Sfero Dökün Katılaşma Özelliklerindeki Farklılıklar
Genel olarak, sfero dökümler, gri demir dökümlerden çok daha fazla büzülme ve gözeneklilik eğilimine sahiptir. Büzülme kusurlarını önlemek, proses tasarımında genellikle çok zor bir problemdir. Bu bağlamda, gerçek üretimden özetlenen deneyim çok tutarsızdır ve her birinin kendi görüşleri vardır: bazı insanlar sıralı katılaştırma ilkesinin takip edilmesi gerektiğini ve hacmi tamamlamak için nihai katılaştırma konumuna büyük bir yükselticinin yerleştirilmesi gerektiğini düşünüyor. dökümün katılaşma işlemi sırasında üretilir. büzülme; Bazı insanlar sfero döküm parçaların sadece küçük kolonlara ihtiyaç duyduğunu ve bazen kolonlar olmadan sağlam dökümlerin üretilebileceğini düşünüyor.
Dökümlerin kalitesini sağlarken prosesin üretim hızını en üst düzeye çıkarmak için, dökme demirin kimyasal bileşimini kontrol etmek yeterli değildir. Sfero dökme demirin katılaşma özelliklerinin anlaşılması temelinde, dökme demirin eritilmesi, küreselleştirilmesi, aşılanması ve işlenmesini etkin bir şekilde kontrol etmek gerekir. Dökme işleminin tüm sürecinde, kalıbın sertliği etkin bir şekilde kontrol edilmelidir.
1. Sfero Dökün Katılaşma Özellikleri
Gerçek üretimde kullanılan sfero dökme demirin çoğu ötektik bileşime yakındır. Kalın duvarlı dökümler ötektik altı bileşim kullanır ve ince duvarlı dökümler ötektik üstü bileşim kullanır, ancak ötektik bileşimden çok uzak değildir.
Ötektik ve ötektik üstü bileşenlere sahip sfero döküm için, ötektik katılaşma sırasında önce sıvı fazdan küçük grafit bilyeler çökeltilir. Ötektik altı bileşime sahip sfero dökme demir için bile, küreselleştirme ve aşılama işleminden sonra erimiş demirin aşırı soğuma derecesindeki artıştan dolayı, önce denge ötektik geçiş sıcaklığından çok daha yüksek bir sıcaklıkta küçük grafit topları çökelecektir. Küçük grafit kürelerin ilk partisi 1300°C veya daha yüksek sıcaklıklarda oluşturulmuştur.
Müteakip katılaşma sürecinde, sıcaklık düştükçe, ilk küçük grafit kürelerin bazıları büyür ve bazıları erimiş demirde yeniden çözülür ve yeni grafit küreler de çöker. Grafit kürelerin çökeltilmesi ve büyümesi geniş bir sıcaklık aralığında gerçekleştirilir.
Grafit top büyüdüğünde etrafındaki erimiş demirdeki karbon içeriği azalır ve grafit topun etrafında grafit topun etrafını saran bir ostenit kabuğu oluşacaktır. Östenit kabuğunun oluşum süresi, kalıptaki dökümün soğuma hızı ile ilgilidir: soğutma hızı yüksektir ve erimiş demirdeki karbonun düzgün bir şekilde dağılması için zamanı yoktur ve östenit kabuğu daha erken oluşur; soğutma hızı düşüktür, bu da erimiş demirdeki soğutma hızı için faydalıdır. Karbon düzgün bir şekilde yayılır ve daha sonra ostenit kabuğu oluşur.
Östenit kabuğu oluşmadan önce, grafit top yüksek karbon içeriğine sahip erimiş demir ile doğrudan temas eder ve erimiş demirdeki karbonun grafit topun içine yayılması kolaydır, böylece grafit top büyür. Ostenit kabuğu oluştuktan sonra, erimiş demirdeki karbonun grafit toplara difüzyonu engellenir ve grafit topların büyüme hızı keskin bir şekilde düşer. Grafit erimiş demirden çökeltildiğinde açığa çıkan gizli kristalleşme ısısı büyük olduğundan, yaklaşık 3600 J/g, östenit erimiş demirden çökeltildiğinde açığa çıkan gizli kristalleşme ısısı daha az, yaklaşık 200 J/g'dir ve etrafında bir östenit kabuğu oluşturur. grafit top Grafit topların büyümesi engellenir, bu da kristalleşme gizli ısısının salınımını önemli ölçüde yavaşlatır. Bu koşullar altında ötektik katılaşmanın ilerlemesi, yeni kristal çekirdekler üretmek için sıcaklığın daha da düşürülmesine bağlıdır. Bu nedenle, küresel grafitli dökme demirin ötektik dönüşümünün nispeten geniş bir sıcaklık aralığında tamamlanması gerekir ve katılaşma sıcaklık aralığı, tipik macun benzeri katılaşma özelliklerine sahip olan gri dökme demirin iki katı veya daha fazladır.
