Pres Döküm Yapışkan Kalıp Hatalarını Çözmek İçin Somut Önlemler
1 Pres dökümlerin yapışmasının nedenleri
Kalıp kusurlarının dökümlere yapışmasının tehlikeleri şunlardır: kalıp dökümleri kalıba yapıştığında, daha hafif yüzey pürüzlüdür, bu da görünümün pürüzlülüğünü etkiler; ağır döküm yüzeyi soyulur, etten, gerilmelerden ve çatlaklardan yoksundur ve ayrıca dökümlerin sızıntı yapmasına neden olarak dökümlere neden olabilir. Kalıp döküm yapışmasının birçok olgusu vardır ve yapışmanın temel nedenleri aşağıdaki gibidir.
1.1 Kalıp döküm alaşımının ve kalıp çeliğinin afinitesi
Kalıp döküm alaşımı ile kalıp çeliği arasındaki afinite ne kadar büyük olursa, eritilmesi ve birbirine bağlanması o kadar kolay olur. Döküm alaşımı kalıp duvarına bağlandıktan sonra, daha fazla kalıptan çıkma direnci olacak ve kalıptan çıkarma sırasında döküm gerilecektir. Dökümün yapışan kısmında (not: karbon tortusundan ayırt edilmelidir) pürüzlü yüzey, soyulma veya malzeme eksikliği gibi çizim izleri olduğunu ve şiddetli yapışma durumunda dökümün yırtılacağını ve hasar göreceğini görsel olarak gözlemleyin. Kalıp boşluğunun yüzeyi, lamine döküm alaşımına görsel olarak yapıştırılmıştır ve renk beyazdır.
Döküm alaşım sıvısının enjeksiyonu veya akışı kalıp duvarına veya maçaya çarptıktan sonra, kalıp duvarı veya maçasının sıcaklığı artar. Yüksek sıcaklıklarda, kalıp duvarının alaşımlı sıvısı ve kalıp çeliği erir ve karşılıklı yapışmayı sağlamak için birbirine kaynak yapar. Alaşım sıvı sıcaklığı ne kadar yüksekse, enjeksiyon hızı o kadar yüksek, kalıp sıcaklığı o kadar yüksek ve kalıp sertliği ne kadar düşükse, alüminyum alaşımlı sıvı ile kalıp çeliği arasındaki afinite ne kadar yüksek olursa, erime ve kaynak yapışması o kadar olasıdır. Kalıp döküm alaşımına yapışan kalıp yüzeyi kalıptan çıkarıldığında, boşluk yüzeyi ve döküm yüzeyi sıkılır ve yırtılır, bu da dökümün yüzeyini yırtar ve döküm yüzeyi yapışkan kalıp gerilimi gibi görünecektir.
Döküm alaşım sıvısının iç kızaktaki doldurma hızı ne kadar yüksek olursa, erimiş metal akışının kalıp duvarı üzerindeki etkisi o kadar şiddetli olur. Erimiş metal doğrudan çekirdeğe veya duvara çarpar ve çarpma kuvveti ısı enerjisine dönüştürülür. Sadece alaşım sıvısının sıcaklığı artmayacak, aynı zamanda etkilenen kısımdaki kalıbın sıcaklığı da çok yükselecek ve bu da alüminyum alaşımlı sıvı ile kalıp çeliği arasındaki afiniteyi büyük ölçüde artıracaktır. Bu nedenle, kalıp yapışmasının, alaşım sıvısının yüksek hızlı etkisine maruz kalan kalıptaki yolluk kısmında meydana gelmesi daha olasıdır. Sabit kalıbın kenarına çarparsa, dökümün sabit kalıbın yanındaki paketleme kuvveti artar.
Kalıbın sertliği yetersizdir ve kalıptan çıkarma sırasında kalıp yüzeyi kalıp döküm alaşımı tarafından sıkıştırılır ve deforme olur veya kalıp çekirdeği bükülür ve deforme olur, böylece kalıbın dökümün kalıptan çıkarılmasına karşı direncini arttırır.
Kalıp malzemelerinin yanlış kullanımı, kalıp sıcaklığı yüksek olduğunda, kalıp döküm alaşımı kalıbın yüzeyine kolayca yapışır.
1.2 Kalıptan çıkarma açısı
Kalıptan çıkarma eğimi çok küçük (veya kalıptan çıkarma eğimi yok veya ters kalıptan çıkarma eğimi yok), kalıbın kenarı düzgün değil (erozyon, ezilme, kusur vb.), yüzey pürüzlü, vb. ve döküm engelleniyor kalıptan çıkarma yönü. Döküm kalıptan çıkarıldığında, dökümün yüzeyi kalıp tarafından gerilir ve dökümün yüzeyi, kalıbın açılma yönü boyunca doğrusal gerilme işaretleri gösterir, yani, dökümün derin boşluğunun başlangıcındaki izler geniş ve derin, kalıbın ucundaki izler giderek küçülür ve hatta kaybolur. Tüm yüzü süzün.
- (1) Kalıp tasarımı ve imalatı doğru değil ve sabit kalıp boşluğunun veya maça şekillendirme yüzeyinin kalıptan çıkarma eğimi çok küçük veya ters bir eğime sahip, bu da kalıptan çıkarmaya karşı döküm direncini çok büyük yapıyor. Dökümde kalıptan çıkarma eğimi gerektirmeyen parçalar için, kalıptan çıkarma eğimini yapmak için döküm için bir işleme payı bırakmak ve daha sonra dökümün kalıptan çıkarma eğimi olmayan parçaların bitirilmesine izin vermek en iyisidir.
- (2) Kalıp göbeği veya kalıp duvarındaki ezilme deformasyonu ve boşluğun yanındaki çıkıntı, dökümün kalıptan çıkarılmasını etkiler ve şekillendirme yüzeyindeki çizikler veya kalıp çatlaması da dökümün kalıptan çıkarılmasını etkiler. .
