Yapışkan Küf Problemi ile Kalıp Ayırıcı İlişkisi
Yapıştırma, kalıp çeliği yüzeyi ile döküm alaşımı arasında kimyasal bir reaksiyona neden olan dolgu metali sıvısının yüksek basınçlı ve yüksek hızda tekrarlanan etkisidir ve kalıbın yüzeyinde kimyasal bir reaksiyon tabakası oluşur. dökümün yapışması olgusuna yol açar. Genel olarak, en ciddi kalıp yapışması çekirdektir.
Döküm parçaları kalıba yapıştığında, daha hafif yüzey pürüzlüdür, bu da görünümün pürüzlülüğünü etkiler; daha ağır olan yüzey soyulur, etten yoksundur, gerilir, yırtılır ve hatta dökümün sızmasına neden olur. Yapışkan kalıbın oluşumu ve genişlemesi sadece dökümün yüzey kalitesini ve boyutsal doğruluğunu azaltmakla kalmaz, kalıp yüzeyinin yoğun tabakasını, özellikle kalıbın yolluk konumunu yok eder, aynı zamanda kalıp tamiri için adam-saat ve maliyetleri de arttırır. ve hatta döküm israfına ve erken kalıp arızasına yol açar.
Yüksek sıcaklık ve yüksek basınç altında erimiş metal ile kalıp arasındaki temas yüzeyinin durumu çok karmaşıktır. İnsanların basınçlı dökümde yapışma sorunu üzerine araştırmaları yavaş yavaş makro yüzeyden mikro yüzeye, nitel analizden matematiksel model analizinin kurulmasına, tek faktörlü araştırmadan çok faktörlü araştırmalara doğru ilerliyor olsa da Kapsamlı araştırma statik araştırmadan dinamik araştırmaya doğru gelişir, ama çoğu hala sezgisel nitel analizde kalıyor. Yapışkan kalıbın özel koşullarına göre, oluşumunu ve genişlemesini etkileyen bazı faktörler özetlenir ve buna göre bazı önleyici tedbirler alınır. Şu anda, fikir birliği şudur: döküm proses parametreleri, kalıp tasarımı, kalıp sıcaklığı, kalıp yüzey kalitesi, doldurma sıcaklığı, kimyasal bileşim ve kalıp ayırıcı maddenin kalitesi, püskürtme işlemi, vb., tümü kalıbın yapışması üzerinde önemli bir etkiye sahiptir, yapıştırmak yerine. Kalıp, kalıp ayırıcıya sezgisel olarak bağlıdır. Bununla birlikte, ayırıcı maddenin kalitesi ve kullanım yöntemi, gerçekten de, kalıp döküm yapışkan kalıbı ile ayrılmaz bir şekilde bağlantılıdır. Kalıp döküm işçileri için, aralarındaki ilişkiyi anlamak ve bilmek, kendinizi ve düşmanı tanımak, kalıp döküm sürecini daha doğru bir şekilde kontrol edebilir.
Ayırıcı maddenin kendisi kimyasal bir üründür ve metal malzemelerden ve kalıplama işlemlerinden farklı bir bilgi alanıdır. Bununla birlikte, disiplinler arası geçiş her zaman yenilik ve gelişimin kaçınılmaz yönelimi olmuştur. Yazar, "yapışkan küfü hangi kuvvet oluşturur? Yapışkan küften en çok hangi faktörler etkilenir? Nasıl önlenir?" ve diğer konular analiz edilir ve özetlenir.Bu temelde, örnek olarak alüminyum alaşımlı kalıp dökümünü alın ve ardından kalıp ayırıcı madde ile kalıp döküm kalıbı arasındaki ilişkiden bahsedin.
Yapışkan Küfün Fizikokimyasal Özellikleri
Yapışkan kalıp teorisi, metal bilimi, kimya ve mekaniği temel alan kapsamlı bir teoridir. Yapışkan kalıp, temel olarak, en önemlisi yapışma olan, döküm ve kalıp arasındaki arayüz malzemesinin molekülleri veya atomları arasındaki fiziksel ve kimyasal etkileşimdir.
Alüminyum, çinko, magnezyum, bakır ve diğer döküm metal malzemeler ve kalıp malzemeleri polikristal bir yapıya sahiptir ve yüzey molekülleri, iç moleküllerden, yani yüzey enerjisinden daha büyük potansiyel enerjiye sahiptir. Hepsinde en düşük yüzey enerjisine yönelme içgüdüsü, yani atomların serbest yüzeydeki düzenini dengeye götürme içgüdüsü vardır. İki metal yüzey birbirine çok yakınsa, yüzey enerjisini azaltmak için aralarındaki kafesler birleşerek yapışmaya neden olur. Hepimizin bildiği gibi, birbirleriyle temas halinde olan katılar arasında yerçekimi kuvveti vardır. Yerçekimi kuvveti, kısa menzilli bağ kuvvetine ait olan metal bağ, kovalent bağ ve iyonik bağdan oluşur. Ayrıca uzun menzilli Von Der Wools Force (Von Der Wools Force) var. Temas mesafesi birkaç nanometre olduğunda, tüm van der Waals kuvvetleri çalışır. 1 nanometre içerisinde çeşitli kısa menzilli kuvvetler devreye girer. Yapışma bağının gücünü tahmin etmek için önce metalin kohezyonunu belirleyin ve ardından temas yüzeyinin yüzey kuvvetini hesaplayın. Ancak metallerin karmaşık elektronik yapısı nedeniyle kohezyon mukavemetini teorik olarak çözmek şu anda mümkün değildir.
Fenomen açısından, yapışma, kimyasal bir kombinasyon veya mekanik bir tıkanıklıktan başka bir şey değildir. Yapışma mukavemeti ile ilgili ana faktörler şunlardır: metalin türü, metalin karşılıklı çözünürlüğü, kristal kafesin yönü, temas sırasında elastoplastik deformasyonun yolu, elastik geri kazanım, segregasyon ve oksidasyon, dislokasyon ve mikro çatlama, temas sıcaklığı , vb. Kalıbın kendisinin yüzey sertleşmesi, yüzey pürüzlülüğü, temas basıncı vb. de önemli faktörlerdir. Farklı atomların bağlanma yeteneği farklıdır ve farklı bileşimlerdeki alaşımlar farklı yapışma eğilimleri gösterir. Bu nedenle uygun kalıp malzemesi ve kalıp ayırıcı formülün seçilmesi, döküm ile kalıp arasındaki yapışmayı en aza indirebilir.
