Yüksek Mukavemetli Gri Dökme Demir Eritme Teknolojisi
Bu makale, elektrikli fırın eritme işleminde daha yüksek karbon eşdeğeri ve daha iyi işleme performansı gereksinimleri koşulları altında yüksek mukavemetli gri dökme demir eritme teknolojisinin nasıl elde edileceğini ve malzemenin eser elementlerinin nasıl kontrol edileceğini tanıtmaktadır.
Anahtar kelimeler: gri dökme demir, karbon eşdeğeri, mekanik özellikler, işleme özellikleri, eser elementler
Geleneksel gri dökme demir eritme kontrol yönü, düşük karbonlu yüksek mukavemetli dökme demirdir (C: 2.7~3.0, Si: 2.0~2.3, Mn: 0.9~1.3). Bu tür malzemeler, malzemenin mekanik özelliklerinin, döküm performanslarının ve işlenmesinin gereksinimlerini karşılayabilmesine rağmen Performans zayıftır. Şirketin pazar gelişimi ve genişlemesi ile, özellikle MINGHE kupol eritme işleminin yerini almak için güç frekanslı elektrikli fırın eritme işlemini kullandığında, MINGHE üretim dizisine, yüksek zorluk ve yüksek teknik kalite gereksinimlerine sahip daha fazla döküm ürünü dahil edilmektedir.
Müşteri sipariş gereksinimlerini karşılamak için elektrikli fırın ergitme koşulları altında yüksek karbon eşdeğeri yüksek mukavemetli dökme demir elde etmek o zamanlar bir araştırma konusuydu. Bu makale, elektrikli fırın eritme koşulları altında yüksek mukavemetli gri dökme demirin üretim teknolojisini açıklamaktadır.
Malzeme Performansını Etkileyen Faktörler
1.1 Karbon eşdeğerinin malzeme özellikleri üzerindeki etkisi
Gri dökme demirin özelliklerini belirleyen ana faktörler, grafit morfolojisi ve metal matrisin özellikleridir. Karbon eşdeğeri (CE=C+1/3Si) yüksek olduğunda grafit miktarı artar ve kuluçka koşulları iyi olmadığında veya eser zararlı elementler bulunduğunda grafitin şekli bozulur. Bu tür grafit, metal matrisin yükü taşıyabilen etkin alanını azaltır ve yükü taşırken stres konsantrasyonuna neden olur, böylece metal matrisin mukavemeti normal olarak kullanılamaz, böylece dökme demirin mukavemetini azaltır. Malzemeler arasında perlit iyi mukavemet ve sertliğe sahipken, ferrit daha yumuşak bir tabana ve daha düşük mukavemete sahiptir. C ve Si miktarı arttıkça perlit miktarı azalacak ve ferrit miktarı artacaktır. Bu nedenle, karbon eşdeğerindeki artış, hem grafit şeklindeki hem de matris yapısındaki dökme demir dökümlerin çekme mukavemetini ve döküm öğesinin sertliğini etkileyecektir. Ergitme işleminin kontrolünde, karbon eşdeğerinin kontrolü malzeme performansının çözülmesi için çok önemli bir faktördür.
1.2 Alaşım elementlerinin malzeme özellikleri üzerindeki etkisi
Gri dökme demirdeki alaşım elementleri esas olarak Mn, Cr, Cu, Sn, Mo ve perlit oluşumunu destekleyen diğer elementlere atıfta bulunur. Bu elementlerin içeriği perlitin içeriğini doğrudan etkileyecektir. Aynı zamanda alaşım elementlerinin eklenmesi nedeniyle belirli bir oranda rafine edilir. Grafit ilavesi, matristeki ferrit miktarını azaltır veya hatta ortadan kaldırırken, perlit belirli bir dereceye kadar rafine edilir ve içindeki ferrit, belirli miktarda alaşım elementi nedeniyle katı bir çözeltidir, böylece dökme demir her zaman vardır. Daha yüksek Mukavemet performansı. Eritme işleminin kontrolünde alaşımın kontrolü de önemli bir araçtır.