Kalıbın sabit kalıplama yüzeyi çok pürüzlü veya işleme ve üretim izleri var, yeterince pürüzsüz değil veya işleme ve cilalama izlerinin hatları kalıptan çıkarma yönü ile uyumsuz veya kalıptan çıkarma yönündeki düzlük zayıf, bu tür kötü yüzeyler nedeniyle artacaktır Kalıptan çıkarma direnci, dökümün kalıptan ayrılmasını engeller ve döküm yüzeyinde cila veya çizik izleri olmasına neden olur. Bu tür çizikler, kalıptan çıkarma yönünde doğrusal oluklardır, sığ olanlar 0.1 mm'den küçüktür ve derin olanlar yaklaşık 0.3 mm'dir.
1.3 Dökümün kalıba sıkılığı
Dökümün genel veya yerel büzülmesi, kalıp üzerinde çok fazla kenetleme kuvvetine sahiptir veya kıstırma kuvvetinin dağılımı dengesiz ve mantıksızdır. Bu sırada kalıbın yapışması nedeniyle döküm deforme olacak, çatlayacak veya kırılacak ve hatta döküm sabit kalıba yapışacaktır. Veya dökümün hareketli kalıbın üst kısmına yapışıp dışarı çıkamaması gibi bir durum olabilir.
- (1) Dökümün sabit kalıba olan toplam veya kısmi paketleme kuvveti, hareketli kalıba gelen paketleme kuvvetinden daha büyüktür ve kalıp açıldığında döküm sıkışmış kalacaktır.
- (2) Kalıptan çıkarma sırasında, hareketli ve sabit kalıplar üzerindeki dökümün her bir parçasının sıkma kuvveti eşit değilse, dışarı çekildiğinde döküm bükülecek, eğrilecek ve eğrilecektir ve dökümün bir parçası olan kısım. sabit kalıp üzerindeki büyük sıkma kuvveti etkilenecektir. Sabit kalıba yapışabilir.
- (3) Sabit kalıbın sıcaklığı çok düşükse veya hareketli kalıbın sıcaklığı çok yüksekse, döküm büzüldüğünde sabit kalıbın paketleme kuvveti hareketli kalıbınkinden daha büyük olacaktır.
- (4) Kalıp ayırıcı madde konsantrasyonu çok düşük, kalıp ayırıcının kalıp ayırıcı performansı iyi değil, sabit kalıp üzerine püskürtülen kalıp ayırıcı yerinde değil ve kalıp ayırıcı miktarı yetersiz, bu da kalıbı etkileyecektir. döküm performansını serbest bırakın. Sıcak kalıp sırasında sabit kalıba çok fazla boya püskürtülürse, sabit kalıbın sıcaklığının hızla artması zorlaşır. Döküm soğuyup küçüldükten sonra sabit kalıp tarafında sıkma kuvveti hareketli kalıba göre daha fazla artacaktır.
- (5) Kalıp yapışması olgusu da vardır: kalıp döküm üretiminin ilk periyodunda, yani sıcak kalıp düşük hızda enjekte edildiğinde, kalıp döküm alaşım sıvısının akışkanlığı nedeniyle hızla düşecektir. düşük kalıp sıcaklığı, doldurma ile sonuçlanır Boşlukta erimiş metal oluşumu çok eksiktir, şekillendirilmiş dökümün gücü çok düşüktür ve dökümün çeşitli parçaları arasındaki bağlantı çok zayıftır. Döküm kalıptan çıkarıldığında, daha fazla sıkma kuvvetine sahip parça diğer parçalarla kolayca kırılır. Ayrılmış ve kalıba sıkışmış. Özellikle sabit kalıbın yan tarafında dökümü çıkarmak için ejektör pimi bulunmadığından sabit kalıba yapışması daha kolaydır.
Döküm sırasında her seferinde meydana gelen yapışma olayı için, oluşum nedenleri detaylı olarak analiz edilmelidir. Örneğin, kalıp döküm sırasında döküm sabit kalıba yapışıyorsa, dökümün sabit kalıba aşırı sıkma kuvvetinin nedenini kontrol etmek gerekir; dökümün sabit kalıp tarafının görünümünü kontrol edin, kalıptan çıkarma yönünü takip edin ve döküm yüzeyinde kalıp izleri var. Yapışan kalıp ciddi şekilde çizildiğinde veya çizildiğinde, döküm parçasının veya tüm dökümün boşlukta çıkmamasına neden olacak büyük bir kalıptan çıkma direnci olacaktır ve döküm sıkışmış kalacak ve yapışmaya neden olacaktır; Şiddetli durumlarda, sadece döküm parçalanmaz ve hasar görmez. Kalıbın çekirdeğinde ve boşluğunda da gerilmeler, çatlaklar ve kırılmalar meydana gelebilir. Kalıp dökümlerinin yapışma fenomeni en çok alüminyum alaşımlarında görülür. Kalıp dökümlerinin yapışma kusurlarını çözmek için özel önlemler aşağıdaki gibidir.
2 Dökümlerin sabit kalıba yapışmasını önlemek için önlemler
2.1 Dökümlerin döküm kalıplarında sabit kalıplara yapışmasını önlemek için önlemler
Yeni üretilen kalıbın deneme kalıbında veya kalıp döküm üretimi sıcak kalıbı başlattığında, kalıp dökümü yapışması olgusu sıklıkla meydana gelir. Kalıp döküm işlemi işlemi normal olduğunda, dökümlerin yapışmasının ana nedeni kalıp döküm işlemi değil, döküm yapı tasarımı, kalıp tasarımı veya imalat sorunu olmalıdır. Kalıp döküm işlemi ve püskürtme hata ayıklaması giderilebilse de, iyileştirici etki geneldir ve çok kararlı değildir ve döküm yapışması olgusu yine de meydana gelecektir.
Döküm sabit kalıba yapışmaya meyilliyse, kalıp dökümden önce iyice ısıtılmalı ve düşük hızlı enjeksiyona başlamadan önce kalıp boşluğu yapışma önleyici kalıp macunu ve basınçlı hava ile kaplanmalıdır. Eşit şekilde üfleyin, her bir kalıp döküm kalıbı için bir kez uygulayın, yaklaşık 20 kalıba dökmeyi deneyin, eğer kalıp hala sabitse, bu, kalıbın bir sorunu olduğu ve onarılması gerektiği anlamına gelir.
