Damgalama Sırasında Kalıp Patlamasının Nedenleri Kalıp Çelik Kullanımı
Farklı damgalama süreçleri ve farklı çalışma koşulları nedeniyle kalıp patlamasının birçok nedeni vardır. Aşağıda, kalıbın tasarımında, imalatında ve kullanımında kalıp patlamasının nedenlerinin kapsamlı bir analizi ve buna karşılık gelen iyileştirme önlemleri yer almaktadır.
Kalıp malzemesi iyi değildir ve sonraki işlemlerde kırılması kolaydır.
Farklı malzemelerin kalıp ömrü genellikle farklıdır. Bu nedenle kalıbın çalışan kısımlarının malzemeleri için iki temel şart ileri sürülmektedir:
- (1) Malzemenin kullanım performansı, yüksek sertliğe (58-64HRC) ve yüksek mukavemete, yüksek aşınma direncine ve yeterli tokluğa, küçük ısıl işlem deformasyonuna ve belirli bir derecede termal sertliğe sahip olmalıdır;
- (2) İyi süreç performansı. Kalıpta çalışan parçaların işlenmesi ve üretim süreci genellikle daha karmaşıktır.
Bu nedenle, dövülebilirlik, işlenebilirlik, sertleşebilirlik, sertleşebilirlik, su verme çatlak hassasiyeti ve öğütme işlenebilirliği gibi çeşitli işleme tekniklerine uyarlanabilir olmalıdır.
Isıl işlem: uygun olmayan su verme ve tavlama işleminin neden olduğu deformasyon
Uygulama, kalıbın ısıl işlem kalitesinin, kalıbın performansı ve hizmet ömrü üzerinde büyük bir etkisi olduğunu kanıtlamıştır. Kalıp arızasının nedenlerinin analizi ve istatistiklerinden, uygun olmayan ısıl işlemden kaynaklanan kalıp arızası "kazalarının" %40'tan fazla olduğu görülebilir.
- (1) Dövme işlemi Bu, kalıp işleme parçalarının üretim sürecinde önemli bir bağlantıdır. Yüksek alaşımlı takım çeliği kalıpları için, genellikle karbürlerin malzemedeki dağılımı gibi metalografik yapı için teknik gereksinimler ileri sürülür.
- (2) Ön ısıl işlem, yapıyı iyileştirmek, dövme boşluğunun yapısal kusurlarını ortadan kaldırmak ve işlemeyi iyileştirmek için kalıp çalışma parçalarının malzemelerine ve gereksinimlerine bağlı olarak tavlama, normalleştirme veya su verme ve tavlama ve diğer ön ısıl işlem işlemlerini benimsemelidir. teknoloji. Yüksek karbonlu alaşımlı kalıp çeliği, ağ ikincil sementit veya zincir karbürlerini ortadan kaldırabilen, karbürleri küreselleştirip rafine edebilen ve su verme ve tavlama Kalitesini sağlamak için faydalı olan karbür dağılımının tekdüzeliğini teşvik edebilen uygun ön ısıl işleme tabi tutulur. .
- (3) Söndürme ve temperleme, kalıbın ısıl işleminde anahtar bağlantılardır. Su verme ve ısıtma sırasında aşırı ısınma meydana gelirse, sadece iş parçasının daha fazla kırılganlığına neden olmakla kalmaz, aynı zamanda soğutma sırasında kolayca deformasyona ve çatlamaya neden olur ve bu da kalıbın ömrünü ciddi şekilde etkiler. Kalıbın söndürülmesi ve ısıtılması sırasında oksidasyon ve dekarburizasyonun önlenmesine özel dikkat gösterilmeli ve ısıl işlem proses özellikleri sıkı bir şekilde kontrol edilmelidir. Koşullar izin verdiğinde, vakumlu ısıl işlem kullanılabilir. Söndürme işleminden sonra zamanla tavlanmalı ve teknik gereksinimlere göre farklı tavlama işlemleri uygulanmalıdır.