Alüminyumun Pres Döküm Kalıplarında Yapışmasının Nedenleri
Yapıştırıcı alüminyumun kendisi metaller arasında kimyasal bir difüzyon reaksiyonudur.
1) Kimyasal Bileşimi
Kalıp döküm alaşımı ile kalıp çeliği arasındaki afinite ne kadar büyük olursa, eritilmesi ve birbirine bağlanması o kadar kolay olur. Alüminyum alaşımındaki demir içeriği %0.7'den az olduğunda, kalıp yüzeyindeki demir atomları, konsantrasyon gradyanı nedeniyle alüminyum sıvısına daha hızlı nüfuz edebilir ve demir-alüminyum veya demir-alüminyum- oluşturmak kolaydır. silikon intermetalik bileşikler ve kalıba yapışır. Açıkçası, saf alüminyumun yapışma eğilimi en ciddi olanıdır, ötektik alüminyum-silikon alaşımının kalıp dökümünde yaygın olarak kullanılan yapışma eğilimi daha küçüktür. Nikel, intermetalik bileşiklerin büyümesini teşvik etme etkisine sahiptir ve alüminyum sıvısındaki ve krom ve nikeldeki inklüzyonlar alüminyum yapışma şansını artırabilir. Yüksek silikon ve artan manganez, ara metal fazın büyüme hızını yavaşlatabilir ve kalıp yapışmasını azaltabilir. Az miktarda stronsiyum (%0.004) ve titanyum (%0.125) alüminyum yapışmasını da azaltabilir.
Kısacası, alaşım bileşimini makul bir aralıkta sıkı bir şekilde kontrol edin ve kalıp yapışmasını önlemenin temeli olan alüminyum alaşımlı sıvının temizliğine bağlı kalın.
2) Kalıp Malzemesi
Kalıp malzemeleri, toplam kalıp maliyetinin yaklaşık %10'unu oluşturuyordu. 1950'lerde eski Sovyetler Birliği'nden ithal edilen 3Cr2W8V sıcak işlenmiş kalıp çeliği Çin'de yaygın olarak kullanılıyordu. 10,000 ila 20,000 kalıp kalıp dökümü yaparken, boşlukta kılcal çatlaklar oluşmaya başladı ve kalıp yapışkan değildi. önlemek. 1990'larda, mükemmel çelik kalitesi H13, Amerika Birleşik Devletleri'nden tanıtıldı. Hem tokluğa hem de tokluğa sahip hava soğutmalı sertleşen bir sıcak iş kalıp çeliği olarak, ömrü 15 ila 200,000 kalıp zamanına ulaşabilir. Bu çelik kalitesi matris olarak kullanılarak çeşitli benzer çelik kaliteleri genişletilmiştir, örneğin: Japan SKD61 of (JIS); Güney Kore'nin STD61'i (KS); BH13 of Britain (BS), vb. Seçilen kalıp malzemesinin kalitesi düşükse, sertleşebilirliği, tokluğu, aşınma direnci, ısıl işlem stabilitesi zayıfsa, kalıp sertliği yetersizse, kalıp yüzeyi pres döküm tarafından sıkıştırılır. Kalıptan çıkarma sırasında alaşım veya maça bükülür ve deforme olur, bu da kalıp eşleşmesini arttırır Dökümlerin kalıp ayırma direnci, doğrudan kalıp yapışmasına yol açan doğuştan gelen kusurlar nedeniyle kalıp yüzeyinde çatlaklar ve kaynak gibi kusurlara neden olmak kolaydır. Dökümün kalıba yapışan kısmı genellikle pürüzlü yüzey, soyulma veya malzeme eksikliği gibi çizim işaretleri gösterir. Şiddetli yapışma durumunda, döküm yırtılır ve hasar görür. Kalıp boşluğunun yüzeyi, bir laminat döküm alaşımına yapışacak ve resimde gösterildiği gibi renk beyaz olacaktır.
Yapışmanın kalıbın sıcak noktasında veya kapının tam karşısında kolayca meydana gelmesinin nedeni, burada metaller arası bileşik katmanın oluşturulmasının kolay olması ve oluşturulan intermetalik bileşik katmanın Al4FeSi ve H13 kalıbının güçlü bir yapışma gücüne sahip olmasıdır. Oluşan ince intermetalik bileşik katman, yüksek hızlı eriyiğin, doldurma sırasında kalıbın yüzeyini tekrar tekrar temizlemesinden kaynaklanır ve intermetalik bileşik katmanın kalıbın yüzeyinden sıyrılmasına neden olur. Aşınmaya dayanıklı malzeme Cr23C6, alüminyum alaşımlı eriyiğin kimyasal etkisini etkili bir şekilde önleyebilir ve kalıp malzemelerinin kaybını ve kalıp yapışmasını azaltabilir.
3) Kalıp Tasarımı
Kalıp döküm işlemi normal olduğunda, ancak yeni bir kalıp kalıba yapıştığında, kalıp döküm işleminde hata ayıklama ve püskürtme düzeltilebilir, ancak kararsız ise, ana nedenin döküm yapısının sorunu olduğu anlamına gelir. tasarım, kalıp tasarımı veya imalatı.
Birincisi, akış yönünün, kesit alanının, enjeksiyon hızının vb. yanlış kontrolü gibi iç kapı tasarımıdır, erimiş metal, kalıp yapışmasına en yatkın olan çekirdeği veya duvarı doğrudan aşındırır. Sabit kalıbın kenarına çarparsa, sabit kalıbın yanındaki dökümün paketleme kuvveti artacaktır. Dökümün genel veya kısmi büzülmesi, kalıbın sıkıştırma kuvvetinin dengesiz ve makul bir dağılımına sahip olduğunda, döküm, sapmış, eğri, eğimli, deforme olmuş, çatlamış, kalıbın yapışması nedeniyle kırılmış ve hatta yapışmış görünecektir. sabit kalıp veya hareketli kalıbın üstüne yapıştırın. . Sabit kalıp boşluğunun kalıptan çıkarma eğimi veya maça oluşturma yüzeyi çok küçükse veya ters eğime sahipse, döküm direnci artacak ve maça çekme ve parça çıkarma sırasında çiziklere neden olacaktır. Ek olarak, kalıp tasarımı erken olması gereken doğruluğu kaybedecek kadar rijit değildir; kalıp yüzey kalitesi ve yüzey güçlendirme işlemi eksiktir; hareketli ve sabit kalıplardaki soğutma sistemi tasarımı mantıksızdır, bu da kalıbın çalışma sıcaklığını dengesiz ve kararlı hale getirir; sıcak düğümler vs var. Yapışkan kalıba yol açar.
