Karbürleme ve su vermede yaygın kusurların ve önleyici tedbirlerin toplanması
Sementleme ve su verme aslında kompozit bir işlemdir, yani karbonlama + su verme. Genellikle ikisi hakkında konuşmaya alışkınız, çünkü aynı ekipman üzerinde tamamlanan iki işlem üretimde en sık karşılaşılan işlemlerdir (ancak karbonlamalı hava soğutması, karbonlamalı yavaş soğutma ve ardından yeniden ısıtma ve söndürme işlemleri de vardır ve ikincil işlemler de vardır). O zaman üretimde karşılaşılan istenmeyen olayların bazıları karbonlama problemleri, bazıları su verme problemleri ve bazıları karbonlama ve su vermenin birleşik etkilerinin sonucudur.
Tüm ısıl işlem süreçlerinin üç temel konudan ayrılamayacağını biliyoruz: ısıtma, ısı koruma ve soğutma. Isıtma sıcaklığı, ısıtma hızı, bekletme süresi, soğutma hızı ve tabii ki atmosfer sorunları dahil olmak üzere ayrıntılı olarak. Dolayısıyla, bir kez bir şeyler ters gittiğinde, alışılmış bir şekilde sebebi bu yönlerden analiz edeceğiz.
Karbürleme ve su verme için genellikle şu göstergeleri test ederiz: ürün yüzey görünümü, yüzey sertliği, çekirdek sertliği, karbonlanmış katman derinliği, (etkin sertleştirilmiş katman derinliği, tamamen sertleştirilmiş katman derinliği) metalografik yapı ve deformasyon. Bu göstergelerle ilgili görüşlerimi sırasıyla paylaşalım.
1. Görünüm sorunu
1. Oksit skalası: Bunun başlıca nedeni ekipman sızıntısı, saf olmayan taşıyıcı gaz veya su içeriğidir. Bunun nedenini ekipman ve hammaddelerden bulmak gerekir.
2. En sıkıntılı bir diğer sorun ise, modern zamanlarda ısıl işlemin yeni ve zorlu bir gerekliliği olan leke sorunudur. Nedenleri karmaşık ve çok derin.
XNUMX. niteliksiz sertlik
1. Yüksek sertlik (tartışılmadı)
2. Düşük sertlik: İki durum vardır, biri niteliksiz karbonlamadır. Bunun nedeni, karbonlanmış katmanın çizimlerin gereksinimlerini karşılamak için çok sığ olması (karbürlenmiş katman sızmamış) veya seçilen algılama ölçeğinin, karbonlanmış katmanı parçalayacak olan mevcut karbonlanmış katmanın tolere edilebilir aralığını aşması olabilir.
Çözüm: Sızıntıyı yenileyin ve inceleme cetvelini takip edin. JBT 6050-2006 "Çelik Parçaların Isıl İşlem Sertlik Muayenesi için Genel Prensipler" Karbürlenmiş tabakanın derinliği aslında sıcaklık, zaman ve karbon potansiyelinin bir fonksiyonudur. Yukarıdaki faktörlerden ısıtma sıcaklığını artırmanın, tutma süresini uzatmanın ve karbonlama potansiyelini artırmanın yollarını düşünebiliriz. (Tabii ki her parametrenin ayarlanması tamamen kendi ekipman ve ürünlerinizin gereksinimleri ile birleştirilmelidir) Yüzeyde at dışı organizasyonların varlığından da kaynaklanabilir. Sertliğin düşük olduğu, yani karbonlamanın nitelikli olduğu, ancak su vermenin niteliksiz olduğu durumlarda başka bir durum ortaya çıkar. Genel olarak, söndürülmez. Bu durum, söylendiği gibi en karmaşık olanıdır: ısıl işlem, dörtte üçü ısıtmaya ve dörtte üçü soğutmaya dayanır. Ayrıca soğutma işleminin ısıl işlem sürecinde işgal ettiği konumu da yansıtır.
Aşağıdaki, tasarladığım karşılaştırmalı bir testtir. Soğutmanın sertlik üzerindeki etkisini tartışabilirsiniz.
