Vermiküler Demir Üretiminin Proses Kontrolü
Gri demir ile karşılaştırıldığında, vermiküler demirin çekme mukavemeti en az %70, elastisite modülü %35 ve yorulma mukavemeti neredeyse iki katına çıkar. Alüminyum alaşımı ile karşılaştırıldığında, vermiküler demirin mukavemeti ve sertliği iki kat daha yüksektir ve yorulma mukavemeti iki kat daha yüksektir. Vermiküler demirin bu özellikleri, motora güç/ağırlık oranını iyileştirme ve silindir basıncını artırma olanağı sağlar. Artan silindir basıncı, yeni nesil doğrudan enjeksiyonlu dizel motorun optimum performansının anahtarıdır. Vermiküler demirin yaygın uygulamasını karşılamak için, döküm endüstrisi şu anda aktif olarak hazırlanmakta, yoğun yatırımlar yapmakta ve vermiküler demir üretimini istikrarlı ve güvenilir hale getirmek için yeni süreçleri yeniden inşa etmektedir.
Prototipten seri üretime kadar vermiküler demir motorlar için belirleyici faktör kalite riskidir. Yüksek kaliteli vermiküler demir için, kararlı bölge çok küçüktür, yalnızca %0.008 magnezyum içeriği aralığındadır. %0.001 magnezyum kaybı gibi eser bir miktar, mekanik özelliklerin %25 ila %40 oranında düşmesine neden olacak olan pul grafit üretecektir. Bu makale, termal analiz yöntemlerine dayalı bir proses kontrol sistemini açıklamaktadır. Sistem, magnezyum kaybını ölçer ve pul grafit oluşumunu önlemek için çevrimiçi olarak erimiş demirin durumunu ayarlar. Bu çevrimiçi kontrol ölçüm ve ayarlama yöntemi, vermiküler demir üretme sürecindeki oynaklığı en düşük noktaya indirir ve vermiküler demir üretiminin neden olduğu kalite riskini temel olarak ortadan kaldırır.
Yüksek beygir gücü, yüksek tork, düşük egzoz emisyonları ve azaltılmış yakıt tüketimi talebi artmaya devam ediyor. Bu, yüksek güçlü dizel motor tasarımcılarını, motorun termal yükünü ve mekanik yükünü büyük ölçüde artıran ateşleme tepe basıncını artırmaya zorlar. Termal yük ve mekanik yük aynı anda artar, böylece şu anda kullanılan konvansiyonel dökme demir ve alaşımlı dökme demir (CrMo) motorlar kullanımlarının üst sınırına ulaşmış veya aşmıştır. Motor üreticileri, daha yüksek mukavemete ve daha iyi ısı direncine sahip malzemelere ihtiyaç duyar.
Vermiküler demir hızla insanlar için tercih edilen malzeme haline geldi. Yeni nesil kamyon motorlarının silindir bloğu, silindir kapağı ve silindir gömleğinin güvenilirliğini büyük ölçüde artırır. Çeşitli özelliklerin (döküm özellikleri, işleme özellikleri, ısıl iletkenlik ve mekanik özellikler gibi) en iyi kombinasyonunu elde etmek için, bu parçalar %0 ila %20 arasında bir küreselleşme oranıyla yapılmalıdır (%80 ila %100 sürünme oranı). ) Vermiküler demirden yapılmıştır. Küreselleşme oranı %20'yi aşarsa, bir dizi olumsuz faktöre neden olur. Örneğin, büzülme miktarı çok fazladır ve silindir kapakları gibi karmaşık şekillere sahip parçalar büzülmeye özellikle eğilimlidir. Diğer bir örnek, işleme sırasında aşırı aşınma nedeniyle takım ömrünün azalmasıdır. Ayrıca termal iletkenlikte önemli bir azalma vardır, bu da termal strese vb. neden olur. Vermiküler demirin diğer ucunda, pul grafit görünümü mekanik özelliklerde doğrusal bir düşüşe neden olacak ve motorun yeni gereksinimleri karşılayamamasına neden olacaktır. Özetle, yeni nesil kamyon motorlarının ihtiyaçlarını karşılamak için yüksek mukavemetli vermiküler demirin sferoidleşme oranı %0 ile %20 arasında olmalıdır (yani, sünme oranı pulsuz, %80'in üzerindedir).
