Tarihteki en eksiksiz kalıp kabul standardı!
1. Kalıplanmış ürünün görünümü, boyutu ve uyumu
1. Ürün yüzeyindeki kusurlara izin verilmez: malzeme eksikliği, yanık, üst beyaz, beyaz çizgi, tepe noktası, kabarma, beyazlaşma (veya çatlama, kırılma), pişirme ve kırışıklıklar. .
2. Kaynak işareti: Genel olarak, dairesel delikli kaynak işaretinin uzunluğu 5 mm'den fazla değildir ve özel şekilli delikli kaynak işaretinin uzunluğu 15 mm'den azdır ve kaynak işaretinin gücü, fonksiyonel güvenlik testini geçebilir. .
3. Büzülme: Görünüşün belirgin bölgelerinde büzülmeye izin verilmez ve belirgin olmayan alanlarda (çentik hissetmeyen) hafif büzülmeye izin verilir. .
4. Genellikle, küçük ürünlerin düzlüğü 0.3 mm'den azdır. Montaj gereksinimleri varsa, montaj gereksinimleri garanti edilmelidir.
5. Belirgin görünümde hava hatları veya malzeme çiçekleri olmamalıdır ve üründe genellikle hava kabarcıkları olmamalıdır.
6. Ürünün geometrik şekli ve boyutsal doğruluğu, resmi ve etkili kalıp çiziminin (veya 3D dosyasının) gereksinimlerini karşılamalıdır. Ürün toleransı, tolerans ilkesine dayanmalıdır. Şaft boyutu toleransı negatif bir toleranstır ve delik boyutu toleransı pozitif bir toleranstır. Müşterinin gerektiği gibi, gerektiği gibi vardır.
7. Ürün et kalınlığı: Ürün et kalınlığının genellikle ortalama et kalınlığı olması, ortalama olmayan et kalınlığının çizim gereksinimlerini karşılaması ve kalıbın özelliklerine göre tolerans -0.1mm olması gerekir.
8. Ürün koordinasyonu: yüzey kabuğu ve alt kabuk koordinasyonu: yüzey hizasızlığı 0.1 mm'den azdır ve çizilme olmamalıdır. Eşleştirme gereksinimlerine sahip delikler, şaftlar ve yüzeyler, eşleştirme aralığını ve kullanım gereksinimlerini sağlamalıdır.
İkincisi, kalıbın görünümü
1. Kalıp isim plakasının içeriği tamamlandı, karakterler açık ve aranjman düzgün.
2. İsim plakası, şablonun ve referans açısının yanında kalıp ayağına sabitlenmelidir. İsim plakası güvenilirdir ve soyulması kolay değildir.
3. Soğutma suyu nozulu plastik blok su nozülünden yapılmalıdır, müşteri aksini gerektiriyorsa, lütfen gereksinimleri takip edin. 4. Soğutma suyu nozulu, kalıp tabanının yüzeyinden dışarı çıkmamalıdır.
5. Soğutma suyu nozulunun havşa ile işlenmesi gerekir. Havşa çapı 25 mm, 30 mm ve 35 mm'dir. Delik pahlıdır ve pah aynı olmalıdır. .
6. Soğutma suyu nozulu giriş ve çıkış için işaretlenmelidir.
7. İşaretleme İngilizce karakterler ve sayılar 5/6'dan büyük olmalı ve konum, musluğun doğrudan 10 mm altında olmalıdır. El yazısı açık, güzel, düzgün ve eşit aralıklı olmalıdır.
8. Kalıp aksesuarları, kalıpların kaldırılmasını ve depolanmasını etkilememelidir. Kurulum sırasında, destek ayakları ile korunması gereken açıkta kalan yağ silindirleri, musluklar, ön sıfırlama mekanizması vb.
9. Destek ayağının montajı, destek ayağının içinden geçen vidalarla kalıp tabanına sabitlenmelidir ve aşırı uzun destek ayağı, işlenmiş bir dış dişli kolon ile kalıp tabanına sabitlenebilir.