Tasarlanan dökümler için, dökümün sabit kalıba sıkıştırma kuvvetinin hareketli kalıba sıkıştırma kuvvetinden daha büyük olduğu doğrudur. Dökümü çıkarmak için dökümün sabit kalıbın kenarına yerleştirilmesine ve döküm yüzeyinin sabit kalıbın kenarına gelmesine izin vermek gerekir. Çıkarma işaretlerini bırakın veya çıkarma işaretlerinin çıkarılmasını kolaylaştırın. Bu şekilde kalıp tasarımı yapılırken dökümün fırlatma mekanizması sabit kalıbın yan tarafında tasarlanmalıdır.
Hareketli ve sabit kalıpların paketleme kuvvetinin hesaplanmasına dikkat ediniz. Sabit kalıbın paketleme kuvveti hareketli kalıbın paketleme kuvvetinden daha büyük olan dökümler için veya sabit kalıbın paketleme kuvveti ve hareketli kalıbınkine benzer hareketli kalıp ile dökümler için, yapıştırmak mümkündür. sabit kalıp hareketli kalıbın dökümüne yapışabilir. Döküm veya kalıbı tasarlarken, döküm veya kalıbın yapısını, taslak açısını, yüzey pürüzlülüğünü vb. Değiştirmek ve hareketli kalıbın döküm kuvvetini sabit sıkma kuvvetinden daha büyük yapmaya çalışmak gerekir. kalıba dökmek.
Sabit kalıbın bir tarafında nispeten büyük bir paketleme kuvvetine sahip dökümler için, yeni bir kalıp tasarlarken, ayırma yüzeyi mümkün olduğunca sabit kalıba eğimli tarafta seçilmeli ve dökümler yerleştirilmelidir. dökümlerin eşleşmesini artırmak için mümkün olduğunca hareketli kalıp boşluğu. Hareketli kalıbın sıkma kuvveti. Sabit kalıp üzerindeki sıkma kuvvetini azaltmak için, döküm tasarımcısı ile sabit kalıbın kalıptan çıkma eğiminin yeniden belirlenmesi ve sabit kalıbın kalıptan çıkma eğiminin mümkün olduğunca arttırılması gerekir; Sabit kalıp tarafında dökümü düzeltmeye veya artırmaya özellikle dikkat edin. Kalıbın kalıba yapışmasıyla gerilen parçanın kalıptan çıkma eğimi. Aynı zamanda, hareketli kalıbın kalıptan çıkarma eğimini uygun şekilde azaltın; ejektör piminin yanındaki hareketli kalıbın kalıptan çıkma eğimini düzeltmeye veya azaltmaya özellikle dikkat edin. Maçayı hareketli kalıba yerleştirmeye çalışın veya hareketli kalıbın bir tarafında maça uzunluğunu artırın.
Sabit kalıbın imalat ve cilalama sırasında kalıptan çıkarmayı etkileyen alt kesikler veya pürüzlü yüzeyler oluşturmasını önlemek gerekir; kalıp denemesinden sonra veya kalıp döküm işlemi sırasında, sabit kalıp boşluğunun deformasyonunu ezilme ve ezilmeden düzeltmek gerekir; alaşımı ortadan kaldırmak için cila veya kimyasal temizlik maddeleri kullanın Sabit kalıbın yüzeyindeki yapışma izleri ve kalıp üzerindeki alaşım yapışıklıkları zamanla giderilmezse, uzun bir süre sonra yapışma olayı daha da ciddileşecektir; sabit kalıp boşluğunun yan duvarının pürüzlü yüzeyini daha iyi parlatın. Ancak sabit kalıp bir ayna yüzeyine parlatıldıktan sonra, boyanın yapışması için elverişli değildir. Kalıp açıldığında, döküm ve kalıp arasında, kalıptan çıkarma direncini artıran sıkı bir vakum boşluğu oluşacaktır, bu nedenle sabit kalıp derin boşluğunun tabanı bir ayna yüzeyine parlatılamaz. . Nitrürlenmiş kalıplar için, yüzeydeki nitrürlenmiş tabakanın zarar görmemesi için cilalama dikkatli yapılmalıdır ve daha fazla cilalanmayı önlemek için kalıp daha fazla yapışacaktır.
Kızağın sabit kalıp üzerindeki etkisinin neden olduğu erozyon ve kalıp yapışma kusurlarını ortadan kaldırmak veya azaltmak için kalıp kızağını değiştirin, yolluğun konumunu, boyutunu ve doldurma akış yönünü uygun şekilde değiştirin. Örneğin:
- ①Erimiş metalin sabit kalıp boşluğu üzerindeki şiddetli etkisini en aza indirmek için erimiş alüminyumun dolum akış yönünü değiştirin. Çekirdek veya duvara eğik bakacak şekilde erimiş metalin doğrudan etkisini değiştirebilirsiniz;
- ②İç rayın kesit alanını uygun şekilde arttırın. İç yolluktaki erimiş metalin akış hızını azaltmak için;
- ③İç rayın konumunu değiştirin, iç rayı dökümün geniş ve kalın pozisyonunda yapın ve sabit kalıbın yan duvarındaki darbeden kaçının;
- ④Döküm Yönteminin derin boşluğunun altındaki beslemeyi almaya çalışın;
- ⑤Açık bir koşucu benimseyin, koşucunun çan ağzı enjeksiyon alanını genişletmek için boşluğa bakar;
- ⑥Kulağın darbe kısmı veya çekirdeği için, kalıbın yüzeyine elektrik uygulamak için bir tungsten karbür çubuk kaplama makinesi kullanılabilir.
Kıvılcım metalurjik yöntemi, tungsten karbür mikropartikül tabakasını püskürtür, metal tungsten partikülleri ve ana metal düşmez, bu da kalıp yüzeyinin yapışma önleyici özelliğini geliştirebilir, örneğin yüzeyde 2 ila 4 mikron kalınlığında bir kaplama biriktirmek gibi. kalıp döküm kalıbının ve sertliği HV4 000~4 500'e ulaşabilir ve çalışma sıcaklığı 800℃'ye ulaşabilir.
