Pres Döküm Alaşımlarının Eritme Bilgisi
Eritme İşleminin Fiziksel ve Kimyasal Olayları
Alaşım eritme, kalıp döküm işleminin önemli bir parçasıdır. Eritme işlemi sadece erimiş metal elde etmek değil, daha da önemlisi, kalıp dökümün iyi bir kristal yapı ve çok küçük gaz ve inklüzyonlar içeren bir metal elde edebilmesi için gereksinimleri karşılayan bir kimyasal bileşim elde etmektir.
Eritme işlemi sırasında, metal ve gaz arasındaki etkileşim ve erimiş metal ile pota arasındaki etkileşim, bileşimde değişikliklere neden olarak inklüzyonlara ve inhalasyona neden olur. Bu nedenle, doğru ergitme prosesi düzenlemelerinin formüle edilmesi ve sıkı bir şekilde uygulanması, yüksek kaliteli dökümler elde etmek için önemli bir garantidir.
1. Metal ve gaz arasındaki etkileşim
Eritme işlemi sırasında karşılaşılan gazlar hidrojen (H2), oksijen (O2), su buharı (H2O), nitrojen (N2), CO2, CO vb. gazlardır. Bu gazlar erimiş metal içinde çözünür veya onlarla reaksiyona girer. Efekt.
2. Gazın kaynağı
Gaz, alaşım sıvısına fırın gazından, fırın astarından, hammaddelerden, akıdan, aletlerden vb. girebilir.
3. Metal ve pota arasındaki etkileşim
Eritme sıcaklığı çok yüksek olduğunda, demir pota çinko sıvısı ile hızlı bir şekilde reaksiyona girer ve potanın yüzeyinde demir oksidasyon reaksiyonu meydana gelir ve Fe2O3 gibi oksitler oluşturur; ek olarak, demir elementi ayrıca çinko sıvısı ile reaksiyona girerek içindeki çinko sıvısı içinde çözünen FeZn13 bileşiğini (çinko cürufu) oluşturur. Demir potanın duvar kalınlığı, hurdaya ayrılana kadar sürekli olarak azalır.
Erime Sıcaklık Kontrolü
1. Kalıp döküm sıcaklığı
Döküm için kullanılan çinko alaşımının erime noktası 382 ~ 386 ℃'dir ve uygun sıcaklık kontrolü çinko alaşımının kompozisyon kontrolünde önemli bir faktördür. Alaşım sıvısının boşluğu doldurmak için iyi akışkanlığını sağlamak için, kalıp döküm makinesinin çinko kabındaki erimiş metalin sıcaklığı 415 ~ 430 ℃'dir. İnce duvarlı ve karmaşık parçaların kalıp döküm sıcaklığının üst sınırı alınabilir; kalın duvarlı ve basit parçaların alt sınırı alınabilir. Merkezi eritme fırınındaki erimiş metalin sıcaklığı 430 ~ 450 ℃'dir. Deve boynuna giren erimiş metalin sıcaklığı temel olarak çinko kaptaki sıcaklıkla aynıdır.
Dökme sıcaklığı, çinko kaptaki erimiş çinkonun sıcaklığı kontrol edilerek doğru bir şekilde kontrol edilebilir ve şunları elde eder:
- ① Erimiş metal oksit içermeyen temiz bir sıvıdır;
- ② Dökme sıcaklığında dalgalanma olmaz.
Aşırı sıcaklığın zararları:
- ① Alüminyum ve magnezyum elementlerinin yanması.
- ② Metal oksidasyon hızı artar, yanma kaybı artar ve çinko cürufu artar.
- ③ Termal genleşmenin etkisi çekiç kafasının sıkışmasına neden olur.
- ④ Dökme demir potada alaşıma daha fazla demir eritilir ve çinko ile demir arasındaki reaksiyon yüksek sıcaklıklarda hızlanır. Demir-alüminyum intermetalik bileşiklerinin sert parçacıkları oluşur ve bu da çekiç kafasında ve kaz boynunda aşırı aşınmaya neden olur.
- ⑤ Buna göre yakıt tüketimi artar.
Çok düşük sıcaklık: Alaşımın akışkanlığı zayıftır, bu da şekillendirmeye elverişli değildir ve kalıp dökümlerinin yüzey kalitesini etkiler.
Mevcut pres döküm makinesi eritme potaları veya fırınları, sıcaklık ölçüm ve kontrol sistemleri ile donatılmıştır. Günlük çalışmalarda, sıcaklık ölçüm cihazlarının doğruluğunu sağlamak için çoğunlukla düzenli denetimler kullanılır. Taşınabilir termometreler (termometreler), fırının gerçek sıcaklığını düzenli olarak ölçmek ve düzeltmek için kullanılır.