Kısacası, sfero dökümün katılaşma özellikleri esas olarak aşağıdaki yönlere sahiptir.
1. Geniş katılaşma sıcaklık aralığı
Demir-karbon alaşımının denge diyagramından, katılaşma sıcaklık aralığı ötektik bileşime yakın geniş değildir. Aslında, erimiş demirin küreselleştirme ve aşılama işleminden sonra katılaşma süreci denge koşullarından çok sapar. Ötektik geçiş sıcaklığının (150°C) yaklaşık 1150°C üzerinde, grafit küreler çökelmeye başlar ve ötektik geçişin tekrar sona erdiği sıcaklık, denge ötektik geçiş sıcaklığından yaklaşık 50°C daha düşük olabilir.
Bu kadar geniş bir katılaşma sıcaklık aralığına sahip bir alaşım, macun benzeri bir katılaşma şeklinde katılaştırılır ve dökümlerin sıralı katılaştırılmasını sağlamak zordur. Bu nedenle, çelik dökümlerin kolonunun tasarım prensibine göre, dökümlerin sıralı katılaşmasını gerçekleştirme ve son katılaşmış sıcak bağlantıda büyük bir kolon yerleştirme proses planı çok uygun değildir.
Grafit küreler çok yüksek sıcaklıklarda çökeltildiğinden ve ötektik dönüşüm meydana geldiğinden, sıvı-katı iki fazı uzun süre bir arada bulunur ve erimiş demirin katılaşması sırasında sıvı büzülmesi ve katılaşma büzülmesi aynı anda meydana gelir. Bu nedenle, yolluk sistemi ve yükseltici benzeri çelik dökümler yoluyla sıvı büzülmesini tam olarak tamamlamak mümkün değildir.
2. Ötektik dönüşüm sırasında grafitin çökelmesi hacim genişlemesine yol açar
Ötektik sıcaklığın yakınında, ostenitin yoğunluğu yaklaşık 7.3g/cm3'tür ve grafitin yoğunluğu yaklaşık 2.15g/cm3'tür. Dökümün katılaşması sırasında grafitin çökelmesi sistemin hacim genişlemesine neden olacaktır. Çökeltilen grafitin yaklaşık %1'i (kütle oranı) %3.4 hacim genişlemesi üretebilir.
Dökme demirde grafitleşme genişlemesinin doğru kullanımı, katılaşma sırasında hacim küçülmesini etkili bir şekilde telafi edebilir. Belirli koşullar altında, kolonsuz sağlam dökümler üretilebilir.
Hem gri dökme demirin hem de sfero dökme demirin ötektik dönüşüm işlemi sırasında grafiti çökelttiği ve hacim genişlemesine uğradığı vurgulanmalıdır. Ancak, iki dökme demirdeki farklı grafit morfolojisi ve büyüme mekanizması nedeniyle, grafitleşme genişlemesinin dökme demirin döküm performansı üzerindeki etkisi de çok farklıdır.
Gri dökme demirin ötektik kümesindeki pul grafit için, erimiş demir ile doğrudan temas halinde olan uç tercihen büyür. Grafitin büyümesinin neden olduğu hacim genişlemesinin çoğu, grafit ucu ile temas halindeki erimiş demir üzerinde etki eder ve bu, onu östenit dallarıyla doldurmaya zorlamak için faydalıdır. Aralarındaki boşluk, dökümü daha yoğun hale getirir.
Sfero dökme demirdeki grafit, bir östenit kabuğu ile çevrili olma koşulu altında büyütülür. Grafit top büyüdüğünde meydana gelen hacim genişlemesi, esas olarak, bitişik ötektik kümeler üzerinde hareket eden östenit kabuğundan geçer; ötektik kümeler aracılığıyla, kalıp duvarlarının hareket etmesine neden olur.
3. Dökümün katılaşması sırasında grafitleşme genişlemesi, kalıbın duvarda hareket etmesine neden olmak kolaydır
Küresel dökme demir, macun benzeri bir katılaştırma yöntemiyle katılaşır. Döküm katılaşmaya başladığında, kalıp-metal ara yüzeyindeki dökümün dış yüzey tabakası gri dökme demirden çok daha incedir ve yavaş büyür. Uzun bir süre sonra bile, yüzey tabakası hala güçlüdür. Düşük sertlikte ince kabuk. İçeride grafitleşmiş genleşme meydana geldiğinde, dış kabuk genişleme kuvvetine dayanacak kadar güçlü değilse dışa doğru hareket edebilir. Kalıbın rijitliği zayıf ise duvar hareketi meydana gelir ve boşluk genişler. Sonuç olarak, sadece dökümün boyutsal doğruluğu etkilenmekle kalmaz, aynı zamanda grafitizasyon genleşmesinden sonraki büzülme tamamlanamaz ve döküm içinde büzülme boşluğu ve gözeneklilik gibi kusurlar meydana gelir.
