Dövme Kalıbının Bozulma Mekanizması
Kalıp dövme şu anda en gelişmiş dövme teknolojisidir ve esas olarak kalıpların temel bileşenlerinin seri üretimi için kullanılır. En büyük dezavantaj, şekillendirme araçlarının zayıf dayanıklılığıdır. diecastingcompany.com editörüne göre, araçların maliyeti, ürünlerin toplam maliyetinin %8-15'i kadardır. Aslında, aşınmış takımların değiştirilmesi için gereken süreyi ve kazara arızalardan kaynaklanan kayıpları göz önünde bulundurursanız, maliyet %30 ila %50 kadar yüksek olabilir. Ayrıca, takımın aşınması dövmenin kalitesinde önemli bir bozulmaya neden olacaktır. Takım aşınmasının neden olduğu en yaygın kusurlar kavite doldurma hataları, yani katlanma, çapak, deformasyon, çizik, delaminasyon ve mikro ve makro çatlaklardır.
Bu kusurlar nihayetinde sahte ürünlerin performansını etkileyecektir. Piyasadaki güçlü rekabet nedeniyle, kalıp dövme ürünleri üreticileri, dövme kalitesini artırırken maliyetlerini düşürmeye devam ediyor. Buna rağmen, zayıf takım dayanıklılığı sorunuyla hala çok ilgileniyorlar.
Bir aletin dayanıklılığı genellikle birkaç şekilde tanımlanır. Üretim açısından, bir aletin dayanıklılığı, dövme sayısı, yani bu aletle elde edilebilecek beklenen kalitede ürün sayısı ile ifade edilir. Bu tanıma göre takımların ortalama dayanıklılıkları 2,000 ile 20,000 adet arasında değişebilmektedir. Aletler açısından dayanıklılık, bozulma ile ilişkilidir, bu nedenle bozulma fenomenine dayanma yeteneği olarak tanımlanır. Bu makale esas olarak ikinci tanımı kullanır. Dövme takımlarının kullanım sırasında çeşitli bozucu faktörlerden etkilendiği ve bu faktörlerin etkileşiminin problemin analizini zorlaştırdığı söylenmelidir. Bu konudaki literatürde, bozulma fenomeninin çeşitli açıklamaları bulunabilir.
Birçok bilim insanının istatistiklerine göre, dövme kalıplarının hizmetten çekilmesinin ana nedeni, aşınma boyutlarındaki değişikliklerden kaynaklanmaktadır. Aşınma nedeniyle kalıp hurdası yaklaşık %70, plastik deformasyon yaklaşık %25 ve yorulma çatlaması ve diğer nedenler yalnızca %5 civarındadır. Çoğu zaman aynı anda birçok olay meydana gelir ve bunların etkileşimi kalıbın tasarımına, dövme ve imalat koşullarına, kalıp malzemesinin ısıl işlemine ve ön kalıbın ve ek parçanın şekline bağlıdır.
Dövme kalıplarının çalışma koşulları: Sıcak kalıpla dövme işleminde, aletler esas olarak üç yönden bozulmaya maruz kalır: yoğun termal şok, periyodik mekanik yük değişiklikleri ve yüksek sıcaklık ve yüksek basınç. Sıcak dövme sırasında çelik ürünlerin akma gerilimini azaltmak için deforme olan metal 10,000-2,000 santigrat dereceye kadar ısıtılır. Malzeme deformasyonu anında, takım yüzeyinin sıcaklığı 800 santigrat dereceye ulaşabilir, ardından yoğun soğutma gelebilir ve bu nedenle takım büyük bir sıcaklık gradyanına maruz kalacaktır. Kalıbın kesitinde, kalıp yüzey sıcaklığı ve yüzeye yakın sıcaklık birkaç yüz santigrat derece farklılık gösterebilir. Sıcak kalıp dövme sıcaklığı, sıcak dövme sıcaklığından daha düşüktür, yani çelik deformasyon sıcaklığı yaklaşık 900 santigrat dereceye ulaşır. Bu, takım yüzeyinin döngüsel olarak ısıtılması ve soğutulması tarafından üretilen yükün, sıcak dövme kadar büyük olmadığı anlamına gelir. Yine de yarı sıcak dövme işleminde kullanılan takımların ömrü hala oldukça kısadır. Bu, esas olarak döngüsel sıcaklığın ve daha büyük mekanik yükün birleşik etkisinden kaynaklanmaktadır. Mekanik yük esas olarak soğutma ve daha sert malzemelerden gelir.