Üretim süreci kontrolünün kullanılıp kullanılmaması, ürünün yıllık çıktısına, ürünün karmaşıklığına ve metalografik yapıda izin verilen değişiklik aralığına bağlıdır. Şekil 1'de gösterildiği gibi, külçe kalıplar gibi nispeten basit, düşük hacimli parçalar genellikle geleneksel döküm yöntemleriyle üretilebilir. Proses kontrolü genellikle gerekli değildir ve ekonomik olarak uygun maliyetli değildir. Egzoz boruları, krank manşonları ve braketler gibi bileşenlerin yıllık üretimi arttığında, proses kontrolünün devreye alınması mantıklı olmalıdır. Bu tür bir ürün büyük bir yıllık üretime sahip olmasına rağmen, yıllık döküm tonajı yüksek değildir. Metalografik yapının gereksinimleri çok katı değildir ve küreselleşme oranının %50 kadar yüksek olmasına izin verir. Ayrıca bu tür parçaların az miktarda işlenmesi nedeniyle üretime eklenebilecek titanyum artışının kontrol edilebilir aralığı genişletmesine izin verilebilir. Bu tür bir ürün için, geleneksel döküm yöntemleri ve sıkı eğitim, vermiküler demir üretimi için genellikle yetkindir. Ancak kalite kontrol açısından süreç kontrolü daha güvenli olmalıdır. Benzer şekilde, proses kontrolü de büyük deniz motoru bloklarının ve silindir kapaklarının üretimi için bir garanti sağlar. Büyük boyut ve düşük üretim miktarı, ürünlerin üretimine elverişli olmasına rağmen, standardı aşan ürünlerin neden olduğu ekonomik kayıplar, bir dizi proses kontrol sistemi eklemek için yeterlidir.
Proses kontrolüne en çok ihtiyaç duyan ürünler, büyük yıllık üretim, yüksek karmaşıklık ve katı teknik gereksinimlere sahip otomobil motor silindir blokları, silindir kapakları ve fren diskleridir. Bu ürünlerin yıllık üretim hacmi ve yıllık tonajları çok yüksektir. Boyutları karmaşıktır, metalografik yapıya ihtiyaç duyarlar ve büzülme boşlukları üretme eğilimindedirler. Bu ürünlerin herhangi bir kalite riski olmamalıdır, aksi takdirde kayıp çok ciddi olacaktır.
Motor bloğu, silindir kapağı ve silindir yatağının performansına ilişkin katı gereksinimler, üretim ürün spesifikasyonlarının temelini oluşturmuştur. Dökülebilirlik, işlenebilirlik ve mekanik özelliklerin en kapsamlı performansını elde etmek için, bileşenin tüm önemli parçalarında küreselleşme oranı %0 ila %20 aralığında olmalıdır. Daha da önemlisi, yerel zayıflıktan kaynaklanan parçalara zarar vermemek için pul grafitten kesinlikle kaçınılmalıdır. İyi bir mekanik katkı elde etmek için serbest karbürler minimuma indirilmelidir. Bu nedenle titanyum kesinlikle eklenmemelidir. Son olarak, üretim açısından bakıldığında, metalografik yapının neden olduğu en düşük hurda oranını sağlamak için dökümhanenin istikrarlı ve güvenilir bir sürece ihtiyacı vardır. Otomotiv endüstrisindeki üreticiler kalite güvencesi ister ve dökümlerin %100'ü metalografik gereksinimleri karşılamalıdır. Silindir bloklarının, silindir kapaklarının ve silindir yuvalarının büyük ölçekli, güvenilir üretimi, dökümden önce süreçteki dalgalanmaları ortadan kaldırmak için erimiş demirin doğru analizini ve çevrimiçi ayarlanmasını gerektirir.