4. Ötektik östenitteki karbon içeriği, gri dökme demirdekinden daha yüksektir
Amerika Birleşik Devletleri'nde RW Heine tarafından yapılan bir araştırma raporuna göre, sfero dökümün ötektik katılaşması sırasında, östenitin karbon içeriği gri dökme demirden daha yüksektir.
Gri dökme demir ötektiği katılaştığında, ötektik kümedeki grafit pulları hem östenit hem de yüksek karbon içeriğine sahip erimiş demir ile doğrudan temas halindedir. Erimiş demirdeki karbon sadece östenit yoluyla grafite yayılmakla kalmaz, aynı zamanda doğrudan grafit pullarına difüze olur, bu nedenle ergimiş demir-östenit ara yüzeyinde östenit içindeki karbon içeriği nispeten düşüktür, yaklaşık %1.55.
Küresel dökme demir ötektik katılaştığında, ötektik kümedeki grafit toplar erimiş demirle değil, yalnızca östenit kabuğuyla temas eder. Grafit toplar büyüdüğünde, erimiş demirdeki karbon, östenit kabuğundan grafit toplara yayılır. Bu nedenle, ergimiş demir-ostenit ara yüzeyinde östenit içindeki karbon içeriği nispeten yüksektir ve yaklaşık %2.15'e ulaşır.
Sfero dökümün ötektik katılaşması sırasında östenitteki karbon içeriği daha yüksek olabilir. Aynı karbon ve silikon içeriği koşulları altında, aynı soğutma hızı korunursa, çöken grafit miktarı daha az olacaktır. Bu nedenle ötektik katılaştığında Hacim büzülmesi gri dökme demirden biraz daha büyük olacaktır. Bu aynı zamanda sfero dökümlerin büzülmeye ve gözenekliliğe daha yatkın olmasının nedenlerinden biridir. Katılaşma işlemi sırasında düşük bir soğutma hızının korunması, grafit şarj analizine elverişli bir faktördür.
Grafitleştirmeyi yeterli kılabilecek koşullar altında ötektik östenitteki karbon içeriği (yani, karbonun östenit içindeki maksimum katı çözünürlüğü), dökme demirdeki silikon içeriği ile ilgilidir ve genellikle aşağıdaki formülle hesaplanabilir.
Östenit içinde karbonun maksimum katı çözünürlüğü CE=2.045-0.178 Si
2. Sfero dökümlerin katılaşması sırasında hacim değişimi
Erimiş demirin kalıba döküldüğü andan ötektik katılaşmanın sonuna ve dökümün tam katılaşmasına kadar, boşluktaki dökme demir sıvı büzülmesine, birincil grafitin çökeltilmesinin neden olduğu hacim genişlemesine ve katılaşmaya uğrayacaktır. ötektik östenitin çökelmesinin neden olduğu büzülme, ötektik grafitin çökelmesinin neden olduğu hacim genişlemesi gibi çeşitli hacim değişiklikleri. Sfero dökme demirin katılaşması sırasında hacim değişikliğinin tanımını kolaylaştırmak için, Şekil 2'de gösterilen basitleştirilmiş faz diyagramına başvurmak gerekir. XNUMX.
1. Erimiş demirin sıvı çekmesi
Erimiş demir kalıba girdikten sonra sıcaklık düştükçe hacim küçülür. Erimiş demirin sıvı çekme miktarı, kimyasal bileşimine ve işleme koşullarına bağlı olarak değişecektir, ancak bu genellikle göz ardı edilir. Genel olarak, sıcaklıktaki her 1.5°C'lik düşüş için %100'lik hacim küçülmesi kabul edilir. Sıvı büzülmesinin meydana geldiği sıcaklık aralığı, döküm sıcaklığından denge ötektik geçiş sıcaklığına (1150°C) düşüşe göre hesaplanır. Sfero döküm parçalar birkaç farklı döküm sıcaklığında döküldüğünde, sıvı çekmesi Tablo 1'de gösterilmektedir.
Tablo 1 Farklı sıcaklıklarda dökme sırasında sfero dökümlerin sıvı çekmesi
Dökme sıcaklığı (℃) | 1400 | 1350 | 1300 |
Sıvı büzülmesi (%) | 3.75 | 3.00 | 2.25 |
2. Birincil grafitin çökelmesinin neden olduğu hacim genişlemesi
Ötektik altı küresel grafitli dökme demir, sıvı sıcaklığının üzerinde küçük grafit küreleri çökeltmesine rağmen, miktar çok küçüktür ve genellikle ihmal edilebilir.