Boyutları Φ3mmX20mm olan, farklı malzemelerden ancak aynı özelliklere ve boyutlara sahip 100 grup test çubuğu alın. (Biz No. 20 çelik test çubuğu No. 1, 20Cr test çubuğu No. 2 ve 20CrMnTi test çubuğu No. 3 olarak adlandırıyoruz.) Test çubukları aynı işlem kullanılarak aynı ısıda karbonlanır. Üç test çubuğunun karbonlanmış katman derinliğinin 0.6-0.7 mm olduğu varsayılırsa (ps: varsayım yalnızca ideal bir durumda kurulmuştur).
Lütfen aşağıdaki koşulları göz önünde bulundurun:
bir. Aynı koşullar altında söndürmeyi bitirin
b. Söndürme ortamı yavaş yağ, hızlı yağ, temiz su, tuzlu sudur.
c. Karıştırmadan ve yoğun bir şekilde karıştırmadan ve söndürmeden aynı ortamda, üç test çubuğunun her biri test için iki grup halinde alınır.
Sementasyon tamamlandıktan sonra A grubuna 800 derecede, B grubuna 860 derecede su verilir. Sertliklerinin yüksekten düşüğe sıralaması nasıldır? Sertleştirilmiş katman (sınır olarak 550HV1.0 ile) derinden sığa nasıl sıralanır? Aynı malzemeden iki test çubuğu alın ve karşılaştırın ve test edin, hangi grup daha yüksek su verme sertliği ve etkin sertleştirilmiş katman derinliği elde edebilir?
Yukarıdaki test sonuçlarından, karbürlenmiş tabakanın derinliğinin, etkili sertleştirilmiş tabakanın derinliğine eşit olmadığı ve gerçek sertleştirilmiş tabaka derinliğinin, malzemenin sertleşebilirliğinden, söndürme sıcaklığından ve soğutmadan etkilendiği sonucuna varılabilir mi? oran. Soğutma ortamının soğutma özellikleri ve söndürme yoğunluğu da söndürme etkisini etkiler. Yukarıdakiler kişilerin görüşleridir, eksiklik varsa ekleyebilirsiniz. Elbette parçaların boyut etkisi de sertleşme etkisini etkiler.
Bence deneyimli bir denetçi, diğer test yöntemlerini düzenleyerek ve birleştirerek düşük sertliğin gerçek nedenini belirleyebilir ve ardından bunu çözmek için gerçek nedeni bulabilir; Bir zanaatkar olarak, geleneksel metal hammaddelerin özelliklerine aşina iseniz, Kendi ekipmanının ve ortamının soğutma performansı, karbonlama ve su verme işlemlerinin formülasyonuna büyük yardımcı olan belirli bir tanınma düzeyine ulaşmıştır.
3. Eşit olmayan sertlik: tek tip fırın sıcaklığı (sementasyon homojenliğini etkiler), ekipman yapısı, atmosfer sirkülasyonu, fırın yükleme, (sementasyon tabakasının homojenliğini etkiler ve aynı zamanda su verme homojenliğini etkiler)
4. Çekirdek sertliği niteliksizdir. Çok yüksek: söndürme sıcaklığı çok yüksek, malzemenin sertleşebilirliği çok iyi, karbon ve alaşım bileşiminin üst sınırı ve orta soğutma hızı çok hızlı. Çekirdek sertliği düşüktür: tam tersi.
Örnek paylaşım: 20# çelik 1.5mm ürün, gereksinimler: sızma katmanı 0.2-0.4mm çekirdek HV250, aynı sektördeki bazı arkadaşlar gereksinimlerin mantıksız olduğunu düşünüyor, (herkes bilmeli ki 20# çelik levha martensitinin en yüksek sertliği olacaktır. HV450-470) Bu sorunu çözmek için öncelikle bu malzemenin özelliklerini anlamalıyız: sertleşebilirlik ve sertleşebilirlik dahil.