1.3 Yük oranının malzemeler üzerindeki etkisi
Geçmişte, kimyasal bileşim spesifikasyonun gerekliliklerini karşıladığı sürece, malzemenin standart mekanik özelliklerini karşılayan bir görünüm elde edebilmemiz gerektiğinde her zaman ısrar ettik, ancak aslında bu görüş yalnızca geleneksel kimyasalı görür. bileşiminde bulunur ve içindeki bazı alaşım elementlerini ve zararlı elementleri yok sayar. Görevi. Örneğin, pik demir Ti'nin ana kaynağıdır, bu nedenle kullanılan pik demir miktarı malzemedeki Ti içeriğini doğrudan etkileyecek ve malzemenin mekanik özellikleri üzerinde büyük bir etkisi olacaktır. Benzer şekilde, hurda çeliği birçok alaşım elementinin kaynağıdır, bu nedenle hurda miktarının dökme demirin mekanik özellikleri üzerinde çok doğrudan bir etkisi vardır. Elektrikli fırının devreye girdiği ilk günlerde, her zaman kupol fırınının şarj oranını kullanıyorduk (pik demir: %25~35, hurda çelik: %30~35). Sonuç olarak malzemenin mekanik özellikleri (çekme mukavemeti) çok düşüktü. Kullanılan çelik miktarı dökme demirin performansını etkilediğinde, hurda miktarı zaman içinde ayarlandıktan sonra sorun hızlı bir şekilde çözülür. Bu nedenle hurda çelik, ergitme kontrol sürecinde çok önemli bir kontrol parametresidir. Bu nedenle, şarj oranı, dökme demir malzemelerin mekanik özellikleri üzerinde doğrudan bir etkiye sahiptir ve ergitme kontrolünün odak noktasıdır.
1.4 İz elementlerin malzeme özellikleri üzerindeki etkisi
Geçmişte, ergitme işlemi sırasında sadece geleneksel beş ana elementin dökme demirin kalitesi üzerindeki etkisine dikkat ederken, diğer eser elementlerin etkisi sadece nitel bir anlayıştı, ancak nadiren nicel olarak analiz edildi ve tartışıldı. Son yıllarda, döküm teknolojisi İlerlemesinin etkisiyle, ergitme ekipmanı sürekli olarak güncellenmekte ve kupollerin yerini kademeli olarak elektrikli fırınlar almaktadır. Elektrikli fırın ergitme kupol ergitmede benzersiz avantajlara sahip olsa da, elektrikli fırın ergitme kupol ergitmenin bazı avantajlarını da kaybeder, bu nedenle bazı eser elementlerin dökme demir üzerindeki etkisi de yansıtılır. Kupoldeki metalurjik reaksiyon çok güçlü olduğundan, yük güçlü bir oksitleyici atmosferde olduğundan, çoğu oksitlenir ve cürufla birlikte boşaltılır, erimiş demirde sadece küçük bir kısım kalır, bu nedenle bazılarının olumsuz etkisi vardır. döküm Kupolün metalürjik süreci boyunca, eser elementlerin genellikle dökme demir üzerinde olumsuz bir etkisi yoktur. Kupolün ergitme işlemi sırasında, kok içindeki nitrojenin bir kısmı ve havadaki nitrojen (N2), yüksek sıcaklıklarda atomlar şeklinde erimiş demirde çözülür ve erimiş demirdeki nitrojen içeriği nispeten yüksek olur.
İstatistiklere göre, elektrikli fırının devreye alınmasından bu yana, yüksek kurşun içeriğinden kaynaklanan atık ürünler ve kurşun içeriği ayarlanamayacak kadar yüksek olduğu için hurdaya ayrılan erimiş demir 100 tondan az değildi ve niteliksiz ürün sayısı nedeniyle Yetersiz nitrojen içeriği de oldukça yüksekti ve bu da şirkete büyük ekonomik kayıplara neden oldu.
