Kum Kaplı Demir Kalıp Döküm Yöntemi ve Uygulaması
Kum Kaplı Demir Kalıp Döküm Nedir?
Demir kalıp kum kaplı döküm, bir kalıp oluşturmak için bir metal kalıbın (demir kalıp olarak adlandırılır) iç boşluğuna ince bir kum tabakasının kaplandığı bir döküm işlemidir. Kum kaplama tabakası nispeten ince (4~8 mm) olduğundan, daha pahalı yüksek kaliteli modelleme malzemelerinin kullanılması ekonomik olarak mantıklıdır. Sonuç olarak, dökümlerin kalitesi büyük ölçüde iyileştirilir ve atık önemli ölçüde azalır; demir kum kaplı döküm kalıbının sertliği sayesinde Çok iyi, dolayısıyla dökümün boyutsal doğruluğunu ve kompaktlığını önemli ölçüde iyileştirir.
Almanya, eski Sovyetler Birliği ve diğer ülkeler, 1960'larda döküm üretiminde, özellikle sfero krank milleri, fren göbekleri, fren diskleri, silindir gömlekleri, bomba kovanları, tank paletleri ve motor üsleri üretimi için demir kum kaplı döküm kullanmaya başladı. , vb. Döküm çeşitleri. Çin'in demir kalıp kum kaplı döküm üzerine uygulama araştırması 1970'lerin başında başladı. 1979'da, Zhejiang Mekanik ve Elektrik Tasarım Enstitüsü ve Yongkang Traktör Fabrikası, S195 krank mili boşluklarının seri döküm üretiminde bu süreci ilk kez kullanmak için işbirliği yaptı. Aynı zamanda, bu işlemle üretilen sfero döküm krank milinin yorulma mukavemeti (yorulma sınırı gerilmesi σ-1 karşılaştırması), kırılma mukavemeti (eşik değer ΔKth ile karşılaştırılması ve kırılma tokluğu K1C karşılaştırması) açısından performans değerlendirmesi tamamlandı. ) ve hizmet ömrü (10000 saatlik tezgahın dayanıklılık testinin karşılaştırılması), vb., kum döküm krank miline kıyasla, kum dökümden daha iyidir. Takip eden 10 yıl içinde süreç uygulamada sürekli olarak iyileştirildi. 1990'ların başında, yedi şirket, özellikle tek silindirli krank milleri ve dört silindirli krank milleri için demir kum kaplı döküm işlemi olmak üzere işlemi uygulamıştı. Büyük bir başarı. Bu dönemdeki temsili işletmeler Yongkang Traktör Fabrikası, Shangyu Güç Makineleri Fabrikası, Wangdu Krank Mili ve Biyel Fabrikası, Wanbei Krank Mili Fabrikası, Jinhua İçten Yanmalı Motor Parçaları Fabrikası, Changzhou Dizel Motor Fabrikası vb.'dir. 1991 yılında, Devlet Planlama Komisyonu demiri onayladı. Ülkenin "Sekizinci Beş Yıllık Planı" nın önemli bir yeni teknoloji tanıtım projesi olarak kalıp kum kaplı döküm ve projenin teknik destek birimi olarak Zhejiang Mekanik ve Elektrik Tasarım Enstitüsü yaptı. Bu, ülkemin demir kalıba kum kaplı döküm teknolojisinde önemli bir gelişmedir. Geliştirme, tanıtımda büyük rol oynamıştır. Enstitümüz tanıtım projesini üstlendikten sonra, takip eden 5 ila 6 yıl içinde, seri üretim için demir kaplı kum dökümünün bir dizi sorunu temel olarak çözüldü.
