Sinterlenmiş Çeliğin Sinterleme Sürecinde Atmosfer Kontrolü ve Performansı
Sinterleme atmosferi ve seçimi
Sadece karbon içeren çeliğin sinterlenmesi düşünülecek olursa, toz metalurjisi endüstrisinde kullanılan sinterleme atmosferi hidrojen, azot, azot + hidrojen (karbon potansiyeli veya karbon potansiyeli yok), amonyak, endotermik gaz, endotermik gaz + azot, sentez Gaz ve vakum için sinterleme atmosferinin doğru seçimi, çeşitli sinterleme atmosferlerinin özelliklerinin ve performansının anlaşılmasını ve kalitenin sağlanması ve maliyetlerin düşürülmesi ilkelerine uygun olarak seçilmesini gerektirir.
Hidrojen güçlü bir indirgeyici atmosferdir. Birçok kişi hidrojenin belirli bir karbonsuzlaştırma etkisine sahip olduğuna inanır, ancak bu büyük ölçüde hidrojenin kendisinden ziyade kullanılan hidrojenin saflığına bağlıdır. Genel olarak, elektroliz veya katalitik dönüşümden sonra hidrojen, H2O, O2, CO ve CH4 vb. Gibi belirli bir miktarda safsızlık gazı içerir, bazen toplam miktar yaklaşık% 0.5'e ulaşabilir. Bu nedenle, oksijen içeriğini ve çiğlenme noktasını azaltmak için kullanmadan önce kurutmak ve saflaştırmak en iyisidir. Bununla birlikte, hidrojenin yüksek fiyatı nedeniyle, özel nedenler olmadıkça, sinterleme atmosferi olarak saf hidrojen nadiren kullanılır.
Azot güvenli ve ucuz bir inert gazdır, ancak saf nitrojen sinterleme sıcaklığında indirgenemez olduğundan, geleneksel toz metalurji çeliğinin üretiminde saf nitrojen sinterleme atmosferi olarak nadiren kullanılır. Son yıllarda nitrojen arıtma maliyetinin düşmesi ve sinterleme fırınının hava sızdırmazlığının artmasıyla birlikte nitrojen, karbon içeren çeliğin sinterlenmesinde sinterleme atmosferi olarak da kullanılmaya başlanmıştır.
Son yıllarda, karbon çeliğinin sinterlenmesinde azot-hidrojen karışımı giderek daha fazla kullanılmaktadır. Azot/hidrojen genellikle 95/5-50/50 arasında kullanılır. Bu karışımın belirli bir indirgenebilirliği vardır ve çiy noktası -60℃'nin altına ulaşabilir, genel olarak konuşursak, bu gazı 4-3℃'de kullanırken belirli bir karbon potansiyelini korumak için belirli bir miktarda CH8 veya C1050H1150 eklenmelidir, sinterleme sırasında 1250℃ üzerindeki karbon çeliği, karbon potansiyelini kontrol etmeye ihtiyaç duymaz. Bu karışım, krom içeren demir bazlı alaşımları oksidasyon olmadan 1120°C'nin altında sinterlemek için kullanılabilir.
Ayrışmış amonyak, amonyak gazının %75 H2 ve %25 N2 içeren ısıtılmış bir katalizör aracılığıyla ayrıştırılmasıyla yapılır. Ancak genel olarak konuşursak, az miktarda ayrışmamış amonyak molekülü her zaman ayrışmış amonyak içinde kalır. Sıcak metal ile yüksek sıcaklıklarda temas ettiklerinde, yüksek derecede aktif hidrojen ve nitrojen atomlarına ayrışırlar ve böylece metali nitrürlerler. Son çalışmalar, düzgün bir şekilde kontrol edilirse, AstaloyCrM'nin 1120°C'de sinterlenmesinin, 90N2/10H2 karışımını daha güçlü indirgenebilirlikle bozacağını ve amonyaklaştıracağını göstermiştir. Bunun ana nedeni, sinterleme işlemi sırasında henüz ayrışmış olan bu aktif hidrojen atomlarının 90N2/'den daha etkili olmasıdır. Amonyağı arındırmak ve ayrıştırmak için, sudan geçirip kurutabilir veya kalan tüm amonyak çıkarılır.