10. Kalıbın ejektör deliğinin boyutu, belirtilen enjeksiyon kalıplama makinesinin gereksinimlerini karşılamalıdır. Küçük kalıplar dışında tek merkez çıkarma için kullanılamaz.
11. Konumlandırma halkası sabit ve güvenilir olmalıdır. Yüzüğün çapı 100 mm ve 250 mm'dir. Konumlandırma halkası, alt plakadan 10-20 mm daha yüksektir. Müşteriler tarafından aksi talep edilmediği sürece.
12. Kalıbın dış boyutları, belirlenen enjeksiyon kalıplama makinesinin gereksinimlerini karşılamalıdır.
13. Yönlendirme gereksinimi olan kalıplar için, ön şablon veya arka şablon üzerinde montaj yönünü belirtmek için bir ok kullanılmalıdır. Okun yanında "YUKARI" olmalıdır. Ok ve metin sarıdır ve yazı tipinin yüksekliği 50 mm'dir.
14. Kalıp tabanı yüzeyinde çukurlar, pas izleri, fazla halkalar, içeri ve dışarı su buharı, yağ delikleri vb. görünümü etkileyen kusurlar olmamalıdır.
15. Kalıbın kaldırılması ve taşınması kolay olmalı ve kaldırma sırasında kalıbın parçaları sökülmemeli ve kaldırma halkası su nozülü, yağ silindiri, ön sıfırlama çubuğu vb. ile etkileşime girmemelidir.
3. Kalıp malzemesi ve sertlik
1. Kalıp tabanı, standarda uygun standart bir kalıp tabanı olmalıdır.
2. Kalıp oluşturan parçalar ve yolluk sistemi (çekirdek, hareketli ve sabit kalıp ekleri, hareketli ekler, ayrık koniler, itme çubukları, yolluk manşonları) 40Cr'den daha yüksek performansa sahip malzemelerden yapılmıştır.
3. Kalıp için aşındırıcı olan plastikleri kalıplarken, kalıplanan parçalar korozyona dayanıklı malzemelerden yapılmalı veya kalıplama yüzeyi korozyon önleyici önlemler almalıdır.
4. Kalıplanmış parçaların sertliği 50HRC'den düşük olmamalı veya yüzey sertleştirme işleminin sertliği 600HV'den yüksek olmalıdır.
Dört, çıkar, sıfırla, halkayı çıkar, çıkar
1. Fırlatma, sıkışma olmadan ve anormal ses olmadan düzgün olmalıdır.
2. Eğimli üst yüzey cilalanmalıdır ve eğimli üst yüzey çekirdek yüzeyinden daha düşüktür.
3. Kayar parçalarda bir yağ oluğu bulunmalı ve yüzey nitrürlenmeli ve işlemden sonra yüzey sertliği HV700 veya daha yüksek olmalıdır.
4. Tüm ejektör çubukları stop-rotasyon konumlandırmasına sahip olmalı ve her ejektör çubuğu numaralandırılmalıdır.
5. Fırlatma mesafesi bir limit bloğu ile sınırlandırılmalıdır.
6. Dönüş yayı için standart parçalar kullanılmalı, yayın her iki ucu cilalanmamalı veya kesilmemelidir.
7. Kaydırıcı ve çekirdek çekme vuruş sınırına sahip olmalıdır, küçük kızak yay ile sınırlıdır, eğer yay kurulumu uygun değilse, oluklu vida kullanılabilir; silindir göbek-çekme bir strok anahtarına sahip olmalıdır.
8. Genel olarak, kaydırıcının çekirdek çekmesi için eğimli kılavuz direkler kullanılır ve eğimli kılavuz direk açısı, kaydırıcının kilitleme yüzeyinin açısından 2°~3° daha küçük olmalıdır. Kaydırıcının stroku çok uzunsa, çizim için yağ silindiri kullanılmalıdır.
9. Silindirin çekirdek çekme oluşturan parçasının uç yüzeyi kaplandığında, silindir kendi kendine kilitlenen bir mekanizma ile donatılmalıdır.
