Kalıp Deformasyonunun Üç Anahtar Faktörü
Şu anda kalıp imalatında, karmaşık kalıp işleme ve ısıl işlem deformasyonu sorunlarını daha iyi çözmek için elektrik deşarjlı işleme, form taşlama, tel kesme vb. gibi yeni teknolojiler uygulanmaktadır. Ancak, bu yeni süreçler çeşitli kısıtlamalar nedeniyle henüz yaygın olarak kullanılmamıştır. Bu nedenle kalıbın ısıl işlem deformasyonunun nasıl azaltılacağı hala çok önemli bir konudur.
Genel olarak, kalıplar yüksek hassasiyet gerektirir. Isıl işlemden sonra işlenmesi ve düzeltilmesi elverişsiz hatta imkansızdır. Bu nedenle ısıl işlemden sonra yapı ve performans gerekliliklere ulaşmış olsa bile deformasyon tolerans dışında ise kurtarılamayacağı için yine de hurdaya ayrılacaktır. Sadece üretimi etkilemekle kalmaz, aynı zamanda ekonomik kayıplara da neden olur.
Isıl işlem deformasyonunun genel yasası burada tartışılmamaktadır. Aşağıda, kalıp deformasyonunu etkileyen bazı faktörlerin kısa bir analizi yer almaktadır.
Kalıp malzemesinin ısıl işlem deformasyonuna etkisi
Malzemelerin ısıl işlem deformasyonu üzerindeki etkisi, çeliğin kimyasal bileşiminin ve orijinal yapının etkisini içerir.
Malzemenin kendisi açısından bakıldığında, ısıl işlem deformasyonu esas olarak bileşimin sertleşebilirlik ve Ms noktası üzerindeki etkisinden etkilenir.
Karbon takım çeliği, normal su verme sıcaklığında su ve yağ ile söndürüldüğünde, Ms noktasının üzerinde büyük bir termal stres oluşur; Ms noktasının altına soğutulduğunda, östenit martensite dönüşerek yapısal gerilime neden olur, ancak karbon takım çeliğinin zayıf sertleşebilirliği nedeniyle, yapısal gerilimin değeri büyük değildir. Ayrıca Ms puanı yüksek değil. Martensit dönüşümü gerçekleştiğinde, çeliğin plastisitesi zaten çok zayıftır ve plastik deformasyonun oluşması kolay değildir. Bu nedenle, termal stresin neden olduğu deformasyon özellikleri korunur ve kalıp boşluğu büzülme eğilimi gösterir. Bununla birlikte, su verme sıcaklığı arttırılırsa (>850°C), yapı stresi de öncü bir rol oynayabilir ve boşluk genişleme eğilimindedir.
9Mn2V, 9SiCr, CrWMn, GCr15 çeliği gibi düşük alaşımlı takım çelikleri ile kalıp yaparken, söndürme deformasyon yasası karbon takım çeliğine benzer, ancak deformasyon miktarı karbon takım çeliğinden daha küçüktür.
Yüksek karbon ve alaşım elementleri içeriği ve düşük Ms noktası nedeniyle Cr12MoV çeliği gibi bazı yüksek alaşımlı çelikler için, su verme işleminden sonra martenzit nedeniyle hacim genişlemesi üzerinde önemli bir etkiye sahip olan daha fazla tutulan ostenit vardır. Bu nedenle, söndürme sonrası deformasyon oldukça küçüktür. Genel olarak, havayla soğutma, havayla soğutma ve nitrat tuzu banyosu ile söndürme sırasında, kalıp boşluğu hafifçe genişleme eğilimindedir; söndürme sıcaklığı çok yüksekse, kalan östenit miktarı artacaktır. Boşluk da küçülebilir.
Kalıp, karbon yapısal çelikten (45 çelik gibi) veya bazı alaşımlı yapısal çelikten (40Cr gibi) yapılmışsa, yüksek Ms noktası nedeniyle, yüzey martensite dönüşmeye başladığında, çekirdek sıcaklığı hala daha yüksektir ve akma mukavemeti Düşük ve belirli bir plastisite derecesine sahiptir. Yüzeyin çekirdeğe olan anlık gerilme dokusu gerilimi, çekirdeğin akma mukavemetini kolayca aşar ve boşluk şişme eğilimi gösterir.