Vermiküler Demir Stabilitesi
Sıkıştırılmış demirin karmaşık parçalar (motor blokları gibi) üretmek için büyük miktarlarda kullanılmamasının nedeni, sıkıştırılmış demirin kararlı alanının üretimde herhangi bir risk olmamasını sağlamak için çok küçük olmasıdır. Genel olarak konuşursak, bu stabil bölge, Şekil 0.008'de gösterildiği gibi yalnızca %2 magnezyum alanını kapsar. Platformun stabil bölgedeki boyutu ve konumu ürüne göre değişir. Aslında, mevcut magnezyum aralığı bundan daha küçüktür. Çünkü her 5 dakikada bir aktif magnezyum %0.001 yanacaktır. Erimiş demirin ilk dökme noktası, son döküm parçada pul grafit görünmemesini sağlamak için sıkıştırılmış demirin keskin dönüş noktasından gri demire yeterince uzak olmalıdır. Erimiş demire magnezyum eklendiğinde, yaklaşık 15 dakika içinde pul grafit görünecektir.
Başlangıç noktası stabil platformun sağ tarafına çok yakın olmamalıdır (yüksek magnezyum içeriği), aksi takdirde daha ince kısımda ve hızlı soğuyan kısımda büyük miktarda küresel grafit oluşmasına neden olacaktır.
Küçük kullanılabilir platform alanına ek olarak, platform alanı sürekli hareket halindedir. Aktif oksijen ve kükürt içeriği yüksekse, daha aktif magnezyum tüketirler ve tüm platform sağa doğru hareket eder (yüksek magnezyum içeriği). Tersine, aktif oksijen ve kükürt içeriği düşükse, platform sola hareket edecektir (düşük magnezyum içeriği). Hammaddelerin bileşimindeki, saflıktaki, oksidasyon derecesi ve nemdeki vb. değişiklikler, insanların sabit bir kimyasal bileşim aralığı ile vermiküler demiri kontrol etmesini imkansız hale getirir.
Vermiküler demirden gri demire dönüşümün sadece aktif magnezyumu %0.001 oranında azaltması gerekse de, magnezyumun yanması tüm parçanın pul grafit olmasına neden olmaz. Aktif magnezyum yeterli olmadığında, grafit önce pullar oluşturur ve katılaştıkça dışa doğru genişler ve magnezyum çöker ve katı-sıvı arayüzünün ön ucunda yoğunlaşır. Başlangıç aktif magnezyum miktarı uygunsa, ötektik sınırında Şekil 3'te gösterildiği gibi vermiküler grafit oluşacaktır. Pul grafit önce saçılmış pul grafit noktaları olarak belirir. Tüm yaygın pul grafitlerin aksine, bu izole pul grafit noktalarının ultrasonla tespit edilmesi zordur. Ultrason ile taranma ihtimalleri yüksek değil.
Magnezyumun vermiküler demire duyarlılığı Şekil 4'te gösterilebilir: Bir ton sıcak metal potaya, sadece 10 gram magnezyum ekleyin, Φ25 test örneğinde dağılan pul grafit noktaları tamamen vermiküler grafite dönüştürülebilir. Pul grafit noktalı test çubuğunun çekme dayanımı sadece 300 MPa iken, aynı test çubuğunun tam kayma ile çekme dayanımı 450 MPa'ya ulaşır.
