Çizim Kalıp Tasarımında Yedi Önlem
Germe kalıpları, tüm damgalama kalıbı endüstrisinin çok büyük bir bölümünü oluşturur. Ortak kaplarımız, motor üzerindeki kabuk ve hemen hemen çoğu üründe az ya da çok gerdirilmesi gereken ürünler bulunur. Kalıbın tasarımı, geleneksel algoritmaya göre hesaplanabileceğini söylemek değildir. Değişkenlerle dolu çok fazla süreç var, özellikle de dönmeyen bazı cisimlerin esnetilmesi, ki bu yasak.
Çünkü çekme kalıbının tasarımında çekme katsayısı, malzemenin sınırına ulaşıp ulaşmadığı, yay kuvvetinin kararı, çekme yönü, yukarı mı aşağı mı olduğu gibi çok fazla faktör göz önünde bulundurulur. , genellikle olamaz Tek seferlik kalıplama, istenen sonucu elde etmek için birçok deneme gerektirir ve bazen kalıp hurdaya ayrılabilir. Bu nedenle, pratikte birikmiş deneyim, çizim kalıbının tasarımına çok yardımcı olur.
Ayrıca kesme malzemesinin boyutu da kalıbın tamamının deneme üretiminde önemli bir rol oynar. Bu nedenle çoğu zaman, bazı düzensiz derin çekilmiş parçalar tasarladığımızda, kalıp tasarım aşamasında genellikle boş bir adım bırakırız.
germe malzemesi
Müşterinin malzeme gereksinimleri çok zorlayıcı olmadığında ve tekrarlanan kalıp denemeleri gereksinimleri karşılayamadığında, iyi çekme özelliklerine sahip bir malzemeye geçebilir ve tekrar deneyebilirsiniz. İyi bir malzeme başarının yarısıdır. Germe için, göz ardı edilmemelidir. Çekme için soğuk haddelenmiş ince çelik saclar esas olarak 08Al, 08, 08F, 10, 15 ve 20 çelikleri içerir. En büyük miktar, çerçeveli çelik ve öldürülmüş çelik olarak ayrılan 08 çeliktir. Kenarlı çelik fiyatı düşüktür ve iyi yüzey kalitesine sahiptir. Ayrışma daha ciddidir ve "gerilme yaşlanması" eğilimine sahiptir. Yüksek damgalama performansı ve görünüm gereksinimleri gerektiren parçalar için uygun değildir. Öldürülmüş çelik, tek tip performansla ancak daha yüksek fiyatla daha iyidir. Temsili marka, alüminyumla öldürülmüş çelik 08Al'dir. Yabancı çelik, Japon SPCC-SD derin çekme çeliğini kullanmıştır ve çekme özellikleri 08Al'den daha iyidir.
Kalıp yüzeyinin bitişi
Derin çekme yapılırken, kalıbın iki tarafı ve boşluk tutucu yeterince taşlanmaz, özellikle paslanmaz çelik levhalar ve alüminyum levhalar çizilirken, ağır durumlarda çekme kırılmalarına yol açabilen çekme izlerinin oluşması daha olasıdır.
Boşluğun boyutunun belirlenmesi
Daha fazla kırışıklık ve daha az çatlak prensibimizdir. Boş konumlandırma tasarımı doğru olmalıdır. Basit şekle sahip dönen gövde çekme parçasının boş çapı incelmiyor. Malzeme kalınlığı değişse de temelde orijinal kalınlığa çok benzer. Yakınlık, boşluğun alanı ile gerilmiş kısmın (kırpma eklenmesi gerekiyorsa) alanının eşit olması ilkesine göre hesaplanabilir. Bununla birlikte, gerilmiş parçaların şekli ve işlemi genellikle karmaşıktır ve bazen inceltilip gerdirilmeleri gerekir. Açılım hesaplamaları yapabilen birçok 3D yazılım olmasına rağmen bunların doğruluğu gereksinimleri %100 karşılayamaz.