Endotermik gaz, hidrokarbon gazının (CH4 veya C3H8) hava ile belirli oranda karıştırılması, 900-1000°C'de ön ısıtma yapılması ve nikel oksit katalizörü ile katalitik olarak dönüştürülmesiyle elde edilen bir tür karışık gazdır. Havanın kömür gazına oranına bağlı olarak, dönüşüm işlemine endotermik veya ekzotermik reaksiyonlar eşlik eder. Ortaya çıkan karışık gaza endotermik gaz veya ekzotermik gaz denir ve reaksiyon aşağıdaki gibi olabilir:
CmHn+m(O2+3.774N2)—mCO+n/H2+1.887mN2
Yukarıdaki reaksiyon tamamen gerçekleştirilecekse, yani CmHm cinsinden tüm C, havadaki O2 ile reaksiyona girmişse, gerekli hava/gaz m/2 (1+3.774) yani 2.387m olmalıdır. Örneğin, kullanılan hidrokarbon gazı CH4 ise, gereken hava/gaz 2.387 olmalıdır ve bu sırada üretilen karışık gaz %40.9 H2, %38.6 N2 ve %20.5 CO içerir. Reaksiyondan sonra karıştırılan gaz H2 içerir. Hava/gazın artmasıyla CO ve CO içeriği azalır, ancak H2O ve CO2 içeriği artar. Ayrıca hava/gazın artmasıyla reaksiyon sonrası karıştırılan gazdaki karbon potansiyelinin azaldığını ve oksidasyon performansının arttığını göstermektedir. Bu aynı zamanda karbon içeren çelik sinterlenirken ekzotermik gazın nadiren kullanılmasının ve çoğu endotermik gazın kullanılmasının ana nedenidir.
Genel olarak, hava/gaz tarafından 2.0-3.0 arasında üretilen karışık gaza absorpsiyon Sıcak gaz, oran 5.0'dan büyük olduğunda üretilen karışık gaza ise ekzotermik gaz denir. Hammadde olarak CH4 ile üretilen endotermik gazın hava/gaz ile çiy noktası arasındaki ilişki, hava/gazın sadece 2.4'ten 2.5'e yükseldiğini ve üretilen karışık gazın çiğlenme noktasının -25°C'den -0°C'ye yükseldiğini göstermektedir. 2.4°C'nin üzerinde. Bu nedenle, kullanıcılar endotermik gazı kendileri üretiyorsa, yeterince düşük çiğlenme noktasına sahip endotermik gaz elde etmek için hammaddelerdeki havanın gaza oranının (tercihen 1000'ten fazla olmayan) kontrolüne özellikle dikkat etmelidirler. Reaksiyondan sonra karıştırılan gazda, farklı gazların oranı reaksiyon sonundaki orana karşılık gelir ki bu genellikle (1100-XNUMX°C) olur.
Reaksiyondan sonra, gazın sıcaklığı değişirse, karıştırılan gazın karbon potansiyeli, çiy noktası ve farklı gazların oranı değişecektir. Birçok toz metalurjisi üreticisi, boru hattı üzerinden aynı anda birkaç sinterleme fırını için gerekli sinterleme atmosferini sağlamak için bir ekzotermik gaz jeneratörü kullanır. Sinterleme fırınına ulaşmadan önce atmosferin sıcaklığı düşürülmüştür. . Boru hattının yalıtımı iyi değilse ve boru hattı duvarının sıcaklığı 800°C'den düşükse, o zaman karışık gazdaki karbonun bir kısmı boru hattı duvarında karbon siyahı şeklinde birikecektir. Başka bir deyişle, karıştırılan gaz sinterleme fırınında sinterleme sıcaklığına yeniden ısıtıldığında, karbon ısısı endotermik gaz üretecinin sağlayabileceği karbon potansiyelinden çok daha düşüktür.