Uzun yıllara dayanan elektrikli fırın ergitme deneyimimize ve teorimize dayanarak, elektrikli fırın ergitme sürecindeki temel eser elementlerin esas olarak N, Pb ve Ti olduğuna inanıyorum. Bu elementlerin gri dökme demir üzerindeki etkileri başlıca şu şekildedir:
Kurşun
Erimiş demirdeki kurşun içeriği yüksek olduğunda (>20PPm), özellikle daha yüksek hidrojen içeriği ile etkileşime girdiğinde, kalın kesitli dökümlerde Widmanstatten grafit oluşturmak kolaydır. Bunun nedeni reçine kumunun iyi ısı yalıtım özelliklerine sahip olması ve erimiş demirin kalıpta soğumasının daha yavaş olması (bu eğilim kalın kesitlerde daha belirgindir), erimiş demirin daha uzun süre sıvı halde kalması ve erimiş demirin katılaşmasıdır. erimiş demir, kurşun ve hidrojenin etkisiyle denge durumunda katılaşma durumuna daha yakındır. Bu tip döküm katılaştığında ve soğumaya devam ettiğinde, ostenit içindeki karbon çökelecek ve katı halde ikincil grafit haline gelecektir. Normal şartlar altında, ikincil grafit, mekanik özellikler üzerinde büyük bir etkisi olmayacak olan ötektik grafit pullarını sadece kalınlaştırır. Bununla birlikte, nitrojen ve hidrojen içeriği yüksek olduğunda, aynı sabit ostenit kristal düzlemi üzerindeki grafitin yüzey enerjisi azalacak ve ikincil grafit, belirli bir ostenit kristal düzlemi boyunca büyüyecek ve metal matrisine uzanacaktır. Mikroskop altında gözlemleyin. Birçok küçük çapak benzeri grafit pulu, Widman grafitinin oluşumunun nedeni olan, yaygın olarak grafit kılları olarak bilinen pul grafit pullarının yanında büyür. Dökme demirdeki alüminyum, sıvı demirin hidrojeni emmesini ve hidrojen içeriğini artırmasını sağlayabilir. Bu nedenle alüminyum, Widmanstatten grafit oluşumu üzerinde dolaylı bir etkiye de sahiptir.
Widmanstatten grafit dökme demirde göründüğünde, mekanik özellikleri, özellikle de şiddetli durumlarda yaklaşık %50 oranında azaltılabilen mukavemet ve sertlik büyük ölçüde etkilenir.
Widman grafiti aşağıdaki metalografik özelliklere sahiptir:
- 1) 100 katlı fotomikrografta, Widmanstatten grafit olan kaba grafit puluna bağlı birçok küçük diken benzeri grafit pulu vardır.
- 2) Ortak kristal grafitin ilişkisi birbirine bağlıdır.
- 3) Widmanstatten grafit ağı, oda sıcaklığında matrisin içine uzandığında, matrisin kırılgan yüzeyi haline gelir ve bu da gri dökme demirin mekanik özelliklerini önemli ölçüde azaltacaktır. Ancak enine kesit görünümden, kırılma çatlakları hala ko-talaş benzeri grafit boyunca uzanıyor.
Azot
Uygun miktarda nitrojen, grafit çekirdeklenmesini teşvik edebilir, perliti stabilize edebilir, gri dökme demirin yapısını iyileştirebilir ve gri dökme demirin performansını iyileştirebilir.