Bir ürün birden fazla işlemden geçmelidir ve ilk işlem genellikle bir körleme işlemidir. Her şeyden önce, körleme kalıbının toplam boyutunu belirlemek için, katlanmamış malzemenin hesaplanmasını yapmak ve boşluğun şekli ve boyutu hakkında genel bir anlayışa sahip olmak gerekir. Kalıp tasarımı tamamlandıktan sonra körleme kalıbının dışbükey ve içbükey kalıp boyutunu işlemeyin. Boşluğu işlemek için önce tel kesmeyi kullanın (boşluk daha büyük olduğunda, bir freze makinesiyle frezelenebilir ve ardından sıkıştırılabilir). Müteakip germe işleminde tekrarlanan deneylerden sonra, boşluğun boyutu nihayet belirlenir ve ardından boşluk kalıbının dışbükey ve içbükey kalıpları işlenir.
Tersine çevrilmiş işlemde, önce çizim kalıbını deneyin ve ardından eforun yarısı olan boşluğun boşluk kenar boyutunu işleyin.
Çekme Katsayısı
Germe katsayısı, germe işleminin hesaplanmasında ana işlem parametrelerinden biridir ve genellikle germe sırasını ve sayısını belirlemek için kullanılır.
Malzeme özellikleri, malzemenin nispi kalınlığı, germe yöntemi (boş tutucunun olup olmadığına atıfta bulunarak), germe süreleri, germe hızı, dışbükey ve içbükey kalıp köşe yarıçapı, yağlama vb. dahil olmak üzere germe katsayısı m'yi etkileyen birçok faktör vardır. .
Çekme katsayısı m'nin hesaplama ve seçim ilkeleri, çeşitli damgalama kılavuzlarında tanıtılan kilit noktalardır. Hesaplama, tablo arama, hesaplama gibi birçok yöntem var ve ben de kitabına göre seçiyorum. Yeni bir şey yok. Lütfen kitabı okuyun. .
Malzemenin nispi kalınlığı, gerdirme yöntemi (boş tutucu olup olmadığına atıfta bulunarak) ve gerdirme sayısı kalıbı tamir ederken ayarlamak kolay değildir, bu yüzden dikkatli olmalısınız. Germe katsayısı m'yi seçerken kontrol etmek için bir meslektaş bulmak en iyisidir.
işleme yağı seçimi
İşleme yağı seçimi çok önemlidir. Yağlama yağının uygun olup olmadığını anlamanın yolu, ürün kalıptan çıkarıldığında, eğer ürün sıcaklığı el değmeyecek kadar yüksekse, yağlama yağı seçimi ve yağlama yöntemi yeniden gözden geçirilmeli ve yağlama yöntemi tekrar gözden geçirilmelidir. boşluğa yağlama yağı uygulanmalıdır. , Veya kağıda bir film poşeti koyun.
Çekme çatlaması olması durumunda, içbükey kalıba yağlama yağı uygulayın (dışbükey kalıba uygulamayın) ve iş parçası, içbükey kalıp tarafında 0.013-0.018 mm'lik bir plastik film ile kaplanır.
İş parçası ısıl işlem
Her ne kadar tavsiye edilmese de germe işlemi sırasında iş parçasının soğuk plastik deformasyon nedeniyle soğuk işleme sertleşmesine uğrayacağını ve bunun plastisitesini azaltacağını ve deformasyon direncini ve sertliğini artıracağını söylemek gerekir. Mantıksız kalıp tasarımına ek olarak, yapılması gerekiyor. Metali yumuşatmak ve plastisiteyi geri kazandırmak için ara tavlama.
Not: Genel işlemde ara tavlama gerekli değildir. Sonuçta, maliyeti artırmak gerekiyor. İşlemi artırmak ve tavlamayı artırmak arasında seçim yapmalı ve dikkatli kullanmalısınız!
Tavlama genellikle düşük sıcaklıkta tavlamayı, yani yeniden kristalleştirme tavını benimser. Tavlama yaparken dikkat edilmesi gereken iki şey vardır: dekarburizasyon ve oksidasyon. Burada esas olarak oksidasyon hakkında konuşuyoruz. İş parçası oksitlendikten sonra oksit tabakası oluşacaktır ve bunun iki zararı vardır: İş parçasının etkin kalınlığını inceltir ve kalıbın aşınmasını artırır.