- (4) Gerilim giderme tavlama kalıbı çalışma parçaları, kaba işleme sonrasında gerilim giderme tavlama işlemine tabi tutulmalıdır. Amaç, su verme sırasında aşırı deformasyon ve çatlakları önlemek için kaba işlemenin neden olduğu iç gerilimi ortadan kaldırmaktır. Yüksek hassasiyet gereksinimleri olan kalıplar için, kalıbın hassasiyetini stabilize etmeye ve hizmet ömrünü iyileştirmeye elverişli olan taşlama veya elektrikli işleme sonrasında stres giderme ve tavlama işleminden geçmeleri gerekir.
Kalıp taşlama düzlüğü yeterli değildir, bu da eğilme deformasyonuna neden olur
Kalıp işleme parçalarının yüzey kalitesi, kalıbın kullanım ömrünü doğrudan etkileyen, kalıbın aşınma direnci, kırılma direnci ve yapışma direnci ile çok yakın bir ilişki içindedir, özellikle yüzey pürüzlülük değeri kalıp ömrü üzerinde büyük bir etkiye sahiptir. Yüzey pürüzlülük değeri çok büyükse, çalışma sırasında stres konsantrasyonu oluşacak ve tepeler ve vadiler arasında kalıbın dayanıklılığını ve iş parçası yüzeyinin korozyon direncini doğrudan etkileyecek olan çatlaklar kolayca oluşacaktır. Kalıbın ömrü Ve hassasiyet, bunun için aşağıdaki hususlara dikkat etmelisiniz:
- (1) Kalıp işleme parçalarının işlenmesi sırasında, parçaların yüzeyinin taşlanması ve yakılması olgusunu ve taşlama işlemi koşulları ve işlem yöntemlerini (taşlama çarkı sertliği, parçacık boyutu, soğutucu, besleme hızı gibi) önlemek gerekir. ve diğer parametreler) sıkı bir şekilde kontrol edilmelidir;
- (2) İşleme işlemi sırasında, kalıp çalışma parçalarının yüzeyinde bıçak izleri, ara katmanlar, çatlaklar ve darbe izleri gibi makro kusurları önleyin. Bu kusurların varlığı, stres konsantrasyonuna neden olacak ve kırılmanın temel nedeni haline gelecek ve bu da kalıbın erken arızalanmasına neden olacaktır;
- (3) Daha küçük bir yüzey pürüzlülük değeri elde etmek ve kalıbın hizmet ömrünü uzatmak için taşlama, taşlama ve cilalama ve diğer bitirme ve ince işlemlerin kullanılması.
Tasarım süreci
Kalıp mukavemeti yeterli değil, bıçak kenarı aralığı çok yakın, kalıp yapısı mantıksız, şablon blok sayısı yetersiz, destek tahtası yok, kalıp doğru yönlendirilmiyor ve boşluk mantıksız.
- (1) Yerleşim ve örtüşme için mantıksız ileri geri besleme düzeni yöntemi ve çok küçük örtüşme değeri genellikle kalıbın hızlı aşınmasına veya dışbükey ve içbükey kalıpların zarar görmesine neden olur. Kalıbın ömrünü iyileştirmek için yerleşim yöntemini ve kenar değerini makul bir şekilde seçin.
- (2) Kalıbın kılavuz mekanizmasının hassas ve güvenilir şekilde yönlendirilmesi, kalıbın çalışma parçalarının aşınmasını azaltmada ve dışbükey ve içbükey kalıpların, özellikle boşluksuz ve küçük boşluklu boşluk kalıplama kalıplarının, kompozit kalıpların hasar görmesini önlemede büyük bir etkiye sahiptir. ve çoklu istasyonlar. Aşamalı kalıplar daha etkilidir. Kalıbın ömrünü arttırmak için kılavuz formunun doğru seçilmesi ve kılavuz mekanizmasının doğruluğunu işlemin doğasına ve parçaların doğruluğuna göre belirlemek gerekir.
- (3) Kalıbın kesici kenarının geometrik parametreleri (dışbükey ve içbükey kalıp).
Tel kesme işlemi
Diş çekme yapay olarak çekilir, diş açma aralığı yanlış işlenir ve metamorfik katman net açı ve diş kesmeden etkilenmez.