4) Kalıp İşleme
Kalıbın taşlama işlemi sırasında oluşan sürtünme ısısı, yüzeyde taşlama çatlaklarına neden olacaktır. Öğütme stresinin varlığı, kalıbın termal yorulma direncini de azaltacaktır. Kalıp boşluğunun yüzeyi, özellikle kızağın pürüzlü yüzeyi veya kalıp yüzeyinde az miktarda çizik ve çizik izi bulunan yerler, potansiyel çatlak kaynaklarıdır. EDM finiş işlemenin yerel yüksek sıcaklığı, yüzeyin altındaki temperlenmiş bölgeyi oluşturur. Bu bölgenin yapısı ve kimyasal bileşimi, matrisinkinden farklıdır. Bu bölgenin sertliği yüksektir. Yüzeyde kalan gerilimin varlığına ek olarak, polisaj işlemi yerinde olmayabilir ve kalıbın erken kullanımında mikro çatlaklar oluşturabilir. Yapışkan kalıba yol açar.
5) Döküm İşlemi
Alaşım sıvısının doldurma sıcaklığı çok yüksekse, demirin difüzyonu ve reaksiyonu hızlanacaktır. Yağlama filmi ne kadar kolay bozulursa, kalıp yüzeyi o kadar kolay tavlanacak ve erozyona ve alüminyum yapışmasına daha duyarlı olacaktır. Enjeksiyon hızı ve basıncı çok yüksekse, kalıp sıcaklığı çok yüksekse ve kalıp sertliği düşükse, erime, kaynak yapışması ve kalıp yapışması kolayca gerçekleşir.
6) Serbest Bırakma Maddesi
Ayırıcı maddenin birincil işlevi, kalıbı korumak ve yüksek hızlı erimiş alüminyumun kalıp üzerindeki termal etkisini azaltmak için sağlam bir yağlayıcı film oluşturmaktır.
Düşük kalıp ayırma ajanları, kalıbı koruma işlevine sahip değildir, çünkü kimyasal bileşimi, sert, pürüzsüz, ısıyı tutan, daha az gaz yapan, kalıntı bırakmayan ve akışa yardımcı olan bir yağlama filminin hızla oluşturulmasının imkansız olduğunu belirler. işlemin gerektirdiği kalıp sıcaklığı aralığında alaşım sıvısı. Püskürtme işlemi nasıl ayarlanırsa yapılsın, temel özellikleri değiştirilemez, bu nedenle gizli kalıp yapışması tehlikesi kaçınılmazdır.
Yapışkan Kalıp Problemini Çözme Yolları
Kalıp yapışması sorunu, birçok faktörün kapsamlı bir tepkisidir. Bu nedenle, kalıp yapışması sorununu çözmek için, deneme yanılmalara izin vererek, birden çok açıdan analiz etmeli ve yargılamalıyız, ancak öznel yargılarda bulunmamalıyız. Yazar tarafından özetlenen aşağıdaki maddeler tamamen kara kutu teorisine dayanan ampirik becerilerdir, yani kalıp bir kara kutu olarak kabul edilir ve doldurma işleminin iç değişiklikleri araştırılmaz ve siyahın sadece iki ucu araştırılır. kutusu giriş parametreleri ve kalıplama efektleridir. Yapışkan modu temel olarak çözmek için derinlemesine mikro-teorik araştırma sonuçlarının rehberliğine ihtiyacı var ve daha gidecek çok yolu var.
- Kapı hızını etkileyen faktörleri kontrol edin: zımba hızı, zımba boyutu, özgül basınç, kapı boyutu, kapı hızını mümkün olduğunca azaltın veya temas açısını önlemek için kapı yönünü boşluk yüzeyine daha küçük bir açıyla temas edecek şekilde ayarlayın 180'e yakın boşluktaki erozyonu azaltmak ve çekirdeğe darbeyi önlemek için dereceler. Termal şok penceresini daraltmak için doldurma süresini azaltın.
- Kalıp soğutma kanalını, özellikle sıcak düğümü ve kalıba yapışması kolay maçayı ayarlayın, gerekirse bir soğutucu ekleyin. Yapışan parçanın kalıp sıcaklığını azaltmak ve sabit ve dengeli bir kalıp sıcaklığı elde etmek için ikinci bir sprey ekleyin veya yapışkan parçaya yüksek termal iletkenliğe sahip kalıp malzemesi yerleştirin.
- Dökümün en küçük çıkış alanında, yüksek doldurma basıncı kalıbın yapışmasına neden olabilir. Dökümlerin kalitesinin karşılanması öncülüğünde, dolum basıncını mümkün olduğunca azaltın. Hem statik basınç hem de basınçlandırma önemlidir. Aynı zamanda basınç ayarı da PQ2 diyagramına göre hesaplanmalı ve ayarlanmalıdır.
- Yüksek kalıp sıcaklığı ve döküm sıcaklığı, kalıbın yapışma eğilimini artıracaktır. Kalıbın yapışmasını etkileyen birkaç faktör olduğunda, kalıp sıcaklığını veya döküm sıcaklığını düşürmek bunu düzeltmenin en iyi yoludur.
- Mo-785, Ti-6AI-4V ve Anviloy 1150 gibi yüksek mukavemetli özel malzemeler, kalıp yapışmasının muhtemel olduğu yerlerde kullanılabilir. Çeşitli kalıp yüzey işleme yöntemleri, kalıp yapışmasını önemli ölçüde azaltabilir. Nitrürleme ve karbonitrürleme işlemi, {TiAl}N ve CrC ve alüminyum film gibi fiziksel buhar biriktirme yoğun tabaka, vb., kalıp yüzeyinin güçlendirilmesi işlemi, kalıp kaplama ---CVD, PVD, TD, vb. Gibi. Mevcut yapışkan kalıp bir an önce ortadan kaldırılması gerekmektedir. Gelişmesine izin verilirse, giderek daha fazla zorluk ve tekrar ortaya çıkacaktır.