Şekil 5'te gösterildiği gibi aşılayıcı ayrıca vermiküler demirin kararlı platformuna karşı çok hassastır: Bir ton erimiş demire 80 gram aşılayıcı eklemek, Φ25 test çubuğundaki küreselleşme oranını %3'ten %21'e yükseltecektir. Aşılama miktarı yüksektir ve küresel grafit oluşumuna elverişli olan kristal çekirdek çoktur. Bu, vermiküler demir platformunu yüksek küreselleşme oranı yönünde yükseltir. Düşük aşılama oranı, platformun aşağı doğru hareket etmesine neden olur. Erimiş demirin aşırı ısınma sıcaklığı, bekletme süresi, hammaddelerin kimyasal bileşimi, aşılayıcı tipi ve aşılama miktarı gibi çok sayıda faktör, vermiküler demir platformunun konumunu etkileyecektir.
Herhangi bir proses kontrol teknolojisinin en temel gereksinimi, erimiş demirin durumunu doğru bir şekilde ölçmek ve analiz etmektir. Vermiküler demir için güvenilir üretim kontrolü, sürünme-kül geçişinden aktif magnezyumun kritik noktasının, müteakip magnezyum tükenmesinin derecesinin ve aşılama derecesinin aynı anda ölçülmesini gerektirir.
200 gramlık termal analiz numunesi, küreselleştirme ve aşılamadan sonra Xinte probu erimiş demire sokularak elde edilir. Üç saniyelik yerleştirme işlemi sırasında, sonda duvarı ve erimiş demir bir termal denge durumuna ulaşır. Geleneksel termal analiz numune kabından farklı olarak, bu ince duvarlı numune alıcı, her seferinde aynı numune hacmini garanti etmekle kalmaz, aynı zamanda numune kabına dökülen erimiş demirde oksidasyonu da önler. Aşırı ısınmanın ölçümü daha doğrudur çünkü geleneksel termal analizde şiddetli yoğuşma fenomeni gibi bir fenomen yoktur.
Şekil 6a'da gösterildiği gibi, Xinte probu preslenmiş gerilmiş çelik sacdan yapılmıştır. Temelde küresel bir kaptır. Erimiş demiri içeren ince çelik duvar, termos benzeri bir yalıtım katmanına sahiptir. Yalıtım tabakasının kalınlığı, eşit ısı dağılımı ve çevreye soğutma sağlamak için yükseklik yönüne göre simetrik olarak kalınlaştırılır ve içindeki demir zz su küresel bir gövdenin katılaşmasına yakındır. Probdaki koruma tüpünde iki adet N tipi termokupl vardır. Termokupl her ölçümden sonra çıkarılabilir ve 100 defadan fazla tekrar tekrar kullanılabilir. İki termokupldan biri kabın tabanında, diğeri ise kabın ısı merkezinde bulunur. Kap küresel olduğundan ve serbestçe askıda kaldığından (bu, ısı emici bir brakete dayanan geleneksel termal analiz numune kabından farklıdır), erimiş demir, Şekil 6b'de gösterildiği gibi kapta düzgün bir ısı akışı oluşturur. Bu ısı akışı, erimiş demirin kap içinde sürekli olarak değiştirilmesine neden olarak, sondanın altında bir akış bölümü oluşturur.
Dökme sırasında erimiş demirin doğal kaybını taklit etmek için, prob duvarında aktif magnezyum ile reaksiyona giren bir kaplama vardır. Erimiş demir, ısı akışı tarafından tahrik edilen kaplanmış duvar boyunca akar. Reaksiyondan sonra erimiş demirin magnezyum içeriği azalır ve kabın dibindeki bölmede birikir. Doğrudan konuşursak: Probun ortasındaki termokupl, ilk dökme durumu olan reaksiyona girmemiş erimiş demiri ölçer; alttaki termokupl, dökümün bitiminden sonraki durumu ölçer. Reaktif kaplamanın formülasyonu çok özeldir. Bölmede biriken erimiş demirin merkezdeki erimiş demirden %0.003 daha az aktif olduğundan emin olunmalıdır. Bu nedenle, başlangıçtaki magnezyum içeriği sürünen kül dönüş noktasına çok yakınsa, bölmedeki erimiş demir, bu alandaki termokupl tarafından ölçülecek olan gri demir üretecektir. Bu şekilde, dökümün başlangıcında, atölye kaçınılmaz magnezyum yanma kaybını dengelemek için daha fazla magnezyum ekleyebilir.