Esasen:
- ①Uzun süredir devam eden maça atıcıların yeniden takılması ve değiştirilmesi sorununu çözen kum kaplı kalıplama makinesini tasarladı ve sonlandırdı;
- ②Standart demir tipi kum kaplı döküm üretim hattı sonuçlandırıldı ve standart hale getirildi ve orijinal nispeten basit demir tipi kum kaplı döküm üretim hattı geliştirildi ve Şanghay Küresel Demir Fabrikası gibi işletmelerde uygulandı;
- ③Kum kaplı demir döküm uygulaması, altı silindirli krank milleri ve üç silindirli krank milleri gibi daha zor döküm işlemlerine sahip bazı dökümlere genişletildi;
- ④ Kum kaplı kalıplamanın kalitesini büyük ölçüde artıran, demir kaplı kum döküm üretimine kaplanmış kumun dahil edilmesi;
- ⑤Demir kalıp kum kaplı döküm işleminin tasarımı daha da standart hale getirildi ve tasarım seviyesi de büyük ölçüde geliştirildi. Demir kalıba kum kaplı döküm prosesinin bilgisayar simülasyon yazılımı ve demir kalıba kum kaplı döküm prosesinin bilgisayar destekli tasarım yazılımı geliştirilmiştir.
Şu anda, ülke genelinde yaklaşık yüz işletme, sfero döküm krank milleri, eksantrik milleri, balans milleri, basınca dayanıklı valf gövdeleri, silindir gömlekleri ve aşınmaya dayanıklı gibi 30'dan fazla çeşit döküm üretmek için demir kum kaplı döküm işlemi uygulamıştır. dişli diskler. Yıllık çıktının döküm olduğu tahmin edilmektedir. Yaklaşık 10×104t. Tipik şirketler arasında Şanghay Otomobil Dökümhanesi Genel Sfero Demir Fabrikası, Shenyang No. 1 Krank Mili Fabrikası, Guangxi Baikuang Grubu, Yixing Makina Genel Fabrikası, Shandong Jiuyang Grubu, Zhejiang Shuguang Krank Mili Fabrikası, Benxi Tianyuan Krank Mili Fabrikası, Baoding Film Makine Fabrikası, Shanxi Lucheng Krank Fabrikası , Hebei Xinji Krank Fabrikası, vb. Bununla birlikte, bu şirketlerin süreci tanıtmanın farklı yolları vardır: bazıları enstitümüze tasarım veya inşa etme işini emanet etmiş, bazıları ise kendi başlarına taklit etmiş ve geliştirmiştir. Bu nedenle demir kalıba kum kaplı döküm işlemindeki ustalıkları çok farklıdır. Sadece demir kalıp kum kaplı döküm fire oranını örnek alarak daha iyi kavrayan birçok firma bunu yaklaşık %3'te sabitleyebilir ve çok iyi ekonomik faydalar elde etmiştir. Bununla birlikte, demir kalıp kum kaplı döküm atık oranı yaklaşık %20 kadar yüksek olan ve bu işlemin ekonomik faydalarını büyük ölçüde dengeleyen birkaç şirket de vardır. Bunun nedeni, bu firmaların sürecin tasarım ve üretim esaslarını tam olarak kavramamış olmaları ve üretim yönetimini ihmal etmeleridir.
Demir kalıp kum kaplı döküm işleminin tasarımı ve fiili üretimi için ana çözümler:
- ①Demir duvarın kalınlığı ve kum kaplama tabakasının kalınlığı ve ikisinin kombinasyonu, farklı duvar kalınlıklarına ve farklı malzemelere sahip dökümlerin katılaştırılması ve soğutulması için farklı gereksinimleri karşılayabilir;
- ②Yüzey kalitesi ve boyutsal doğruluk için farklı dökümlerin gereksinimlerini karşılamak için uygun ve ekonomik kum kaplama kalıplama yöntemi;
- ③Proses parametreleri. Yolluk sistemi, kum püskürtme sistemi, egzoz sistemi vb. tespiti;
- ④ Seri üretimin gerçekleştirilmesi. Örneğin, üretim hattının ve kum kaplı ana ve yardımcı ekipmanın tasarımı ve şekli;
- ⑤Dökme, soğutma ve ambalajdan çıkarma düzenlemelerinin yanı sıra döküm bileşiminin ayarlanması gibi süreç düzenlemelerinin formülasyonu.