10. Genişliği 150 mm'yi geçen büyük kızakların altında aşınmaya dayanıklı plakalar bulunmalıdır. Aşınmaya dayanıklı plaka malzemesi T8A olmalıdır. Isıl işlemden sonraki sertlik HRC50-55'tir. Aşınmaya dayanıklı plaka, geniş yüzeyden 0.05-0.1 mm daha yüksektir. Yağ deposunu açın.
11. İtici çubuk yukarı aşağı hareket etmemelidir.
12. Üst çubuğa dikenler ekleyin ve dikenlerin üründen kolayca çıkarılabilmesi için dikenlerin yönü tutarlı olmalıdır.
13. İtici pim deliği ile ejektör pimi arasındaki boşluk, sızdırmazlık bölümünün uzunluğu ve ejektör pimi deliğinin yüzey pürüzlülüğü, ilgili işletme standartlarının gerekliliklerine uygun olmalıdır.
14. Ürün, operatörün çıkarması için uygun olmalıdır.
15. Ürün çıkarıldığında, eğimli üst kısmı takip etmek kolaydır ve üst çubuk yivli veya kazınmış olmalıdır.
16. Üst çubuğa sabitlenen üst blok sağlam ve güvenilir olmalı, çevresi etrafındaki şekilsiz kısım 3°~5° eğimle işlenmeli ve alt çevre pahlı olmalıdır.
17. Kalıp tabanındaki yağ geçiş deliğinde demir talaşı olmamalıdır.
18. Dönüş çubuğunun uç yüzü düzdür ve punta kaynağı yoktur. Embriyo kafasının altında conta yok, punta kaynağı.
19. Üç plakalı kalıbın kapı plakası düzgün bir şekilde kayar ve kapı plakasının açılması kolaydır.
20. Kalıbın montaj yönünün her iki tarafına üç plakalı kalıp limit çubukları düzenlenmeli veya limit çubukların operatöre müdahale etmesini önlemek için kalıp tabanına çekme plakaları eklenmelidir.
21. Yağ devresi ve hava geçişi düzgün olmalı ve hidrolik ejektör sıfırlaması yerinde olmalıdır.
22. Kılavuz manşonun alt kısmında bir egzoz portu açılmalıdır.
23. Konumlandırma pimi montajı için boşluk olmamalıdır.
5. Soğutma ve ısıtma sistemi
1, Soğutma veya ısıtma sistemi tamamen engellenmemiş olmalıdır.
2. Conta güvenilir olmalı, sistem 0.5 MPa basınç altında sızdırmamalı ve kontrol edilmesi ve onarılması kolay olmalıdır.
3. Kalıp tabanında açılan sızdırmazlık oluğunun boyutu ve şekli ilgili standartların gereksinimlerini karşılamalıdır.
4. Sızdırmazlık halkası yerleştirildiğinde gres sürülmeli ve yerleştirildikten sonra kalıp tabanının yüzeyinden daha yüksek olmalıdır.
5. Su ve yağ akış kanalı ayırıcıları kolay korozyona uğramayan malzemelerden yapılmalıdır.
6. Ön ve arka kalıplarda merkezi su kaynağı kullanılmalıdır.
Altı, dökme sistemi
1, Kapı ayarı ürünün görünümünü etkilememeli ve ürün montajını karşılamamalıdır.
2. Yolluk bölümü ve uzunluğu makul bir şekilde tasarlanmalı ve şekillendirme kalitesinin sağlanması öncülüğünde süreç mümkün olduğunca kısaltılmalı ve doldurma ve soğutma süresini kısaltmak için kesit alanı azaltılmalıdır. Aynı zamanda, dökme sisteminin plastik kaybı en az olmalıdır.
3. Üç plakalı kalıp yolluklarının ön kalıbın arkasındaki kısmı yamuk veya yarım daire şeklinde olmalıdır.
4. Üç plakalı kalıbın kapı plakası üzerinde bir malzeme kırıcısı vardır, kapı girişinin çapı 3 mm'den az olmalıdır ve bilye kafası kapı plakasına 3 mm derinliğinde girintili bir adıma sahiptir.