Alttaki termokupl bir vermiküler demir eğrisi gösteriyorsa, başlangıçtaki magnezyum içeriğinin, dökümün bitiminden sonra pul grafit olmayacak kadar yüksek olduğunu gösterir.
Şekil 7, numune ölçümünden sonra Xinte probunun bir kesit erozyon diyagramıdır. Şekilde bölme alanını, ana numune alanını ve termokupl koruma tüpünü açıkça görebilirsiniz. Aktif magnezyum %0.003 oranında azaltıldığından, ayırma bölgesinde D-şekilli grafit ve ferrit matrisi oluşur. Alttaki pul grafit alanının boyutu, ana numune alanındaki ilk magnezyum içeriğini doğrudan yansıtır. Bu bölgenin boyutu, altta salınan ısıdan hesaplanabilir. Isı salınımı ile bölmenin boyutu arasındaki varyans regresyon katsayısı 0.9'u aşıyor, bu da ikisi arasındaki ilişkinin çok yakın olduğunu kanıtlıyor. Serbest kalan ısı, soğutma eğrisinin zaman entegrasyonu ile elde edilir. Aynı anda hem akımda hem de dökümün sonunda erimiş demirin durumunu ölçen bu yöntem, dökümden önce magnezyum içeriğinin doğruluğunu sağlar.
Vermiküler demir, küreselleştirici maddelere ve aşılayıcılara karşı çok hassas olduğundan, dökümhanelerin gri demir ve sfero döküm üretiminde kullanılan aşırı arıtma yöntemlerini kullanması mümkün değildir. Şekil 8'de gösterildiği gibi, duyarlılığı nedeniyle vermiküler demir, yalnızca magnezyum platform alanında değil, yalnızca kare bir pencere içinde kararlıdır. Güvenilir bir vermiküler demir üretim süreci, metalografik yapının hedefi karşılamasını sağlamak için baştan sona küreselleşmeyi ve aşılamayı kontrol etmelidir.
Ne kadar çaba gösterilirse gösterilsin, yönetim ne kadar katı olursa olsun, erimiş demirin dalgalanması her zaman kaçınılmazdır. İnsanların erimiş demir tedavisi hakkında ne kadar doğru bilgi sahibi olmaları bir yana, sandviç yöntemi gibi tek adımlı tedavi yöntemleri, her tedavinin dar vermiküler demir penceresine gireceğini garanti edemez. Karıştırma oranı, fırın sıcaklığı, tutma süresi, erimiş demir potanın ön ısıtma derecesi, kılavuz çekme hızı, erimiş demir kılavuz çekme konumu (iç veya dış ölçüm), kılavuz çekme erimiş demir ağırlığı, alaşım torba durumu, küreselleştirme maddesi gibi çok sayıda üretim değişkeni (PeSiMg)'nin gerçek magnezyum içeriği, sandviç yönteminde her katmanın alaşım düzeni ve hurda demir talaşlarının kapsamı, vb., tümü magnezyum emilimini etkileyecektir. Bu faktörlere ek olarak, aktif oksijen ve aktif kükürt içeriği de vermiküler demir pencerenin boyutunu ve konumunu değiştirecektir. Erimiş demirin potada kalma süresi, nakliye süresi ve dökme süresindeki değişiklikler, mevcut yanma süresini değiştirecektir.
Ancak, en öngörülemeyen dalgalanma faktörleri, operatör hataları veya farklı çalışma alışkanlıkları nedeniyle farklı operatörler arasındaki farklılıklardır.