Dökümü hareketli kalıbın yan tarafına çekmek için, ejektör çubuğunun başından kama şeklinde bir dikenli kanca tamir edilebilir (kanca uzunluğu 5-8 mm, döküm parça kalınlığı 1-2 mm'dir). Şekil 1), dökümü hareketli kalıbın yanına doğru çekin ve ardından dökümün üzerindeki dikenli kancayı çıkarın. Dökümün hareketli kalıp üzerindeki sıkma kuvvetini arttırmak için, döküm üzerinde bitirilmesi gereken parçalar ve parçaların görünümü etkilemeyen yan yüzeyleri için karşılık gelen kalıp parçalarının yüzey pürüzlülüğü arttırılabilir. kaliteli, dökümün hareketli kalıbın sıkma kuvveti üzerindeki etkisini arttırmak için. Daha açık, daha belli.
Hareketli kalıbın sıkma kuvvetini arttırmak için uygun gergi çubukları kullanılabilir (bkz. Şekil 2):
- ①Dökümün görünümünü etkilememesi durumunda, hareketli kalıbın yan yüzeyinde veya maçanın yüzeyinde birkaç yiv açılabilir veya kalıpta yaklaşık 0.1 ila 0.2 mm derinliğinde birkaç çentik taşlanabilir. . . Ancak, düzensiz fırlatma kuvvetini önlemek için kanca oluğunun ejektör çubuğunun yakınında açılması gerektiğine dikkat edin;
- ②Kalıbı açarken, dökümü hareketli kalıbın kenarına çekmek için yolluk kullanmak isterseniz, iç yolluktan hareket ettiricinin yan tarafındaki gergi nervürlerini onarabilir veya taşlayabilirsiniz. 0.2'lik birkaç derinlik. ~0.3 mm içbükey nokta, koşucunun hareketli kalıba sıkıştırma kuvvetini arttırır;
- ③Ayrıca, itici pimi iç rayın yanındaki kızak üzerine ayarlayabilir, ejektör pimini kalıp yüzeyinden 5-8 mm daha aşağıya kısaltabilir ve ejektör piminin kalıp ağzının 3 mm altında olduğu tarafı 2 genişliğe kadar kırpabilirsiniz. 3 mm'ye kadar, 0.3~0.5 mm derinliğe sahip dairesel bir oluk. Dökümden sonra oluşan halka şeklindeki germe nervürü, koşucuyu hareket ettirir ve koşucu, dökümü, iç kızağın içinden hareketli kalıbın yanına çeker. Daha iyi sonuçlar;
- ④Eğer ladin burcunun kek ve ladin üzerine büyük bir çekme kuvveti uyguladığı için ise, döküm sabit kalıba getirilir ve hareketli kalıbın yolluk tarafında ve bölünmüş ladin tarafında germe nervürleri tamir edilebilir. koni. Kalıp açıldığında kızağı ve pastayı hareketli kalıbın yanına gerdirme çubuğu ile çekin;
- ⑤ Nispeten kalın duvarlı dökümler veya bitmesi gereken iç delikli dökümler için, hareketli kalıp maçasının kalıptan çıkma eğimi azaltıldıktan sonra, sabit kalıp sorunu çözülemezse, maçanın ortasında olabilir. uzunluk 2 ila 3 mm genişliğinde ve 0.2 ila 0.5 mm derinliğinde bir halka oluğu, bir germe nervürü oluşturmak için onarılır ve halka germe nervürü, dökümü hareketli kalıbın yanına çeker. Dökümün deforme olmasını önlemek için böyle bir maçanın yakınında dökümü çıkarmak için en az 2 ejektör pimi olması gerektiğini unutmayın.
Sabit kalıp tarafındaki paketleme kuvveti, hareketli kalıp tarafındaki paketleme kuvvetinden daha büyük olan dökümlerde, dökümün sabit kalıptan düzgün bir şekilde çıkabilmesi için, ejektör plakası, ejektör çubuğu ve sıfırlama çubuğu, dökümü çıkarmak için tasarlanmıştır. hareketli kalıp gibi döküm. Kalıbı açarken dökümü çıkarmak için sabit kalıp üzerindeki üst plakayı ve ejektör çubuğunu itmek için sabit kalıbın bir tarafına bir yağ silindiri veya bir yay eklemek mümkündür. Ejektör plakasının arkasında bir yay vardır. Kalıp açıldığında, sabit kalıp ejektörü ayırma yüzeyinden dışarı atılır. Kalıp kapatıldığında, hareketli kalıp ayırma yüzeyi, sabit kalıp itme plakasını ve ejektörü sıfırlamak için dört sıfırlama çubuğunu itmek için kullanılır.
Dökümü sabit kalıptan çıkarmak için ejektör çubuğunu kullanmak için, üç plakalı iki parçalı ayırma kalıbına benzer kanca çubuk, darbe bloğu ve silindir mekanizması da kullanılabilir (bakınız Şekil 5, döküm, ejektör çubuğu ve sıfırlama çubuğu şekilde gösterilmemiştir), Dökümleri sabit kalıptan çıkarmak için sabit kalıp çıkarıcı itme plakasını sürmek için kalıp açma eylemine dayanarak. Yapı aşağıdaki gibidir: Verilen kalıp için dökümü çıkarmak için ejektör piminin ejeksiyon yapısını tasarlayın, sabit kalıbın ejektör plakasının 5 sabit kalıp modelinden 6 dışarı çıkmasına izin verin ve üzerine dört (veya iki) kanca yerleştirin. hareketli kalıp 1. Dört (veya iki) kanca çubuğu (4), kalıp kapatıldığında sabit kalıbın (6) yan tarafına doğru uzanır. Kanca çubuğu 4, darbe bloğu 7, yay 3 ve makara mekanizması 8, dört kanca çubuğunu 4 ve sabit kalıbı yapmak için kullanılır. Kalıbın üst itme plakası bir kanca ile birleştirilir. Kalıp açıldığında, hareketli kalıp çekme çubuğu 4, sabit kalıp ejektör iticisini 5 kancalar ve sabit kalıp itici, dökümü sabit kalıptan çıkarmak için ejektör çubuğunu hareket ettirmek için ejektörü 5 iter. Bu sırada döküm ve hareketli kalıp eşzamanlı olarak hareket eder. Belirli bir vuruşa hareket ettikten sonra, dört kanca çubuğunun kancalarını sabit kalıp çıkarıcı itme plakasından ayırmak için darbe bloğu, silindir ve yay mekanizmasını kullanın, sabit kalıp çıkarıcı itme plakasının hareketi durur ve hareketli kalıp ayırma yüzeyi ayrıca kalıp kapalıyken de kullanılır. Sabit kalıp çıkarıcının konumuna geri dönmesini sağlamak için dört sıfırlama çubuğunu sabit kalıp çıkarıcı itme plakasına geri itin.