Demir Tipi Kum Kaplı Dökümün Isı Değişim Özellikleri
Demir kum kaplı döküm kalıbına sıvı metal döküldükten sonra “döküm-kum kaplama-demir kalıp” kararsız bir ısı değişim sistemidir. Problemi basitleştirmek için dökümün yarı sınırlı olduğu varsayılır; ve sistemdeki her bir bileşenin sıcaklık alanının düz bir çizgide dağıldığı varsayılır. Şekil 1, sistemin bir bölümünü göstermektedir. Açıktır ki, sistemdeki her bir bileşenden aynı özgül ısı akışı q geçer:
Sırasıyla, döküm ve kum kaplı katman ile demir kalıp ve kum kaplı katman arasındaki ısı değişim yoğunluğunu temsil eden iki ısı transfer kriteri. k1, dökümün termal direncinin kum kaplamanın termal direncine oranıdır; k2, demir tipinin ısıl direncinin kum kaplamanın ısıl direncine oranıdır. k1 ve k2 kombinasyonu göz önüne alındığında, kum kaplamanın kalınlığının değişmesiyle, "döküm-kum kaplama-demir kalıp" arasında gerçekte oluşabilecek aşağıdaki üç farklı ısı transferi durumu vardır:
- ① k≤1 ve k2≤1 olduğunda, kum kaplama tabakası normal kalınlıktadır ve kum kaplama tabakasının kalınlığı azaldıkça dökümün soğuma hızı artar.
- ②Kum kaplı tabakanın kalınlığı belirli bir kalınlığı aştığında, demir kalıbın dökümün soğuması üzerinde hiçbir etkisi yoktur. Şu anda, sıradan kum dökümüne veya reçineli kum dökümüne eşdeğerdir. Kum kaplı tabakanın ısıl iletkenliği demir tipine göre çok daha küçük olduğu için döküm yavaş soğur.
- ③K≧1 ve k2≧1 olduğunda, kum kaplamanın kalınlığı metal kalıp dökümüne eşdeğer olan çok incedir.
Yukarıdaki ısı değişim özellikleri deneylerle doğrulanmıştır. Krank mili (CTЦ-14) demir tipi kum kaplı dökümün kum kaplama tabakasının kalınlığı kademeli olarak 4 ila 32 mm arasında değiştiğinde, krank mili yapısındaki sementit miktarı sürekli olarak azalır ve perlit miktarı ve ferrit miktarı artmaya devam ediyor. Kum kaplı tabakanın kalınlığı 4 mm'den az olduğunda, dökümün soğutma mukavemeti metal tipininkine (kalın boya) benzerdir; kum kaplı tabaka 32 mm'den büyük olduğunda, soğutma mukavemeti sıradan reçine kum dökümüne eşdeğerdir.
Çeşitli dökümlerin üretiminde demir kum kaplı döküm kullanıldığında, dökümün katılaşma oranını kontrol etmek için kum kaplı tabakanın kalınlığını ve demirin kalınlığını belirlemek deneyler veya ampirik benzetme yoluyla yapılır. Örneğin, 490Q sünek demir krank mili demir kalıp kum kaplı döküm işleminin tasarımında, kum kaplama tabakasının kalınlığı 5-8 mm'dir ve demir kalıbın duvar kalınlığı 20-30 mm'dir, bu da yüksek kaliteyi üretir. - kolonsuz dökme sfero döküm. Ana sebep:
- ① Kum kaplı katman, dökümün soğuma hızını etkin bir şekilde düzenler, bir yandan dökümün beyaz görünme olasılığını azaltırken, diğer yandan soğutma hızı kum dökümden daha fazladır. Şekil 2'de gösterildiği gibi, erimiş demir kum kaplı demir kalıba döküldüğünde, 930 dakika sonra dökümün sıcaklığı yaklaşık 8°C'ye düşer ve kum kalıbın aynı sıcaklığa düşmesi 24 dakika sürer. ve soğutma hızı yaklaşık 3 kat artar. Sonuç olarak, dökümlerin mekanik özellikleri önemli ölçüde iyileştirilir.