Ardından, söndürme etkisini etkileyen yukarıda belirtilen faktörleri birleştirin ve ısıtmanın ve soğutmanın yollarını bulun. Bu durumda, malzeme sabittir. Söndürme sıcaklığından ve soğutma hızından bir yol bulabiliriz. Bu üretici aşırı hızlı yağ kullanıyor. Söndürme yoğunluğunu azaltmak gereksinimleri karşılamıyorsa, söndürme sıcaklığını da düşürebiliriz. Yöntem.
Yine aynı cümle, 860-760 dereceden, (sıcaklık belirli bir seviyeye düşürüldüğünde, çekirdekteki aşırı soğutulmuş östenitten belirli bir miktar ferrit çökelecek ve bu sırada sertlik düşecektir. , Daha fazla sıcaklık düşerse, çökeltilen ferrit miktarı arttıkça sertlik azalır.
İşte bir hatırlatma: Ekipmanın mevcut koşullarını tam olarak birleştirmek ve özel uygun sığ geçirgenlik endeksi hakkında yaygara yapmak gerekir.
3. Karbürlenmiş tabaka veya etkili karbonlanmış tabaka daha derin ve daha sığdır.
Daha önce bahsedildiği gibi, infiltrasyon tabakasının derinliği sıcaklık, zaman ve karbon konsantrasyonunun kapsamlı bir fonksiyonudur. Bu sorunu çözmek için, ısıtma sıcaklığı, ısıtma hızı, tutma süresi, soğutma hızı ve karbon katmanındaki karbon konsantrasyon gradyanını kontrol ederek başlamalıyız. Sıcaklık ne kadar yüksek olursa, süre o kadar uzun olur ve karbon potansiyeli ne kadar yüksek olursa, infiltrasyon tabakası o kadar derin olur ve bunun tersi de geçerlidir.
Ama aslında, bu basit olmaktan çok daha fazlasıdır. Bir karbonlama prosesi tasarlamak için ayrıca ekipmanı, fırın kapasitesini, yağ özelliklerini, metalografik yapıyı, malzemenin sertleşebilirliğini, karbonlu katmandaki karbon konsantrasyon gradyanını ve soğutma hızını da göz önünde bulundurmalısınız. Ve diğer birçok faktör. Bu, önceki düşük sertlik durumuna referansla analiz edilebilir ve derinlemesine açıklanmayacaktır.
Dördüncüsü, metalografik organizasyon
Aşırı martenzit: Hammaddede iri taneler var veya normalize edilmemiş ve karbonlama sıcaklığı çok yüksek. Çözüm: normalleştirme veya çoklu normalleştirme, (normalleştirme sıcaklığının karbonlama sıcaklığından 20-30 derece daha yüksek olması önerilir) Mümkünse, karbonlama ve yavaş soğutmayı ve ardından yeniden ısıtma ve söndürmeyi düşünün
Aşırı Paralimpik: söndürme sıcaklığı çok yüksek, östenitteki karbon içeriği çok yüksek (karbon potansiyeli çok yüksek). Çözüm: Tam difüzyon ve koşullar izin verirse, söndürme sıcaklığını, yüksek sıcaklıkta temperlemeyi ve yeniden ısıtmayı ve söndürmeyi veya kriyojenik muameleyi azaltabilir.
Aşırı karbür: östenitte çok yüksek karbon içeriği (çok yüksek karbon potansiyeli), çok yavaş soğutma işlemi, karbür çökelmesi
Çözüm: tamamen dağıtın, soğutma hızını kontrol edin, karbonlama ve su verme arasındaki sıcaklık farkını mümkün olduğunca azaltın ve düşük sıcaklıkta veya düşük sıcaklıkta söndürmeyi mümkün olduğunca az kullanın. Bu prosesin kullanılması gerekiyorsa fırın yükü kontrol edilmelidir. Düşünelim: aynı ekipman 920°C'de karbonlanır ve 820°C'de su verilir. Fırın kapasitesi 1000kg ve 600kg ve soğutma hızı aynı mı? Hangisi daha uzun sürecek? Hangi karbür kalitesi daha yüksektir?