Azotun gri dökme demir üzerinde iki ana etkisi vardır. Biri grafitin şekli üzerindeki etki, diğeri ise matris yapısı üzerindeki etkidir. Azotun grafit morfolojisi üzerindeki etkisi çok karmaşık bir süreçtir. Esas olarak kendini gösterir: grafit yüzey üzerindeki adsorpsiyon tabakasının etkisi ve ötektik grubun boyutunun etkisi. Nitrojen grafitte hemen hemen çözünmez olduğundan, ötektik katılaşma işlemi sırasında grafit büyümesinin ön tarafında ve grafitin her iki tarafında azot sürekli olarak adsorbe edilir, bu da özellikle grafit genişlediğinde, çökelme işlemi sırasında çevreleyen grafit konsantrasyonunda bir artışa neden olur. Erimiş demir. Uçta, sıvı-katı arayüzünde grafitin büyümesini etkiler. Ötektik büyüme işlemi sırasında, grafit levhanın ucunda ve her iki tarafında azot konsantrasyonu dağılımında önemli bir fark vardır. Grafit yüzeyindeki azot atomlarının adsorpsiyon tabakası, karbon atomlarının grafit yüzeyine difüzyonunu engelleyebilir. Grafit cephesinin nitrojen konsantrasyonu iki tarafınkinden daha yüksek olduğunda, grafitin uzunlamasına yönde büyüme hızı azalır. Buna karşılık, yanal büyüme daha kolay hale gelir ve sonuç olarak grafit kısalır ve kalınlaşır. Aynı zamanda, grafit büyüme sürecinde her zaman kusurlar olduğu için, azot atomlarının bir kısmı kusur konumunda adsorbe edilir ve dağılamaz ve tane sınırı grafit büyümesinin önünde asimetrik olarak eğimli olacaktır ve dinlenme hala orijinal yönde büyüyecektir. Grafit dallar üretir ve grafit dallarının artması, grafitin kısalmasının bir başka nedenidir. Bu şekilde, grafit yapının iyileştirilmesi nedeniyle, dökme demir performansının iyileştirilmesine elverişli olan matris yapısı üzerindeki bölme etkisi azaltılır.
Azotun matris yapısı üzerindeki etkisi perlit dengeleyici bir element olmasıdır. Azot içeriğindeki artış, dökme demirin ötektoid dönüşüm sıcaklığını düşürür. Bu nedenle, gri dökme demirde belirli bir miktarda nitrojen bulunduğunda, ötektoid dönüşümün aşırı soğuma derecesi arttırılabilir, böylece perlit arıtılır. Öte yandan, nitrojenin atom yarıçapı karbon ve demirinkinden daha küçük olduğu için, kristal kafesinin bozulmasına neden olarak ferrit ve sementit içinde çözünmek için arayer atomları olarak kullanılabilir. Yukarıdaki iki nedenden dolayı azot, matris üzerinde güçlendirici bir etkiye sahip olabilir.
Azot, gri dökme demirin performansını iyileştirebilse de, belirli bir miktarı aştığında, Şekil 2'de gösterildiği gibi azot gözenekleri ve mikro çatlaklar oluşacaktır, bu nedenle azot kontrolü belirli bir aralıkta kontrol edilmelidir. Genellikle 70-120PPm, 180PPm'yi aştığında, dökme demirin performansı keskin bir şekilde düşecektir.
Ti, dökme demirde zararlı bir elementtir. Bunun nedeni, titanyumun nitrojen ile güçlü bir afiniteye sahip olmasıdır. Gri dökme demirde titanyum içeriği yüksek olduğunda azotun güçlendirici etkisine faydalı değildir. İlk olarak, nitrojen ile bir TiN bileşiği oluşturur, bu da azaltır. Aslında, bunun nedeni tam olarak bu serbest nitrojenin gri dökme demir üzerinde katı bir çözelti güçlendirme etkisine sahip olmasıdır. Bu nedenle titanyum içeriğinin seviyesi gri dökme demirin performansını dolaylı olarak etkiler.
