Pres Döküm Üretiminde Alüminyum Alaşım ve Yardımcı Malzeme Yönetimi
Ana Malzeme Yönetimi
1. Alüminyum alaşımlı külçelerin giriş kontrolü
Alüminyum alaşımının gaz içeriği ve sert nokta gereksinimleri nedeniyle, alüminyum külçe üretim tesisleri, yüksek gaz içeriği ve alüminyum külçelerdeki birçok kirlilik gibi kusurların kalıplara miras kalmasını önlemek için iyi bir arıtma, gaz giderme ve cüruf giderme işi yapmalıdır. alüminyum sıvı döküm. Alüminyum alaşımlı külçe fabrikaya girdikten sonra ilk adım görünümü incelemektir. Alüminyum külçenin yüzeyinin pürüzsüz, pürüzlü olmayan, yağ lekeleri, küf ve oksit ölçeği içermemesi ve alüminyum alaşımlı külçenin kırılma yapısının ince ve yoğun olması gerekir. Ciddi bir ayrışma, büzülme veya büzülme olmamalıdır. Cüruf ve kapanımlar. Kullanılan alaşım bileşiminin kalifiye olduğundan emin olmak için her partinin bileşiminden ve ısı numarasından numune alınması. Özel gereksinimleri olan ürünlerin üretiminde, diğer test maddelerinin eklenmesi gerekir. Örneğin, mekanik performans gereksinimleri olan ürünler üretilirken, alüminyum alaşımlı külçe üretime teslim edildiğinde, her fırın için bir çekme test çubuğu sunulması gerekir; hava geçirmezlik gereksinimleri olan ürünler üretilirken, alüminyum alaşımlı külçenin iğne deliği derecesi arttırılmalıdır. Tespit etmek
Gerçek üretimde kullanılan alüminyum alaşımlarının türleri genellikle bir sınıfla sınırlı değildir ve her bir alüminyum alaşımı sınıfının kimyasal bileşim gereksinimleri oldukça farklıdır. Bir alaşım sınıfındaki ana elementler, başka bir alaşım sınıfındadır. Bir kirlilik olarak kabul edilebilir. Birden fazla kalitenin bir arada bulunması için, kullanım sırasında karışma oluşmasını önlemek için her bir kalitedeki alaşımları görsel olarak net bir şekilde ayırt etmek gerekir. Genel önlem, farklı markalara ve farklı üreticilere ait alüminyum alaşımlarının görünüşünün rengini açık ve düzgün bir şekilde belirlemek ve farklı malzemeleri fabrikaya ulaştıktan sonra farklı alanlarda depolamaktır.
2. Alüminyum alaşımlı eritme işlemi kontrolü
Üretim uygulaması, alaşımlı eriyik kalitesinin iyileştirilmesinin, döküm kalitesinin iyileştirilmesinde önemli bir faktör olduğunu göstermektedir. Bu nedenle, niteliksiz hammaddelerin atölyeye veya üretime girmemesi için hammadde yönetimi sıkı bir şekilde kontrol edilmelidir. Alaşım eritme sürecinin gerektirdiği standartlara sıkı sıkıya bağlı kalın ve çeşitli hammaddelerin (yeni malzemeler, geri dönüştürülmüş malzemeler ve yardımcı malzemeler) yönetimini güçlendirin.
Alüminyum alaşımlı eritme işlemi, erime sıcaklığı, eritme süresi ve yeniden ateşlenen malzemelerin oranı, özellikle yeniden ateşlenen malzemeler kesinlikle sınıflandırılmalı ve yönetilmeli ve karıştırılmamalıdır. Geri dönüştürülmüş malzeme temiz olmalı ve yağ, pas, silt, nem ve ek parçalar içermemelidir. Geri dönüştürülmüş malzemedeki yağlı kirleticiler, alüminyum külçe üreticisi tarafından yeniden eritilebilir ve kullanım için doğrudan eritme fırınına konulamaz; saçılan alüminyum bloklar için ise elekten geçirilmeli ve içindeki toz, kum ve diğer döküntüler temizlenebilir. Kullanım: Erimiş alüminyumun yeniden ısıtma için kullanıldığı durumlarda, arıtma maddesi ve cüruf giderici oranı, eritme için sadece alüminyum alaşımlı külçe kullanıldığındakinden daha fazladır. Bağıl nemin yüksek olduğu havalarda yapılan üretimde, geri dönüştürülen malzeme oranı %30'u, geri dönüştürülen malzeme kuru havalarda uygun şekilde artırılabilir ancak %40'ı geçmemelidir.