Çeliğin orijinal yapısı da söndürme deformasyonu üzerinde belirli bir etkiye sahiptir. Burada atıfta bulunulan "çeliğin birincil yapısı", çelikteki kapanımların seviyesini, bantlı yapının seviyesini, bileşenlerin ayrılma derecesini, serbest karbürlerin dağılımının yönlülüğünü, vb. ve ayrıca farklı yapıları içerir. Farklı ön ısıl işlemlerden (perlit, temperli sorbit, temperli troostit vb.) Kalıp çeliği için ana husus, karbürlerin ayrılması, karbürlerin şekli ve dağılımıdır.
Yüksek karbonlu ve yüksek alaşımlı çelikte (Cr12 çelik gibi) karbür ayrışmasının su verme deformasyonu üzerindeki etkisi özellikle açıktır. Karbür segregasyonu, ostenit durumuna ısıtıldıktan sonra çeliğin bileşimsel homojensizliğine neden olduğundan, farklı bölgelerdeki Ms noktaları yüksek veya düşük olacaktır. Aynı soğutma koşulları altında, önce ostenitin martensite dönüşümü gerçekleşir ve dönüştürülmüş martensitin özgül hacmi karbon içeriğine bağlı olarak değişir ve hatta bazı düşük karbonlu ve düşük alaşımlı bölgeler martensit yoktur (ancak beynit, troostite, vb.), hepsi su verme işleminden sonra parçaların düzensiz deformasyonuna neden olur.
Farklı karbür dağılım biçimlerinin (granüler veya lifli biçimde dağılmış) matrisin genleşmesi ve büzülmesi üzerinde farklı etkileri vardır, bu da ısıl işlemden sonraki deformasyonu da etkileyecektir. Genel olarak, boşluk, karbür elyafların yönü boyunca genişler ve daha belirgindir, ancak elyafa dik yön azalır, ancak önemli değildir. Bazı fabrikalar bunun için özel düzenlemeler yapmıştır. Kavitenin deformasyonunu azaltmak için kavitenin yüzeyi karbür fiberin yönüne dik olmalıdır. Karbür taneli olduğunda Eşit olarak dağıtıldığında, boşluk düzgün genişleme ve büzülme gösterir.
Ek olarak, yapının son ısıl işlemden önceki durumu da deformasyon üzerinde belirli bir etkiye sahiptir. Örneğin, küresel perlitin orijinal yapısı, söndürmeden sonra pul pul perlitten daha küçük bir deformasyon eğilimine sahiptir. Bu nedenle, katı deformasyon gereksinimleri olan kalıplar, genellikle kaba işlemeden sonra su verme ve temperleme işlemine ve ardından bitirme ve son ısıl işleme tabi tutulur.
Kalıp geometrisinin deformasyona etkisi
Kalıp geometrisinin ısıl işlem deformasyonu üzerindeki etkisi aslında termal stres ve organizasyonel stres yoluyla çalışır. Kalıbın şekli çeşitli olduğu için, ondan tam deformasyon yasasını özetlemek hala zordur.
Simetrik kalıplar için, boşluğun deformasyon eğilimi, boşluk boyutuna, şekil boyutuna ve yüksekliğine göre düşünülebilir. Kalıbın duvarı ince ve yüksekliği küçük olduğunda, söndürmek daha kolaydır. Bu zamanda, doku stresinin öncü bir rol oynaması mümkündür. Bu nedenle, boşluk genellikle şişme eğilimindedir. Aksine et kalınlığı ve yüksekliği fazla ise sertleşmesi kolay değildir. Şu anda, termal stres öncü bir rol oynayabilir. Bu nedenle, boşluk genellikle küçülme eğilimindedir. Burada bahsedilenler genel bir eğilimdir. Üretim pratiğinde, parçanın spesifik şeklini, çelik kalitesini ve ısıl işlem sürecini vb. dikkate almak ve tecrübeyi uygulama yoluyla sürekli olarak özetlemek gerekir. Gerçek üretimde, kalıbın dış boyutları genellikle ana çalışma boyutları değildir ve deformasyon taşlama vb. ile düzeltilebilir, bu nedenle yukarıdaki ana analiz boşluğun deformasyon eğilimidir.
Asimetrik kalıpların deformasyonu aynı zamanda termal stres ve doku stresinin birleşik etkilerinin bir sonucudur. Örneğin, ince duvarlı ve ince kenarlı bir kalıp için, kalıp duvarı ince olduğu için, söndürme sırasında iç ve dış arasındaki sıcaklık farkı küçüktür, bu nedenle termal stres küçüktür; ancak söndürülmesi kolaydır ve yapı stresi büyüktür, bu nedenle deformasyon boşluğu genişletme eğilimindedir.