Kalıbın kesici kenarı çoğunlukla tel kesme ile işlenir. Tel kesme işleminin termal etkisi ve elektrolizi nedeniyle, kalıbın yüzeyinde belirli bir kalınlıkta metamorfik tabaka üretilir, bu da yüzey sertliğinin azalmasına neden olur ve mikro çatlaklar vb. kalıp boşluğunu doğrudan etkileyen erken aşınmaya eğilimlidir. Kenarları tutmak ve kesmek kolaydır ve kalıbın servis ömrünü kısaltır. Bu nedenle, on-line kesme işleminde, metamorfik tabakanın derinliğini en aza indirmek için makul elektrik standartları seçilmelidir.
Zımba Ekipmanı Seçimi
Zımba tonajı, zımbalama kuvveti yeterli değil ve kalıp çok derin ayarlanmış.
Damgalama ekipmanının (presler gibi) doğruluğu ve sağlamlığı, kalıbın ömrü üzerinde son derece önemli bir etkiye sahiptir. Damgalama ekipmanı yüksek hassasiyete ve iyi sertliğe sahiptir ve kalıbın ömrü büyük ölçüde iyileştirilmiştir. Örneğin, karmaşık silikon çelik sac kalıbın malzemesi, ortalama 2 ila 10,000 yeniden öğütme ömrüne sahip sıradan bir açık preste kullanılabilen Crl30,000MoV'dur; yeni bir hassas preste, kalıbın yeniden öğütme ömrü 60,000 ila 120,000'e ulaşabilir.
damgalama işlemi
Damgalama parçalarının hammadde kalınlık toleransı tolerans dışıdır, malzeme performans dalgalanmaları, kötü yüzey kalitesi (pas gibi) veya kirli (yağ lekeleri gibi) vb., kalıp çalışma parçalarının daha fazla aşınmasına ve yıpranmasına neden olur ve kolay yongalama. Bu sebeple not edilmelidir:
- (1) Damgalama deformasyon kuvvetini azaltmak için mümkün olduğunca iyi damgalama işlenebilirliğine sahip hammaddeler kullanın;
- (2) Damgalamadan önce hammaddelerin kalitesi, kalınlığı ve yüzey kalitesi kesinlikle kontrol edilmeli ve hammaddeler silinerek temizlenmelidir. Gerekirse, yüzey oksitleri ve pas giderilmelidir;
- (3) Damgalama işlemine ve hammadde türlerine göre gerektiğinde yumuşatma işlemi ve yüzey işlemi düzenlenebilir ve uygun yağlayıcılar ve yağlama işlemleri seçilebilir.
8. Üretim operasyonlarının doğru kullanımı ve makul bakımı.
Lütfen yeniden basım için bu makalenin kaynağını ve adresini saklayın:Damgalama Sırasında Kalıp Patlamasının Nedenleri Kalıp Çelik Kullanımı
Minhe Basınçlı Döküm Şirketi kaliteli ve yüksek performanslı Döküm Parçaları üretmeye ve sağlamaya adamıştır (metal döküm parça yelpazesi esas olarak şunları içerir: İnce Duvarlı Döküm,Sıcak Kamara Basınçlı Döküm,Soğuk Oda Döküm), Yuvarlak Servis (Döküm Servisi,Cnc İşleme,Kalıp yapımı,Yüzey İşleme).Herhangi bir özel Alüminyum döküm, magnezyum veya Zamak/çinko döküm ve diğer döküm gereksinimleri bizimle iletişime geçebilirsiniz.
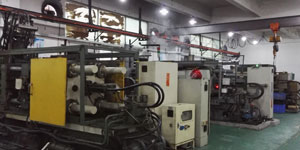
ISO9001 ve TS 16949 kontrolünde, tüm işlemler yüzlerce gelişmiş basınçlı döküm makinesi, 5 eksenli makine ve blasterlerden Ultra Sonic yıkama makinelerine kadar diğer tesisler aracılığıyla gerçekleştirilir. Müşterinin tasarımını gerçeğe dönüştürmek için deneyimli mühendisler, operatörler ve müfettişlerden oluşan ekip.