Erimiş alüminyumun eritme işleminden sonra cüruf ve gazdan arındırılması zamanında yapılmalı ve ilgili parametreler gerektiği gibi kaydedilmelidir. Merkezi eritme işleminde, eritme işlemi sırasında ürünün kimyasal bileşiminin kalifiye olduğundan emin olmak için her bir alüminyum sıvı kabının kimyasal bileşimi test edilmelidir. Ek olarak, uzun süreli eritmeden kaçınılmalıdır, aksi takdirde alüminyum alaşımlı sıvıdaki hidrojen içeriği artacak ve bu da döküm ürününün mukavemetini ve hava sızdırmazlığını etkileyecektir. Genellikle, eritmeden kalıp döküme kadar 4 saati geçmez.
Yardımcı Malzemelerin Yönetimi
1. Ayırıcı maddenin kontrolü
Kalıp ayırıcı madde kullanımı, sıvı metalin sorunsuz bir şekilde doldurulmasını sağlayabilir, şekillendirmeyi kolaylaştırabilir, kalıbın yapışmasını önleyebilir, dökümlerin parlak, pürüzsüz ve düz yüzey kalitesi elde etmesini sağlayabilir ve üretim ritmi, döküm yüzeyi ve iç kalite üzerinde büyük bir etkiye sahip olabilir. Aynı zamanda kalıbı koruyabilir, kalıp yüzeyinde yüksek sıcaklıktaki sıvı metalin aşınmasını önleyebilir, kalıbın ısıl iletkenliğini ve kalıp sıcaklığını azaltabilir ve kalıbın ömrünü uzatabilir. Kalıp açıldığında, dökümün düzgün bir şekilde çıkarılmasına yardımcı olur ve ayrıca zımba, ejektör çubuğu ve hareketli parçaların sürtünmesini ve aşınmasını azaltmada önemli bir rol oynar. Ayırıcı ajanın kontrolü, yalnızca ayırıcı ajanın seçimini ve oranını değil, aynı zamanda operatör tarafından ayırıcı ajanın püskürtülmesi ve fön ile kurutulmasının yönetimini de içerir. Genel olarak, ayırıcı maddenin seçimi aşağıdaki gereksinimlere sahiptir.
- Yüksek sıcaklıkta ve düşük buharlaşma noktasında iyi yağlayıcılığa sahiptir. Ayırıcı maddedeki su 100-150°C'de hızla buharlaşabilir.
- Kalıp döküm kalıpları ve kalıp döküm parçaları üzerinde aşındırıcı etkisi yoktur ve istikrarlı performansa sahiptir. Ayırıcı madde çok hızlı uçmamalı ve havada kalınlaşmamalıdır.
- Yüksek sıcaklıkta hiçbir zararlı gaz çökelmeyecek ve döküm boşluğunun yüzeyinde herhangi bir kirlenme oluşmayacaktır.