5. Bilye uçlu çekme çubuğu güvenilir bir şekilde sabitlenmelidir, konumlandırma halkasının altına bastırılabilir, başsız vidalarla sabitlenebilir veya bir baskı plakası ile bastırılabilir.
6. Kapılar ve yolluklar, çizimlerin boyut gereksinimlerine göre işlenmelidir ve manuel taşlama ve cilalama makinelerine izin verilmez.
7. Nokta kapısı, şartnamenin gereklerine uygun olmalıdır.
8. Koşucunun ön ucunda soğuk slug deliği olarak bir uzantı olmalıdır.
9. Çekme çubuğunun Z şeklindeki ters çevrilmiş tokası yumuşak bir geçişe sahip olmalıdır.
10. Ayırma yüzeyindeki yolluk yuvarlak olmalı, ön ve arka kalıplar yanlış hizalanmamalıdır.
11. Ejektör çubuğundaki gizli geçitte yüzey büzülmesi olmamalıdır.
12. Şeffaf ürünler için soğuk slug deliğinin çapı ve derinliği tasarım standartlarını karşılamalıdır.
13. Sapın çıkarılması kolaydır, ürünün görünümünde kapı izi yoktur ve ürün montajında artık sap yoktur.
14. Kavisli kanca gizli kapısı için, ek parçanın iki parçası nitrürlenmeli ve yüzey sertliği HV700'e ulaşabilir.
Yedi, sıcak yolluk sistemi
1. Sıcak yollukların kablolama düzeni, kolay bakım için makul olmalı ve kablolama numarası bire bir yazışma olmalıdır.
2. Sıcak yolluk güvenlik açısından test edilmelidir ve zemine karşı yalıtım direnci 2MW'den büyük olmalıdır.
3. Sıcaklık kontrol kabini, sıcak meme ve sıcak yolluk için standart parçalar kabul edilmelidir.
4. Ana akış bağlantı noktası kovanı, dişlerle sıcak yolluk ile bağlantılıdır ve alt yüzey, sızdırmazlık için sıcak yolluk ile temas halindedir.
5. Sıcak yolluk, ısıtma plakası veya ısıtma çubuğu ile iyi temas halindedir ve ısıtma plakası vidalar veya saplamalarla sabitlenmiştir ve yüzey iyi oturur.
6. J tipi termokupl kullanılmalı ve sıcaklık kontrol ölçer ile eşleştirilmelidir.
7. Her bir ısıtma elemanı grubu, termokupllar tarafından kontrol edilmeli ve termokuplların konumu makul bir şekilde düzenlenmelidir.
8. Nozul, tasarım gereksinimlerini karşılamalıdır.
9. Sıcak yolluk, en az iki konumlandırma pimi ile güvenilir şekilde konumlandırılmalı veya vidalarla sabitlenmelidir.
10. Sıcak yolluk ile şablon arasında yalıtım pedi olmalıdır.
11. Sıcaklık kontrol ölçerin ayarlanan sıcaklığı ile gerçek ekran sıcaklığı arasındaki hata ±5°C'den az olmalı ve sıcaklık kontrolü hassas olmalıdır.
12. Kavite ve nozul montaj deliği geçmelidir.
13. Sıcak yolluk kabloları demetlenmeli ve bir baskı plakası ile kaplanmalıdır.
14. Açıkça işaretlenmesi gereken aynı özellikte iki soket vardır.
15. Kontrol hattı kılıflı olmalı ve hasar görmemelidir.
16. Sıcaklık kontrol kabininin yapısı güvenilirdir ve vidalar gevşek değildir.
17. Soket, bakalit üzerine kuruludur ve şablonun maksimum boyutunu aşamaz.
18. Teller kalıbın dışına çıkmamalıdır.
19. Sıcak yolluk veya şablonun tellerle temas ettiği tüm yerler yuvarlak geçişlere sahip olmalıdır.
20. Şablon montajı yapılmadan önce tüm devrelerde açık devre veya kısa devre yoktur.