- Yüksek film oluşturan ısı direnci sıcaklığına, güçlü kalıp kalitesine ve iyi yağlama etkisine sahip yüksek kaliteli kalıp ayırıcı maddeler kullanın. Gerilmeyi önlemek için yeni kalıpları denerken kalıp macunu uygulayın. Kalıpların yapışmasının kolay olduğu yüksek sıcaklıktaki alanlar için, yapışmaz mum macunu düzenli olarak uygulanabilir veya kısmen yapışma önleyici mum sıvısı püskürtülebilir.
- Kalıp çıkarma açısını dikkatlice izleyin ve izin verilen maksimum değeri, kalıp döküm kalıbı standardına uygun olmalıdır.
- Kalıp döküm alaşımının kompozisyon tasarımı, kalıp yapışmasına neden olabilecek faktörleri dikkate almalıdır. Örneğin, izin verilen aralık dahilinde, alüminyum alaşımındaki demir içeriğinin %0.7'den az olmayacak şekilde kontrol edilmesi tavsiye edilir. Düşük erime noktalı metallerle karıştırılarak oluşan kalıp yapışmasını önlemek gerekir. Kimyasal bileşimi ayarlamak için bir ana alaşım kullanıldığında, magnezyum ve çinko gibi tek tek metallere ek olarak, şiddetli ayrışmanın kalıp yapışmasına neden olmasını önlemek için alüminyum sıvıya saf metaller eklenemez. Saflaştırılmış alaşım sıvısı iyi akışkanlığa sahiptir ve genişleyebilir. Kalıp yapışmasını önlemek için işlem penceresi.
- Kalıp döküm alaşımının büzülmesi ne kadar büyük olursa, kalıba yapışması o kadar kolay olur ve yüksek sıcaklık dayanımı o kadar kötü olur. Bazı alaşımlar daha büyük bir büzülme oranına sahiptir. Alaşımın sıvı ve katı sıcaklık aralığı ne kadar geniş olursa, alaşımın büzülmesi o kadar büyük olur. Dökümün yapısal şekline ve karmaşıklığına göre, büzülmeden kaynaklanan yapışma ve deformasyonun giderilmesi zor ise, düşük hacimli büzülme ve lineer büzülme ve yüksek sıcaklık dayanımı olan bir alaşıma geçilmesi düşünülmelidir; veya alaşım bileşimini ayarlayın (alüminyum silikon gibi) Alaşımdaki silikon içeriği arttığında, dökümün büzülme hızı küçülür) büzülme oranını azaltır; veya alaşımların büzülme eğilimini azaltmak için alüminyum alaşım sıvısına %0.15 ila %0.2 titanyum ve diğer tane incelticiler eklemek gibi alaşımı modifiye edin.
Kalıp Ayırıcı ve Yapışkan Kalıp Arasındaki İlişki
Döküm dinamik bir termodinamik süreçtir. Alüminyum ve çinko gibi alaşımlar, boşluğun yüzeyine güçlü bir şekilde yapışma eğilimindedir. Püskürtülen ayırma maddesi, metalin boşluğun yüzeyine yapışmasını önlemek için boşluk ve sıvı metal arasında bir ayırıcı madde olarak hareket edebilir. Ayırıcı ajanın (bileşim, konjonktival sıcaklık, hava hacmi, kalıntı, konjonktival kuvvet, sonraki yüzey kaplama üzerindeki etkisi vb.) ve makul çalışma teknolojisinin (ayırıcı madde konsantrasyonu, kalıp sıcaklık dağılımı, atomizasyon işlemi, püskürtme Süresi ve mesafesi, vb.) dikkatli seçimi .) Kalıp yapışmasını önlemek için önemli faktörlerdir.
Yarım yüzyıldan fazla bir süredir, kalıp döküm teknolojisinin gelişmesiyle birlikte kalıp ayırıcı maddeler de buna göre gelişmiştir. Bu iyileştirmeler arasında ayırıcı madde bileşimi, film oluşumu, sıcaklık direnci, kayganlık, kalıp yapışmasının ve kaynaklanmanın önlenmesi ve vücuda zararsız ve güvenli olan çevre koruma gereksinimlerine uygunluk yer alır. Erken yağ + grafit kaplamalardan su bazlı kaplamalara, sıradan yağ bazlı sabun emülsiyon serisinden şu anda yaygın olarak kullanılan modifiye silikon yağı serisi su bazlı ayırıcı maddelere, susuz konsantre ayırıcı maddelere (mikro püskürtme için) ve geliştirin reaktif yarı kalıcı kaplamalara ve toz inorganik kaplamalara doğru. Ancak şimdiye kadar, sınırlamalar veya dezavantajlar olmaksızın olası tüm özellikleri sağlayabilen bir ayırıcı madde ortaya çıkmamıştır. Yarı kalıcı boya, çinko alaşımlı kalıp döküm için test edilmiştir. Kalıbın yüzeyine kimyasal olarak bağlıdır. Kaplama 698ºC'de stabildir, ancak aşınması kolaydır, bu nedenle dayanıklılığını arttırmaya çalışmak gerekir. Alüminyum ve magnezyum alaşımlarının kalıp dökümü için esas olarak kaplamanın termal stabilitesinin nasıl iyileştirileceğidir. Çevre koruma ve güvenlik açısından, zararlı çözücülerin azaltılması veya ortadan kaldırılması da dikkate alınmalıdır. Son yıllarda yarı kalıcı kalıplara ve kalıcı kalıplara yönelik çok sayıda araştırma çalışması yapılmıştır. Yeni kaplamalar geliştirerek, kaynak ve yapışmanın üstesinden gelerek ve sonunda kalıp ayırıcı maddelerden vazgeçerek bu, çığır açan bir yeniliktir. Ancak şimdiye kadar elde edilen sonuçlar endüstriyel uygulamalarda kullanılamaz. Başlıca problemler kaplamanın dayanıklılığı, kaplama yöntemi ve fiyatıdır.