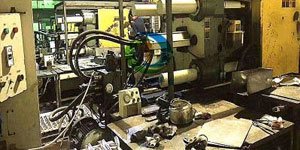
Dökümlerin sözleşmeli üreticisi. Yetenekler, 0.15 lbs'den başlayan soğuk oda alüminyum döküm parçaları içerir. 6 lbs'ye kadar, hızlı değişim kurulumu ve işleme. Katma değerli hizmetler arasında polisaj, titreşim, çapak alma, kumlama, boyama, kaplama, kaplama, montaj ve kalıplama yer alır. Çalışılan malzemeler arasında 360, 380, 383 ve 413 gibi alaşımlar bulunur.
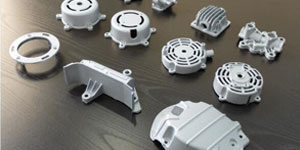
Çinko pres döküm tasarım yardımı/eşzamanlı mühendislik hizmetleri. Hassas çinko dökümlerin özel üreticisi. Minyatür dökümler, yüksek basınçlı dökümler, çok kızaklı kalıp dökümleri, geleneksel kalıp dökümleri, birim kalıp ve bağımsız kalıp dökümleri ve boşluklu sızdırmaz dökümler üretilebilir. Dökümler, +/- 24 inç toleransta 0.0005 inç'e kadar uzunluk ve genişliklerde üretilebilir.
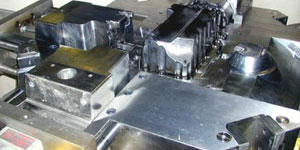
ISO 9001: 2015 sertifikalı döküm magnezyum üreticisi, Yetenekler arasında 200 ton sıcak odaya ve 3000 ton soğuk odaya kadar yüksek basınçlı magnezyum kalıp dökümü, takım tasarımı, cilalama, kalıplama, işleme, toz ve sıvı boyama, CMM özelliklerine sahip tam kalite güvencesi bulunur , montaj, paketleme ve teslimat.
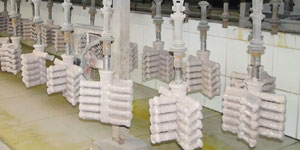
ITAF16949 sertifikalı. Ek Döküm Hizmeti Dahil yatırım dökümleri,kum dökümü,Yerçekimi Döküm, Kayıp Köpük Döküm,Savurma döküm,Vakumlu Döküm,Kalıcı Kalıp Döküm,.Yetenekler arasında EDI, mühendislik yardımı, katı modelleme ve ikincil işleme yer alır.
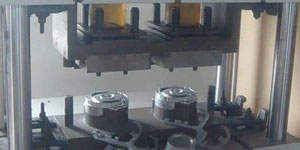
Döküm Endüstrileri Arabalar, Bisikletler, Uçaklar, Müzik aletleri, Deniz Araçları, Optik cihazlar, Sensörler, Modeller, Elektronik cihazlar, Muhafazalar, Saatler, Makineler, Motorlar, Mobilya, Mücevher, Jigler, Telekom, Aydınlatma, Tıbbi cihazlar, Fotoğraf cihazları, Robotlar, Heykeller, Ses ekipmanları, Spor ekipmanları, Aletler, Oyuncaklar ve daha fazlası.
Bundan sonra ne yapmanıza yardımcı olabiliriz?
∇ Ana Sayfaya Git Çin Döküm
→Döküm Parçaları-Ne yaptığımızı öğren.
→ Hakkında İlgili İpuçları Pres Döküm Hizmetleri
By Minghe Döküm Üreticisi |Kategoriler: Faydalı Makaleler |Malzeme Etiketler: Alüminyum Döküm, Çinko Döküm, Magnezyum Döküm, Titanyum Döküm, Paslanmaz Çelik Döküm, Pirinç Döküm,Bronz Döküm,Döküm Videosu,Tarihçe,Alüminyum Döküm |Yorumlar Kapalı