Dövme aletlerinin dejenerasyon mekanizması
Dövme aletlerinin hizmet ömrü esas olarak onların tasarımına, hazırlanmasına, alet malzemelerinin ısıl işlemine, dövme koşullarına, ön kalıpların ve maça bloklarının şekline vb. bağlıdır. Bu konuda literatürde bozulma hakkında birçok bilgi bulabiliriz. Bu mekanizmalar farklı kategorilere ayrılmıştır. Araştırma sonuçları, dövme aletlerinin yüzeyinde esas olarak aşağıdaki aşınma mekanizmalarının meydana geldiğini göstermektedir: aşındırıcı aşınma, termomekanik yorulma, plastik deformasyon, yorulma çatlaması, yapışkan aşınma ve oksidasyon. Takımın çalışma girintisinin şekli, özel bozulma mekanizmasının oluşma oranını belirleyen temas süresini, basıncı, sürtünme yolunu ve sıcaklık değişikliklerini belirler.
Düz alanda, alet ile termal malzeme arasındaki temas süresi en uzundur ve aynı zamanda maksimum basıncın oluştuğu yerdir. Termomekanik yorulma, ana bozunma mekanizmasıdır.
Yuvarlamanın iç yarıçapı, esas olarak deformasyon dövme işlemi sırasında yoğunlaşma eğiliminde olduğunda ortaya çıkan dış yükün artmasının neden olduğu döngüsel çekme yükünden etkilenir. Sonuç olarak, yorulma mikro çatlakları, aletin servisi sırasında büyük çatlaklara dönüşür ve bu yerlerde ortaya çıkar. Kalıp göçüğünün dış yarıçapı ve yüksek sıcaklık koşullarında malzemenin zayıflaması nedeniyle kalıp baskısının flaş köprüsüne girdiği yer, malzemenin akma noktası o kadar düşük, bu da plastik deformasyona yol açar. Deforme olmuş malzemelerin yoğun akışı, bu alanlarda, yüksek sıcaklıkta oksidasyon işlemi sırasında aletin dövme malzemesinin yüzeyinde oluşan sert oksitler tarafından daha da kötüleşen abrasif aşınmaya neden olur.
Dövme kalıplarının bozunma mekanizmasının yapışkan aşınması
Özellikle yüzeyin düzensiz olduğu yüzey tabakasının plastik deformasyon alanında adeziv aşınma meydana gelir. Genellikle benzer malzeme etkileşimleri veya kimyasal afinite gösteren malzemeler (tipik dövme işleme koşulları) nedeniyle yüksek basınç ve nispeten düşük hız koşulları altında oluşur. Daha yüksek basınç koşulları altında, malzeme kalıplama aletin yüzeyi boyunca kayar, oksit kaplamayı kaldırarak aletin taze yüzeyini açıkta bırakır. Bu esas olarak yüzey çıkıntısının düzensiz alanında (pürüzlü yüzeyin tepe kısmı) meydana gelir.
Bu yerlerdeki malzemeler atomlar arası kuvvetlerin çalışmaya başlaması için birbirine yakın yerleştirildiğinde yerel metal bağları oluşur. Daha sonra yüzeyler birbirine daha fazla kayarken metal bağı yok edildi. Bu işlemde yüzey tabakasının plastik deformasyonu oluşur. Metal bağının kopması, yüzeye yapışma eğiliminde olan metal parçacıkların soyulmasına yol açar.