Deneyimli kalıp döküm sendikaları erimeyi çıplak gözle gözlemler. Eriyik sıyırma işleminden sonra çok viskoz ve berrak değilse cüruf hızla yükselmez, bu da sıcaklığın uygun olduğunu gösterir; eriyik çok viskoz ise, sıcaklığın düşük olduğunu gösterir; Cüruftan sonra sıvı yüzeyinde bir kırağı tabakası belirir ve cüruf çok hızlı yükselir, bu da sıcaklığın çok yüksek olduğunu ve zamanla ayarlanması gerektiğini gösterir.
2. Sıcaklık nasıl sabit tutulur
- ① En iyi yöntemlerden biri: çinko külçe ergitmek üzere doğrudan çinko kabına eklendiğinde büyük sıcaklık değişikliklerinden kaçınmak için bir merkezi eritme fırını ve bir kalıp döküm makinesi fırını bir bekletme fırını olarak kullanın. Konsantre eritme, alaşım bileşiminin stabilitesini sağlayabilir.
- ② İkinci en iyi yöntem: gelişmiş metal sıvı otomatik besleme sisteminin kullanılması, sabit bir besleme hızı, alaşım sıvı sıcaklığı ve çinko kap sıvı seviyesini koruyabilir.
- ③ Mevcut üretim koşulları çinko kapta doğrudan besleme ise, beslemeden kaynaklanan sıcaklık değişimini azaltmak için küçük alaşımlı külçelerin eklenmesine bir kerede tüm alaşım külçesinin eklenmesi önerilir.
3. Çinko cürufu üretimi ve kontrolü
Alaşımı katıdan sıvıya eritmek karmaşık bir fiziksel ve kimyasal işlemdir. Gaz, erimiş metal ile kimyasal olarak reaksiyona girer ve oksijen reaksiyonu en güçlüsüdür ve alaşımın yüzeyi belirli bir miktarda pislik üretmek için oksitlenir. Cüruf, oksitler ve metaller arası demir, çinko ve alüminyum bileşikleri içerir. Eriyik yüzeyinden sıyrılan cüruf genellikle yaklaşık %90 çinko alaşımı içerir. Çinko cüruf oluşumunun reaksiyon hızı, erime sıcaklığı arttıkça katlanarak artar.
Normal şartlar altında, orijinal çinko alaşımlı külçenin cüruf çıkışı, %1 ila %0.3 aralığında olan %0.5'den azdır; yeniden eritme memelerinin ve atık iş parçalarının cüruf çıkışı genellikle %2 ile %5 arasındadır.
Çinko cüruf miktarının kontrolü
- ① Erime sıcaklığını sıkı bir şekilde kontrol edin, sıcaklık ne kadar yüksek olursa çinko cürufu o kadar fazla olur.
- ② Alaşım sıvısının çinko kapta karıştırılmasından mümkün olduğunca kaçının, herhangi bir şekilde karıştırmak, daha fazla alaşım sıvısının havadaki oksijen atomlarıyla temas etmesine ve böylece daha fazla köpük oluşmasına neden olacaktır.
- ③ Çok sık cüruf atmayın. Erimiş alaşım havaya maruz kaldığında oksitlenir ve pislik oluşturur. Fırın yüzeyinde ince bir köpük tabakası tutmak, tenceredeki sıvının daha fazla oksitlenmemesine yardımcı olacaktır.
- ④ Cüruf oluştururken, alaşım sıvısının karışmasını mümkün olduğunca önlemek için gözenekli (Ф6 mm) disk şeklinde bir cüruf tırmığı kullanarak pisliğin altını hafifçe kazıyın ve kazınmış cürufu alın. Erimiş metalin çinko tencereye geri akmasını sağlamak için hafifçe vurun.
Çinko cüruf tedavisi
- ① Kendi kendini işlemenin maliyeti daha yüksek olabileceğinden, hammadde tedarikçisine veya özel işleme tesisine geri sat.
- ② Pres döküm tesisi kendi başına halleder. Ayrı bir fırın gereklidir ve çinko cürufu yeniden eritme sıcaklığı 420 ila 440°C aralığındadır. Aynı anda akı ekleyin. 100 kg cürufu eritmek için önce metal yüzeye eşit olarak dağıtılan ve daha sonra bir karıştırıcı ile erimiş metale eşit olarak karıştırılan 0.5 ~ 1.5 kg akı eklenmesi gerekir (yaklaşık 2 ~ 4 dakika). 5 dakika beklettikten sonra yüzeyde bir tabaka oluşur, bu tabaka daha çok kir gibidir, bu yüzden kazıyın.
