Emprenye Teknolojisinin Motor İmalatında Uygulanması
Alüminyum silindirler gibi hafif malzemelerden yapılmış parçaların emprenye işlemi, iş parçalarının hurda oranını etkili bir şekilde azaltabilir ve kalitelerini önemli ölçüde iyileştirebilir. Ürün kalitesini sağlama öncülüğünde, üretim maliyetlerini etkin bir şekilde azaltabilir ve üretim verimliliğini artırabilirler.
Motor hafifliği ve emprenye işlemi önerisi
Hafif ağırlık, dünya çapında çevre koruma ve enerji tasarrufuna gösterilen dikkat tarafından belirlenen çağdaş otomobil endüstrisinde bir trend haline geldi. Veriler, bir otomobilin kendi ağırlığı %10 oranında azaltılırsa yakıt verimliliğinin %15 oranında artırılabileceğini gösteriyor. Yakıt verimliliğindeki artış, otomobilin yakıt tüketiminin ve emisyonlarının azalması anlamına gelir. Bu nedenle, arabanın ağırlığını azaltmak, arabanın enerji tasarrufunu ve çevre korumasını iyileştirmenin en etkili yoludur. Motor, bir arabanın en kritik büyük grubudur ve ağırlığını azaltmak, arabanın ağırlığını azaltmak için çok önemlidir.
Teknik açıdan bakıldığında, tüm makine yapısının optimizasyonu, aksesuar modülleri ve hafif ağırlık gibi hafifliği elde etmenin birçok yolu vardır, ancak geleneksel malzemelerin yerine plastik, alüminyum alaşımları ve magnezyum alaşımları gibi hafif malzemelerin kullanılması gibi. dökme demir olarak mevcut azalmadır. Motor ağırlığının ana yolu. Aslında, alüminyum alaşımı motor silindir kafalarında, emme manifoldlarında ve su pompası gövdeleri ve yağ pompası gövdeleri gibi daha küçük parçalarda uzun yıllardır yaygın olarak kullanılmaktadır ve son on yılda giderek daha fazla şirket alüminyum alaşımlı silindir bloklarını benimsemiştir. Bununla birlikte, dökme demir ile karşılaştırıldığında, alüminyum dökümler, kristal oluşumu, büzülme ve gaz emilimi nedeniyle döküm işlemi sırasında iç gevşeklik, büzülme ve gözeneklere daha yatkındır. Bu kusurlu dökümler, işlemeden sonra yoğun bir yüzey tabakasına sahiptir. Alan kaldırılır, böylece dahili organizasyon kusurları ortaya çıkar. Motorda sızdırmazlık gerektiren alüminyum dökümler için üretim hattında kaçak tespit sürecinden geçerken kusurlu mikro gözeneklerin varlığı aşırı sızıntıya neden olacak ve bazen partiler halinde bile atık ürünler üretecektir. Bu koşullar ancak çoklu talaşlı imalattan sonra keşfedilebileceğinden ciddi adam-saat, hammadde ve enerji israfına da neden olacaktır. Alüminyum dökümlerin yüksek hurda oranı sorununu çözmek için üretimde belirli arıtma önlemlerinin alınması gerektiği görülmektedir. Şu anda en yaygın kullanılan teknoloji emprenye işlemi, yani sızıntı tıkamadır. Sözde "emprenye", infiltrantın belirli koşullar altında alüminyum dökümün mikro gözeneklerine sızmasıdır ve katılaşmadan sonra, gözenek içine sızan dolgu maddesi ve dökümün gözeneğinin iç duvarı bir bütün olarak bağlanır. Parçaların basınçlandırma, sızıntı önleme ve sızıntı önleme için gerekli olan bir işlem teknolojisini karşılayabilmesi için mikro gözenekleri bloke edin.