2.2 Dökümlerin kalıp döküm işlemi açısından sabit kalıba yapışmasını önleyici tedbirler
Kalıp üzerine sprey kaplama, alaşım sıvısının akış darbe hızı ve kalıp sıcaklığı, dökümün yapışmasını etkileyen ana faktörlerdir.
Kalıp ayırıcı maddenin çeşidi, kalitesi, konsantrasyonu, püskürtme konumu, püskürtme süresi ve miktarı dökümün yapışma durumunu etkiler Ⅲ. Hareketli ve sabit kalıpların her iki tarafında dökümün bırakma etkisini ayarlamak için püskürtülen kalıp ayırıcı miktarını kullanın. Dökümün sabit kalıba yapışmasını önlemek için hareketli kalıba püskürtülen kalıp ayırıcının süresi ve miktarı uygun şekilde azaltılabilir. Hareketli kalıbın üzerine püskürtülen boya ince ve homojen olmalı ancak boya gözden kaçmamalıdır. Kalıp yüzeyinin sıcaklığını düşürmek için, özellikle sabit kalıp süzülmüş dökümlerin yüzeyi ve çizim işaretli yüzeyler için, sabit kalıba püskürtülen ayırıcı madde miktarını artırın, püskürtme miktarını artırın. Sabit kalıbın yan tarafında sabit bir konum yoksa veya kalıp izi yoksa, püskürtülen kaplama miktarını uygun şekilde artırmaya dikkat edin.
Kalıbın çizim işaretli yüzeyine, kalıp dökümünden sonra boya püskürtülmeden önce yapışma önleyici kalıp macunu uygulayın, böylece yapışma önleyici kalıp macunu kalıp yüzeyine yüksek bir sıcaklıkta sinterlenir, böylece bir alaşım sıvısı ve kalıp yüzeyi arasında oluşum oluşur Daha kalın bir diyafram tabakası, kalıptan çıkarmada daha iyi bir rol oynayabilir.
Kalıp sıcaklığını uygun şekilde ayarlayın ve kontrol edin. Döküm sıkılığı ve yapışma kalıbının stresini, kalıbın sıcaklık farkı ve dökümün büzülmesini ve kalıp sıcaklığı ile alaşım büzülmesi ve kalıbın sıkılığı arasındaki ilişkiyi analiz etmek gerekir. Döküm yüzeyinde yapışkan bir kalıp gerilimi varsa, dökümün yüzey kalitesini sağlarken daha düşük bir kalıp sıcaklığı kullanmaya çalışın. Dökümün kendisi büyük bir sıkma kuvvetine sahipse, kalıptan çıkarma sırasında dökümün büzülmesini azaltabilecek daha yüksek bir kalıp sıcaklığı kullanmaya çalışın, yani döküm büyük bir sıkma kuvvetine ulaşmadığında, kalıptan çıkarmaya başlayacaktır.
Hareketli kalıbın sıcaklığının nispeten düşürülmesi ve dökümün büzülmesini teşvik etmek, dökümün hareketli kalıba sıkılığını artırabilir; sabit kalıbın sıcaklığını nispeten artırmak ve dökümün büzülmesini azaltmak, dökümün sabit kalıba sıkılığını azaltabilir. Hareketli kalıbın soğutma suyunun akış hızının arttırılması hareketli kalıbın kalıp sıcaklığını düşürebilir; sabit kalıbın soğutma suyunun akışını azaltmak veya kapatmak, sabit kalıbın kalıp sıcaklığını artırabilir. Genel olarak, kalıp döküm alüminyum alaşımlı dökümler için, hareketli kalıp boşluğunun yüzey sıcaklığını, kalıbı açtıktan sonra 1 ila 3 saniye içinde ölçün. Yüzey sıcaklığı 300℃'den, tercihen (240±40)℃'den fazla olmamalıdır; ve püskürtmeden sonra kalıbı kapatmadan önce Sabit kalıp boşluğunun yüzey sıcaklığını 1 ila 3 saniye içinde ölçün ve 140℃'den az olmamalıdır.
Dökme sıcaklığı, kalıp sıcaklığı gibi, dökümün büzülmesini ve ambalajın sıkılığını değiştirebilir. Dökme sıcaklığının arttırılması ve kalıbın açılma süresinin kısaltılması, paketleme kuvvetini azaltabilir, ancak alaşım sıvısı ile kalıp çeliği arasındaki afiniteyi artıracak ve dökümün kalın duvarlı kısmında yapışma olasılığına neden olacaktır.
3 Dökümlerin hareketli kalıba yapışmasını önlemek için önlemler
3.1 Döküm kalıpları açısından dökümlerin hareketli kalıba yapışmasını önleyici tedbirler
Dökümlerin hareketli kalıba yapışmasının ana nedeni, dökümlerin hareketli kalıba çok fazla sıkma kuvvetine sahip olması ve ejektör çubuğunun fırlatma kuvvetinin yetersiz olmasıdır. Ejeksiyon kuvveti yeterince büyük değilse, basınçlı döküm makinesinin ejeksiyon silindirinin hidrolik basıncını veya ejeksiyon hızını artırmak gerekir. Ejektör piminin çapı çok küçükse veya ejektör pimlerinin sayısı azsa, ejektör piminin gücü yeterince güçlü değildir ve ejektör pimi bükülebilir veya kırılabilir.