- ③ Nozul malzemeleri, nozul malzemelerini yeniden eriten atık parçalar, atık malzemeler, çöp yerleri, hurdaya ayrılan iş parçaları vb., yeniden eritme için doğrudan kalıp döküm makinesinin çinko kabına konmamalıdır. Bunun nedeni, bu meme malzemelerinin yüzeyinin kalıp döküm oluşturma işlemi sırasında oksitlenmesi ve çinko oksit içeriğinin orijinal alaşım külçesinden çok daha yüksek olmasıdır. Bu nozul malzemeleri çinko kapta yeniden eritildiğinde, çinko oksit yüksek sıcaklık koşullarında viskoz bir durumda olduğundan, çinko kaptan çıkarıldığında, büyük miktarda alaşım bileşeni alınacaktır. Meme malzemesini ve diğer malzemeleri yeniden eritmenin amacı çinko oksidi sıvı alaşımdan etkin bir şekilde ayırmaktır. Eritme sırasında bir miktar çözücü eklenmeli ve bir külçeye döküldükten sonra kullanılmalıdır.
4. Galvanik atıkların yeniden eritilmesi
Elektrokaplama atığı, elektrokaplama atığı içindeki bakır, nikel, krom ve diğer metaller çinkoda çözünmez olduğundan ve çinko alaşımında sert parçacıklar olarak bulunacağından, elektrokaplama olmayan atıklardan ayrı olarak eritilmelidir, bu da parlatma ve işlemede zorluklara neden olacaktır.
Elektrokaplama hurdasının yeniden eritilmesi sırasında kaplama malzemesinin çinko alaşımından ayrılmasına dikkat edin. Galvanik hurdayı önce çinko alaşımı eriyiği içeren potaya koyun. Bu sırada eriyiği karıştırmayın veya akı eklemeyin. Yüksek bir erime noktasına sahip olmak için kaplama malzemesini kullanın. Alaşım içinde erimez, ancak ilk süre için eriyiğin yüzeyinde yüzer. Tamamen eridiğinde, yüzeyde herhangi bir pislik olup olmadığını görmek için krozeyi 15-20 dakika bekletin ve pisliği kazıyarak temizleyin. Bu işlemden sonra rafinaj maddesi eklemenin gerekli olup olmadığını göreceğiz.
5. Eritme işleminde dikkat edilmesi gereken hususlar
- 1. Pota: Kullanmadan önce yüzeydeki yağ, pas, cüruf ve oksitleri temizlemek için temizlenmelidir. Dökme demir potadaki demir elementin alaşımda çözülmesini önlemek için, pota 150 ~ 200 ℃'ye önceden ısıtılmalı, çalışma yüzeyine bir kat boya püskürtülmeli ve ardından tamamen çıkarmak için 200 ~ 300 ℃'ye ısıtılmalıdır. boyadaki su.
- 2. Aletler: Eritme aletleri kullanılmadan önce yüzeydeki kirler temizlenmeli, metalle temas eden kısımlar önceden ısıtılmalı ve boyanmalıdır. Alet ıslatılmamalıdır, aksi takdirde eriyiğin sıçramasına ve patlamasına neden olur.
- 3. Alaşımlı malzeme: yüzeyde emilen nemi çıkarmak için eritmeden önce temizleyin ve ön ısıtın. Alaşım bileşimini kontrol etmek için yeni malzemenin 2/3'ü ve geri dönüştürülmüş malzemenin 1/3'ü kullanılması tavsiye edilir.
- 4. Erime sıcaklığı 450°C'yi geçmemelidir.
- 5. Çinko tencerede sıvı yüzeyindeki köpüğü zamanında temizleyin, çinko malzemesini zamanında doldurun ve eriyik seviyesinin normal yüksekliğini koruyun (pota yüzeyinde 30 mm'den az değil), çünkü çok fazla köpük ve çok düşük sıvı seviyesi kolaydır Malzeme cürufu kuğuboynu silindire girer, çelik dizgiyi, çekiç kafasını ve silindirin kendisini zorlar, bu da çekiç kafası, kuğu boynu ve çekiç kafası hurdasının sıkışmasına neden olur.
- 6. Eriyik üzerindeki pislik, çıkarmak üzere biriktirmek üzere bir cüruf kazıyıcı ile hafifçe çalkalanır.
Lütfen yeniden basım için bu makalenin kaynağını ve adresini saklayın: Pres Döküm Alaşımlarının Eritme Bilgisi
Minhe Basınçlı Döküm Şirketi kaliteli ve yüksek performanslı Döküm Parçaları üretmeye ve sağlamaya adamıştır (metal döküm parça yelpazesi esas olarak şunları içerir: İnce Duvarlı Döküm,Sıcak Kamara Basınçlı Döküm,Soğuk Oda Döküm), Yuvarlak Servis (Döküm Servisi,Cnc İşleme,Kalıp yapımı,Yüzey İşleme).Herhangi bir özel Alüminyum döküm, magnezyum veya Zamak/çinko döküm ve diğer döküm gereksinimleri bizimle iletişime geçebilirsiniz.