Bu durumda fırındaki karbon potansiyelini sağlamak için sinterleme fırınına uygun miktarda metan veya propan eklenmelidir. Şimdi bazı yabancı toz metalurjisi üreticileri, sıcaklık değişikliklerinden dolayı sinterleme atmosferini etkilememek için her sinterleme fırınının yanına küçük bir endotermik gaz jeneratörü kurmaya ve yeni üretilen endotermik gazı soğutmadan doğrudan sinterleme fırınında kullanmaya başladılar. . . Hatırlanması gereken bir diğer nokta ise, nikel oksit katalizörünün katalitik etkisiyle dahi, taşıma sonrası elde edilen karışım gazında az miktarda hidrokarbon gazının (CH4 veya C3H8 vb.) kalmasıdır. Ek olarak, gazlar arasında 900-1100℃ Reaksiyon dengeye ulaştıktan sonra, kullanımdan önce kurutulması gereken az miktarda CO2 ve H2O (gaz halinde) üretilecektir.
Endotermik gaza nitrojen eklenmesi, atmosferin karbon potansiyeline ve çiğlenme noktasına duyarlılığını tamponlamak ve sinterleme atmosferinde bazı korelasyon katsayılarını kolaylaştırmak için endotermik gazdaki nispi CO, CO2 ve H2O içeriğini azaltabilir. kontrol etmek.
Sentetik gaz, son yıllarda yabancı sinterleme fırını üreticileri tarafından sinterleme fırınında (fırın dışında bir endotermik gaz jeneratörüne ihtiyaç duymadan) doğrudan endotermik gaz üretmek (seyreltmek) için önerilen bir yöntemdir. Gaz halindeki metil alkol ile nitrojeni belli bir oranda karıştırır ve ardından direkt olarak sinterleme fırınına aktarır. Yüksek sıcaklık sinterleme bölgesinde aşağıdaki reaksiyonlar meydana gelir:
CH3OH—CO+2H2
Ayrışmış gazdaki CO ve H2 oranı, CH4 ile olağan yöntemle üretilen endotermik gazın oranına eşit olduğundan ve karışık nitrojen, endotermik gaz (1L) ile aynı bileşime sahip karışık bir atmosfer sentezlemek için birleştirilebilir. Metan, 1.05nm3 nitrojene karşılık gelir). En büyük avantajı fırın dışında endotermik gaz jeneratörü gerektirmemesidir. Ek olarak, kullanıcılar kendi gereksinimlerine göre seyreltilmiş endotermik gaz üretmek için farklı miktarlarda nitrojen gazını karıştırabilirler.
Vakum ayrıca, çoğunlukla paslanmaz çelik ve diğer malzemeleri sinterlemek için kullanılan, ancak karbon çeliğini sinterlemek için yaygın olarak kullanılmayan bir tür sinterleme atmosferidir.
Sinterleme atmosferinin fiziksel özellikleri
Sinterleme atmosferi makalelerinin ve raporlarının çoğu, sinterleme işlemi sırasında farklı sinterleme atmosferleri ve sinterlenmiş gövde arasındaki kimyasal davranışı tartışır, ancak nadiren farklı atmosferlerin fiziksel özelliklerinin sinterleme üzerindeki etkisini tartışır, ancak bu etki çoğu durumda olamaz. yok sayılmak. Örneğin, gaz viskozitesindeki fark, sinterlenmiş gövdenin kimyasal konsantrasyon gradyanına açıklık boyunca yüzeyden içeriye doğru neden olacak ve böylece sinterlenmiş gövdenin yüzey özelliklerini etkileyecektir. Başka bir örnek olarak, farklı gazların ısı kapasitesi ve ısıl iletkenliği, sinterleme süresi ve soğutma hızı üzerinde büyük bir etkiye sahiptir. Bu bölüm, okuyucuların referans olması için farklı sıcaklıklarda (sinterleme sıcaklığı civarında) bazı sinterleme atmosferlerinin ana fiziksel özelliklerini listeler.