Dökümün hareketli kalıba yapışma kuvveti küçükse, döküm kalıptan çıkarıldığında gerinim daha hafiftir veya kalıbın pürüzlü yüzeyinin neden olduğu direnç küçüktür, ancak döküm çıkarıldığında deforme olur ve kalıba yapışan kısım parlatılmalı, nitrürlenmeli veya arttırılmalıdır. Püskürtülen ayırıcı madde miktarı ayrılma direncini azaltır. . Döküm kuvveti hareketli kalıba yapışıyorsa, döküm kalıptan çıkarıldığında döküm ciddi şekilde gerilir, dökümün üst kısmı kırılır veya bağlantısı kesilir veya döküm ejektör tarafından çıkarılır, döküm açısı uygun şekilde arttırılmalıdır. Dökümlerin veya kalıpların tasarımını iyileştirin ve dökümlerin kalıplara yapışmasına neden olan ve büzülmeyi etkileyen mantıksız yapıları ortadan kaldırın.
Dökümün eşit olmayan fırlatma kuvvetinin neden olduğu yapışma kalıbı gerilmesini önlemek için, kalıp çıkarma plakasını iten kalıp döküm makinesinin dört itme çubuğu aynı uzunlukta olmalı ve fark 0.20 mm'den fazla olmamalıdır. ; makine itme çubuğu ve ejektör Dökümün ejektör çubuğunun konumu dengeli ve makul olmalı ve kalıp boşluğunun merkezinden sapmamalı ve dökümün ejektör silindirinin merkezinden sapmamalıdır. makine.
Maça çekme ve çıkarma ayarları dengeli değilse, döküm eşit olmayan bir şekilde gerilecek ve yön değiştirecektir. Döküm makinesinin hidrolik ejeksiyon silindirinin itme çubuğunun uzunluğu aynı değilse, dökümün ejeksiyon kuvveti eşit değilse veya itme çubuğunun konumu yanlış düzenlenmişse, döküm ejeksiyon sırasında sapacaktır. . İyileştirme önlemleri şunlardır: kalıp yapısını değiştirin, maça çekme mekanizmasını ve ejektör çubuğunun konumunu ayarlayın, böylece döküm kuvveti eşit bir şekilde dışarı atılır ve dökümün paralel ve eşit bir şekilde dışarı itilmesini sağlayın; ejektör çubuklarını ve kalıbın dökümlerini eşit bir şekilde gerdirmek için kalıp döküm makinesinin itme çubuğunun (kullanımı en kolay 4-6 itme çubuğu) ejeksiyon mekanizmasını, konumunu ve miktarını ayarlayın; ejektör çubuklarının sayısını makul bir şekilde artırın, ejektör çubuklarının çapını artırın ve ejektör çubuğunun konumlarını, ejeksiyon dengesini sağlayacak şekilde düzenleyin.
Düz parçaların ve ince cidarlı dökümlerin deformasyon direnci yetersiz ise ejektör pimlerinin sayısı ve çapı arttırılmalıdır. İtici pimin dökümün küçük çıkıntısı üzerinde durmasına izin vermek için ejektör konumuna küçük bir çıkıntı da ekleyebilirsiniz. Büyük ejeksiyon kuvveti alanı, döküm kuvvetini tek tip hale getirir.
Yüksek kaliteli kalıp çeliği kullanın, böylece kalıp sıcaklığı yüksek olduğunda, döküm alaşımının yüzeye yapışması kolay olmaz. Yüksek kaliteli kalıp çeliği ile, kalıp yüzeyinde erken mikro çatlaklar oluşmaz ve bu da alaşım yapışmasını ortadan kaldırır.
Kalıp sertliği yetersiz veya kırılgan olduğunda, alaşım sıvısı kalıba yapışmaya eğilimlidir. Kalıp sertliğinin makul olup olmadığını kontrol etmek ve ayrıca kalıp çeliğinin kırılganlığını önlemek için ısıl işlem sürecini kontrol etmek gerekir. Modüllerin, kalıp eklerinin ve iç rayın etkisine dayanabilecek tüm maçaların sertliği, kalıp boşluğu modülünün sertliğinden HRc3~5 daha yüksektir. Kalıp tasarımı herhangi bir sorun olmadığını doğruladığında ve döküm kalıbı yapışma gerilmesinin ortadan kaldırılması hala zor olduğunda, yüzeyi iyileştirmek için nitrürleme, KANI 7C, tungsten kaplama, PVD nano titanyum kaplama vb. gibi yüzey işleme önlemleri kullanılmalıdır. kalıbın sertliği.
Kalıp boşluğunun yüzeyi için genellikle yağ taşı ve zımpara kağıdı ile parlatılır. Yapışan kısmı parlatmak için pnömatik bir alet kullanıyorsanız, kalıbın yüzeyindeki nitrür tabakasına zarar vermemek için kalıba zarar vermemeye dikkat etmelisiniz, aksi takdirde ne kadar parlatılmışsa kalıp o kadar yapışkan olacaktır. Dava. Yapışkan kalıbın veya yapışkan örtünün boşluk olmayan kısmını temizlerken, tümsekleri çıkarmak için bir spatula kullanabilir ve ardından zımpara kağıdı ile hafifçe parlatabilirsiniz. Çukurları dışarı çıkarmayın, aksi takdirde daha ciddi yapışmalara neden olur. Kalıp boşluğundaki yapışkan kalıbı herhangi bir zamanda temizlemek için keski kullanmamaya dikkat edin, böylece kalıp boşluğunu oymayın.
3.2 Dökümlerin hareketli kalıba yapışmasını önleyecek önlemler pres döküm prosesi açısından
Kalıp döküm makinesinin yüksek hızlı enjeksiyon hızını azaltın veya yolluk doldurma hızını uygun şekilde azaltmak için kalıptaki yolluk alanını artırın. İç çarkın doldurma hızı artırılmadan iç çark alanı arttırılırsa doldurma süresi kısaltılabilir, iç çarkın çarpmasıyla oluşan toplam ısı azaltılabilir ve darbeyi azaltma etkisi iç koşucu elde edilebilir.