Daha önce belirtildiği gibi, çökeltilen grafitin her %1'i (kütle oranı), %3.4'lük bir hacim genişlemesi üretebilir. Bu nedenle, birincil grafitin çökeltilmesinin neden olduğu hacim genişlemesi 3.4G'ye eşittir.
Tablo 2, farklı karbon ve silikon içeriklerine sahip birkaç küresel dökme demirden birincil grafitin çökelmesinin neden olduğu hacim genişlemesini göstermektedir.
Çöken birincil grafit, dökme demirin katılaşması sırasında sıvı büzülmesini telafi edebilse de, duvar kalınlığı 40 mm'den fazla olan dökümler için, grafit kapanımları veya grafit yüzmesi gibi kusurların meydana gelmesi muhtemeldir. Bu durumda karbon ve silikon içeriğinin kontrolüne özel dikkat gösterilmelidir.
Tablo 2 Birkaç küresel dökme demirde birincil grafitin çökelmesinin neden olduğu hacim genişlemesi
- Dökme demirin karbon içeriği (%):3.6/3.5/3.6/3.7/3.6/3.7/3.8
- Dökme demirin silikon içeriği (%):2.2/2.4/2.4/2.4/2.6/2.6/2.6
- Ötektik karbon içeriği CC (%)/3.54/3.47/3.47/3.47/3.40/3.40/3.40
- Birincil grafit G başlangıç (%)/0.06/0.03/0.13/0.24/0.21/0.31/0.41 yağış miktarı
- Birincil grafit çökeltisinin neden olduğu hacim genişlemesi (%):0.21/0.10/0.44/0.82/0.71/1.05/1.39
3. Ötektik östenitin çökelmesinin neden olduğu hacim küçülmesi
Ötektik ostenitin çökelmesinin neden olduğu hacim küçülmesini hesaplamak için ötektik sıvı fazın kütle fraksiyonu (bundan sonra "ötektik sıvı faz miktarı" olarak anılacaktır), sıvı çekme miktarı ve ötektik östenit biriminden çökeltilen ötektik ostenit sıvı faz dikkate alınmalıdır Hacim ve katılaşma büzülmesi. Sıvı çekmesinin hesaplanması yukarıda açıklanmıştır. Ötektik sıvı fazdan çökelen ostenitin katılaşma büzülmesi genellikle %3.5'tir.
Tablo 3, farklı karbon ve silikon içeriklerine sahip birkaç küresel dökme demirde ötektik östenitin çökelmesinin neden olduğu hacim küçülmesini göstermektedir.
Tablo 3 Birkaç küresel dökme demirde ötektik östenitin çökelmesinin neden olduğu hacim küçülmesi
- Dökme demirin karbon içeriği (%) 3.6/3.5/3.6/3.7/3.6/3.7/3.8
- Dökme demirin silikon içeriği (%)/2.2/2.4/2.4/2.4/2.6/2.6/2.6
- Ötektik sıvı faz miktarı (%) 99.94/99.97/99.87/99.76/99.79/99.69/99.59
- Birim ötektik sıvı fazda çökelen ostenit miktarı (%)~98.1
- 1400℃ (%)/3.30/3.30/3.30/3.30/3.30/3.29/3.29'da dökerken ostenitin hacim küçülmesi
- 1350℃ (%)/3.33/3.33/3.33/3.32/3.32/3.32/3.32'da dökerken ostenitin hacim küçülmesi
- 1300℃'de dökme sırasında ostenitin hacim küçülmesi (%) 3.35/3.35/3.35/3.35/3.35/3.34/3.34
Yaygın olarak kullanılan birkaç küresel dökme demir için, dökme sıcaklığını 1350℃'nin altında tutun. Kalıbın duvar hareketi olmaması durumunda, dökümün katılaşması sırasında grafitleşmenin neden olduğu hacim genişlemesi, sıvı büzülmesini ve katılaşma büzülmesini telafi edebilir. Yükseltici ayar yapmadan sağlam dökümler yapmak mümkündür. Dökme sıcaklığı 1400℃ olduğunda, dökme demir için daha yüksek bir karbon eşdeğeri seçilirse, grafitleşme genleşmesi çeşitli hacim büzülmesini de telafi edebilir, ancak bu yöntem yalnızca ince duvarlı dökümler için uygundur, daha kalın duvarlı dökümler grafit içermeye eğilimlidir. ve cüruf Grafit yüzer kusurları.