Sinterleme sırasında atmosferle ilgili problem örnekleri
1 Mum alma sırasında parçaların yüzeyindeki çatlama örnekleri
Ağ bantlı sinterleme fırını kullanıldığında ve sinterleme atmosferi olarak endotermik gaz kullanıldığında, mum alma bölgesindeki sıcaklık artış hızı ve atmosfer iyi kontrol edilmezse, yüzey çatlaması meydana gelecektir. Birçok insan bu fenomenin yağlayıcının hızlı ayrışmasından kaynaklandığını düşünüyor, ancak durum böyle değil. Asıl sebep, endotermik gazdaki karbon monoksitin demir, nikel ve diğer metallerin katalizi altında 450-700℃ sıcaklık aralığında katı karbon ve karbondioksite ayrıştırılmasıdır. Hacmini genişleten ve yukarıda bahsedilen yüzey çatlaması olgusuna neden olan, sinterlenmiş gövdenin gözeneklerinde yeni biriken katı karbondur.
Parçaların kalitesi, farklı atmosferlerde sinterleme işlemi sırasında sıcaklığa göre değişir. Bunlardan atmosfer 3, kuru endotermik kömür gazıdır ve atmosfer 4 ve 5, farklı miktarlarda su buharı eklenmiş endotermik kömür gazıdır. Sinterleme işlemi sırasında parçaların kalitesinin yaklaşık 200°C'de düşmeye başladığı, bu da içindeki katı yağlayıcının sürekli olarak ayrıştığı ve sinterleme gövdesinden taşarak kalitesini düşürdüğü anlamına gelir. Tabii ki, karıştırılan tozda katı yağlayıcı yoksa, yukarıdaki fenomen mevcut değildir. Yukarıdaki üç atmosfer kullanılırsa, atmosfer yaklaşık 450°C'de sinterlenmiş gövdenin kalitesinden ne kadar kuruysa, bu olay o kadar ciddi olacaktır.
Ancak ilginç olan şu ki, gaz 3 (kuru endotermik gaz) kullanıldığında, katı yağlayıcıların varlığından bağımsız olarak yüzey çatlaması meydana gelir, bu da bunun doğrudan mum alma ile ilgili olmadığını gösterir ve çatlaklarda karbonca zengin gaz bulunur. Olgu, yukarıdaki açıklamanın doğruluğunu teyit edebiliriz.
Yukarıda bahsedilen çatlama olgusunun ortaya çıkmasını önlemenin birkaç yolu vardır. En doğrudan şey, kırık hatları kırmadan sinterleme atmosferini endotermik gazdan hidrojen-azot karışımına değiştirmektir. Sinterleme atmosferi değiştirilemiyorsa iki yöntem vardır. Biri su buharı içeren endotermik gazın bir kısmını sinterleme fırınının mum alma bölgesine üflemektir. Ancak, bu yöntemin fiili operasyonda kararlı kontrol elde etmesi zordur.
Sinterleme fırınının hava akışı kontrolü iyi değildir ve sinterleme bölgesine giren yüksek çiy noktası atmosferi olgusu sinterleme kalitesini etkileyebilir. İkinci ve en iyi yöntem ise sinterleme fırınının mum alma bölgesindeki parçaların ısıtma hızını artırarak en kısa sürede 450'yi geçmesini sağlamaktır. -600°C'de çatlamanın meydana geldiği alanda, sözde hızlı mum alma genellikle bu fenomen için tasarlanmıştır.