Dövme kalıplarının bozunma mekanizmasının aşındırıcı aşınması
Malzeme kaybı genellikle aşındırıcı aşınmaya bağlanır. Soyulmuş parçacıkların boyutu esas olarak dövme katsayısına ve takım yüzey tabakasının özelliklerine bağlıdır. Yapışkan aşınmanın bir örneği, şekilde gösterildiği gibi CV evrensel mafsal muhafazasının dövme işleminin ikinci aşamasıdır. Bu işlemde malzemenin deforme olduğu sıcaklık yaklaşık 900°C'dir, yani genellikle bu tür aşınmaya meyilli olan geleneksel sıcak dövme işleminden çok daha düşüktür. Yapıştırıcı aşınması, malzemenin kendisine veya kesit alanının azaldığı alete yapışacaktır.
Abrazif aşınma, malzeme kaybının bir sonucudur ve esas olarak malzemenin yüzeyden ayrılmasıyla elde edilir. Aşındırıcı aşınma, gevşek veya sabit aşındırıcı parçacıklar olduğunda veya etkileşim yüzeyinde düzensiz çıkıntı bölümleri olduğunda meydana gelir. Dövme aleti için sertliği, deforme olmuş malzemeden çok daha yüksektir. Bu durumda, dövme aleti ile deforme olmuş malzeme arasındaki temas kısmında aşındırıcı parçacıklar görülürse, abrazif aşınma meydana gelecektir. Aşındırıcı aşınma, dövme parçasından ayrılan küçük parçacıkların yüzeyinde ve yüksek sıcaklık koşullarında kalıp ve kalıp yüzeyinde oluşan sert oksit parçacıklarının ortaya çıkmasıyla daha da kötüleşecektir. Bu mekanizma sayesinde, malzemenin deformasyonunun değiştiği yön boyunca oluklar oluşturulur.
Şekilleri ve derinlikleri esas olarak dövme koşullarına bağlıdır. Çıkıntı yapan kısım özellikle aşınmaya karşı hassastır ve daha sonraki servisi sırasında aletin yüzeyinden hızla çıkar, bu da malzeme kaybına ve malzeme geometrisinde değişikliklere yol açar. Abrasiv aşınma oluşturması özellikle kolay ve ayrıca abrasiv aşınmaya karşı özellikle hassas, malzemenin deformasyonu sırasında en uzun kaymanın meydana geldiği yerdir. En yaygın olanı, kalıbın flaş köprüsüne girdiği kalıp boşluğunun dış yarıçapıdır.
Lütfen yeniden basım için bu makalenin kaynağını ve adresini saklayın: Dövme Kalıbının Bozulma Mekanizması
Minhe Basınçlı Döküm Şirketi kaliteli ve yüksek performanslı Döküm Parçaları üretmeye ve sağlamaya adamıştır (metal döküm parça yelpazesi esas olarak şunları içerir: İnce Duvarlı Döküm,Sıcak Kamara Basınçlı Döküm,Soğuk Oda Döküm), Yuvarlak Servis (Döküm Servisi,Cnc İşleme,Kalıp yapımı,Yüzey İşleme).Herhangi bir özel Alüminyum döküm, magnezyum veya Zamak/çinko döküm ve diğer döküm gereksinimleri bizimle iletişime geçebilirsiniz.
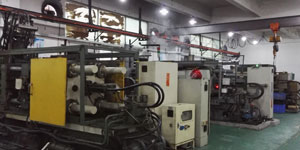
ISO9001 ve TS 16949 kontrolünde, tüm işlemler yüzlerce gelişmiş basınçlı döküm makinesi, 5 eksenli makine ve blasterlerden Ultra Sonic yıkama makinelerine kadar diğer tesisler aracılığıyla gerçekleştirilir. Müşterinin tasarımını gerçeğe dönüştürmek için deneyimli mühendisler, operatörler ve müfettişlerden oluşan ekip.