Kalıbın deformasyonunu azaltmak için, ısıl işlem departmanı, enine kesit boyutunda büyük farklılıklar olan kalıp yapılarından, simetrik kalıp şekillerinden ve karmaşık yapılar için bölünmüş yapılardan kaçınmak gibi kalıp tasarımını iyileştirmek için kalıp tasarım departmanı ile birlikte çalışmalıdır. kalıplar.
Kalıp şekli değiştirilemediğinde, deformasyonu azaltmak için başka önlemler alınabilir. Bu önlemlerin genel düşüncesi, her bir parçanın eşit şekilde soğutulabilmesi için soğutma koşullarını iyileştirmektir; ayrıca, parçaların su verme deformasyonunu sınırlamak için çeşitli zorunlu önlemlere de yardımcı olunabilir. Örneğin, proses deliklerinin eklenmesi, her parçanın eşit şekilde soğutulması için bir ölçüdür, yani kalıbın bazı kısımlarında delikler açmak, böylece deformasyonu azaltmak için kalıbın her bir parçası eşit şekilde soğutulabilir. Ayrıca, iç delik ile dış tabaka arasındaki soğutma farkını artırmak ve boşluğu küçültmek için söndürmeden sonra genişlemesi kolay olan kalıbın çevresine asbest ile sarılabilir. Kalıp üzerinde tutma nervürleri veya takviye nervürleri, deformasyonu azaltmak için bir başka zorunlu önlemdir. Özellikle şişme boşluklu kalıplar ve genişletilmesi veya büzülmesi kolay çentikli kalıplar için uygundur.
Isıl işlemin kalıp deformasyonuna etkisi
1. Isıtma hızının etkisi
Genel olarak konuşursak, söndürme ısıtması sırasında, ısıtma hızı ne kadar hızlı olursa, kalıpta deformasyona ve çatlamaya neden olması muhtemel olan, kalıpta üretilen termal stres o kadar büyük olur. Özellikle alaşımlı çelikler ve yüksek alaşımlı çelikler için, zayıf ısı iletkenlikleri nedeniyle ön ısıtmaya özel dikkat gösterilmelidir. Karmaşık şekillere sahip bazı yüksek alaşımlı kalıplar için birden fazla ön ısıtma adımının uygulanması gerekir. Bununla birlikte, bireysel durumlarda, hızlı ısıtma bazen deformasyonu azaltabilir. Bu sırada, merkez "soğuk" kalırken, kalıbın sadece yüzeyi ısıtılır, bu nedenle doku stresi ve termal stres buna bağlı olarak azalır ve çekirdeğin deformasyon direnci daha fazladır. , Böylece, bazı fabrika deneyimlerine göre, delik hatvesi deformasyonunu çözmek için kullanılan söndürme deformasyonunu azaltmak belirli bir etkiye sahiptir.
2. Isıtma sıcaklığının etkisi
Söndürme ısıtma sıcaklığı, malzemenin sertleşebilirliğini etkiler ve aynı zamanda östenitin bileşimini ve tane boyutunu etkiler.
- (1) Sertleşebilirlik açısından, yüksek ısıtma sıcaklığı termal gerilimi artıracak, ancak aynı zamanda sertleşebilirliği artıracaktır, bu nedenle yapısal gerilim de artar ve kademeli olarak hakim olur. ., genel su verme sıcaklığında söndürüldüğünde, iç çap küçülme eğilimi gösterir, ancak su verme sıcaklığı ≥8°C'ye yükseltilirse, sertleşebilirlik artar ve yapısal stres giderek baskın hale gelir, Böylece iç çap bir eğilim gösterebilir. kabarmak.
- (2) Östenit bileşimi açısından, söndürme sıcaklığındaki artış, östenit karbon içeriğini ve söndürmeden sonra martensitin kareliğini (artan özgül hacim) arttırır, bu da söndürmeden sonraki hacmi arttırır.
- (3) Ms noktası üzerindeki etkiye daha yakından bakıldığında, su verme sıcaklığı ne kadar yüksek olursa, östenit taneleri o kadar iri olur, bu da parçaların deformasyonunu ve çatlama eğilimini artıracaktır.
Özetle, tüm çelik kaliteleri, özellikle bazı yüksek karbonlu orta ve yüksek alaşımlı çelikler için, su verme sıcaklığı, kalıbın su verme deformasyonunu açıkça etkileyecektir. Bu nedenle, söndürme ısıtma sıcaklığının doğru seçimi çok önemlidir.