2 AstaloyCrM sinterleme örneği
Metal krom, düşük fiyatı ve iyi güçlendirici etkisi nedeniyle alaşımlı çelikte yaygın olarak kullanılmaktadır. Bununla birlikte, krom içeren sinterlenmiş çelik, üretim sürecinde birçok sorunla karşılaşacaktır. Biri, daha düşük oksijen ve karbon içeriğine sahip hammadde tozu elde etmek için sıkı bir atomizasyon ve tavlama indirgeme işleminden geçmesi gereken krom içeren demir tozunun üretimidir. .
İsveçli Honganas AB, şu anda bu hammadde tozunu düşük maliyetle üretebilen dünyadaki tek üreticidir. İkincisi, yüksek kaliteli krom içeren demir tozu elde edilebilse bile, sinterleme ve ortam sıcaklığı, özellikle sinterleme atmosferi iyi kontrol edilemezse, sinterleme ve oksidasyon sırasında oksitlenme olasılığının daha yüksek olacağı ve sinterleme performansı düşecektir.
Termodinamik hesaplamalar ve çok sayıda deney, AsaloyCrM'nin sinterleme atmosferi olarak endotermik gaz kullanılması durumunda, çiy noktası çok düşük olsa bile sinterleme gereksinimlerinin karşılanamayacağını kanıtlamıştır.
Yani AsaloyCrM'nin sinterlenmesi için sadece saf hidrojen veya hidrojen-azot karışımı kullanılabilir. Şu anda, ikincisinin çoğu kullanılmaktadır. , Hidrojen oranı %5-20 arasındadır. Okuyucuya sadece sinterleme atmosferinin bileşimini sağlamak için değil, aynı zamanda sinterleme atmosferinin kalitesini de sağlamak için hatırlatılmalıdır.
Burada sözde kalite, genellikle atmosferdeki kısmi oksijen basıncı ile kalibre edilen sinterleme atmosferindeki oksidasyon derecesini ifade eder. 1120℃'de sinterleme yaparken, atmosferdeki oksijen kısmi basıncı 1×10-14Pa'dan düşükse, sinterleme işlemi sırasında oksidasyon meydana gelmez.
Sıcaklık düşürüldüğünde, oksidasyonu önlemek için atmosferdeki oksijen kısmi basıncının bile düşük olması gerekir. Ayrıca 1125℃'de sinterlenen AsaloyCrM'nin 1×10-14Pa'da oksitlenmemesini de sağlayabilir. Yukarıdaki hesaplama deneysel verilerle doğrulanmıştır.
Lütfen yeniden basım için bu makalenin kaynağını ve adresini saklayın: Sinterlenmiş Çeliğin Sinterleme Sürecinde Atmosfer Kontrolü ve Performansı
Minhe Basınçlı Döküm Şirketi kaliteli ve yüksek performanslı Döküm Parçaları üretmeye ve sağlamaya adamıştır (metal döküm parça yelpazesi esas olarak şunları içerir: İnce Duvarlı Döküm,Sıcak Kamara Basınçlı Döküm,Soğuk Oda Döküm), Yuvarlak Servis (Döküm Servisi,Cnc İşleme,Kalıp yapımı,Yüzey İşleme).Herhangi bir özel Alüminyum döküm, magnezyum veya Zamak/çinko döküm ve diğer döküm gereksinimleri bizimle iletişime geçebilirsiniz.
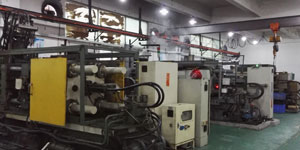
ISO9001 ve TS 16949 kontrolünde, tüm işlemler yüzlerce gelişmiş basınçlı döküm makinesi, 5 eksenli makine ve blasterlerden Ultra Sonic yıkama makinelerine kadar diğer tesisler aracılığıyla gerçekleştirilir. Müşterinin tasarımını gerçeğe dönüştürmek için deneyimli mühendisler, operatörler ve müfettişlerden oluşan ekip.