Döküm basıncını uygun şekilde azaltın: İnce duvarlı parçalar ve gözenek gerektirmeyen dökümler için 40-55MPa gibi daha küçük bir basınç seçebilirsiniz; genel dökümler 55-75 MPa'yı seçer; gözenek gereksinimleri olan kalın duvarlı parçalar ve dökümler için, 75~100MPa gibi daha yüksek bir basınç kullanın; büyük bir basınç kullanılması gerektiğinde 100~140 MPa seçilebilir. Döküm basıncı ne kadar yüksek olursa, dökümün mekanik özellikleri o kadar iyi ve dökümün kalıba sıkılığı o kadar yüksek olur. Kalıp yapışması meydana gelirse, uygun döküm basıncının kullanıldığını doğrulamak gerekir. Dökümün daha yüksek bir sıcaklıkta kalıptan çıkarılabilmesi ve kalıbın sıkıştırma kuvvetinin maksimum değere ulaşmaması için kalıp açma süresini (kalıp soğuma süresi) uygun şekilde azaltın, bu da dökümün kalıba sıkıştırma kuvvetini azaltabilir ve azaltabilir. kalıbın yapışması. derece.
Dökümün kalıptan ayrılma açısı çok küçükse, dökümün kalıba yapışmasına neden olma olasılığı yüksektir. Bu nedenle, alaşım malzemesine ve dökümün boyut yapısına göre uygun bir kalıptan çıkarma açısı seçmek gerekir. Kalıp yapışması meydana geldiğinde, çekim açısının uygun şekilde arttırılması, termal şok ve büzülmeden kaynaklanan yapışma olgusunu ortadan kaldırabilir. Döküm yapısı makul değilse, büzülme ve soğutma işlemi sırasında dökümün her bir parçasının büzülmesinin düzensiz olmasına ve büzülmeye karşı direncin dengesiz olmasına neden olur. Mümkünse ve gerekliyse, duvar kalınlığını üniform hale getirmek için dökümün tasarım yapısını iyileştirin, örneğin kesitin kalınlığı için, kalın parçaları içi boş yapılar veya nervürlü bağlantı yapıları olarak tasarlamaya çalışın; büyük kalınlık farklılıklarına sahip geçiş parçalarından kaçının; mantıksız çıkıntıları, çıkıntıları ve takviye nervürlerini ortadan kaldırın. Dökümün içbükey köşesinde döküm filetosunun veya kalıptan çıkarma açısının arttırılması da kalıbın yapışmasını önleyebilir.
Kalıbın iç koşucu ve alaşım sıvısının darbe boşluğunu doldurduğu kısım, kalıbın dökümde kalın duvar kalınlığına sahip kısmı ve dökümün girintili köşesi yakınında, etkilenmesi kolaydır. Alaşım sıvısı uzun süre. Döküm çubukları ve gerilmeler oluşur, bu nedenle kalıbın bu kısımlarına su soğutması için soğutma suyu boruları sağlanmalıdır. İnce çekirdek soğutma için soğutma suyunun basıncı arttırılmalıdır. Bunlar kalıp sıcaklığını azaltabilir ve kalıbın yapışmasını önleyebilir.
Döküm alaşımı, döküm yüzeyinde kalıp yüzeyine yapışırsa, yüzeyde bazı küçük kabarcıklar oluşur. Bu olay için kalıp yüzeyi zımpara bezi ve yağ taşı ile parlatılır ve kalıp tekrar tekrar yapıştırılır, bu da sorunu tamamen çözemez. Bu tür yapışmayı çözmenin daha iyi bir yolu, yapıştırma kalıbının yüzeyinde bilyalı dövme yapmak veya kalıbın yapışan kısmının yüzeyini 0.2~0.5 mm genişliğinde ve 0.2~0 derinliğinde yapmaktır. 5 mm'lik net desen ve 2 ila 5 mm aralık, döküm yüzeyine yapışma kusurlarını ortadan kaldırabilir.
Yolluğun büzülmesi, döküm deformasyonuna ve kalıp yapışmasına neden olur. Dal koşucusunun alanını azaltmak için dal koşucusunun uzunluğu uzatılmalıdır; koşucunun genişliği azaltılmalı, koşucunun boyu uzatılmalı ve koşucu küçültülmelidir. Kanal sayısı; Kızakların büzülmelerinin dökümler üzerindeki etkisini ortadan kaldırmak için kalıbın yolluklarının soğutma suyu ile soğutulmasını arttırın.
Döküm alüminyum alaşımının demir içeriği ne kadar azsa (<%0.6 gibi), alüminyum alaşımlı sıvı ile kalıp çeliği arasındaki afinite o kadar yüksek ve kalıba yapışma olasılığı o kadar yüksek. Alüminyum alaşımlı sıvının demir içeriğinin uygun şekilde arttırılması, alüminyum alaşımının kalıba yapışmasını daha iyi azaltabilir; genel olarak, kalıp döküm alüminyum alaşım sıvısındaki demir içeriğinin %0.6 ila %0.95 arasında kontrol edilmesi gerekir. Düşük erime noktalı metallerle karıştırılarak oluşan kalıp yapışmasını önlemek gerekir. Kimyasal bileşimi ayarlamak için bir ana alaşım kullanıldığında, magnezyum ve çinko gibi tek tek metallere ek olarak, şiddetli ayrışmanın kalıp yapışmasına neden olmasını önlemek için alüminyum sıvıya saf metaller eklenemez.
Kalıp döküm alaşımının büzülmesi ne kadar büyük olursa, kalıba yapışması o kadar kolay olmakla kalmaz, aynı zamanda yüksek sıcaklık mukavemeti de o kadar kötü olur. Bazı alaşımlar daha büyük bir büzülme oranına sahiptir; alaşımın sıvı ve katı faz sıcaklık aralığı ne kadar genişse, alaşımın büzülmesi o kadar büyük olur. Dökümün yapısal şekline ve karmaşıklığına göre, kalıp yapışması ve büzülmeden kaynaklanan deformasyonun giderilmesi zorsa, küçük gövde büzülmesi ve lineer büzülme ve yüksek sıcaklık dayanımı olan bir alaşıma geçmeyi düşünün; veya alaşım bileşimini (alüminyum gibi) ayarlayın. Silikon alaşımındaki silikon içeriği arttığında, dökümün büzülme oranı küçülür) büzülme oranını azaltmak için; veya alaşımı modifiye etmek için, alaşımı küçültmek için alüminyum alaşım sıvısına %0.15 ila %0.2 metal titanyum ve diğer tane incelticiler ekleyin.