Şu anda, ayırıcı maddenin püskürtülmesi esas olarak manuel bir işlemdir ve makul bir püskürtme işlemi, dökümün kalitesini, döküm kalıbının ömrünü ve üretim verimliliğini sağlamak için önemli bir faktördür. Kalıp ayırıcı maddenin püskürtme süresi aynı zamanda kalıp ayırma performansı, seyreltme oranı, farklı kalıp ayırma şekilleri ve farklı kalıp ayırma maddelerinin farklı kalıp sıcaklıkları ile de değişir. Ayırıcı madde, koruyucu bir film halinde yoğunlaşması için püskürtme tabancasından kalıbın yüzeyine püskürtülür. Bu uzun zaman alır. İşlem tamamlanmadığında, genellikle dökümdeki gevşek kusurların temel nedeni olan döküm işlemi gerçekleştirilir. Döküm prosesinin düzenlemelerine göre, farklı tipte bir ayırıcı madde ve farklı seyreltme oranları için makul bir püskürtme zaman aralığı benimsenmelidir. Döküm işçileri, proses parametrelerinin üst ve alt sınırlarının anlamını ve ayar etkisinin eğilimini anlamalı ve üretilen dökümlerin yüzey koşullarına göre uygun ayarlamalar yapmalıdır.
Su bazlı ayırıcı maddeler kullanıldığında, ayırıcı maddelerin oranı sıkı bir şekilde kontrol edilmelidir. Ayırıcı maddenin suya oranı çok kalınsa, kalıp yüzeyinde daha kalın bir film oluşacak ve kalıp yüzeyinde yavaş yavaş ayırıcı madde birikimi oluşacaktır. Ayırıcı maddedeki nem tamamen boşaltılamaz ve kalıp döküm parçasını oluşturacak olan gaz üretilir. İç kompaktlık bozulur. Ayırıcı maddenin suya oranı çok ince olursa, etki elde edilemez ve kalıp döküm parçalarında gerilim ve kalıp yapışması meydana gelir.
Bu nedenle, kalıp döküm atölyesinin kalite kontrolünde kalıp ayırıcının yönetimi, kalıp döküm parçalarının kalitesi üzerinde daha büyük bir etkiye sahiptir. Kalıp ayırıcının oranından sorumlu olacak özel bir kişinin atanması ve kalıp döküm üretim sürecinde kalıp ayırıcı ve su oranının çeşitli türlerde açıkça belirtilmesi gibi bu alandaki yönetimin güçlendirilmesi gerekmektedir. ürünler, ayırıcı ajan hazırlama sürecine göre belirlenir ve nicelenir. Püskürtme yaparken, operatör püskürtme eylemi konusunda sıkı bir eğitim almalıdır ve eylem, gereksinimler ve spesifikasyonlara uygun olarak gerçekleştirilmelidir ve daha fazla püskürtmeye, daha az püskürtmeye veya püskürtmeyi kaçırmaya izin verilmez.
2. Punch yağı yönetimi
Şu anda, yağ bazlı zımba yağlama yağı veya parçacık yağlama kullanımının çoğu, hangi zımba yağlaması olursa olsun, alüminyum sıvı namluya girdikten sonra kısa sürede tamamen yakılmalı ve kalıntı dağıtılmalıdır. Alaşım sıvısının üst tabakasında, böylece zımba yağının ürün üzerindeki etkisi çok büyük olmayacaktır. Aksi takdirde yanma sonucu oluşan gaz ve yanma sonrası kalıntılar ürüne girer ve sonuç hayal edilebilir.
Zımba yağını doğrulamanın basit yolu, kalıp üzerindeki malzeme sapının rengini gözlemlemektir. Genel olarak, malzeme sapının kalınlığı, zımba çapının 1/3 ila 1/4'ü kadardır ve zımba yağının kararma uzunluğu, malzeme sapının kalınlığının 3'ünü geçmemelidir. /5; Aynı zamanda, malzeme sapının ucunda belirgin bir kararma (yani çok fazla grafit tozu kalıntısı) olmamalıdır. Aksi takdirde ürün işlendikten sonra gözenek gibi kusurlar kaçınılmaz olarak artacaktır.