Öngörülebilir gelecekte, çeşitli serbest bırakma maddelerinin geliştirilmesi ve araştırılması hala vazgeçilmez olacaktır. Kalıp döküm parçasının kalıplama yüzeyi ile kalıp yüzeyi arasında önemli bir temas basıncı vardır. Döküm parçası, kalıp dökümü sırasında üç yönlü eşit dağılmamış basınç gerilimine maruz kalır. Bu nedenle, ayırıcı madde püskürtülerek oluşturulan yağlayıcı filmin yırtılması kolaydır ve yüksek sıcaklık da yağlama filminde kimyasal değişikliklere neden olur. . İkinci ekstrüzyon sırasında, az miktarda yeni metal yüzey görünecektir. Yeni yüzey, orijinal metal yüzeyden farklı fiziksel ve kimyasal özelliklere sahiptir. Yağlayıcı koruması yoktur ve kalıba yapışması kolaydır ve kalıbın aşınmasına neden olur. Aynı zamanda, dökümün iç deformasyonunun eşit olmayan dağılımından kaynaklanan ek gerilim ve artık gerilim de kalıp sıkışana kadar parçayı almanın zorluğunu arttırmaktadır.
Kalıp için, kalıp döküm işleminin değişmesi ve kalıbın sıcaklık alanı nedeniyle, şekillendirme işlemi bir tür aralıklı ve kararsız sürtünmedir ve kalıbın farklı parçaları farklıdır. Bu durumdaki yağlama mekanizması, genel fizikte Coulomb sürtünme teoremi tarafından analiz edilemez ve tanımlanamaz. Yurtiçinde ve yurtdışında uzmanlar, çeşitli karmaşık kimyasal bileşimlere sahip yağlayıcıları incelerken, art arda mekanik-moleküler sürtünme teorisi, yapışma-ligou sürtünme teorisi, sınır sürtünmesi, karışık sürtünme, elastik viskoz sürtünme teorisi vb. ortaya koydular.
Alüminyumun kalıplara yapışmasını azaltmak için kullanılan grafit ayırıcı maddeler, çevresel etki nedeniyle artık kullanılmamaktadır. Ayırıcı maddenin mekanizması, alüminyum alaşımlı sıvının doğrudan kalıp yüzeyi ile temasını engellerken, döküm ile kalıp arasında koruyucu bir film oluşturmaktır. Bu, ayırıcı maddenin alüminyum alaşımlı sıvının ayrılmasına ve etkisine dayanacak yeterli güce sahip olmasını gerektirir. Kalıp yüzeyinin sıcaklığı genellikle alaşım döküm sıcaklığının %35 ila %45'inde kontrol edilir, böylece ayırıcı madde kalıp yüzeyinde tamamen emilebilir ve kalıbı koruyabilir. Kapının yanındaki kalıp ve derin oluklar alüminyum yapışmasına eğilimlidir. Alüminyum alaşım yapışmasının meydana geldiği kalıp yüzeyinin şekli şekilde gösterilmiştir. Bu küçük düzensiz çukurların başlangıç çapı yaklaşık 0.6 mikrondur ve sonunda yavaş yavaş 3.6 mikron çapında küçük çukurlara dönüşürler. Yapışkan bir kalıp oluşturma eğilimi arttıkça bu küçük çukurların çapı 15 µm'ye ulaşabilir ve sonunda çatlaklar oluşur. Bu küçük çukurlar ve çatlaklar sonunda alüminyum ile doldurulur ve mekanik bağlanma da meydana gelebilir.
Ayırıcı maddenin rolü, kalıbın yüzeyini ve kalıp dökümünü ayırmak, kalıbın hasarını azaltmak, dökümün yüzeyini pürüzsüz hale getirmek ve aynı zamanda kalıbın soğutulması, ayarlanması ve kontrolünde rol oynamaktır. . Ayırıcı madde ve kalıp yüzeyi, polar olmayan veya polar fiziksel adsorpsiyon filmi, kimyasal adsorpsiyon filmi ve kimyasal reaksiyon filmi üretebilir. Ayırıcı ajanda polar moleküller olmadığında, ayırıcı ajan sadece kalıp yüzeyinde polar olmayan bir fiziksel adsorpsiyon filmi üretebilir; aksi takdirde polar bir fiziksel adsorpsiyon filmi üretebilir. İkincisinin gücü, polar olmayan fiziksel adsorpsiyon zarınınkinden daha fazladır. Kalıp ayırıcı bileşendeki atomlar ve kalıp yüzeyindeki atomlar ortak elektronları paylaştığında, kalıp yüzeyinde kimyasal bir adsorpsiyon filmi üretilecektir. Gücü, polar fiziksel adsorpsiyon filminden daha yüksektir. Belirli bir temas basıncı ve sıcaklığı altında, ayırıcı madde içindeki aşırı basınç maddesi, bir kimyasal reaksiyon filmi oluşturmak için kalıp yüzeyi ile kimyasal olarak reaksiyona girebilir. Gücü, kimyasal adsorpsiyon membranından daha fazladır. Genel olarak konuşursak, ayırıcı maddenin adsorpsiyon filminin gücü ne kadar yüksek olursa, yapışmayı önleme etkisi o kadar iyi olur. Bu nedenle, farklı kalıp döküm parçalarına göre, yüksek mukavemetli bir adsorpsiyon filmi oluşturmak için karşılık gelen ayırıcı maddeyi seçmek çok önemlidir.
Genel mineral yağ ile hazırlanan su bazlı ayırıcı madde, polar olmayan bir hidrokarbon organik bileşiktir (CnH2n+1). Oluşan film, kalıbın yüzeyinde zayıf adsorpsiyon kuvvetine ve moleküllerin kendilerinin kohezyonuna sahiptir ve film mukavemeti çok düşüktür. Yağ asitleri, yağlı asit sodyum sabunları, asitler (ROH) vb. gibi hayvansal ve bitkisel yağlardan hazırlanmış, bir ucunda polar olmayan bir hidrokarbon grubu ve diğer ucunda polar olan su bazlı bir ayırıcı. Bu molekülün kalıcı bir dipolü vardır. Kalıp yüzeyi ile temas halindeyken, kutupsal uç kalıp yüzeyini çekerken, kutupsal olmayan uç dışa bakar ve metal yüzey üzerinde hizalanır. Adsorplanan moleküllerin tabakası sadece birkaç nanometre kalınlığındadır. Polarize edici katkı maddeleri eklendiğinde, Polimerizasyon kalıbın yüzeyinde katı bir film oluşturur ve aynı zamanda moleküllerin yan adsorpsiyon kuvvetini güçlendirir. Bu fiziksel adsorpsiyon filminin gücü ve kayganlığı, polar olmayan moleküllü fiziksel adsorpsiyon filmininkinden çok daha yüksektir.