Beşler. At dışı ve dahili oksidasyon
İç oksidasyon: Çelikte bulunan krom, manganez ve molibden gibi alaşım elementleri ile atmosferdeki oksitleyici atmosferin (başlıca oksijen, su, karbon dioksit) arasında oluşan ve matristeki alaşım elementlerini tüketerek azalmaya neden olan reaksiyondur. malzemenin sertleşebilirliği. Mikroskop altında siyah ağ yapısı görülebilir, özü matristeki alaşım elementlerinin tükenmesi ve sertleşebilirliğin azalmasıyla elde edilen troostit yapısıdır.
Çözüm, ortamın soğutma hızını arttırmanın, söndürme yoğunluğunu arttırmanın ve fırındaki oksitleyici atmosferi azaltmanın yollarını bulmaktır (karbonlama ham ve yardımcı malzemelerinin saflığını sağlamak, dengeli hava miktarını en aza indirmek, dengeli havayı kontrol etmek). havadaki nem içeriği ve ekipmanın sızdırmadığından emin olun.Yeterli egzoz) Konvansiyonel ekipmanın ortadan kaldırılması zordur. Düşük basınçlı vakumlu karbonlama ekipmanının tamamen ortadan kaldırılabileceği söylenir. Ek olarak, güçlü bilyeli dövme, dahili oksidasyon seviyesini de azaltabilir.
Bazı uzmanların görüşlerini okudum ve bazıları karbonitrürleme işlemindeki aşırı amonyağın ciddi atsızlığa da neden olabileceğine inanıyor. Kişisel olarak bu konuda farklı bir fikrim var: belki de amonyaktaki aşırı su içeriğinden kaynaklanıyordur? Birçok karbonitrürleme işlemine maruz kaldığım için, ürünü incelerken ata ait olmayan belirgin bir doku bulunamadı. (Ama bu görüşün yanlış olduğunu düşünmüyorum) Bazı yabancı makine sanayileri, özellikle dişli sektörü olmak üzere iç oksidasyona büyük önem veriyor. Yurtiçinde, derinliğin genellikle nitelikli olarak 0.02 mm'den fazla olmaması gerekir.
Martensitik olmayan: Ferrit, beynit ve tabii ki iç oksidasyon tipi troostit gibi su verme sonrası karbürizasyon veya su verme problemlerinden dolayı karbürlenmiş tabakanın yüzeyinde martensitik olmayan yapı görülür. Üretim mekanizması, iç oksidasyona benzer ve çözüm de benzerdir.
Altı. deformasyon sorunu
Bu bir sistem sorunudur ve aynı zamanda ısıl işlem yapan personelimiz için de en sıkıntılı sorundur. Hammadde proses soğutma ortamının çeşitli yönlerinden garanti edilir. Yukarıdaki içerik yalnızca kişisel bir deneyimdir. Herhangi bir tutarsızlık varsa, beni düzeltebilirsiniz, teşekkür ederim.
Lütfen yeniden basım için bu makalenin kaynağını ve adresini saklayın:Karbürleme ve su vermede yaygın kusurların ve önleyici tedbirlerin toplanması
Minhe Basınçlı Döküm Şirketi kaliteli ve yüksek performanslı Döküm Parçaları üretmeye ve sağlamaya adamıştır (metal döküm parça yelpazesi esas olarak şunları içerir: İnce Duvarlı Döküm,Sıcak Kamara Basınçlı Döküm,Soğuk Oda Döküm), Yuvarlak Servis (Döküm Servisi,Cnc İşleme,Kalıp yapımı,Yüzey İşleme).Herhangi bir özel Alüminyum döküm, magnezyum veya Zamak/çinko döküm ve diğer döküm gereksinimleri bizimle iletişime geçebilirsiniz.
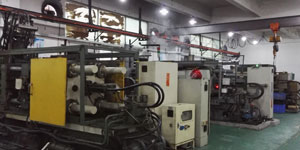
ISO9001 ve TS 16949 kontrolünde, tüm işlemler yüzlerce gelişmiş basınçlı döküm makinesi, 5 eksenli makine ve blasterlerden Ultra Sonic yıkama makinelerine kadar diğer tesisler aracılığıyla gerçekleştirilir. Müşterinin tasarımını gerçeğe dönüştürmek için deneyimli mühendisler, operatörler ve müfettişlerden oluşan ekip.