Üretim sürecinde her zaman zımba yağlama cihazının çalışma durumuna da dikkat etmeliyiz. Yağlayıcı çok fazla veya çok az püskürtülürse, basınç odasının ve zımbanın ömrü ve kalıp dökümün kalitesi üzerinde olumsuz bir etkisi olacaktır. Kullanılan yağlayıcı miktarını ayarlarken hem zımbanın kayganlığını hem de kalıbın sökülebilirliğini dikkate almak gerekir. Özellikle partikül yağlama kullanıldığında, kalıp döküm kalıbında mum peletleri nasıl kullanılırsa kullanılsın, organik maddenin buharlaşması sorunu olacaktır. Çok miktarda uçucu organik madde iyi bir şekilde boşaltılamıyorsa, kalıp döküm kısmında gözeneklerin oluşması üzerinde büyük bir etkisi olacaktır.
3. Zımba yönetimi
Zımba ve basınç odası birbirine bağlı bir sistem oluşturur. Normal şartlar altında, basınç odasının ömrü 2 ila 3 yıla ulaşabilir ve bir zımbanın ömrü kısadır, bir vardiyadır ve uzun ömür 10,000 defadan fazla olabilir. Ömür farkı, ürün kalitesinde dalgalanmalara ve üretim maliyetlerinde önemli değişikliklere neden olacaktır. Bu nedenle, iyi bir zımba yönetimi, yalnızca kalıp döküm parçalarının kalitesini stabilize etmekle kalmaz, aynı zamanda kalıp dökümün üretim maliyetini de büyük ölçüde azaltır.
- Zımba boyutu tasarımı. Normal şartlar altında, zımba ile basınç odası arasında belirli bir boşluk olması gerekir. Uygulama, ideal boşluğun yaklaşık 0.1 mm olduğunu göstermektedir. Enjeksiyon sırasında, boşluk çok büyükse, alüminyum alaşımlı sıvı boşluğa girebilir ve alüminyum sıvı sızıntısı ve duman meydana gelir, bu da zımbanın aşınmasını şiddetlendirecek ve zımbanın ömrünü azaltacaktır; boşluk çok küçük ise, zımba işlemde hareket eder Sıkışma olur, zımba hızı işlem tarafından önceden belirlenen hıza ulaşamaz, kalıbın doldurma süresi uzar ve kalıp dökümün kalite sorunları parçalar artar. Bu nedenle, kritik boşluğu nihayet kontrol etmek, zımbanın ömrünü uzatmak ve ürünün kalitesini sağlamak için zımbanın işlenmesi ve üretimi kesinlikle çizime göre yapılmalıdır.
- Zımbanın soğutulması Pres döküm işlemi, zımbanın sıcaklığının sürekli değiştiğini belirlediğinden, sıcaklık değişimiyle birlikte zımba ile basınç odası arasındaki boşluk da değişmektedir. Bu değişiklikler sadece zımbanın hizmet ömrünü değil, aynı zamanda kalıp döküm işlemi sırasında enjeksiyon işleminin stabilitesini de etkiler. İdeal boşluğu korumak için zımbayı soğutmak gerekir. Tasarımda, pistonun enjeksiyon çubuğunun su çekirdeği tarafından tamamen soğutulduğu ve zımba ısısının maksimum ölçüde alındığı ve zımba ile basınç odası arasındaki ideal boşluğun korunabileceği düşünülmüştür. kararlı. Bu önlemler, her bir kalıbın enjeksiyon işleminin stabilitesini ve kalıp döküm ürünlerinin kalitesinin stabilitesini sağlamaya yardımcı olur. Uygulama, iyi zımba soğutmalı enjeksiyon sisteminin, enjeksiyon işleminin stabilitesini sağlarken zımbanın hizmet ömrünü büyük ölçüde uzatabileceğini göstermiştir. Bununla birlikte, zımbanın soğutma suyu devresini sızdırmaz hale getirmek için iyi bir iş yapmak ve zımba ile enjeksiyon çubuğu arasındaki zayıf sızdırmazlıktan kaynaklanan soğutma suyu sızıntısına karşı dikkatli olmak gerekir. Soğutma suyu sızıntısına yeterince dikkat edilmezse ürün ciddi şekilde etkilenecektir. Hava sızdırmazlığı.