- ②Demir kalıbın tavizi yoktur, ancak ince kum kaplama kalıbın büzülme direncini uygun şekilde azaltabilir; ve demir kalıbın sertliği, hiçbir yükseltici döküm elde etmek için katılaştırma işlemi sırasında sfero dökümün grafitizasyon genişlemesini etkin bir şekilde kullanır; ince kum kaplama nedeniyle, boşluğun deforme olması kolay değildir ve dökümün hassasiyeti, kum kalıbınınkinden büyük ölçüde geliştirilmiştir.
Sırasıyla, döküm ve kum kaplı katman ile demir kalıp ve kum kaplı katman arasındaki ısı değişim yoğunluğunu temsil eden iki ısı transfer kriteri. k1, dökümün termal direncinin kum kaplamanın termal direncine oranıdır; k2, demir tipinin ısıl direncinin kum kaplamanın ısıl direncine oranıdır. k1 ve k2 kombinasyonu göz önüne alındığında, kum kaplamanın kalınlığının değişmesiyle, "döküm-kum kaplama-demir kalıp" arasında gerçekte oluşabilecek aşağıdaki üç farklı ısı transferi durumu vardır:
- ① k≤1 ve k2≤1 olduğunda, kum kaplama tabakası normal kalınlıktadır ve kum kaplama tabakasının kalınlığı azaldıkça dökümün soğuma hızı artar.
- ②Kum kaplı tabakanın kalınlığı belirli bir kalınlığı aştığında, demir kalıbın dökümün soğuması üzerinde hiçbir etkisi yoktur. Şu anda, sıradan kum dökümüne veya reçineli kum dökümüne eşdeğerdir. Kum kaplı tabakanın ısıl iletkenliği demir tipine göre çok daha küçük olduğu için döküm yavaş soğur.
- ③K≧1 ve k2≧1 olduğunda, kum kaplamanın kalınlığı metal kalıp dökümüne eşdeğer olan çok incedir.
Yukarıdaki ısı değişim özellikleri deneylerle doğrulanmıştır. Krank mili (CTЦ-14) demir tipi kum kaplı dökümün kum kaplama tabakasının kalınlığı kademeli olarak 4 ila 32 mm arasında değiştiğinde, krank mili yapısındaki sementit miktarı sürekli olarak azalır ve perlit miktarı ve ferrit miktarı artmaya devam ediyor. Kum kaplı tabakanın kalınlığı 4 mm'den az olduğunda, dökümün soğutma mukavemeti metal tipininkine (kalın boya) benzerdir; kum kaplı tabaka 32 mm'den büyük olduğunda, soğutma mukavemeti sıradan reçine kum dökümüne eşdeğerdir.
Çeşitli dökümlerin üretiminde demir kum kaplı döküm kullanıldığında, dökümün katılaşma oranını kontrol etmek için kum kaplı tabakanın kalınlığını ve demirin kalınlığını belirlemek deneyler veya ampirik benzetme yoluyla yapılır. Örneğin, 490Q sünek demir krank mili demir kalıp kum kaplı döküm işleminin tasarımında, kum kaplama tabakasının kalınlığı 5-8 mm'dir ve demir kalıbın duvar kalınlığı 20-30 mm'dir, bu da yüksek kaliteyi üretir. - kolonsuz dökme sfero döküm. Ana sebep:
- ① Kum kaplı katman, dökümün soğuma hızını etkin bir şekilde düzenler, bir yandan dökümün beyaz görünme olasılığını azaltırken, diğer yandan soğutma hızı kum dökümden daha fazladır. Şekil 2'de gösterildiği gibi, erimiş demir kum kaplı demir kalıba döküldüğünde, 930 dakika sonra dökümün sıcaklığı yaklaşık 8°C'ye düşer ve kum kalıbın aynı sıcaklığa düşmesi 24 dakika sürer. ve soğutma hızı yaklaşık 3 kat artar. Sonuç olarak, dökümlerin mekanik özellikleri önemli ölçüde iyileştirilir.