Bununla birlikte, Tablo 5'te listelenen bilgiler denge diyagramından elde edilmiştir ve 'potansiyel olarak çökeltilmiş karbon'un katılaşma işlemi sırasında grafit kristalleri tarafından tamamen çökeltildiği öncülüne dayanmaktadır. Fiili üretimde, elbette, etkili küreselleştirme ve aşılama işlemine dayanmalıdır ve yeterli grafitizasyon esastır. Yüksek soğutma hızlarına sahip dökümler ve ince duvarlı dökümler için, ötektik katılaşma sırasında yetersiz grafitleşme nedeniyle ötektik grafitin çökelmesinin neden olduğu hacim genişlemesi yukarıda belirtilen hesaplanan değerden daha azdır ve yine de aşağıdaki gibi kusurların üretilmesi kolaydır. büzülme boşlukları ve büzülme gözenekliliği. .
Aynı zamanda kalıbın sertliği de çok önemli bir faktördür. Döküm kalıbının rijitliği yüksek değilse ve grafitleşme ve genleşme sırasında duvar hareketi meydana gelirse, genleşme sonrası büzülme tamamlanamaz ve döküm içinde büzülme boşluğu ve büzülme gözenekliliği gibi kusurlar olacaktır.
3. Yükselticisiz döküm gerçekleştirme koşulları
Dökümün tamamlanmasından katılaşmanın sonuna kadar dökümde sıvı büzülmesi ve katılaşma büzülmesi meydana gelecektir. Ayrıca, sünek demir, macun benzeri bir katılaştırma yöntemiyle katılaştırıldığı için, yükselticisiz döküm elde etmek için sıvı büzülmesini dökme sistemi ile tam olarak desteklemek zordur. Dökme demirin sıvı büzülmesi ve katılaşma büzülmesi, grafit kristalleri çökeltildiğinde hacim genişlemesi ile telafi edilmelidir. Bunun için aşağıdaki şartların sağlanması gerekmektedir.
Erimiş demirin metalurjik kalitesi iyidir
Normal şartlar altında, karbon eşdeğerinin 4.3 veya 4.4 seçilmesi daha iyidir ve karbon eşdeğeri, ince duvarlı dökümler için uygun şekilde artırılabilir. Çöken grafit miktarını arttırmak için karbon eşdeğeri aynı tutuluyorsa, karbon içeriğini arttırmak silikon içeriğini arttırmaktan daha avantajlıdır.
Küreselleştirme işlemi sıkı bir şekilde kontrol edilmelidir. Grafitin küreselleşmesinin sağlanması koşulu altında, artık magnezyum miktarı mümkün olduğunca azaltılmalı ve artık magnezyumun kütle oranı yaklaşık %0.06'da tutulmalıdır.
Aşılama tedavisi yeterli olmalıdır. Küreleme tedavisi ile aynı zamanda yapılan aşılama işleminin yanı sıra, dökme sırasında anlık aşılama da yapılmalıdır. İnce duvarlı dökümlerin, erimiş demir serbest bırakılmadan önce aşılanması en iyisidir.
Dökümün katılaşması sırasında soğuma hızı çok yüksek olmamalıdır.
Dökümün soğuma hızı çok yüksekse, katılaşma işlemi sırasında grafit tam olarak analiz edilemez ve grafitleşme genleşmesi, dökme demirin büzülmesini telafi etmek için yeterli değildir ve dolayısıyla yükselticisiz döküm gerçekleştirilemez.
Düşük sıcaklıkta dökme
Sıvı büzülmesini azaltmak için, döküm sıcaklığı en iyi 1350℃, genellikle 1320±20℃'nin altında kontrol edilir.
Pul şeklindeki iç kapıyı kullanma
Grafitleşme ve genleşme sırasında erimiş demirin iç kapıdan dışarı atılmasını önlemek için, erimiş demir kalıpla doldurulduktan sonra iç kapının hızla katılaşması gerekir. Bu nedenle, kolonsuz döküm şemasına geçildiğinde ince ve geniş bir iç kapı kullanılmalıdır. , Genişliğin kalınlığa oranı genellikle 4 ila 5'tir. İç kapak kalınlığı seçiminde, dökme sıcaklığı da dikkate alınmalı, dökme işlemi sırasında iç kapak katılaşmamalıdır.
Kalıbın sertliğini iyileştirin
Grafitleme genleşmesi sırasında boşluğun genişlemesini önlemek için, kalıbın sertliğinin iyileştirilmesi, döküm kalitesinin sağlanması için önemli koşullardan biridir. Kil ıslak kum modelleme veya çeşitli kendiliğinden yerleşen kum modelleme kullanımından bağımsız olarak, "dövülerek katı" üzerine ne kadar vurgu yapılırsa yapılsın aşırı olmayacaktır.