Genel olarak konuşursak, çok yüksek bir söndürme ısıtma sıcaklığı seçmek deformasyon için iyi değildir. Performansı etkilememek için her zaman daha düşük bir ısıtma sıcaklığı kullanılır. Bununla birlikte, söndürmeden sonra daha fazla östenit kalıntısı olan bazı çelik kaliteleri için (Cr12MoV, vb. gibi), kalan östenit miktarı, kalıbın deformasyonunu ayarlamak için ısıtma sıcaklığı ayarlanarak da ayarlanabilir.
3. Söndürme soğutma hızının etkisi
Genel olarak, soğutma hızının Ms noktasının üzerine çıkarılması, termal stresi önemli ölçüde artıracaktır ve bunun sonucunda termal stresin neden olduğu deformasyon artma eğilimi gösterir; Ms noktasının altında soğuma hızının artması, esas olarak doku stresinin neden olduğu deformasyonun Artma eğilimine girmesine neden olur.
Farklı çelik kaliteleri için, Ms noktalarının farklı yükseklikleri nedeniyle, aynı su verme ortamı kullanıldığında, farklı deformasyon eğilimleri vardır. Aynı çelik kalitesi için, farklı su verme ortamları kullanılıyorsa, farklı soğutma kapasiteleri nedeniyle farklı deformasyon eğilimleri de vardır.
Örneğin, karbon takım çeliğinin Ms noktası nispeten düşüktür, bu nedenle su soğutması kullanıldığında, termal stresin etkisi baskın olma eğilimindedir; soğutma kullanıldığında, yapısal stres geçerli olabilir.
Gerçek üretimde, kalıplar derecelendirildiklerinde veya derecelendirildiklerinde-östemperlendiğinde genellikle tam olarak söndürülmezler, bu nedenle ısıl stres genellikle boşluğu küçültme eğiliminde olan ana etkidir. Bununla birlikte, termal stres şu anda çok büyük olmadığı için, Bu nedenle, toplam deformasyon nispeten küçüktür. Su-yağ çift-sıvı su verme veya yağ su verme kullanılırsa, neden olan termal stres daha fazladır ve boşluk büzülmesi artacaktır.
4. Temperleme sıcaklığının etkisi
Temperleme sıcaklığının deformasyon üzerindeki etkisi, esas olarak temperleme işlemi sırasında yapının dönüşümünden kaynaklanır. Temperleme işlemi sırasında "ikincil söndürme" fenomeni meydana gelirse, tutulan ostenit martensite dönüştürülür ve üretilen martensitin özgül hacmi, kalıp boşluğunun genişlemesine neden olacak şekilde tutulan ostenitinkinden daha büyüktür; Cr12MoV gibi bazı yüksek alaşımlı takım çelikleri için, ana gereksinim olarak kırmızı sertlik gerektiren yüksek sıcaklıkta su verme kullanılır. Çoklu temperleme yapıldığında, temperleme her yapıldığında hacim bir kez genişler.
Diğer sıcaklık bölgelerinde temperlenirse, söndürülmüş martenzitin temperlenmiş martensite (veya temperlenmiş sorbit, temperlenmiş troostite, vb.) dönüşmesi nedeniyle özgül hacim azalır ve bu nedenle boşluk büzülme eğilimi gösterir.
Ayrıca temperleme sırasında kalıptaki artık gerilmenin gevşemesi de deformasyonu etkiler. Kalıp su verildikten sonra, yüzey çekme gerilimi durumundaysa, temperlemeden sonra boyut artacaktır; tam tersine, yüzey bir basınç gerilimi durumundaysa büzülür. Ancak örgütsel dönüşüm ve stres rahatlamasının iki etkisinden birincisi esastır.
Lütfen yeniden basım için bu makalenin kaynağını ve adresini saklayın: Kalıp Deformasyonunun Üç Anahtar Faktörü
Minhe Basınçlı Döküm Şirketi kaliteli ve yüksek performanslı Döküm Parçaları üretmeye ve sağlamaya adamıştır (metal döküm parça yelpazesi esas olarak şunları içerir: İnce Duvarlı Döküm,Sıcak Kamara Basınçlı Döküm,Soğuk Oda Döküm), Yuvarlak Servis (Döküm Servisi,Cnc İşleme,Kalıp yapımı,Yüzey İşleme).Herhangi bir özel Alüminyum döküm, magnezyum veya Zamak/çinko döküm ve diğer döküm gereksinimleri bizimle iletişime geçebilirsiniz.