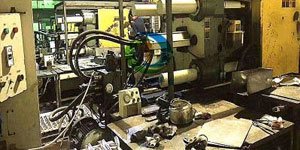
Dökümlerin sözleşmeli üreticisi. Yetenekler, 0.15 lbs'den başlayan soğuk oda alüminyum döküm parçaları içerir. 6 lbs'ye kadar, hızlı değişim kurulumu ve işleme. Katma değerli hizmetler arasında polisaj, titreşim, çapak alma, kumlama, boyama, kaplama, kaplama, montaj ve kalıplama yer alır. Çalışılan malzemeler arasında 360, 380, 383 ve 413 gibi alaşımlar bulunur.
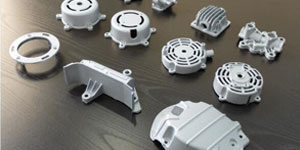
Çinko pres döküm tasarım yardımı/eşzamanlı mühendislik hizmetleri. Hassas çinko dökümlerin özel üreticisi. Minyatür dökümler, yüksek basınçlı dökümler, çok kızaklı kalıp dökümleri, geleneksel kalıp dökümleri, birim kalıp ve bağımsız kalıp dökümleri ve boşluklu sızdırmaz dökümler üretilebilir. Dökümler, +/- 24 inç toleransta 0.0005 inç'e kadar uzunluk ve genişliklerde üretilebilir.
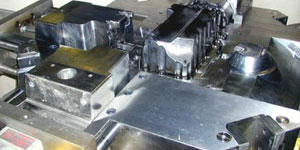
ISO 9001: 2015 sertifikalı döküm magnezyum üreticisi, Yetenekler arasında 200 ton sıcak odaya ve 3000 ton soğuk odaya kadar yüksek basınçlı magnezyum kalıp dökümü, takım tasarımı, cilalama, kalıplama, işleme, toz ve sıvı boyama, CMM özelliklerine sahip tam kalite güvencesi bulunur , montaj, paketleme ve teslimat.
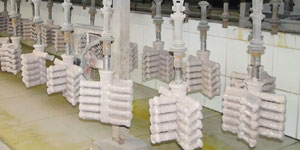
ITAF16949 sertifikalı. Ek Döküm Hizmeti Dahil yatırım dökümleri,kum dökümü,Yerçekimi Döküm, Kayıp Köpük Döküm,Savurma döküm,Vakumlu Döküm,Kalıcı Kalıp Döküm,.Yetenekler arasında EDI, mühendislik yardımı, katı modelleme ve ikincil işleme yer alır.
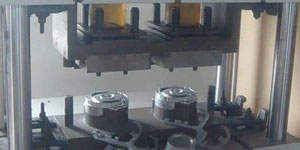
Döküm Endüstrileri Arabalar, Bisikletler, Uçaklar, Müzik aletleri, Deniz Araçları, Optik cihazlar, Sensörler, Modeller, Elektronik cihazlar, Muhafazalar, Saatler, Makineler, Motorlar, Mobilya, Mücevher, Jigler, Telekom, Aydınlatma, Tıbbi cihazlar, Fotoğraf cihazları, Robotlar, Heykeller, Ses ekipmanları, Spor ekipmanları, Aletler, Oyuncaklar ve daha fazlası.
Bundan sonra ne yapmanıza yardımcı olabiliriz?
∇ Ana Sayfaya Git Çin Döküm
→Döküm Parçaları-Ne yaptığımızı öğren.
→ Hakkında İlgili İpuçları Pres Döküm Hizmetleri
By Minghe Döküm Üreticisi |Kategoriler: Faydalı Makaleler |Malzeme Etiketler: Alüminyum Döküm, Çinko Döküm, Magnezyum Döküm, Titanyum Döküm, Paslanmaz Çelik Döküm, Pirinç Döküm,Bronz Döküm,Döküm Videosu,Tarihçe,Alüminyum Döküm |Yorumlar Kapalı