Vakum basıncı emprenye işlemi
Şu anda, alüminyum dökümlerin yurtiçinde ve yurtdışında üretiminde, genellikle vakumlu basınçlı sızma yöntemi benimsenmektedir. Bu işlem esas olarak bir vakum basınç tankında gerçekleştirilir. Proses akışına göre üç aşamaya ayrılabilir: ön işlem, emprenye işlemi ve işlem sonrası. Çeşitli adımları temel olarak şunları içerir: ön işleme mikro gözenekli ön işlem olarak da adlandırılır; bu işlem esas olarak bir sonraki işleme hazırlanmak için dökümleri yağdan arındırır, temizler ve kurutur; emprenye işleminin ilk adımı iş parçasını bir sepete yerleştirmektir. Ardından sepeti emprenye tankına yerleştirin; parçaların gözeneklerindeki gazı çıkarmak için emprenye tankını vakumlayın; dolgu macununu depolama tankından emprenye tankına taşıyın ve hala vakum altında olan parçaları daldırın; Dolgu macunundaki gazı çıkarmak için emprenye tankını tekrar vakumlayın; vakumu boşaltın ve emprenye tankını sıkıştırılmış hava ile basınçlandırın, bu da dolgu macununun gözeneklere itilmesine yardımcı olur; basıncı boşaltın ve dolgu macununu depolama tankına geri gönderin; İşlem sonrası esas olarak parçaları çıkarmak, sıkarak kurutmak, durulamak ve kürleme işlemlerini tamamlamaktır.
Ön işlemin temel amacı, parçaların yüzeyindeki yağ lekelerini, metal talaşları ve tozu çıkarmak, emprenye kalitesini iyileştirmek ve emprenye sıvısına yağ ve mekanik kirliliklerin girmesini ve penetrasyonu etkilemesini önlemektir. yapışma. Yaygın olarak kullanılan yağ giderme yöntemleri arasında solventle yağ giderme, kül suyuyla yağ giderme ve elektrokimyasal yağ giderme bulunur. Dökümler yukarıda belirtilen yağ alma ve temizleme işlemlerinden sonra çıkarılır, sıcak su ile durulanır ve ardından 80-90 ℃'de kurutulur. Islatma etkisini iyileştirmek ve büyük miktarda suyun vakum pompasına girmesini önlemek için temizlikten sonra kurutma çok önemlidir.
Emprenye işlemi, önceden işlenmiş iş parçalarını mühürlemek ve vakumlamak için emprenye tankına koymak, tanktaki hava ve ince tozu ve dökümün gözeneklerini tamamen çıkarmak ve doldurma ve sızma için basınç farkı dinamik koşullarını oluşturmaktır. emprenye maddesinin. Ardından infiltrant, tanktaki negatif basınç tarafından emilir ve vakum tekrar çekilir. İkinci vakumlamanın amacı, gazı içeren emprenye sıvısının dökümün mikro gözenekli kusurlarına nüfuz etmesini önlemek ve katılaşma sırasında sızdırmazlığı etkileyen gözeneklerin oluşmasını önlemek için tanktaki emprenye sıvısındaki gazı boşaltmaktır. verim. Son olarak, doldurulan ve dökümün gözeneklerine sızan sızıntının, kusurun her bir parçasının en derin kısmına daha fazla nüfuz etmesi için basınçlandırın. Emprenye, inorganik veya organik maddelerden hazırlanan sıvı bir maddedir. Şu anda en yaygın kullanılan metakrilat PC504/66 dolgu macunu ısıtma altında kürlenir ve polimerizasyon sırasında düşük büzülmesiyle belirgin mikro gözenek dolgusu sağlar. Yetenek, aynı zamanda düşük viskozitesi, dolgu macununun mikro gözeneklere hızlı ve derinlemesine nüfuz etmesine yardımcı olur. Kürleşmiş dolgu macunu -50~200 ℃ aralığında normal şekilde çalışabilir.
Son işlem, iş parçasını damlatmak, temizlemek ve katılaşması için bir kürleme fırınına koymaktır, böylece dökümün gözeneklerine giren infiltrant, katı bir katılaşmış film oluşturmak üzere sıvıdan katıya dönüşür. Sertleştirme sıcaklığı genellikle 80~90 ℃'ye ayarlanır veya 25 saat boyunca oda sıcaklığında (24 ℃'nin üzerinde) tutulur. Döküm 300 ℃ üzerinde kullanılırsa, 80 ℃'de 2 saat ve daha sonra 110 ℃'de 1 saat kürlenmelidir.