Büyük ölçekli seri üretimde, tek güvenli yol, işlemden sonra erimiş demirin katılaşma özelliklerini ölçmektir. Bu şekilde, vermiküler demir pencerenin boyutunu, konumunu ve alaşım absorpsiyonunu etkileyen çeşitli faktörler kapsamlı bir şekilde ölçülmüş, analiz edilmiş ve değerlendirilmiştir. Daha sonra uygun miktarda magnezyum ve aşılayıcı eklenebilir. Her bir pota erimiş demir, ideal duruma yükseltildikten sonra dökülür. Bu iki aşamalı, ölçüm ve ayar proses kontrol yöntemi, üretim değişkenliğini en aza indirir ve dökümde pul grafit riskini tamamen ortadan kaldırır.
Sıcak Metal Pota ile Vermiküler Demir Üretiminin Proses Kontrolü
Şekil 9'da gösterildiği gibi, proses kontrolü, ilk küreselleştirme ve aşılama işleminden sonra erimiş demirin termal analizi ile başlar. Analiz sonucuna göre tel sürme makinesi magnezyum ve aşı ile eklenecek telin uzunluğunu otomatik olarak gösterir ve operatörün başlatmasını bekler. Besleme hattı tamamlandığında pota hemen döküm hattına gönderilir. Tüm ölçüm ve ayar süreci yaklaşık üç dakika sürer. Bu süre zarfında atölye, cüruf giderme gibi geleneksel ön döküm işlemlerini gerçekleştirebilir. Bu da döküm hattının devamlılığını sağlar.
Operasyonel bir bakış açısından, ham erimiş demir magnezyum içermez ve inkübasyon kapasitesi de çok sınırlıdır. Küreselleştirme ve aşılamadan sonra, magnezyum ve aşılayıcılar önce erimiş demirdeki aktif oksijeni ve sülfürü yerler ve ardından erimiş demiri tahta üzerinde belirli bir konuma "zıplar". Şekil 10'daki örnekte, erimiş demirin magnezyum indeksi ve aşılama indeksi sırasıyla 65 ve 45'tir. Gölge üretiminin ana değişim parametreleri ölçüm ve işlemden sonra erimiş demirde gösterildiğinden, termal analiz sonuçları erimiş demirin mevcut durumunu doğrudan yansıtır. Geriye kalan tek şey, erimiş demiri mevcut konumundan gerekli başlangıç noktasına yükseltmek için uygun miktarda magnezyum ve aşılayıcı eklemektir. Şekil 10'daki örnekte, önce yedi adet magnezyum kablo daha sonra 23 adet aşılama kablosu eklenmiştir. İndeks birimi ile kablo uzunluğu arasındaki ilgili ilişki, ürüne ve atölyeye göre kalibre edilir ve programda derlenir. Yaklaşık 100,000 vermiküler demir dökümün geçmiş deneyimine dayanarak, eklenen ortalama magnezyum kablo miktarı ton başına 5 metredir. Metre başına 12 gram magnezyum içerir ve %50 emilim oranıyla hesaplandığında, bir ton erimiş demir başına eklenen magnezyum miktarı sadece 30 gramdır. İlave miktarı çok küçük olduğundan ve ana değişiklikler ilk tedavide zaten meydana geldiğinden, ayarlama çok etkili ve güvenilirdir. Ayarlamadan sonra termal analiz yapmaya gerek yoktur.
İlk işlemde, işlemden sonraki durum ilk dökme konumundan daha düşük olmalıdır, böylece magnezyum ve aşılayıcının emilmesine faydalı olan tüm faktörler optimal değere ulaşsa bile, erimiş demir yalnızca ilk dökme durumuna ulaşacaktır. . Aşırı işlem görmemek dışında işlem sonrası erimiş demir, gri demir ve beyaz demir durumunda değildir. Döküm işlemini daha verimli hale getirmek için, her bir erimiş demir potasının magnezyum indeksi ve aşılama indeksi proses blok diyagramında gösterilir. Blok diyagramın değişen trendine göre operatör bir sonraki potaya eklenen erimiş demir miktarını ayarlayabilir. Karbon eşdeğer değeri de ekranda görüntülenir. Bu veriler, izlenebilmesi ve kapsamlı olabilmesi için üretim günlüğünde düzenlenmiş ve saklanmıştır ve ayrıca kalite güvencesi gereksinimlerini de karşılamaktadır.