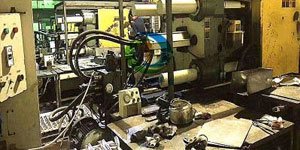
Dökümlerin sözleşmeli üreticisi. Yetenekler, 0.15 lbs'den başlayan soğuk oda alüminyum döküm parçaları içerir. 6 lbs'ye kadar, hızlı değişim kurulumu ve işleme. Katma değerli hizmetler arasında polisaj, titreşim, çapak alma, kumlama, boyama, kaplama, kaplama, montaj ve kalıplama yer alır. Çalışılan malzemeler arasında 360, 380, 383 ve 413 gibi alaşımlar bulunur.
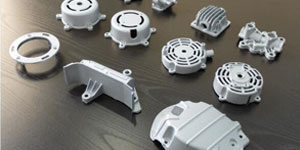
Çinko pres döküm tasarım yardımı/eşzamanlı mühendislik hizmetleri. Hassas çinko dökümlerin özel üreticisi. Minyatür dökümler, yüksek basınçlı dökümler, çok kızaklı kalıp dökümleri, geleneksel kalıp dökümleri, birim kalıp ve bağımsız kalıp dökümleri ve boşluklu sızdırmaz dökümler üretilebilir. Dökümler, +/- 24 inç toleransta 0.0005 inç'e kadar uzunluk ve genişliklerde üretilebilir.
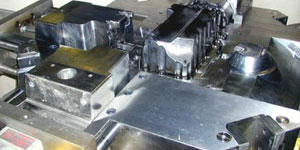
ISO 9001: 2015 sertifikalı döküm magnezyum üreticisi, Yetenekler arasında 200 ton sıcak odaya ve 3000 ton soğuk odaya kadar yüksek basınçlı magnezyum kalıp dökümü, takım tasarımı, cilalama, kalıplama, işleme, toz ve sıvı boyama, CMM özelliklerine sahip tam kalite güvencesi bulunur , montaj, paketleme ve teslimat.
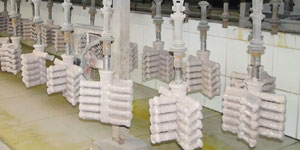
ITAF16949 sertifikalı. Ek Döküm Hizmeti Dahil yatırım dökümleri,kum dökümü,Yerçekimi Döküm, Kayıp Köpük Döküm,Savurma döküm,Vakumlu Döküm,Kalıcı Kalıp Döküm,.Yetenekler arasında EDI, mühendislik yardımı, katı modelleme ve ikincil işleme yer alır.
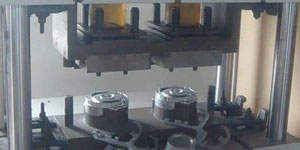
Döküm Endüstrileri Arabalar, Bisikletler, Uçaklar, Müzik aletleri, Deniz Araçları, Optik cihazlar, Sensörler, Modeller, Elektronik cihazlar, Muhafazalar, Saatler, Makineler, Motorlar, Mobilya, Mücevher, Jigler, Telekom, Aydınlatma, Tıbbi cihazlar, Fotoğraf cihazları, Robotlar, Heykeller, Ses ekipmanları, Spor ekipmanları, Aletler, Oyuncaklar ve daha fazlası.
Bundan sonra ne yapmanıza yardımcı olabiliriz?
∇ Ana Sayfaya Git Çin Döküm
→Döküm Parçaları-Ne yaptığımızı öğren.
→ Hakkında İlgili İpuçları Pres Döküm Hizmetleri
By Minghe Döküm Üreticisi |Kategoriler: Faydalı Makaleler |Malzeme Etiketler: Alüminyum Döküm, Çinko Döküm, Magnezyum Döküm, Titanyum Döküm, Paslanmaz Çelik Döküm, Pirinç Döküm,Bronz Döküm,Döküm Videosu,Tarihçe,Alüminyum Döküm |Yorumlar Kapalı