim kurulumu ve işleme. Katma değerli hizmetler arasında polisaj, titreşim, çapak alma, kumlama, boyama, kaplama, kaplama, montaj ve kalıplama yer alır. Çalışılan malzemeler arasında 360, 380, 383 ve 413 gibi alaşımlar bulunur.
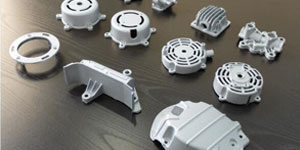
Çinko pres döküm tasarım yardımı/eşzamanlı mühendislik hizmetleri. Hassas çinko dökümlerin özel üreticisi. Minyatür dökümler, yüksek basınçlı dökümler, çok kızaklı kalıp dökümleri, geleneksel kalıp dökümleri, birim kalıp ve bağımsız kalıp dökümleri ve boşluklu sızdırmaz dökümler üretilebilir. Dökümler, +/- 24 inç toleransta 0.0005 inç'e kadar uzunluk ve genişliklerde üretilebilir.
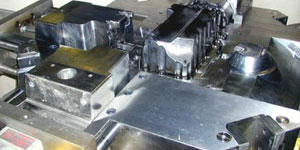
ISO 9001: 2015 sertifikalı döküm magnezyum üreticisi, Yetenekler arasında 200 ton sıcak odaya ve 3000 ton soğuk odaya kadar yüksek basınçlı magnezyum kalıp dökümü, takım tasarımı, cilalama, kalıplama, işleme, toz ve sıvı boyama, CMM özelliklerine sahip tam kalite güvencesi bulunur , montaj, paketleme ve teslimat.
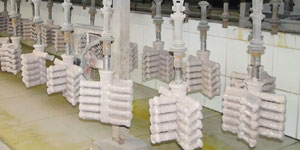
ITAF16949 sertifikalı. Ek Döküm Hizmeti Dahil yatırım dökümleri,kum dökümü,Yerçekimi Döküm, Kayıp Köpük Döküm,Savurma döküm,Vakumlu Döküm,Kalıcı Kalıp Döküm,.Yetenekler arasında EDI, mühendislik yardımı, katı modelleme ve ikincil işleme yer alır.
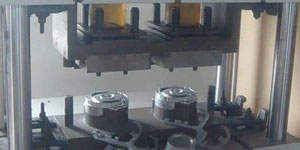
Döküm Endüstrileri Arabalar, Bisikletler, Uçaklar, Müzik aletleri, Deniz Araçları, Optik cihazlar, Sensörler, Modeller, Elektronik cihazlar, Muhafazalar, Saatler, Makineler, Motorlar, Mobilya, Mücevher, Jigler, Telekom, Aydınlatma, Tıbbi cihazlar, Fotoğraf cihazları, Robotlar, Heykeller, Ses ekipmanları, Spor ekipmanları, Aletler, Oyuncaklar ve daha fazlası.
Bundan sonra ne yapmanıza yardımcı olabiliriz?
∇ Ana Sayfaya Git Çin Döküm
→Döküm Parçaları-Ne yaptığımızı öğren.
→ Hakkında İlgili İpuçları Pres Döküm Hizmetleri
By Minghe Döküm Üreticisi |Kategoriler: Faydalı Makaleler |Malzeme Etiketler: Alüminyum Döküm, Çinko Döküm, Magnezyum Döküm, Titanyum Döküm, Paslanmaz Çelik Döküm, Pirinç Döküm,Bronz Döküm,Döküm Videosu,Tarihçe,Alüminyum Döküm |Yorumlar Kapalı