Termal analiz ve müteakip ayarlamalar vermiküler demir üretimini garantilese de, analiz için nihai dökümün ladin kabından numune alınması tavsiye edilir. Geleneksel kalite denetimi ile karşılaştırıldığında, bu termal analiz sonucu çevrimiçi analiz sağlayabilir ve gerekirse dökümleri sınıflandırabilir. Probdaki magnezyum kaybının simülasyonu, bu "tahribatsız" inceleme tekniğini metalografik ve ultrasonik yöntemlerden daha etkili hale getirir. Bu yöntem daha büyük bir numune boyutunu ölçtüğü için, erimiş demirin sonraki 10-15 dakika içinde nasıl katılaşacağını da tespit eder.
Sonuç olarak
Proses kontrol sisteminin seçimi, ürüne ve döküm prosesine bağlıdır. Vermiküler demir motor kapağı ve silindir gibi karmaşık ürünleri dökerken, sistem aynı anda magnezyum ve aşılayıcı içeriğini kontrol etmelidir, böylece dökümün başından sonuna kadar çok dar bir pencere içinde olur. En iyi dökülebilirliği, mekanik katkıyı ve diğer kapsamlı performansı ve en iyi kullanım işlevini sağlamak için küreselleştirme oranı %0 ila %20 (sürünme oranı %80 ila %100) arasında olmalıdır. Lokal kusurları ve zayıflıkları önlemek için pul grafit lekeleri tamamen ortadan kaldırılmalıdır.
Herhangi bir proses kontrol sisteminin başlangıç noktası, erimiş demirin durumunu doğru ve etkili bir şekilde ölçmektir. Güvenilir büyük ölçekli vermiküler demir üretimi, süreç değişikliklerini ve insan operasyon hatalarını ortadan kaldırmak için uygulanabilir kontrol yöntemlerine sahip olmalıdır. Proses değişikliklerini ortadan kaldırmanın en etkili yolu, küreselleştirme ve aşılamadan sonra erimiş demir üzerinde termal analiz yapmaktır. Termal analiz sonuçlarına göre, dökümden önce doğru miktarda magnezyum ve aşılayıcı ilave edilir. Bu çevrimiçi ölçüm ve ayarlama yöntemi, döküm üretim hattının stabilitesini sağlar ve büyük ölçekli vermiküler demir üretiminin getirdiği çeşitli riskleri ortadan kaldırır.
Lütfen yeniden basım için bu makalenin kaynağını ve adresini saklayın: Vermiküler Demir Üretiminin Proses Kontrolü
Minhe Basınçlı Döküm Şirketi kaliteli ve yüksek performanslı Döküm Parçaları üretmeye ve sağlamaya adamıştır (metal döküm parça yelpazesi esas olarak şunları içerir: İnce Duvarlı Döküm,Sıcak Kamara Basınçlı Döküm,Soğuk Oda Döküm), Yuvarlak Servis (Döküm Servisi,Cnc İşleme,Kalıp yapımı,Yüzey İşleme).Herhangi bir özel Alüminyum döküm, magnezyum veya Zamak/çinko döküm ve diğer döküm gereksinimleri bizimle iletişime geçebilirsiniz.
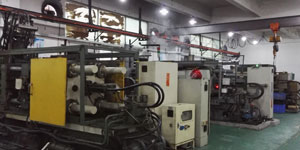
ISO9001 ve TS 16949 kontrolünde, tüm işlemler yüzlerce gelişmiş basınçlı döküm makinesi, 5 eksenli makine ve blasterlerden Ultra Sonic yıkama makinelerine kadar diğer tesisler aracılığıyla gerçekleştirilir. Müşterinin tasarımını gerçeğe dönüştürmek için deneyimli mühendisler, operatörler ve müfettişlerden oluşan ekip.