- ②Demir kalıbın tavizi yoktur, ancak ince kum kaplama kalıbın büzülme direncini uygun şekilde azaltabilir; ve demir kalıbın sertliği, hiçbir yükseltici döküm elde etmek için katılaştırma işlemi sırasında sfero dökümün grafitizasyon genişlemesini etkin bir şekilde kullanır; ince kum kaplama nedeniyle, boşluğun deforme olması kolay değildir ve dökümün hassasiyeti, kum kalıbınınkinden büyük ölçüde geliştirilmiştir.
Demir Kum Kaplı Dökümlerin Soğuma Hızı
Demir kum kaplı dökümlerin soğuma hızını etkileyen faktörler arasında döküm et kalınlığı, döküm malzemesi, döküm sıcaklığı, kum kaplama kalınlığı, kum kaplama malzemesi, demir kalıp kalınlığı, demir kalıp malzemesi ve kalıp sıcaklığı yer alır. Burada sadece döküm et kalınlığının (bc), kum kaplama kalınlığının (bm) ve demir kalınlığının (bi) etkisi tartışılmıştır.
bc, bm ve bi'nin Döküm Soğutmasına Etkisi
Aşağıdaki deney koşullarında yapılan farklı döküm et kalınlıkları (sırasıyla 10mm, 20mm, 40mm, 80mm), farklı kum kaplama kalınlıkları (sırasıyla 4mm ve 32mm) ve farklı demir tipi duvar kalınlıkları (sırasıyla 32mm ve 8mm) demir tipi kum kaplı dökümlerin soğuma hızı: dökümün kimyasal bileşimi %3.52C, %2.46Si, %0.80Mn, %0.18P, %0.031S'dir ve kum kaplı katmanın kimyasal bileşimi: %90 kuvars kumu, %8 kil, %2 Kömür tozu, %3 nem
- ①Döküm et kalınlığı, kum kaplama kalınlığı ve demir et kalınlığı dökümün soğuma hızını etkiler. Bu nedenle fiili üretimde gerekli soğuma hızını elde etmek için farklı döküm et kalınlıklarına göre uygun demir kalıp kalınlığı ve kum kaplama kalınlığı seçilmelidir.
- ② Aynı soğuma hızını elde etmek için uygun kum kaplama kalınlığı ve demir et kalınlığı seçilerek farklı kalınlıklarda dökümler elde edilebilir. Örneğin, Şekil 3'te bölge I, kalınlığın 10 mm ve 20 mm olduğu anlamına gelir, bölge II, 20 mm ve 40 mm anlamına gelir ve bölge III, 40 mm anlamına gelir. Ve 80 mm dökümlerin soğutma aralığı arasındaki örtüşme.
- ③Farklı kalınlıktaki dökümler için aynı soğuma hızını elde etmek için bm ve bi değiştirilebilse de, tüm döküm kalınlıkları aynı soğuma hızını sağlayamaz. Deneysel koşullar altında, 10 mm kalınlığında ve 40 mm kalınlığında dökümler elde edilemez. Tam olarak aynı soğutma hızı (eğriler arasında örtüşme yoktur).