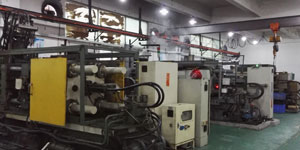
ISO9001 ve TS 16949 kontrolünde, tüm işlemler yüzlerce gelişmiş basınçlı döküm makinesi, 5 eksenli makine ve blasterlerden Ultra Sonic yıkama makinelerine kadar diğer tesisler aracılığıyla gerçekleştirilir. Müşterinin tasarımını gerçeğe dönüştürmek için deneyimli mühendisler, operatörler ve müfettişlerden oluşan ekip.
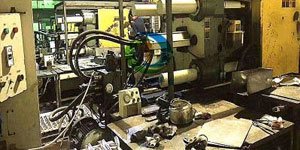
Dökümlerin sözleşmeli üreticisi. Yetenekler, 0.15 lbs'den başlayan soğuk oda alüminyum döküm parçaları içerir. 6 lbs'ye kadar, hızlı değişim kurulumu ve işleme. Katma değerli hizmetler arasında polisaj, titreşim, çapak alma, kumlama, boyama, kaplama, kaplama, montaj ve kalıplama yer alır. Çalışılan malzemeler arasında 360, 380, 383 ve 413 gibi alaşımlar bulunur.
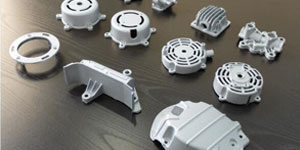
Çinko pres döküm tasarım yardımı/eşzamanlı mühendislik hizmetleri. Hassas çinko dökümlerin özel üreticisi. Minyatür dökümler, yüksek basınçlı dökümler, çok kızaklı kalıp dökümleri, geleneksel kalıp dökümleri, birim kalıp ve bağımsız kalıp dökümleri ve boşluklu sızdırmaz dökümler üretilebilir. Dökümler, +/- 24 inç toleransta 0.0005 inç'e kadar uzunluk ve genişliklerde üretilebilir.
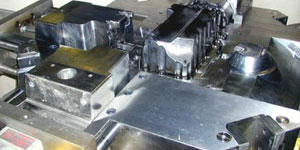
ISO 9001: 2015 sertifikalı döküm magnezyum üreticisi, Yetenekler arasında 200 ton sıcak odaya ve 3000 ton soğuk odaya kadar yüksek basınçlı magnezyum kalıp dökümü, takım tasarımı, cilalama, kalıplama, işleme, toz ve sıvı boyama, CMM özelliklerine sahip tam kalite güvencesi bulunur , montaj, paketleme ve teslimat.
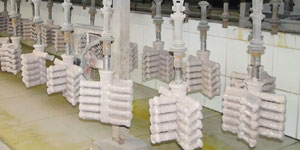
ITAF16949 sertifikalı. Ek Döküm Hizmeti Dahil yatırım dökümleri,kum dökümü,Yerçekimi Döküm, Kayıp Köpük Döküm,Savurma döküm,Vakumlu Döküm,Kalıcı Kalıp Döküm,.Yetenekler arasında EDI, mühendislik yardımı, katı modelleme ve ikincil işleme yer alır.
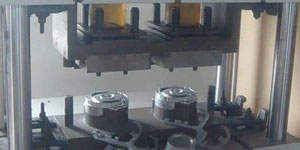
Döküm Endüstrileri Arabalar, Bisikletler, Uçaklar, Müzik aletleri, Deniz Araçları, Optik cihazlar, Sensörler, Modeller, Elektronik cihazlar, Muhafazalar, Saatler, Makineler, Motorlar, Mobilya, Mücevher, Jigler, Telekom, Aydınlatma, Tıbbi cihazlar, Fotoğraf cihazları, Robotlar, Heykeller, Ses ekipmanları, Spor ekipmanları, Aletler, Oyuncaklar ve daha fazlası.
Bundan sonra ne yapmanıza yardımcı olabiliriz?
∇ Ana Sayfaya Git Çin Döküm
→Döküm Parçaları-Ne yaptığımızı öğren.
→ Hakkında İlgili İpuçları Pres Döküm Hizmetleri
By Minghe Döküm Üreticisi |Kategoriler: Faydalı Makaleler |Malzeme Etiketler: Alüminyum Döküm, Çinko Döküm, Magnezyum Döküm, Titanyum Döküm, Paslanmaz Çelik Döküm, Pirinç Döküm,Bronz Döküm,Döküm Videosu,Tarihçe,Alüminyum Döküm |Yorumlar Kapalı