Kendiliğinden sertleşen kum ile daha büyük dökümler yaparken, döküm üzerindeki bazı kalın parçalara karşılık gelen kalıbın yüzeyine soğutulmuş demir veya grafit bloklar yerleştirilmelidir. Soğuk demir ve grafit blokların elbette bir soğutma etkisi vardır, ancak aynı zamanda kalıbın sertliğini iyileştirmedeki rollerini doğru bir şekilde anlamaları gerekir. Bazı durumlarda, ana işlevi kalıbın sertliğini arttırmak olan soğutulmuş demir veya grafit bloklar yerine refrakter tuğlaların kullanılması.
4. Yüksek sertlikte kalıplar kullanıldığında yükselticinin ayar prensibi
Sfero döküm parçalar üretmek için çeşitli kendinden ayarlı kum kalıplama işlemleri, kabuk kalıplama işlemleri veya maça montaj kalıplama işlemleri kullanıldığında, kalıbın sertliği nispeten yüksektir, bu da sıvı büzülme ve katılaşma büzülmesini desteklemek için grafitleşme genişlemesini kullanmak için uygundur. dökme demir. Düzgün bir şekilde kontrol edilirse, sağlam dökümler üretmek için yükselticisiz bir işlem kullanmak mümkün olacaktır. Çeşitli nedenlerle kolonsuz işlem uygun değilse dar boyunlu kolon kullanılabilir.
Yükseltici olmadan döküm işlemi
Erimiş demirin yüksek kalıp sertliği ve iyi metalurjik kalitesi koşulları altında, dökümlerin soğuma hızını düşük tutmak, böylece grafit tamamen kristalleşebilir, kolonsuz döküm gerçekleştirmek için önemli bir koşuldur.
Goto ve diğerleri tarafından yapılan bir araştırma raporuna göre, sfero dökümlerin katılaşma süresi 20 dakikadan fazladır ve grafit çökeltme miktarı doyma değerine ulaşabilir.
SI Karsay, ortalama döküm modülünün 25 mm'den az olmamasının, kolonsuz döküm gerçekleştirmenin koşullarından biri olduğuna inanmaktadır. Spesifik olarak, levha dökümlerin ortalama et kalınlığı 50 mm'den az olmamalıdır.
Goto ve diğerleri tarafından ifade edilen görüşler. ve Karsay farklıdır ve soğutma hızının analizinden aslında aynıdırlar.
Erimiş demirin metalurjik kalitesinin iyi olması koşuluyla (ön aşılama işleminin veya dinamik aşılama işleminin kullanılması ve diğer önlemler gibi), bazı ince duvarlı dökümler de yükseltici olmadan dökülebilir.
Yükselticisiz döküm sürecini benimserken, yolluk sisteminin tasarımı aşağıdaki görüşlere atıfta bulunabilir.
(1) Koşucu hakkında
Koşucu daha büyük ve daha uzun olmalıdır. Genel olarak konuşursak, ladin enine kesit alanının, koşucunun enine kesit alanının ve iç kapının enine kesit alanının oranı 4:8:3 olabilir. Kesit yüksekliğinin yolluk genişliğine oranı (1.8~2):1 olarak alınabilir.
Bu şekilde, yolluk sistemi, dökümün sıvı büzülmesini tamamlama konusunda daha iyi bir etkiye sahiptir.
(2) İç kapı hakkında
Dökümün boşluktaki hacimsel genleşmesinin oluşturduğu basıncın, erimiş demirin iç kapaktan döküm sistemine geri akmasına neden olmasını önlemek için ince şekilli bir iç kapak kullanılmalı ve kalınlığı seçilmelidir. dökme işlemi sırasında iç kapının engellenmeyeceğinden emin olun. İlke, boşluk doldurulduktan hemen sonra katılaşmak ve katılaşmaktır. Genel olarak konuşursak, kesit kalınlığının iç kapının genişliğine oranı 1:4 olabilir.
İç kapak ince ve kesit alanı küçük olduğundan, boşluğun hızlı bir şekilde doldurulmasını sağlamak için daha büyük dökümler için çoklu iç kapılar sağlanmalıdır. Bu sayede dökümün sıcaklığını eşitleme ve sıcak noktaları azaltma etkisi de vardır.
2. İnce boyun yükseltici kullanın
Aşağıdaki durumlar varsa, kolonsuz bir döküm şemasının kullanılması dökümlerin kalitesini garanti edemezse, dar boyunlu bir kolon kullanmayı düşünebilirsiniz:
- L Dökümün duvarı incedir ve katılaşma sırasında grafitleşme yetersizdir;
- L Döküm üzerinde dağınık sıcak düğümler vardır ve içeride büzülme kusurlarına izin verilmez;
- L Dökme sıcaklığı daha yüksektir (1350℃'nin üzerinde).