Şirket koşullarının uygun olmadığı durumlarda genellikle normal tavlama yapılır. Oksit tufal üretimini azaltmak için tavlama sırasında fırın mümkün olduğunca doldurulmalıdır. Ayrıca toprak yöntemlerini de kullandım:
- Birkaç parça olduğunda, diğer parçalarla karıştırılabilir (öncül: tavlama işlemi parametreleri temelde aynı olmalıdır)
- İş parçasını demir kutuya koyun ve ardından fırına kaynak yapın. Oksit tortusunu ortadan kaldırmak için tavlama sonrası duruma göre dekapaj işlemi yapılmalıdır.
Firma şartları müsait olduğunda azot fırını tavlama yani parlak tavlama kullanılabilir. Yakından bakmazsanız, renk tavlama öncesi ile hemen hemen aynıdır.
Deneme kalıbında güçlü soğuk işlem sertleşmesi veya çekme çatlakları olan metalle başa çıkmanın başka bir yolu olmadığında, ara tavlama işlemini ekleyin.
Birkaç nokta ekleyin
- Ürün çizimindeki ölçü, dış ölçünün mü yoksa iç boşluk ölçüsünün mü garanti edildiğini netleştirmek için mümkün olduğunca bir tarafta işaretlenmelidir ve iç ve dış ölçüler aynı anda işaretlenemez. Başkaları tarafından sağlanan çizimlerin bu tür sorunları varsa, onlarla iletilmelidir. Birleşebilirlerse, birleştirilmeleri gerekir. Birleştirilemezlerse, iş parçası ile diğer parçalar arasındaki montaj ilişkisini bilmelidirler.
- Son işlem için, iş parçasının boyutu dışarıdadır, ana kalıptır, zımba boyutunun küçültülmesiyle boşluk elde edilir; iş parçasının boyutu içeride, zımba ana kalıptır ve boşluk, kalıbın boyutu artırılarak elde edilir;
- Dışbükey ve içbükey kalıpların köşe yarıçapı, sonraki kalıp onarımına kolaylık sağlayacak şekilde mümkün olduğunca küçük tasarlanmalıdır.
- İş parçası çatlamasının nedenini değerlendirirken şunlara bakın: Kötü malzeme kalitesinden kaynaklanan çatlaklar çoğunlukla tırtıklı veya düzensiz şekillerdedir ve işlemden ve kalıptan kaynaklanan çatlaklar genellikle nispeten düzgündür.
- "Daha fazla kırışıklık, daha az çatlak". Bu prensibe göre malzemenin akışını ayarlayın. Yöntemler, boşluk tutucunun basıncını ayarlamayı, çekme boncukunu arttırmayı, dışbükey ve içbükey kalıp filetosunun yarıçapını kırpmayı ve iş parçası üzerindeki işlem açıklığını kesmeyi içerir.
- Aşınma direncini sağlamak ve çekme çiziklerini önlemek için dışbükey ve içbükey kalıp ve boşluk tutucu su verilmiş veya sert krom kaplamalı veya yüzey TD işlemine tabi tutulmalıdır. Tungsten çelik gerektiğinde dışbükey ve içbükey kalıp olarak kullanılabilir.
Lütfen yeniden basım için bu makalenin kaynağını ve adresini saklayın: Çizim Kalıp Tasarımında Yedi Önlem
Minhe Basınçlı Döküm Şirketi kaliteli ve yüksek performanslı Döküm Parçaları üretmeye ve sağlamaya adamıştır (metal döküm parça yelpazesi esas olarak şunları içerir: İnce Duvarlı Döküm,Sıcak Kamara Basınçlı Döküm,Soğuk Oda Döküm), Yuvarlak Servis (Döküm Servisi,Cnc İşleme,Kalıp yapımı,Yüzey İşleme).Herhangi bir özel Alüminyum döküm, magnezyum veya Zamak/çinko döküm ve diğer döküm gereksinimleri bizimle iletişime geçebilirsiniz.
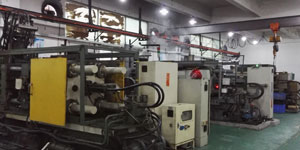
ISO9001 ve TS 16949 kontrolünde, tüm işlemler yüzlerce gelişmiş basınçlı döküm makinesi, 5 eksenli makine ve blasterlerden Ultra Sonic yıkama makinelerine kadar diğer tesisler aracılığıyla gerçekleştirilir. Müşterinin tasarımını gerçeğe dönüştürmek için deneyimli mühendisler, operatörler ve müfettişlerden oluşan ekip.