Fiziksel adsorpsiyon filmi sıcaklığa çok duyarlıdır ve kalıbın yüzeyinde adsorbe edilen polar moleküller, sürekli adsorpsiyon ve desorpsiyonun dinamik bir denge durumundadır. Sıcaklık yükselir, desorpsiyon artar, adsorpsiyon filminin kalınlığı azalır ve sınır adsorpsiyon filminin gücü azalır, moleküllerin desorbe olmasına, kaotik yöne ve hatta filmi eritmesine neden olur ve bunun tersi de geçerlidir. Fiziksel adsorpsiyon filmi yalnızca düşük temas basıncı ve düşük sıcaklık koşulları altında etkilidir, bu nedenle bu tip ayırıcı madde yalnızca düşük kalıp sıcaklıklarında çalışabilir. Fiziksel adsorpsiyonun seçiciliği yoktur, kimyasal adsorpsiyonun belirgin seçiciliği vardır, yani belirli bir adsorban yalnızca belirli maddeleri adsorbe edebilir. Bu nedenle istenilen etkiyi elde etmek için kalıba ve döküm malzemesine, pres döküm proses koşullarına (kalıp sıcaklığı, döküm duvar kalınlığı, dolum sıcaklığı, basınç vb.) göre farklı kalıp ayırıcı maddeler seçilmelidir.
Ana gövde olarak modifiye silikon yağı yüksek moleküler polimer ile hazırlanan su bazlı ayırıcı ajan, polar molekülleri, kimyasal bağlanma kuvveti ve yüzey kombinasyonu ile oluşan kimyasal adsorpsiyona ait olan kalıbın yüzeyi ile kimyasal olarak birleştirilir. Bu nedenle, film iyi bir ısı direncine, yüksek termal stabiliteye, geri dönüşü olmayan adsorpsiyon filmine, güçlü yapışmaya ve iyi bırakma etkisine sahiptir. Fiyatı biraz daha yüksek olmasına rağmen, yüksek kalıp sıcaklığı, yüksek basınç ve büyük ve ince duvarlı karmaşık parçalar gerektiren basınçlı döküm için kalıp yapışmasını önlemede belirgin avantajları vardır.
Kalıp yapışmasını önlemek için püskürtme işlemi çok önemlidir. Operatör kalıbın yapıştığını tespit ettiğinde, bunun konsantrasyonun düşük olması veya dozajın küçük olması ve filmin erimiş metalin termal stresine ve türbülans etkisine dayanamayacak kadar ince olması doğaldır ve ardından püskürtün. Yapışkan kalıp üzerinde daha fazla kalıp ayırıcı. Sonuç genellikle gözeneklere neden olan ve sorunu karmaşıklaştıran yerel boya birikimi veya kalıntısıdır. Doğru yöntem, yapışmanın meydana geldiği alana bir tür yapışma önleyici macun --- yapışma önleyici mum uygulamak ve özel işlem yapmak olmalıdır. Yapışma önleyici mum, yarı sentetik yüksek sıcaklık hammaddelerinden hazırlanan, fırçalanması kolay bir kaynak önleyici merhemdir. Etkili bileşen zararlı maddeler içermez. Macundaki yüksek sıcaklığa dayanıklı tungsten bazlı bileşik veya molibden bazlı bileşik içeriği, alüminyum alaşımının arayüz etkisini etkili bir şekilde önleyebilir ve kalıba yapışmasını önleyebilir.
Kalıp sıcaklığı kalıp ayırıcının adsorpsiyon etkisini etkileyen önemli bir faktördür. Çok düşük (150ºC'nin altında), kalıp sıcaklığı hızla suyun buharlaşma noktasının altına düşer, kalıp ayırıcı madde kalıp yüzeyinde birikemez, sadece kalıp yüzeyinden geçer ve taşıyıcı su buharlaşmak için çok geç kalır, bu da yaygın gözeneklere neden olabilir; kalıp sıcaklığı Çok yüksek (398ºC'nin üzerinde), kalıp ayırıcı, kalıp yüzeyindeki buhar tabakası tarafından itilir ve kalıp ayırıcı maddenin adsorpsiyon kapasitesi büyük ölçüde azalır. Sadece kalıp ayırıcının özelliklerinin gerektirdiği ıslatma sıcaklığına ulaşıldığında, kalıp yüzeyi ile gerçekten temas ederek bir kompakt oluşturabilir mi? Kaplama izolasyon rolü oynar.
Püskürtme işlemi de adsorpsiyon etkisini doğrudan etkiler. Genel olarak, püskürtme borusunun basıncı, ayırıcı maddenin basıncından 0.35-0.70 bar daha yüksek olduğunda (geniş alanlı püskürtme için 1.05 bar gerekebilir), atomizasyon etkisi iyidir; mikro püskürtme ve darbeli püskürtme için atomizasyon etkisi daha iyidir. Önemli. Püskürtme süresine gelince, yeterince kalın bir izolasyon filmi oluşturmak için 0.10-2.0 saniye kadar kısa bir süre yeterlidir. Darbeli püskürtme süresi bu aralıktadır, ancak ayırıcı madde şu anda boşluğu soğutmak için büyük miktarlarda kullanıldığından, genellikle 5.0-120 saniye sürer. Açıkça, ayırıcı maddenin bir kısmı kalıbın yüzeyinden akmakta ve boşa harcanmaktadır. Daha karmaşık ve hassas otomatik püskürtme cihazlarının ortaya çıkmasıyla, püskürtme açısı ve mesafesinin yalnızca üretimden önce ayarlanması ve sabitlenmesi gerekir.