Kum Kaplama Kalınlığı (bm) ve Demir Et Kalınlığı (bi) Seçimi
Bm ve bi genellikle deneyime veya deneye dayalı olarak belirlenir. 10 ila 80 mm arasında döküm kalınlığı (bc) ve 600℃ ambalaj açma sıcaklığı için uygun bir grafik yöntemi. Ordinat soğuma süresidir. Sağdaki eğrinin apsisi, bilinen dökümün 600°C'ye soğuması için gereken süreden ve çeşitli dökümlerin kalınlığından ve gerekli döküm et kalınlığında belirlenebilen kum kaplamanın kalınlığı ile işaretlenmiştir. (10, 20 , 40, 80mm) biliniyorsa, kum kaplamanın kalınlığını ve demir kalıbın kalınlığını belirlemek çok uygundur. Eğrinin sol yarısının yatay ekseninden karşılık gelen bc'yi (örneğin bc=20mm) bulun ve yatay bir çizgi çizin.
İki çizgi çapraz çizgili eğri aralığında kesişiyorsa, bu dökümün demir kum kaplama Döküm için uygun olduğunu gösterir. Bu yatay çizgiyi sağa doğru uzatın, bc=20mm alana kadar uzanacak ve gerekli kum kaplama kalınlığını elde etmek için bu alana dikey bir çizgi çekecektir. Ancak kum kaplamanın en küçük kalınlığını ve demir kalıbın kalınlığını elde etmek için bu dikey çizgi mümkün olduğunca sağa çekilmelidir. Tespit edilmesi gereken kum-kaplama tabakasının kalınlığı bu aralıkta değilse, komşu eğri aralığından da benzer şekilde bulabilirsiniz.
- ①Döküm et kalınlığı, kum kaplama kalınlığı ve demir et kalınlığı dökümün soğuma hızını etkiler. Bu nedenle fiili üretimde gerekli soğuma hızını elde etmek için farklı döküm et kalınlıklarına göre uygun demir kalıp kalınlığı ve kum kaplama kalınlığı seçilmelidir.
- ② Aynı soğuma hızını elde etmek için uygun kum kaplama kalınlığı ve demir et kalınlığı seçilerek farklı kalınlıklarda dökümler elde edilebilir. Örneğin, Şekil 3'te bölge I, kalınlığın 10 mm ve 20 mm olduğu anlamına gelir, bölge II, 20 mm ve 40 mm anlamına gelir ve bölge III, 40 mm anlamına gelir. Ve 80 mm dökümlerin soğutma aralığı arasındaki örtüşme.
- ③Farklı kalınlıktaki dökümler için aynı soğuma hızını elde etmek için bm ve bi değiştirilebilse de, tüm döküm kalınlıkları aynı soğuma hızını sağlayamaz. Deneysel koşullar altında, 10 mm kalınlığında ve 40 mm kalınlığında dökümler elde edilemez. Tam olarak aynı soğutma hızı (eğriler arasında örtüşme yoktur).
Lütfen yeniden basım için bu makalenin kaynağını ve adresini saklayın: Kum Kaplı Demir Kalıp Döküm Yöntemi ve Uygulaması
Minhe Basınçlı Döküm Şirketi kaliteli ve yüksek performanslı Döküm Parçaları üretmeye ve sağlamaya adamıştır (metal döküm parça yelpazesi esas olarak şunları içerir: İnce Duvarlı Döküm,Sıcak Kamara Basınçlı Döküm,Soğuk Oda Döküm), Yuvarlak Servis (Döküm Servisi,Cnc İşleme,Kalıp yapımı,Yüzey İşleme).Herhangi bir özel Alüminyum döküm, magnezyum veya Zamak/çinko döküm ve diğer döküm gereksinimleri bizimle iletişime geçebilirsiniz.
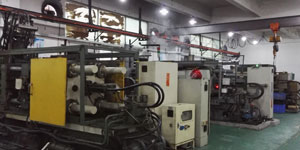
ISO9001 ve TS 16949 kontrolünde, tüm işlemler yüzlerce gelişmiş basınçlı döküm makinesi, 5 eksenli makine ve blasterlerden Ultra Sonic yıkama makinelerine kadar diğer tesisler aracılığıyla gerçekleştirilir. Müşterinin tasarımını gerçeğe dönüştürmek için deneyimli mühendisler, operatörler ve müfettişlerden oluşan ekip.