21. Tüm kablolar, iyi bir yalıtım performansı ile doğru şekilde bağlanmalıdır.
22. Şablon takıldıktan ve kelepçelendikten sonra tüm devreler bir multimetre ile tekrar kontrol edilmelidir.
8. Şekillendirme parçası, ayırma yüzeyi, egzoz oluğu
1. Ön ve arka kalıpların yüzeyinde görünümü etkileyen pürüzler, çukurlar, pas ve diğer kusurlar olmamalıdır.
2. Uç, kalıp çerçevesi ile uyumludur ve yuvarlatılmış köşelerin çevresinde 1 mm'den az boşluk olmalıdır.
3. Ayırma yüzeyi temiz ve düzenli tutulur. Boşlukları önlemek için taşınabilir taşlama çarkı yoktur ve sızdırmazlık parçasında ezik yoktur.
4. Egzoz oluğunun derinliği plastiğin taşma değerinden az olmalıdır.
5. Eklerin araştırılması ve dağıtımı, düzgün yerleştirme ve güvenilir konumlandırma ile yerinde olmalıdır.
6. Ek parçalar, uçlar vb. güvenilir şekilde yerleştirilip sabitlenmeli, yuvarlak parçaların dönmesi engellenmeli ve eklerin altına bakır veya demir sac konulmamalıdır.
7. İtici çubuğun uç yüzü, çekirdek ile uyumludur.
8. Ön ve arka kalıpların şekillendirici kısmında alt kesik, pah gibi kusurlar yoktur.
9. Kaburgalar düzgün bir şekilde dışarı itilmelidir.
10. Çok gözlü kalıp ürünleri için sol ve sağ kısımlar simetriktir ve L veya R belirtilmelidir. Müşterinin pozisyon ve boyut gereksinimleri varsa, müşteri gereksinimlerini karşılamalıdır. Genel olarak, görünümü ve montajı etkilemeyeceği yere ekleyin. Yazı tipi boyutu 1/8'dir.
11. Kalıp tabanının kenetleme yüzeyi yerinde olmalı ve alanın %75'inden fazlasına dokunulmalıdır.
12. İtici çubuklar yan duvarlara daha yakın ve nervür ve göbeklerin yanına yerleştirilmeli ve daha büyük ejektör çubukları kullanılmalıdır.
13. Aynı parçalar için 1, 2, 3 vb. rakamlar belirtilmelidir.
14. Her temas yüzeyi, nüfuz eden yüzey ve ayırma yüzeyi araştırılmalı ve yerinde eşleştirilmelidir.
15. Ayrılan yüzey sızdırmazlık parçası tasarım standartlarını karşılamalıdır. Orta boy kalıplar için 10-20 mm, büyük kalıplar için 30-50 mm ve kalan parçalar boşluk kalmayacak şekilde işlenir.
16. Cilt dokusu ve kumlama, müşterinin gereksinimlerini eşit şekilde karşılamalıdır.
17. Görünüş gereksinimi olan ürünlerde ürünlerin üzerindeki vidalarda çekme önleyici ölçüler olmalıdır.
18. Derinliği 20 mm'den fazla olan vidalı kolonlar için kriko boruları kullanılmalıdır.
19. Ürünün et kalınlığı üniform olmalı ve sapma ±0.15 mm'nin altında kontrol edilmelidir.
20. Nervürlerin genişliği, dış yüzeyin et kalınlığının %60'ından az olmalıdır.
21. Eğimli çatı ve sürgü üzerindeki geçme göbekler güvenilir bir sabitleme yöntemine sahip olmalıdır.
22. Ön kalıp arka kalıba veya arka kalıp ön kalıba yerleştirilir ve yanlar eğik düzlemlerle kilitlenmeli ve hava kalmayacak şekilde işlenmelidir.
Dokuz, enjeksiyon kalıplama üretim süreci
1, Kalıp, enjeksiyon kalıplama üretiminin stabilitesine ve normal enjeksiyon kalıplama işlemi koşulları aralığında işlem parametre ayarının tekrarlanabilirliğine sahip olmalıdır.