Kalıp ayırıcı kullanan kalıp döküm mühendisleri için önemli olanın kalıp ayırıcıların profesyonel bilgilerini tüketmek ve daha sonra kendi kararlarına göre seçmek değil, Avrupa ve Amerika kalıp döküm endüstrilerinden öğrenmek olduğunu düşünüyorum. ve üreticilerin kalıp ayırıcı maddelerin üretiminde uzmanlaşmalarına izin verin. Döküm üreticisi tarafından sağlanan döküm yapı şemasına, döküm makinesinin tonajına, dökümlerin performans gereksinimlerine ve işlem sonrası işlem gereksinimlerine, en uygun kalıp ayırıcı modeli ve yöntemine göre. Tatmin edici sonuçlar elde edilene kadar kullanılması tavsiye edilir. Çünkü kalıp ayırıcı maddelerin üretiminde gerçekten uzmanlaşan üreticiler, kalıp ayırıcı maddelerin performans özelliklerini en iyi şekilde bilmeli ve körlükten kurtulmak ve verimli bir üretim döngüsünü sürdürmek için onlarla etkileşime girmelidir.
Doğru Tutun Kalıp Yapıştırma
Kalıp döküm üretiminin özü, alaşım eritme ve kalıpların kalitesidir. Yapışkan kalıpları önleyen ve bunlarla uğraşan tüm faktörler arasında, yüksek kaliteli kalıp malzemelerinin seçimi esastır, kalıp tasarımı ve işlenmesi ve standart ısıl işlem anahtardır ve kullanım sırasında zamanında ve etkili bakım ana yoldur. Kalıp yapışması meydana geldiğinde, kalıp döküm işlemini yapan taraf ve kalıp üreticisi genellikle birbirini suçlar. Bu anlaşılabilir bir durumdur, çünkü yapışmayı tetikleyen faktörler çeşitlidir ve şu an için kesin bir yargıya varmak zordur. Ama her halükarda asıl özellik kalıba düşüyor, bu yüzden sıkışmış kalıplar için önce kalıbın kendisini analiz etmeli ve ele almalıyız.
- Kalıp döküm kalıbının yüzey cilalaması gereksinimleri karşılamalıdır. Sert EDM tabakasını çıkarmak için iyice cilalayın ve yüzey çok fazla cilalanmamalıdır.
- Kalıp döküm kalıbına yapışan alüminyumu zamanında temizleyin ve kalıp üzerinde yüzey işleme ve stres giderme işlemini zamanında yapın. Kalıbın yüzeyinde alüminyum yapışması varsa ve yüzeyde küçük kabarcıklar varsa, yüzeyi cilalamak için zımpara bezi ve yağ taşı kullanın ve ardından kalıbı tekrar tekrar yapıştırın. Daha iyi tedavi yöntemi, yapışan kalıbın kalıp yüzeyini veya yapışma konumunda olan kalıbı kumlamaktır Yüzeyde, 0.2-0.5 mm genişliğinde, 0.2-0.5 mm derinliğinde ve aralıklı bir ağ deseni Döküm yüzeyine kalıp yapışma kusurlarını ortadan kaldırabilecek 2-5 mm üretilebilir.
- Kalıbın alüminyuma yapışmasının kolay olduğu yerlerde sıcaklığı en aza indirmeye çalışın.
- Kalıp üzerinde yüzey işlemi gerçekleştirmek için daha yüksek erime noktasına sahip özel malzemeler kullanın ve kalıbın yapışmasını önlemek için kalıbın yüzeyine yapıştığı konuma yapıştırılabilir. Molibden alaşımları, tungsten alaşımları, titanyum alaşımları, özel nitrürler veya düşük sıcaklıkta karbon ve azot bileşikleri gibi yeni malzemeler. Alüminyum ve molibden arasındaki aktivasyon enerjisi nispeten yüksektir, bu nedenle kalıbın yüzeyinde molibden infiltrasyonunun kullanılması, yapışma önleyici performansı etkili bir şekilde artırabilir.
- Yeni kalıplar ve sabit kalıba yapışan dökümlere eğilimli kalıplar için, kalıp dökümden önce kalıp iyi hazırlanmalıdır. Kalıbı ön ısıtma yapın, alevli püskürtme tabancasıyla ısıtın. Isıtma için alaşım sıvısının doğrudan kalıba dökülmesine izin verilmez ve ön ısıtma sıcaklığı 180~220ºC'de kontrol edilir. Ve düşük hızlı enjeksiyona başlamadan önce, kalıp boşluğuna kalıp macunu sürün ve basınçlı hava ile eşit şekilde üfleyin. Kalıp döküm kalıbı başına bir kez uygulanır ve test kalıp dökümü, kalıbın gerilmesini önlemek için çok etkili olan yaklaşık 20 kalıptır. Kalıp hala sıkışmışsa, kalıpta bir sorun var ve kalıbın onarılması gerekiyor demektir.
- Kalıbın hareketli kısmını veya küçük çekirdeği sökerken, boşluğa zarar vermemek için yalnızca yumuşak bakır, alüminyum, kurşun çubuklar veya lastik çekiçlerin hafifçe vurulmasına izin verilir.
- Belirli sayıda kalıba döküm yapıldıktan sonra, kalıp düzenli olarak gerilim giderme işlemine tabi tutulmalıdır.
Kalıp döküm yapışmasının birçok nedeni vardır ve yapışmayı çözmeye yönelik önlemler de farklıdır. Yapışmanın nedenleri dikkatli bir şekilde gözlemlenmeli ve analiz edilmeli ve ilgili önlemler hedefe yönelik bir şekilde alınmalıdır. Şu anda, yapışma olgusunun oluşum mekanizmasına ilişkin araştırmalar, henüz nitel analiz aşamasındadır. Farklı alaşım malzemeleri farklı yapışma eğilimleri gösterir; nicel teorik araştırma sonuçlarının rehberliğinde daha etkili test yöntemlerinin bulunması gerekmektedir. , Daha fazla deneysel araştırma yapmak.
Sürekli yeni malzemelerin ve yeni proses teknolojilerinin ortaya çıkmasıyla, kalıp yapışması sorununu çözmek için yeni fikirler ve yeni yöntemler ve hatta yıkıcı yenilikçi teknolojiler, yapışmayı önlemeye dayanan mevcut geleneksel kuralları etkiliyor. Örneğin, Kuzey Amerika kalıp dökümü kendi geliştirdiği bir iyileştirme işlevine sahip kalıcı kalıp geliştiriyor ve hiçbir ayırıcı madde mevcut proses teknolojisinin gelecekte devrilmesine veya ortadan kaldırılmasına neden olabilir. Bu nedenle, bilimsel araştırmalarda sabrımızı korurken, istikrarlı ve istikrarlı bir şekilde gelişmiş kalıp döküm teknolojisini özümsemeye devam etmemiz gerekiyor, Çin'in kalıp dökümünde yeni bir sıçrama hemen köşede.