4. Pota yönetimi
Alüminyum alaşımlarının basınçlı dökümü için potaların kullanımı, özellikle dökme demir potaların kullanımı çok önemlidir. Potalar kesinlikle pota özelliklerine uygun olarak çalıştırılamıyorsa, sonraki üretim sürecinde alüminyum alaşım bileşimindeki Fe içeriği standardı aşabilir. Tecrübelerimize göre, eğer dökme demir pota, yeni potun kullanım gereksinimlerine sıkı sıkıya bağlı olarak pota boyası ile fırçalanabilirse ve kullanım sırasında her 3 günde bir fırçalanabilirse, temel olarak tüm kalıp boyunca Fe içeriğindeki artış. döküm üretim süreci %0.2'yi geçmeyecektir (bu, şirketin yıllara göre istatistiksel verileridir, farklı şirketler arasında bazı farklılıklar olabilir). Alüminyum alaşımlı külçelerin gelen muayenesini kontrol etme öncülüğünde, üretilen dökümlerin alaşım bileşiminin standart gereksinimleri karşıladığını tam olarak garanti edebilir. Grafit potaların kullanımında demirin artmasıyla ilgili bir endişe olmasa da buna da dikkat edilmelidir. Grafit potaların ilk kullanımı için kurutma işlemi kesinlikle uygulanmalıdır. Bu işlemler gelecekte grafit potaların hizmet ömrünü etkileyecektir ve iyi bir şekilde önceden ısıtılmamıştır. Grafit pota ömrü büyük ölçüde etkilenecektir. Her bir grafit potanın yüksek fiyatı, dökümün üretim maliyetini etkileyecektir.
Sonuç
Kalite yönetiminin beş ana unsuru arasında, yukarıdakiler esas olarak "malzemeler" ve "insanlar" konularını tartışır. Hammadde ve yardımcı malzemeleri yönetirken, personel eğitimi ve yönetimi iyi yapılmalı ve döküm işçilerinin teknik seviyesi daha da geliştirilmelidir. Döküm üretiminde kalite problemlerini etkin bir şekilde çözmek için, toplam kalite yönetimi fikrini döküm atölyesinin kalite kontrolüne uygulayın ve üretime rehberlik etmek için sistematik döküm üretim teorisi bilgisini kullanın. kalıp döküm atölyesinin kalite kontrol kabiliyetini kesinlikle yeni bir seviyeye yükseltecektir. .
Lütfen yeniden basım için bu makalenin kaynağını ve adresini saklayın: Pres Döküm Üretiminde Alüminyum Alaşım ve Yardımcı Malzeme Yönetimi
Minghe Döküm Şirketi, kaliteli ve yüksek performanslı Döküm Parçaları üretmeye ve sağlamaya kendini adamıştır (metal döküm parça yelpazesi esas olarak şunları içerir: İnce Duvarlı Döküm,Sıcak Kamara Basınçlı Döküm,Soğuk Oda Döküm), Yuvarlak Servis (Döküm Servisi,Cnc İşleme,Kalıp yapımı,Yüzey İşleme).Herhangi bir özel Alüminyum döküm, magnezyum veya Zamak/çinko döküm ve diğer döküm gereksinimleri bizimle iletişime geçebilirsiniz.
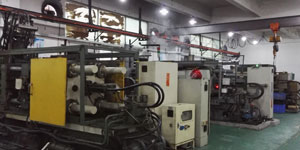
ISO9001 ve TS 16949 kontrolünde, tüm işlemler yüzlerce gelişmiş basınçlı döküm makinesi, 5 eksenli makine ve blasterlerden Ultra Sonic yıkama makinelerine kadar diğer tesisler aracılığıyla gerçekleştirilir. Müşterinin tasarımını gerçeğe dönüştürmek için deneyimli mühendisler, operatörler ve müfettişlerden oluşan ekip.