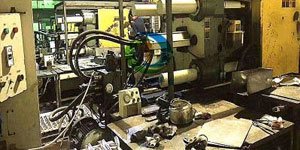
Dökümlerin sözleşmeli üreticisi. Yetenekler, 0.15 lbs'den başlayan soğuk oda alüminyum döküm parçaları içerir. 6 lbs'ye kadar, hızlı değişim kurulumu ve işleme. Katma değerli hizmetler arasında polisaj, titreşim, çapak alma, kumlama, boyama, kaplama, kaplama, montaj ve kalıplama yer alır. Çalışılan malzemeler arasında 360, 380, 383 ve 413 gibi alaşımlar bulunur.
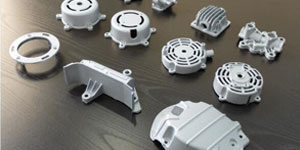
Çinko pres döküm tasarım yardımı/eşzamanlı mühendislik hizmetleri. Hassas çinko dökümlerin özel üreticisi. Minyatür dökümler, yüksek basınçlı dökümler, çok kızaklı kalıp dökümleri, geleneksel kalıp dökümleri, birim kalıp ve bağımsız kalıp dökümleri ve boşluklu sızdırmaz dökümler üretilebilir. Dökümler, +/- 24 inç toleransta 0.0005 inç'e kadar uzunluk ve genişliklerde üretilebilir.
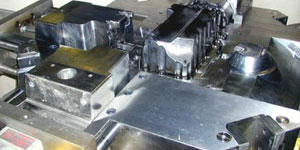
ISO 9001: 2015 sertifikalı döküm magnezyum üreticisi, Yetenekler arasında 200 ton sıcak odaya ve 3000 ton soğuk odaya kadar yüksek basınçlı magnezyum kalıp dökümü, takım tasarımı, cilalama, kalıplama, işleme, toz ve sıvı boyama, CMM özelliklerine sahip tam kalite güvencesi bulunur , montaj, paketleme ve teslimat.
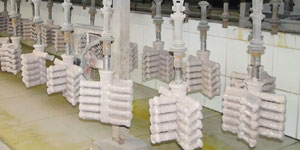
ITAF16949 sertifikalı. Ek Döküm Hizmeti Dahil yatırım dökümleri,kum dökümü,Yerçekimi Döküm, Kayıp Köpük Döküm,Savurma döküm,Vakumlu Döküm,Kalıcı Kalıp Döküm,.Yetenekler arasında EDI, mühendislik yardımı, katı modelleme ve ikincil işleme yer alır.
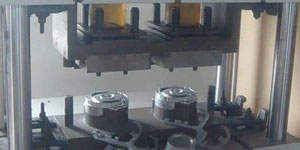
Döküm Endüstrileri Arabalar, Bisikletler, Uçaklar, Müzik aletleri, Deniz Araçları, Optik cihazlar, Sensörler, Modeller, Elektronik cihazlar, Muhafazalar, Saatler, Makineler, Motorlar, Mobilya, Mücevher, Jigler, Telekom, Aydınlatma, Tıbbi cihazlar, Fotoğraf cihazları, Robotlar, Heykeller, Ses ekipmanları, Spor ekipmanları, Aletler, Oyuncaklar ve daha fazlası.
Bundan sonra ne yapmanıza yardımcı olabiliriz?
∇ Ana Sayfaya Git Çin Döküm
→Döküm Parçaları-Ne yaptığımızı öğren.
→ Hakkında İlgili İpuçları Pres Döküm Hizmetleri
By Minghe Döküm Üreticisi |Kategoriler: Faydalı Makaleler |Malzeme Etiketler: Alüminyum Döküm, Çinko Döküm, Magnezyum Döküm, Titanyum Döküm, Paslanmaz Çelik Döküm, Pirinç Döküm,Bronz Döküm,Döküm Videosu,Tarihçe,Alüminyum Döküm |Yorumlar Kapalı