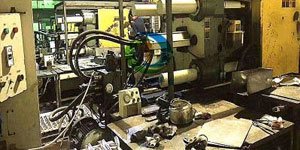
Dökümlerin sözleşmeli üreticisi. Yetenekler, 0.15 lbs'den başlayan soğuk oda alüminyum döküm parçaları içerir. 6 lbs'ye kadar, hızlı değişim kurulumu ve işleme. Katma değerli hizmetler arasında polisaj, titreşim, çapak alma, kumlama, boyama, kaplama, kaplama, montaj ve kalıplama yer alır. Çalışılan malzemeler arasında 360, 380, 383 ve 413 gibi alaşımlar bulunur.
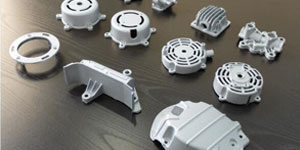
Çinko pres döküm tasarım yardımı/eşzamanlı mühendislik hizmetleri. Hassas çinko dökümlerin özel üreticisi. Minyatür dökümler, yüksek basınçlı dökümler, çok kızaklı kalıp dökümleri, geleneksel kalıp dökümleri, birim kalıp ve bağımsız kalıp dökümleri ve boşluklu sızdırmaz dökümler üretilebilir. Dökümler, +/- 24 inç toleransta 0.0005 inç'e kadar uzunluk ve genişliklerde üretilebilir.
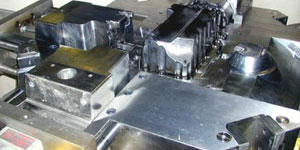
ISO 9001: 2015 sertifikalı döküm magnezyum üreticisi, Yetenekler arasında 200 ton sıcak odaya ve 3000 ton soğuk odaya kadar yüksek basınçlı magnezyum kalıp dökümü, takım tasarımı, cilalama, kalıplama, işleme, toz ve sıvı boyama, CMM özelliklerine sahip tam kalite güvencesi bulunur , montaj, paketleme ve teslimat.
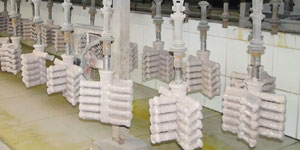
ITAF16949 sertifikalı. Ek Döküm Hizmeti Dahil yatırım dökümleri,kum dökümü,Yerçekimi Döküm, Kayıp Köpük Döküm,Savurma döküm,Vakumlu Döküm,Kalıcı Kalıp Döküm,.Yetenekler arasında EDI, mühendislik yardımı, katı modelleme ve ikincil işleme yer alır.
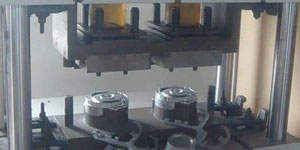
Döküm Endüstrileri Arabalar, Bisikletler, Uçaklar, Müzik aletleri, Deniz Araçları, Optik cihazlar, Sensörler, Modeller, Elektronik cihazlar, Muhafazalar, Saatler, Makineler, Motorlar, Mobilya, Mücevher, Jigler, Telekom, Aydınlatma, Tıbbi cihazlar, Fotoğraf cihazları, Robotlar, Heykeller, Ses ekipmanları, Spor ekipmanları, Aletler, Oyuncaklar ve daha fazlası.
Bundan sonra ne yapmanıza yardımcı olabiliriz?
∇ Ana Sayfaya Git Çin Döküm
→Döküm Parçaları-Ne yaptığımızı öğren.
→ Hakkında İlgili İpuçları Pres Döküm Hizmetleri
By Minghe Döküm Üreticisi |Kategoriler: Faydalı Makaleler |Malzeme Etiketler: Alüminyum Döküm, Çinko Döküm, Magnezyum Döküm, Titanyum Döküm, Paslanmaz Çelik Döküm, Pirinç Döküm,Bronz Döküm,Döküm Videosu,Tarihçe,Alüminyum Döküm |Yorumlar Kapalı