2. Kalıp enjeksiyon üretimi sırasında enjeksiyon basıncı, genellikle enjeksiyon kalıplama makinesinin anma maksimum enjeksiyon basıncının %85'inden az olmalıdır.
3. Kalıbın enjeksiyon kalıplama üretiminin enjeksiyon hızı, üç çeyrek vuruşun enjeksiyon hızı, nominal maksimum enjeksiyon hızının %10'undan az veya nominal maksimum enjeksiyon hızının %90'ından fazla değildir.
4. Enjeksiyonla kalıplama sırasında kalıbın tutma basıncı, genel olarak gerçek maksimum enjeksiyon basıncının %85'inden az olmalıdır.
5. Enjeksiyon kalıplama üretimi sırasında kalıbın sıkıştırma kuvveti, geçerli modelin nominal sıkıştırma kuvvetinin %90'ından az olmalıdır.
6. Enjeksiyon kalıplama üretim sürecinde, ürün ve meme malzemesi kolay ve güvenli bir şekilde çıkarılmalıdır (süre genellikle 2 saniyeyi geçmez).
7. Uçlu kalıplar için, uçların montajı kolaydır ve üretim sırasında uçlar güvenilir bir şekilde sabitlenir.
10. Paketleme ve nakliye
1 Kalıp boşluğu temizlenmeli ve pas önleyici yağ ile püskürtülmelidir.
2. Kayar parçalar yağlanmalıdır.
3. Döküm burcunun girişi gres ile kapatılmalıdır.
4. Kalıpta bir sıkıştırma parçası bulunmalıdır ve özellikler tasarım gereksinimlerini karşılamalıdır.
5. Yedek parçalar ve aşınan parçalar, ayrıntılı bir liste ve tedarikçinin adı ile birlikte eksiksiz olmalıdır.
6. Kalıp suyu, sıvı, gaz ve elektrik giriş ve çıkışlarına yabancı maddelerin girmemesi için sızdırmazlık önlemleri alınmalı;
7. Müşterinin isteğine göre kalıbın dış yüzeyine boya püskürtün.
8. Kalıplar, müşterilerin istediği şekilde nem geçirmez, su geçirmez ve darbeye dayanıklı ambalajlarda paketlenmelidir.
9. Kalıp ürün çizimleri, yapısal çizimler, soğutma ve ısıtma sistemi çizimleri, sıcak yolluk çizimleri, yedek parça ve kalıp malzemesi tedarikçi detayları, çalıştırma talimatları, kalıp test raporları, fabrika muayene sertifikaları ve elektronik belgeler eksiksiz olmalıdır.
Lütfen yeniden basım için bu makalenin kaynağını ve adresini saklayın: Tarihteki en eksiksiz kalıp kabul standardı!
Minhe Basınçlı Döküm Şirketi kaliteli ve yüksek performanslı Döküm Parçaları üretmeye ve sağlamaya adamıştır (metal döküm parça yelpazesi esas olarak şunları içerir: İnce Duvarlı Döküm,Sıcak Kamara Basınçlı Döküm,Soğuk Oda Döküm), Yuvarlak Servis (Döküm Servisi,Cnc İşleme,Kalıp yapımı,Yüzey İşleme).Herhangi bir özel Alüminyum döküm, magnezyum veya Zamak/çinko döküm ve diğer döküm gereksinimleri bizimle iletişime geçebilirsiniz.
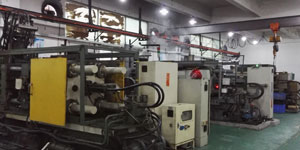
ISO9001 ve TS 16949 kontrolünde, tüm işlemler yüzlerce gelişmiş basınçlı döküm makinesi, 5 eksenli makine ve blasterlerden Ultra Sonic yıkama makinelerine kadar diğer tesisler aracılığıyla gerçekleştirilir. Müşterinin tasarımını gerçeğe dönüştürmek için deneyimli mühendisler, operatörler ve müfettişlerden oluşan ekip.