Üretim sürecinin hangi bölümünün emprenye edildiğine göre, farklı üretim tesisleri ve farklı iş parçası türleri çok farklıdır. Az sayıda şirket, yüksek üretim doğruluğu ve hava sızdırmazlığı gerektiren tüm aktarma organları parçaları için tek tip düzenlemeler yapacaktır: bu tür parçalar, iyileştirme elde etmek için işlemeden önce, yani hala döküm durumundayken emprenye edilmelidir. Döküm performansının amacı, talaşlı imalat sırasında takım ömrünün uzatılması ve ürün kalitesinin sağlanmasıdır. Bununla birlikte, çoğu fabrika hala farklı parça türlerine göre farklı yöntemler benimsemektedir. Genel olarak konuşursak, motordaki alüminyum silindir bloğu gibi birkaç önemli parça için, genellikle tüm parçaların döküm halindeyken emprenye edilmesi ve ardından gönderilmesi gerekir. OEM. OEM'in üretim hattında belirli bir süreçten sonra bazı iş parçalarının belirli kriterlere göre emprenye edilmesi ise OEM'in üretim sürecine bağlıdır.
Çoğu parça için, genellikle döküm halindeyken emprenye edilmeleri gerekmez. Bunun yerine fiili duruma göre üretim sürecinde belli bir süreçten sonra emprenye işlemi uygulanmaktadır. Yani, birkaç işleme işleminden sonra parçalar, bazı parçaların sızıntı tespit değerinin belirtilen aralık içinde olduğu onaylandığında, reddedilen iş parçasının yalnızca bu kısmı emprenye edilir. Çoğu durumda, reddedilen iş parçalarının oranı çok düşüktür (kabaca %1 ila %2), ancak bu oran belirli bir sınırı aştığında (özel duruma bağlı olarak), OEM boş fabrikanın tüm dökümlerin emprenye edilmesini isteyecektir. .
Ayrıca yapısal nedenlerden dolayı OEM'in üretim sürecine dahil edilmeyen emprenye işlemi gerektiren bazı parçalar da vardır. Kaçak tespit sonuçları tolerans dışı olan parçalar için, gerçek ölçüm değeri ne kadar büyük olursa olsun, doğrudan hurdaya çıkarılacaktır. Ancak, sızıntı değeri iş parçasının oranını belirli bir ölçüde aşarsa, ana motor fabrikası da tüm döküm boşlukları için emprenye işlemi gerekliliğini ortaya koyacaktır.
Peki, emprenye işleminin fiili işlemi nerededir? Yurtiçinde ve yurtdışında ortak uygulama, bağımsız ve profesyonel işletmeler tarafından üstlenilmektedir. Bu sadece verimli ve kaliteyi sağlamak kolay olmakla kalmaz, aynı zamanda montaj tesisi için maliyet de nispeten düşüktür. Bununla birlikte, büyük partilere, hızlı üretim hızına ve yüksek ürün kalitesi gereksinimlerine sahip birkaç motor fabrikası da bulunmaktadır. Atölyede kapalı bir alan açacaklar, böylece yukarıda belirtilen emprenye işlemi yapan profesyonel fabrikalar nispeten tek, verimli ve daha yüksek derecede mekanizasyona sahip emprenye üretim hattı, atölyenin bir bölümüne eşdeğerdir. Tabii ki, bu "çalışma bölümünün" çalışma hızı, genel bir üretim hattından daha düşüktür.
Emprenye edilmiş iş parçalarının çoklu tanımlarını gerçekleştirin
Hepimizin bildiği gibi motorun ana gövdesi olarak silindir bloğu bunlar arasında en büyük ve en ağır kısımdır. Alüminyum alaşımı seçildiğinde, ağırlığının yaklaşık yarı yarıya azaltılması, motorun hafifliği için en büyük öneme sahiptir. Bununla birlikte, motordaki diğer alüminyum dökümlerle karşılaştırıldığında, silindir bloğunun karmaşık yapısı ve işleme işlemlerinin sayısı göz önüne alındığında, döküm ve biçimlendirme işlemi sırasında alüminyum silindir bloğunda iç kusur olasılığı da daha yüksektir. Bu nedenle, kalitesini sağlamak için daldırma Sızma sürecinin nasıl standartlaştırılacağı ve verimli bir şekilde benimseneceği de işletmeler tarafından en çok ilgilenilen konudur. Aşağıda alüminyum silindir örnek alınarak, emprenye edilmesi gereken iş parçalarının tanımlanması ve onaylanması sorunu temsili bir vaka üzerinden daha ayrıntılı olarak açıklanmaktadır. Modern bir araba motoru fabrikasında yeni inşa edilmiş bir alüminyum silindir işleme üretim hattı, iş parçası ara temizleme istasyonuna girmeden önce tüm kaba işleme süreçlerini tamamladı. Ana yatak kapağının bir sonraki montajından ve müteakip bitirme işlemlerinden önce bir sızdırmazlık test istasyonu kuruldu. Alüminyum silindir bloğunun düşük basınçlı yağ geçişi, su geçişi ve yüksek basınçlı yağ geçişinin kaçak tespitinin yanı sıra bu istasyon aynı zamanda bir kapı kurmaya eşdeğerdir. Ölçülen kaçak değerine göre bu alüminyum silindirin emprenye edilip edilmediğini belirlemek gerekir.