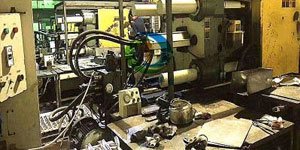
Dökümlerin sözleşmeli üreticisi. Yetenekler, 0.15 lbs'den başlayan soğuk oda alüminyum döküm parçaları içerir. 6 lbs'ye kadar, hızlı değişim kurulumu ve işleme. Katma değerli hizmetler arasında polisaj, titreşim, çapak alma, kumlama, boyama, kaplama, kaplama, montaj ve kalıplama yer alır. Çalışılan malzemeler arasında 360, 380, 383 ve 413 gibi alaşımlar bulunur.
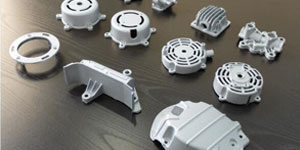
Çinko pres döküm tasarım yardımı/eşzamanlı mühendislik hizmetleri. Hassas çinko dökümlerin özel üreticisi. Minyatür dökümler, yüksek basınçlı dökümler, çok kızaklı kalıp dökümleri, geleneksel kalıp dökümleri, birim kalıp ve bağımsız kalıp dökümleri ve boşluklu sızdırmaz dökümler üretilebilir. Dökümler, +/- 24 inç toleransta 0.0005 inç'e kadar uzunluk ve genişliklerde üretilebilir.
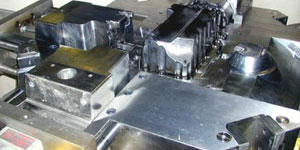
ISO 9001: 2015 sertifikalı döküm magnezyum üreticisi, Yetenekler arasında 200 ton sıcak odaya ve 3000 ton soğuk odaya kadar yüksek basınçlı magnezyum kalıp dökümü, takım tasarımı, cilalama, kalıplama, işleme, toz ve sıvı boyama, CMM özelliklerine sahip tam kalite güvencesi bulunur , montaj, paketleme ve teslimat.
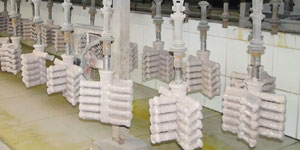
ITAF16949 sertifikalı. Ek Döküm Hizmeti Dahil yatırım dökümleri,kum dökümü,Yerçekimi Döküm, Kayıp Köpük Döküm,Savurma döküm,Vakumlu Döküm,Kalıcı Kalıp Döküm,.Yetenekler arasında EDI, mühendislik yardımı, katı modelleme ve ikincil işleme yer alır.
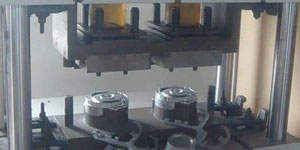
Döküm Endüstrileri Arabalar, Bisikletler, Uçaklar, Müzik aletleri, Deniz Araçları, Optik cihazlar, Sensörler, Modeller, Elektronik cihazlar, Muhafazalar, Saatler, Makineler, Motorlar, Mobilya, Mücevher, Jigler, Telekom, Aydınlatma, Tıbbi cihazlar, Fotoğraf cihazları, Robotlar, Heykeller, Ses ekipmanları, Spor ekipmanları, Aletler, Oyuncaklar ve daha fazlası.
Bundan sonra ne yapmanıza yardımcı olabiliriz?
∇ Ana Sayfaya Git Çin Döküm
→Döküm Parçaları-Ne yaptığımızı öğren.
→ Hakkında İlgili İpuçları Pres Döküm Hizmetleri
By Minghe Döküm Üreticisi |Kategoriler: Faydalı Makaleler |Malzeme Etiketler: Alüminyum Döküm, Çinko Döküm, Magnezyum Döküm, Titanyum Döküm, Paslanmaz Çelik Döküm, Pirinç Döküm,Bronz Döküm,Döküm Videosu,Tarihçe,Alüminyum Döküm |Yorumlar Kapalı