Dar boyunlu yükselticinin ana işlevi, büzülme veya gözeneksiz bir döküm elde etmek için dökümün sıvı büzülmesine kısmi bir katkı sağlamaktır. Döküm ile bağlantılı dar boyun, grafitleşme ve genleşme sırasında erimiş demirin yükselticiye girmesini önlemek için döküm katılaşmaya başlamadan önce katılaştırılmalıdır. Yükseltici boyun ve döküm arasındaki bağlantının kalınlığı en küçüktür ve erimiş demirin döküme ikmalini kolaylaştırmak için yükselticiye giden geçiş bölümünde kalınlık kademeli olarak arttırılır.
Yükseltici boynun kalınlığı genellikle dökümün besleme kısmının kalınlığının 0.4 ila 0.6'sı kadar olabilir.
Mümkünse, koşucuyu yükselticiye bağlamak en iyisidir ve erimiş demir, bir iç kapı olmadan yükselticinin boynundan doldurulur.
5. Kil ıslak kum tipini kullanırken yükselticinin ayar prensibi
Kil yeşil kum kalıbının sertliği zayıftır ve kalıp duvarının hareketi nedeniyle boşluk hacmini genişletmek kolaydır. Boşluk hacminin genişlemesi, kalıplama kumunun kalitesi, kalıbın kompaktlığı, dökme sıcaklığı ve kalıp gibi birçok faktörden etkilenir. Boşluktaki vb. erimiş demirin statik basınç kafası, gerçek hacim genişlemesi %2-8 arasında olabilir.
Boşluğun hacim genişlemesi büyük ölçüde değiştiğinden, yükselticinin ayarlanma ilkesi, özel duruma bağlı olarak elbette farklıdır.
İnce duvarlı dökümler
Duvar kalınlığı 8 mm'den az olan dökümlerde genellikle belirgin duvar hareketi yoktur ve erimiş demir kalıpla doldurulduktan sonra sıvı büzülme çok büyük değildir ve yükselticisiz döküm işlemi kullanılabilir. Yolluk sisteminin tasarımı önceki bölüme başvurabilir.
8-12 mm et kalınlığına sahip dökümler
Bu tip dökümler için, eğer duvar kalınlığı üniform ise ve büyük sıcak noktalar yoksa, düşük sıcaklıktaki döküm sıkı bir şekilde kontrol edildiği sürece, kolonsuz döküm prosesi de kullanılabilir.
Sıcak derz varsa, büzülme deliklerine ve içeride büzülmeye izin verilmiyorsa, sıcak derzin boyutuna göre dar boyunlu bir yükseltici ayarlanmalıdır.
Duvar kalınlığı 12 mm'nin üzerinde olan dökümler
Bu tür dökümlerin kil yaş kum kalıplarla üretiminde duvar hareketi oldukça fazladır ve iç kusuru olmayan dökümlerin üretilmesi daha zordur. Proses planını formüle ederken, önce dar boyunlu bir kolon kullanmayı düşünün ve düşük sıcaklıkta dökmeyi sıkı bir şekilde kontrol edin. Bu çözüm sorunu çözemezse, özel bir yükseltici tasarlanmalıdır.
Sfero döküm parçalar üretmek için kil ıslak kum kullanın. Bir yükseltici kurmak istiyorsanız, şunları yapmak en iyisidir:
- Kalıp doldurulduktan sonra katılaşması için LA ince iç kapı kullanılır. İç kapı katılaştıktan sonra, döküm ve yükseltici, kapı sistemi ile bağlantılı olmayan bir bütün oluşturur;
- L Döküm sıvı büzülmeye maruz kaldığında, yükseltici döküme erimiş demiri doldurur;
- L Döküm grafitleştirildiğinde ve genleştiğinde, erimiş demir boşluktaki basıncı serbest bırakmak için yükselticiye akar. Kalıp duvarı üzerindeki etkisini azaltın;
- L Döküm gövdesi grafitleşme ve genleşmeden sonra ikincil büzülmeye maruz kaldığında, yükseltici döküme demir sıvı beslemesi sağlayabilir.
Bunu söylemek karmaşık görünmüyor, ancak aslında, yükselticinin tasarımında birçok etkili faktör dikkate alınmalıdır ve şimdiye kadar etkili bir spesifik şema görülmedi ve kullanımı kolay eksiksiz bir set yok. veri. Üretimde, dökümlerin kalitesini ve proses verim oranını hesaba katmak ve çoğu zaman araştırmak ve denemek gerekir.
Lütfen yeniden basım için bu makalenin kaynağını ve adresini saklayın: Sfero Dökün Katılaşma Özelliklerindeki Farklılıklar
Minhe Basınçlı Döküm Şirketi kaliteli ve yüksek performanslı Döküm Parçaları üretmeye ve sağlamaya adamıştır (metal döküm parça yelpazesi esas olarak şunları içerir: İnce Duvarlı Döküm,Sıcak Kamara Basınçlı Döküm,Soğuk Oda Döküm), Yuvarlak Servis (Döküm Servisi,Cnc İşleme,Kalıp yapımı,Yüzey İşleme).Herhangi bir özel Alüminyum döküm, magnezyum veya Zamak/çinko döküm ve diğer döküm gereksinimleri bizimle iletişime geçebilirsiniz.