İş parçası için ayarlanmış iki tarama limiti vardır: ilki, düşük basınçlı yağ kanalını örnek alarak incelenen parçanın kaçak oranıdır, kaçak oranı limiti 30 CC/dak'dır; ikinci eleme sınırı Bu denetlenen parça, alüminyum silindirde bir sızıntı olup olmadığını, ancak emprenye işlemiyle gidermenin mümkün ve gerekli olup olmadığını belirleme amacıdır. Alçak basınçlı yağ geçişi örnek olarak alındığında, tablo bunun 500 CC/dk olduğunu göstermektedir. Bunun ışığında, ara temizleme işleminden sonra alüminyum silindir gövdesi taşıma kanalı boyunca sızdırmazlık test istasyonuna girdiğinde, iş parçasının ölçülen sızıntı değerlerinden herhangi biri tabloda verilen ilgili eleme sınırından düşükse, Sızıntı oranı nitelikli olarak değerlendirilecek ve daha sonra bir sonraki sürece akacaktır. Ancak ölçülen gerçek sızıntı değerlerinden herhangi biri sızıntı oranını aştığı ancak hurda sınırının altında olduğu sürece, örnek olarak tablodaki düşük basınçlı yağ geçişini alın, aralık 30 ile 500CC/dak arasındadır. Alüminyum silindir bloğu, emprenye işlemi için çıkarılması gereken, kanal tarafından ters yönde gönderilen ve daha sonra manuel olarak çıkarılıp gönderilen bir iş parçası olarak işlem görür. Ölçülen sızıntı değeri tablodaki hurda sınırına ulaşan veya hatta aşan çok az sayıda iş parçasına gelince, bunlar konveyör kanalından dışarı akacaktır. Yukarıda bahsedilen algılama, tarama ve yönlendirme işlemi robot tarafından sızdırmazlık test istasyonunda gerçekleştirilir.
Özetle, alüminyum silindirlerin ve diğer parçaların emprenye işleminden sonra, sadece hurda oranı azalmaz ve kalite önemli ölçüde iyileşir, aynı zamanda kaliteyi sağlama öncülüğünde üretim maliyeti de azalır ve üretkenlik etkin bir şekilde iyileştirilir. Bu nedenle, çağdaş otomobil motoru endüstrisinin giderek daha hafif hale gelmesi sürecinde, sızma teknolojisinin bilimsel ve makul kullanımı, alüminyum alaşımının ve diğer hafif malzeme dökümlerinin (mikro gözenekler gibi kusurlar gibi) doğasında bulunan sorunları tamamen çözmek için en iyi çözümdür.
Lütfen yeniden basım için bu makalenin kaynağını ve adresini saklayın:Emprenye Teknolojisinin Motor İmalatında Uygulanması
Minhe Basınçlı Döküm Şirketi kaliteli ve yüksek performanslı Döküm Parçaları üretmeye ve sağlamaya adamıştır (metal döküm parça yelpazesi esas olarak şunları içerir: İnce Duvarlı Döküm,Sıcak Kamara Basınçlı Döküm,Soğuk Oda Döküm), Yuvarlak Servis (Döküm Servisi,Cnc İşleme,Kalıp yapımı,Yüzey İşleme).Herhangi bir özel Alüminyum döküm, magnezyum veya Zamak/çinko döküm ve diğer döküm gereksinimleri bizimle iletişime geçebilirsiniz.