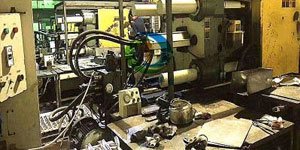
Dökümlerin sözleşmeli üreticisi. Yetenekler, 0.15 lbs'den başlayan soğuk oda alüminyum döküm parçaları içerir. 6 lbs'ye kadar, hızlı değişim kurulumu ve işleme. Katma değerli hizmetler arasında polisaj, titreşim, çapak alma, kumlama, boyama, kaplama, kaplama, montaj ve kalıplama yer alır. Çalışılan malzemeler arasında 360, 380, 383 ve 413 gibi alaşımlar bulunur.
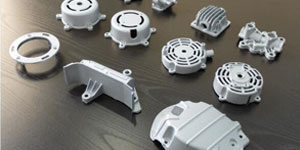
Çinko pres döküm tasarım yardımı/eşzamanlı mühendislik hizmetleri. Hassas çinko dökümlerin özel üreticisi. Minyatür dökümler, yüksek basınçlı dökümler, çok kızaklı kalıp dökümleri, geleneksel kalıp dökümleri, birim kalıp ve bağımsız kalıp dökümleri ve boşluklu sızdırmaz dökümler üretilebilir. Dökümler, +/- 24 inç toleransta 0.0005 inç'e kadar uzunluk ve genişliklerde üretilebilir.
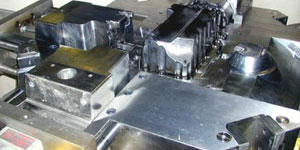
ISO 9001: 2015 sertifikalı döküm magnezyum üreticisi, Yetenekler arasında 200 ton sıcak odaya ve 3000 ton soğuk odaya kadar yüksek basınçlı magnezyum kalıp dökümü, takım tasarımı, cilalama, kalıplama, işleme, toz ve sıvı boyama, CMM özelliklerine sahip tam kalite güvencesi bulunur , montaj, paketleme ve teslimat.
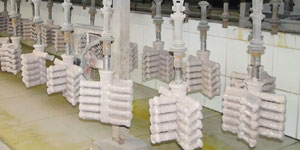
ITAF16949 sertifikalı. Ek Döküm Hizmeti Dahil yatırım dökümleri,kum dökümü,Yerçekimi Döküm, Kayıp Köpük Döküm,Savurma döküm,Vakumlu Döküm,Kalıcı Kalıp Döküm,.Yetenekler arasında EDI, mühendislik yardımı, katı modelleme ve ikincil işleme yer alır.
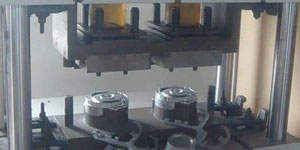
Döküm Endüstrileri Arabalar, Bisikletler, Uçaklar, Müzik aletleri, Deniz Araçları, Optik cihazlar, Sensörler, Modeller, Elektronik cihazlar, Muhafazalar, Saatler, Makineler, Motorlar, Mobilya, Mücevher, Jigler, Telekom, Aydınlatma, Tıbbi cihazlar, Fotoğraf cihazları, Robotlar, Heykeller, Ses ekipmanları, Spor ekipmanları, Aletler, Oyuncaklar ve daha fazlası.
Bundan sonra ne yapmanıza yardımcı olabiliriz?
∇ Ana Sayfaya Git Çin Döküm
→Döküm Parçaları-Ne yaptığımızı öğren.
→ Hakkında İlgili İpuçları Pres Döküm Hizmetleri
By Minghe Döküm Üreticisi |Kategoriler: Faydalı Makaleler |Malzeme Etiketler: Alüminyum Döküm, Çinko Döküm, Magnezyum Döküm, Titanyum Döküm, Paslanmaz Çelik Döküm, Pirinç Döküm,Bronz Döküm,Döküm Videosu,Tarihçe,Alüminyum Döküm |Yorumlar Kapalı