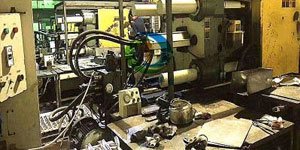
Dökümlerin sözleşmeli üreticisi. Yetenekler, 0.15 lbs'den başlayan soğuk oda alüminyum döküm parçaları içerir. 6 lbs'ye kadar, hızlı değişim kurulumu ve işleme. Katma değerli hizmetler arasında polisaj, titreşim, çapak alma, kumlama, boyama, kaplama, kaplama, montaj ve kalıplama yer alır. Çalışılan malzemeler arasında 360, 380, 383 ve 413 gibi alaşımlar bulunur.
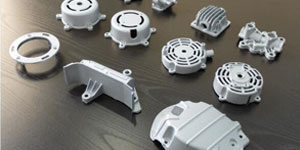
Çinko pres döküm tasarım yardımı/eşzamanlı mühendislik hizmetleri. Hassas çinko dökümlerin özel üreticisi. Minyatür dökümler, yüksek basınçlı dökümler, çok kızaklı kalıp dökümleri, geleneksel kalıp dökümleri, birim kalıp ve bağımsız kalıp dökümleri ve boşluklu sızdırmaz dökümler üretilebilir. Dökümler, +/- 24 inç toleransta 0.0005 inç'e kadar uzunluk ve genişliklerde üretilebilir.
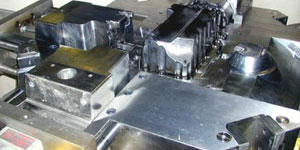
ISO 9001: 2015 sertifikalı döküm magnezyum üreticisi, Yetenekler arasında 200 ton sıcak odaya ve 3000 ton soğuk odaya kadar yüksek basınçlı magnezyum kalıp dökümü, takım tasarımı, cilalama, kalıplama, işleme, toz ve sıvı boyama, CMM özelliklerine sahip tam kalite güvencesi bulunur , montaj, paketleme ve teslimat.
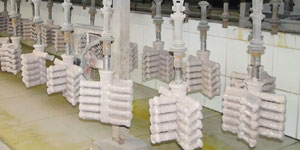
ITAF16949 sertifikalı. Ek Döküm Hizmeti Dahil yatırım dökümleri,kum dökümü,Yerçekimi Döküm, Kayıp Köpük Döküm,Savurma döküm,Vakumlu Döküm,Kalıcı Kalıp Döküm,.Yetenekler arasında EDI, mühendislik yardımı, katı modelleme ve ikincil işleme yer alır.
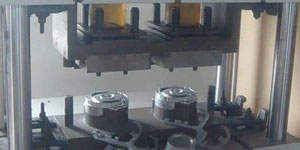
Döküm Endüstrileri Arabalar, Bisikletler, Uçaklar, Müzik aletleri, Deniz Araçları, Optik cihazlar, Sensörler, Modeller, Elektronik cihazlar, Muhafazalar, Saatler, Makineler, Motorlar, Mobilya, Mücevher, Jigler, Telekom, Aydınlatma, Tıbbi cihazlar, Fotoğraf cihazları, Robotlar, Heykeller, Ses ekipmanları, Spor ekipmanları, Aletler, Oyuncaklar ve daha fazlası.
Bundan sonra ne yapmanıza yardımcı olabiliriz?
∇ Ana Sayfaya Git Çin Döküm
→Döküm Parçaları-Ne yaptığımızı öğren.
→ Hakkında İlgili İpuçları Pres Döküm Hizmetleri
By Minghe Döküm Üreticisi |Kategoriler: Faydalı Makaleler |Malzeme Etiketler: Alüminyum Döküm, Çinko Döküm, Magnezyum Döküm, Titanyum Döküm, Paslanmaz Çelik Döküm, Pirinç Döküm,Bronz Döküm,Döküm Videosu,Tarihçe,Alüminyum Döküm |Yorumlar Kapalı