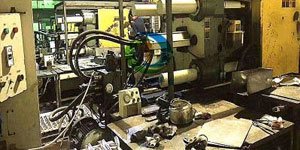
Dökümlerin sözleşmeli üreticisi. Yetenekler, 0.15 lbs'den başlayan soğuk oda alüminyum döküm parçaları içerir. 6 lbs'ye kadar, hızlı değişim kurulumu ve işleme. Katma değerli hizmetler arasında polisaj, titreşim, çapak alma, kumlama, boyama, kaplama, kaplama, montaj ve kalıplama yer alır. Çalışılan malzemeler arasında 360, 380, 383 ve 413 gibi alaşımlar bulunur.
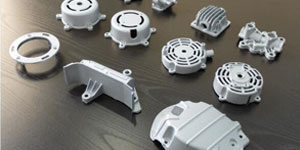
Çinko pres döküm tasarım yardımı/eşzamanlı mühendislik hizmetleri. Hassas çinko dökümlerin özel üreticisi. Minyatür dökümler, yüksek basınçlı dökümler, çok kızaklı kalıp dökümleri, geleneksel kalıp dökümleri, birim kalıp ve bağımsız kalıp dökümleri ve boşluklu sızdırmaz dökümler üretilebilir. Dökümler, +/- 24 inç toleransta 0.0005 inç'e kadar uzunluk ve genişliklerde üretilebilir.
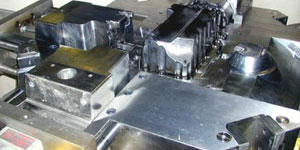
ISO 9001: 2015 sertifikalı döküm magnezyum üreticisi, Yetenekler arasında 200 ton sıcak odaya ve 3000 ton soğuk odaya kadar yüksek basınçlı magnezyum kalıp dökümü, takım tasarımı, cilalama, kalıplama, işleme, toz ve sıvı boyama, CMM özelliklerine sahip tam kalite güvencesi bulunur , montaj, paketleme ve teslimat.
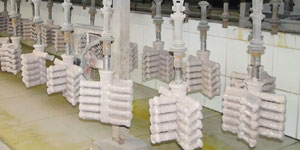
ITAF16949 sertifikalı. Ek Döküm Hizmeti Dahil yatırım dökümleri,kum dökümü,Yerçekimi Döküm, Kayıp Köpük Döküm,Savurma döküm,Vakumlu Döküm,Kalıcı Kalıp Döküm,.Yetenekler arasında EDI, mühendislik yardımı, katı modelleme ve ikincil işleme yer alır.
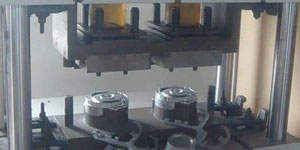
Döküm Endüstrileri Arabalar, Bisikletler, Uçaklar, Müzik aletleri, Deniz Araçları, Optik cihazlar, Sensörler, Modeller, Elektronik cihazlar, Muhafazalar, Saatler, Makineler, Motorlar, Mobilya, Mücevher, Jigler, Telekom, Aydınlatma, Tıbbi cihazlar, Fotoğraf cihazları, Robotlar, Heykeller, Ses ekipmanları, Spor ekipmanları, Aletler, Oyuncaklar ve daha fazlası.
Bundan sonra ne yapmanıza yardımcı olabiliriz?
∇ Ana Sayfaya Git Çin Döküm
→Döküm Parçaları-Ne yaptığımızı öğren.
→ Hakkında İlgili İpuçları Pres Döküm Hizmetleri
By Minghe Döküm Üreticisi |Kategoriler: Faydalı Makaleler |Malzeme Etiketler: Alüminyum Döküm, Çinko Döküm, Magnezyum Döküm, Titanyum Döküm, Paslanmaz Çelik Döküm, Pirinç Döküm,Bronz Döküm,Döküm Videosu,Tarihçe,Alüminyum Döküm |Yorumlar Kapalı