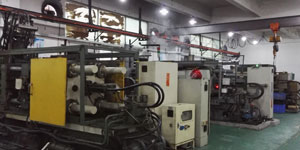
ISO9001 ve TS 16949 kontrolünde, tüm işlemler yüzlerce gelişmiş basınçlı döküm makinesi, 5 eksenli makine ve blasterlerden Ultra Sonic yıkama makinelerine kadar diğer tesisler aracılığıyla gerçekleştirilir. Müşterinin tasarımını gerçeğe dönüştürmek için deneyimli mühendisler, operatörler ve müfettişlerden oluşan ekip.
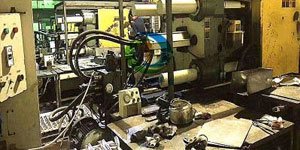
Dökümlerin sözleşmeli üreticisi. Yetenekler, 0.15 lbs'den başlayan soğuk oda alüminyum döküm parçaları içerir. 6 lbs'ye kadar, hızlı değişim kurulumu ve işleme. Katma değerli hizmetler arasında polisaj, titreşim, çapak alma, kumlama, boyama, kaplama, kaplama, montaj ve kalıplama yer alır. Çalışılan malzemeler arasında 360, 380, 383 ve 413 gibi alaşımlar bulunur.
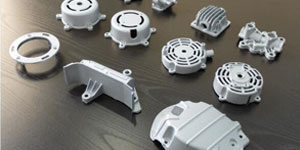
Çinko pres döküm tasarım yardımı/eşzamanlı mühendislik hizmetleri. Hassas çinko dökümlerin özel üreticisi. Minyatür dökümler, yüksek basınçlı dökümler, çok kızaklı kalıp dökümleri, geleneksel kalıp dökümleri, birim kalıp ve bağımsız kalıp dökümleri ve boşluklu sızdırmaz dökümler üretilebilir. Dökümler, +/- 24 inç toleransta 0.0005 inç'e kadar uzunluk ve genişliklerde üretilebilir.
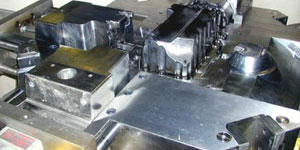
ISO 9001: 2015 sertifikalı döküm magnezyum üreticisi, Yetenekler arasında 200 ton sıcak odaya ve 3000 ton soğuk odaya kadar yüksek basınçlı magnezyum kalıp dökümü, takım tasarımı, cilalama, kalıplama, işleme, toz ve sıvı boyama, CMM özelliklerine sahip tam kalite güvencesi bulunur , montaj, paketleme ve teslimat.
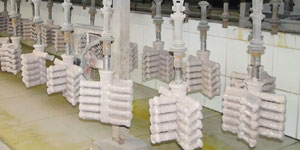
ITAF16949 sertifikalı. Ek Döküm Hizmeti Dahil yatırım dökümleri,kum dökümü,Yerçekimi Döküm, Kayıp Köpük Döküm,Savurma döküm,Vakumlu Döküm,Kalıcı Kalıp Döküm,.Yetenekler arasında EDI, mühendislik yardımı, katı modelleme ve ikincil işleme yer alır.
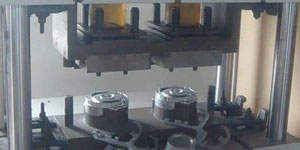
Döküm Endüstrileri Arabalar, Bisikletler, Uçaklar, Müzik aletleri, Deniz Araçları, Optik cihazlar, Sensörler, Modeller, Elektronik cihazlar, Muhafazalar, Saatler, Makineler, Motorlar, Mobilya, Mücevher, Jigler, Telekom, Aydınlatma, Tıbbi cihazlar, Fotoğraf cihazları, Robotlar, Heykeller, Ses ekipmanları, Spor ekipmanları, Aletler, Oyuncaklar ve daha fazlası.
Bundan sonra ne yapmanıza yardımcı olabiliriz?
∇ Ana Sayfaya Git Çin Döküm
→Döküm Parçaları-Ne yaptığımızı öğren.
→ Hakkında İlgili İpuçları Pres Döküm Hizmetleri
By Minghe Döküm Üreticisi |Kategoriler: Faydalı Makaleler |Malzeme Etiketler: Alüminyum Döküm, Çinko Döküm, Magnezyum Döküm, Titanyum Döküm, Paslanmaz Çelik Döküm, Pirinç Döküm,Bronz Döküm,Döküm Videosu,Tarihçe,Alüminyum Döküm |Yorumlar Kapalı