4 Sonuç
Kalıp dökümlerin yapışmasının birçok nedeni vardır ve yapışmayı çözmeye yönelik önlemler de farklıdır. Makale, özel olarak, kalıp dökümlerinin yapışma kusurlarını çözmek için önlemler önermektedir. Yapışmanın nedenlerini dikkatlice gözlemlemeli, analiz etmeli ve hedefe yönelik önlemler almalıyız. Karşılık gelen karşı önlemler, kalıp yapışması sorununu etkili bir şekilde çözebilir.
Lütfen yeniden basım için bu makalenin kaynağını ve adresini saklayın: Pres Döküm Yapışkan Kalıp Hatalarını Çözmek İçin Somut Önlemler
Minghe Döküm Şirketi, kaliteli ve yüksek performanslı Döküm Parçaları üretmeye ve sağlamaya kendini adamıştır (metal döküm parça yelpazesi esas olarak şunları içerir: İnce Duvarlı Döküm,Sıcak Kamara Basınçlı Döküm,Soğuk Oda Döküm), Yuvarlak Servis (Döküm Servisi,Cnc İşleme,Kalıp yapımı,Yüzey İşleme).Herhangi bir özel Alüminyum döküm, magnezyum veya Zamak/çinko döküm ve diğer döküm gereksinimleri bizimle iletişime geçebilirsiniz.
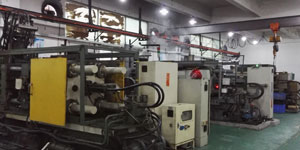
ISO9001 ve TS 16949 kontrolünde, tüm işlemler yüzlerce gelişmiş basınçlı döküm makinesi, 5 eksenli makine ve blasterlerden Ultra Sonic yıkama makinelerine kadar diğer tesisler aracılığıyla gerçekleştirilir. Müşterinin tasarımını gerçeğe dönüştürmek için deneyimli mühendisler, operatörler ve müfettişlerden oluşan ekip.
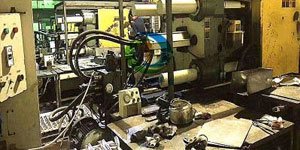
Dökümlerin sözleşmeli üreticisi. Yetenekler, 0.15 lbs'den başlayan soğuk oda alüminyum döküm parçaları içerir. 6 lbs'ye kadar, hızlı değişim kurulumu ve işleme. Katma değerli hizmetler arasında polisaj, titreşim, çapak alma, kumlama, boyama, kaplama, kaplama, montaj ve kalıplama yer alır. Çalışılan malzemeler arasında 360, 380, 383 ve 413 gibi alaşımlar bulunur.
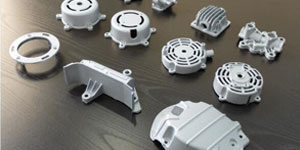
Çinko pres döküm tasarım yardımı/eşzamanlı mühendislik hizmetleri. Hassas çinko dökümlerin özel üreticisi. Minyatür dökümler, yüksek basınçlı dökümler, çok kızaklı kalıp dökümleri, geleneksel kalıp dökümleri, birim kalıp ve bağımsız kalıp dökümleri ve boşluklu sızdırmaz dökümler üretilebilir. Dökümler, +/- 24 inç toleransta 0.0005 inç'e kadar uzunluk ve genişliklerde üretilebilir.
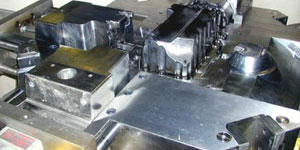
ISO 9001: 2015 sertifikalı döküm magnezyum üreticisi, Yetenekler arasında 200 ton sıcak odaya ve 3000 ton soğuk odaya kadar yüksek basınçlı magnezyum kalıp dökümü, takım tasarımı, cilalama, kalıplama, işleme, toz ve sıvı boyama, CMM özelliklerine sahip tam kalite güvencesi bulunur , montaj, paketleme ve teslimat.
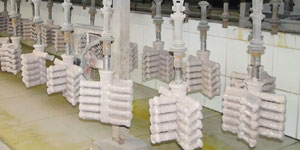
ITAF16949 sertifikalı. Ek Döküm Hizmeti Dahil yatırım dökümleri,kum dökümü,Yerçekimi Döküm, Kayıp Köpük Döküm,Savurma döküm,Vakumlu Döküm,Kalıcı Kalıp Döküm,.Yetenekler arasında EDI, mühendislik yardımı, katı modelleme ve ikincil işleme yer alır.
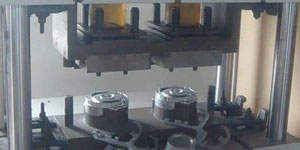
Döküm Endüstrileri Arabalar, Bisikletler, Uçaklar, Müzik aletleri, Deniz Araçları, Optik cihazlar, Sensörler, Modeller, Elektronik cihazlar, Muhafazalar, Saatler, Makineler, Motorlar, Mobilya, Mücevher, Jigler, Telekom, Aydınlatma, Tıbbi cihazlar, Fotoğraf cihazları, Robotlar, Heykeller, Ses ekipmanları, Spor ekipmanları, Aletler, Oyuncaklar ve daha fazlası.
Bundan sonra ne yapmanıza yardımcı olabiliriz?
∇ Ana Sayfaya Git Çin Döküm
→Döküm Parçaları-Ne yaptığımızı öğren.
→ Hakkında İlgili İpuçları Pres Döküm Hizmetleri
By Minghe Döküm Üreticisi |Kategoriler: Faydalı Makaleler |Malzeme Etiketler: Alüminyum Döküm, Çinko Döküm, Magnezyum Döküm, Titanyum Döküm, Paslanmaz Çelik Döküm, Pirinç Döküm,Bronz Döküm,Döküm Videosu,Tarihçe,Alüminyum Döküm |Yorumlar Kapalı