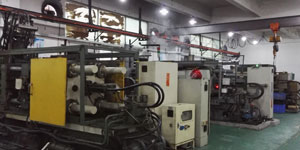
ISO9001 ve TS 16949 kontrolünde, tüm işlemler yüzlerce gelişmiş basınçlı döküm makinesi, 5 eksenli makine ve blasterlerden Ultra Sonic yıkama makinelerine kadar diğer tesisler aracılığıyla gerçekleştirilir. Müşterinin tasarımını gerçeğe dönüştürmek için deneyimli mühendisler, operatörler ve müfettişlerden oluşan ekip.
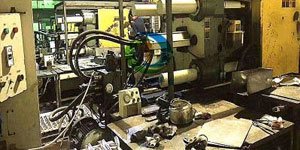
Dökümlerin sözleşmeli üreticisi. Yetenekler, 0.15 lbs'den başlayan soğuk oda alüminyum döküm parçaları içerir. 6 lbs'ye kadar, hızlı değişim kurulumu ve işleme. Katma değerli hizmetler arasında polisaj, titreşim, çapak alma, kumlama, boyama, kaplama, kaplama, montaj ve kalıplama yer alır. Çalışılan malzemeler arasında 360, 380, 383 ve 413 gibi alaşımlar bulunur.
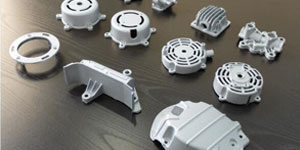
Çinko pres döküm tasarım yardımı/eşzamanlı mühendislik hizmetleri. Hassas çinko dökümlerin özel üreticisi. Minyatür dökümler, yüksek basınçlı dökümler, çok kızaklı kalıp dökümleri, geleneksel kalıp dökümleri, birim kalıp ve bağımsız kalıp dökümleri ve boşluklu sızdırmaz dökümler üretilebilir. Dökümler, +/- 24 inç toleransta 0.0005 inç'e kadar uzunluk ve genişliklerde üretilebilir.
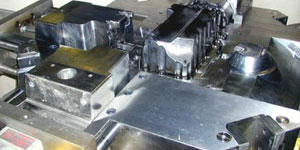
ISO 9001: 2015 sertifikalı döküm magnezyum üreticisi, Yetenekler arasında 200 ton sıcak odaya ve 3000 ton soğuk odaya kadar yüksek basınçlı magnezyum kalıp dökümü, takım tasarımı, cilalama, kalıplama, işleme, toz ve sıvı boyama, CMM özelliklerine sahip tam kalite güvencesi bulunur , montaj, paketleme ve teslimat.
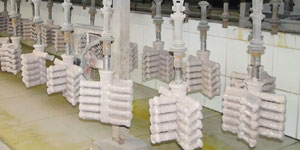
ITAF16949 sertifikalı. Ek Döküm Hizmeti Dahil yatırım dökümleri,kum dökümü,Yerçekimi Döküm, Kayıp Köpük Döküm,Savurma döküm,Vakumlu Döküm,Kalıcı Kalıp Döküm,.Yetenekler arasında EDI, mühendislik yardımı, katı modelleme ve ikincil işleme yer alır.
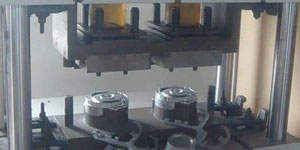
Döküm Endüstrileri Arabalar, Bisikletler, Uçaklar, Müzik aletleri, Deniz Araçları, Optik cihazlar, Sensörler, Modeller, Elektronik cihazlar, Muhafazalar, Saatler, Makineler, Motorlar, Mobilya, Mücevher, Jigler, Telekom, Aydınlatma, Tıbbi cihazlar, Fotoğraf cihazları, Robotlar, Heykeller, Ses ekipmanları, Spor ekipmanları, Aletler, Oyuncaklar ve daha fazlası.
Bundan sonra ne yapmanıza yardımcı olabiliriz?
∇ Ana Sayfaya Git Çin Döküm
→Döküm Parçaları-Ne yaptığımızı öğren.
→ Hakkında İlgili İpuçları Pres Döküm Hizmetleri
By Minghe Döküm Üreticisi |Kategoriler: Faydalı Makaleler |Malzeme Etiketler: Alüminyum Döküm, Çinko Döküm, Magnezyum Döküm, Titanyum Döküm, Paslanmaz Çelik Döküm, Pirinç Döküm,Bronz Döküm,Döküm Videosu,Tarihçe,Alüminyum Döküm |Yorumlar Kapalı