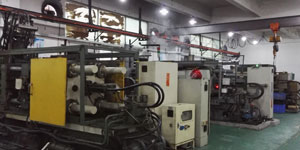
ISO9001 ve TS 16949 kontrolünde, tüm işlemler yüzlerce gelişmiş basınçlı döküm makinesi, 5 eksenli makine ve blasterlerden Ultra Sonic yıkama makinelerine kadar diğer tesisler aracılığıyla gerçekleştirilir. Müşterinin tasarımını gerçeğe dönüştürmek için deneyimli mühendisler, operatörler ve müfettişlerden oluşan ekip.
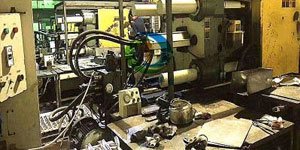
Dökümlerin sözleşmeli üreticisi. Yetenekler, 0.15 lbs'den başlayan soğuk oda alüminyum döküm parçaları içerir. 6 lbs'ye kadar, hızlı değişim kurulumu ve işleme. Katma değerli hizmetler arasında polisaj, titreşim, çapak alma, kumlama, boyama, kaplama, kaplama, montaj ve kalıplama yer alır. Çalışılan malzemeler arasında 360, 380, 383 ve 413 gibi alaşımlar bulunur.
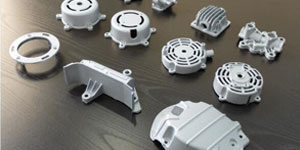
Çinko pres döküm tasarım yardımı/eşzamanlı mühendislik hizmetleri. Hassas çinko dökümlerin özel üreticisi. Minyatür dökümler, yüksek basınçlı dökümler, çok kızaklı kalıp dökümleri, geleneksel kalıp dökümleri, birim kalıp ve bağımsız kalıp dökümleri ve boşluklu sızdırmaz dökümler üretilebilir. Dökümler, +/- 24 inç toleransta 0.0005 inç'e kadar uzunluk ve genişliklerde üretilebilir.
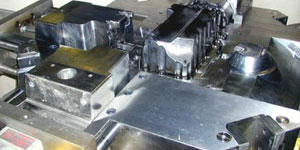
ISO 9001: 2015 sertifikalı döküm magnezyum üreticisi, Yetenekler arasında 200 ton sıcak odaya ve 3000 ton soğuk odaya kadar yüksek basınçlı magnezyum kalıp dökümü, takım tasarımı, cilalama, kalıplama, işleme, toz ve sıvı boyama, CMM özelliklerine sahip tam kalite güvencesi bulunur , montaj, paketleme ve teslimat.
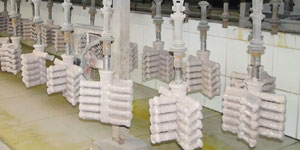
ITAF16949 sertifikalı. Ek Döküm Hizmeti Dahil yatırım dökümleri,kum dökümü,Yerçekimi Döküm, Kayıp Köpük Döküm,Savurma döküm,Vakumlu Döküm,Kalıcı Kalıp Döküm,.Yetenekler arasında EDI, mühendislik yardımı, katı modelleme ve ikincil işleme yer alır.
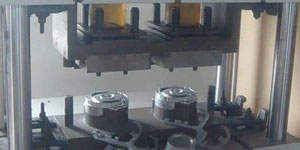
Döküm Endüstrileri Arabalar, Bisikletler, Uçaklar, Müzik aletleri, Deniz Araçları, Optik cihazlar, Sensörler, Modeller, Elektronik cihazlar, Muhafazalar, Saatler, Makineler, Motorlar, Mobilya, Mücevher, Jigler, Telekom, Aydınlatma, Tıbbi cihazlar, Fotoğraf cihazları, Robotlar, Heykeller, Ses ekipmanları, Spor ekipmanları, Aletler, Oyuncaklar ve daha fazlası.
Bundan sonra ne yapmanıza yardımcı olabiliriz?
∇ Ana Sayfaya Git Çin Döküm
→Döküm Parçaları-Ne yaptığımızı öğren.
→ Hakkında İlgili İpuçları Pres Döküm Hizmetleri
By Minghe Döküm Üreticisi |Kategoriler: Faydalı Makaleler |Malzeme Etiketler: Alüminyum Döküm, Çinko Döküm, Magnezyum Döküm, Titanyum Döküm, Paslanmaz Çelik Döküm, Pirinç Döküm,Bronz Döküm,Döküm Videosu,Tarihçe,Alüminyum Döküm |Yorumlar Kapalı