Minhe Basınçlı Döküm Şirketi Hassas ve demir dışı dökümlerin Özel üreticisidir. Ürünler arasında alüminyum ve çinko dökümler. Alüminyum dökümler 380 ve 383 dahil alaşımlarda mevcuttur. Spesifikasyonlar artı /- 0.0025 toleransları ve 10 lbs'lik maksimum kalıp ağırlığını içerir. Çinko döküm parçaları Zamak no gibi standart alaşımlarda mevcuttur. 3, Zamak no. 5 & Zamak no. 7 & ZA-8 & ZA-27 gibi hibrit alaşımlar. Spesifikasyonlar arasında artı /- 0.001 tolerans ve 4.5 lb'lik maksimum kalıplama ağırlığı bulunur.
Lütfen yeniden basım için bu makalenin kaynağını ve adresini saklayın: Yapışkan Küf Problemi ile Kalıp Ayırıcı İlişkisi
Minhe Basınçlı Döküm Şirketi kaliteli ve yüksek performanslı Döküm Parçaları üretmeye ve sağlamaya adamıştır (metal döküm parça yelpazesi esas olarak şunları içerir: İnce Duvarlı Döküm,Sıcak Kamara Basınçlı Döküm,Soğuk Oda Döküm), Yuvarlak Servis (Döküm Servisi,Cnc İşleme,Kalıp yapımı,Yüzey İşleme).Herhangi bir özel Alüminyum döküm, magnezyum veya Zamak/çinko döküm ve diğer döküm gereksinimleri bizimle iletişime geçebilirsiniz.
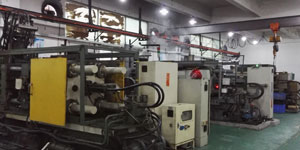
ISO9001 ve TS 16949 kontrolünde, tüm işlemler yüzlerce gelişmiş basınçlı döküm makinesi, 5 eksenli makine ve blasterlerden Ultra Sonic yıkama makinelerine kadar diğer tesisler aracılığıyla gerçekleştirilir. Müşterinin tasarımını gerçeğe dönüştürmek için deneyimli mühendisler, operatörler ve müfettişlerden oluşan ekip.
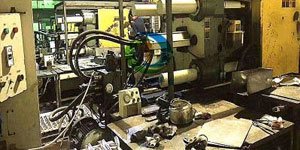
Dökümlerin sözleşmeli üreticisi. Yetenekler, 0.15 lbs'den başlayan soğuk oda alüminyum döküm parçaları içerir. 6 lbs'ye kadar, hızlı değişim kurulumu ve işleme. Katma değerli hizmetler arasında polisaj, titreşim, çapak alma, kumlama, boyama, kaplama, kaplama, montaj ve kalıplama yer alır. Çalışılan malzemeler arasında 360, 380, 383 ve 413 gibi alaşımlar bulunur.
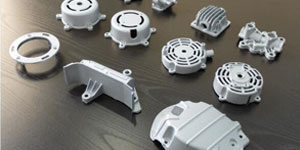
Çinko pres döküm tasarım yardımı/eşzamanlı mühendislik hizmetleri. Hassas çinko dökümlerin özel üreticisi. Minyatür dökümler, yüksek basınçlı dökümler, çok kızaklı kalıp dökümleri, geleneksel kalıp dökümleri, birim kalıp ve bağımsız kalıp dökümleri ve boşluklu sızdırmaz dökümler üretilebilir. Dökümler, +/- 24 inç toleransta 0.0005 inç'e kadar uzunluk ve genişliklerde üretilebilir.
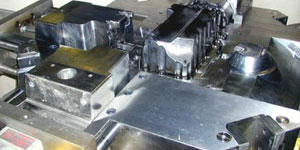
ISO 9001: 2015 sertifikalı döküm magnezyum üreticisi, Yetenekler arasında 200 ton sıcak odaya ve 3000 ton soğuk odaya kadar yüksek basınçlı magnezyum kalıp dökümü, takım tasarımı, cilalama, kalıplama, işleme, toz ve sıvı boyama, CMM özelliklerine sahip tam kalite güvencesi bulunur , montaj, paketleme ve teslimat.
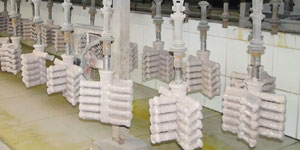
ITAF16949 sertifikalı. Ek Döküm Hizmeti Dahil yatırım dökümleri,kum dökümü,Yerçekimi Döküm, Kayıp Köpük Döküm,Savurma döküm,Vakumlu Döküm,Kalıcı Kalıp Döküm,.Yetenekler arasında EDI, mühendislik yardımı, katı modelleme ve ikincil işleme yer alır.
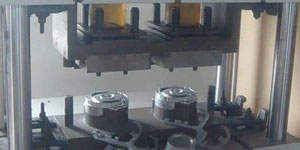
Döküm Endüstrileri Arabalar, Bisikletler, Uçaklar, Müzik aletleri, Deniz Araçları, Optik cihazlar, Sensörler, Modeller, Elektronik cihazlar, Muhafazalar, Saatler, Makineler, Motorlar, Mobilya, Mücevher, Jigler, Telekom, Aydınlatma, Tıbbi cihazlar, Fotoğraf cihazları, Robotlar, Heykeller, Ses ekipmanları, Spor ekipmanları, Aletler, Oyuncaklar ve daha fazlası.
Bundan sonra ne yapmanıza yardımcı olabiliriz?
∇ Ana Sayfaya Git Çin Döküm
→Döküm Parçaları-Ne yaptığımızı öğren.
→ Hakkında İlgili İpuçları Pres Döküm Hizmetleri
By Minghe Döküm Üreticisi |Kategoriler: Faydalı Makaleler |Malzeme Etiketler: Alüminyum Döküm, Çinko Döküm, Magnezyum Döküm, Titanyum Döküm, Paslanmaz Çelik Döküm, Pirinç Döküm,Bronz Döküm,Döküm Videosu,Tarihçe,Alüminyum Döküm |Yorumlar Kapalı