Erime kontrol teknolojisi
2.1 Malzemenin kimyasal bileşiminin seçimi
Yukarıdaki analiz yoluyla, kimyasal bileşimin kontrolü ergitme teknolojisinde çok önemlidir ve ergitme kontrolünün temelidir. Bu nedenle, malzemenin performansını sağlamak için makul bir kimyasal bileşim esastır. Genellikle, yüksek mukavemetli dökme demirin (çekme mukavemeti ≥300N/mm2) bileşim kontrolü esas olarak vb. içerir. C, Si, Mn, P, S, Cu, Cr, Pb, N
2.3 İz elementlerin kontrol teknolojisi
Gerçek proses kontrolünde, yükün analizine dayalı olarak, kurşun kaynağının esas olarak hurda çelik olduğu teyit edilir. Bu nedenle, hammaddedeki kurşunun kontrolü esas olarak hurda çelikteki Pb kapanımlarını kontrol etmektir ve kurşun içeriği genellikle 15 ppm'nin altında kontrol edilir. Ham erimiş demirdeki kurşun içeriği > 20 ppm ise, inkübasyon tedavisi sırasında özel bozulma tedavisi yapılacaktır.
Ti esas olarak pik demirden elde edildiğinden, Ti'nin kontrolü esas olarak pik demiri kontrol etmektir. Bir yandan, satın alırken pik demirde Ti içeriği konusunda katı gereksinimlerin ortaya konulması gerekmektedir. Genellikle, pik demirin titanyum içeriğinin: Ti<%0.8 olması gerekir ve diğer bir yön, kullanım miktarını pik demirin titanyum içeriğine göre zamanında ayarlamaktır.
Esas olarak yeniden karbonlama malzemeleri ve hurda çelikten gelir, bu nedenle N'nin kontrolü esas olarak yeniden karbonlama malzemelerini ve hurda çeliği kontrol etmektir. Bununla birlikte, yukarıda bahsedildiği gibi, çok düşük ve çok yüksek, gri dökme demirin performansı üzerinde olumsuz bir tarafa sahiptir, bu nedenle N'nin içeriği genellikle: 70~120ppm'dir, ancak N'nin içeriği, Ti'nin içeriği. Genel olarak, N ve Ti arasındaki ilişki şöyledir: N:Ti=1:3.42, yani Ti'nin %0.01'i 30PPm nitrojen emebilir. Üretim sırasında önerilen genel azot miktarı: N=0.006~0.01+Ti/3.42.
2.4 Eritme işleminin kontrol teknolojisi
1) Aşılama teknolojisi
Aşılama işleminin amacı, grafitizasyonu teşvik etmek, beyaz ağız eğilimini azaltmak ve uç yüzey hassasiyetini azaltmaktır; grafit morfolojisini kontrol edin ve aşırı soğutulmuş grafiti ortadan kaldırın; ötektik kümelerin sayısını uygun şekilde arttırın ve dökme demirin mukavemet performansını ve diğer performans amaçlarını iyileştirmek için pul perlit oluşumunu teşvik edin.
Erimiş demir sıcaklığının aşılama üzerindeki etkisi ve erimiş demir sıcaklığının kontrol edilmesi aşılama üzerinde önemli etkiye sahiptir. Erimiş demirin aşırı ısınma sıcaklığının belirli bir aralıkta arttırılması ve belirli bir süre tutulması, pik demirin genetik etkisini ortadan kaldırmak için erimiş demirde tamamen çözülebilen çözünmemiş grafit parçacıklarının erimiş demirde kalmasını sağlayabilir ve aşılayıcının aşılama etkisine tam oyun verin, Erimiş demirin doğurganlık yeteneğini geliştirin. Proses kontrolünde, aşırı ısınma sıcaklığı 1500~1520℃'ye yükseltilir ve aşılama sıcaklığı 1420~1450℃'de kontrol edilir.
Aşılayıcının partikül boyutu, aşılayıcının durumunun önemli bir göstergesidir ve aşılayıcı etkisi üzerinde büyük bir etkiye sahiptir. Parçacık boyutu çok ince ise, erimiş cürufa dağılması veya oksitlenmesi ve etkisini kaybetmesi kolaydır. Parçacık boyutu çok büyükse, aşılayıcı tamamen erimez veya çözülmez. Sadece aşılama etkisini tam olarak uygulayamamakla kalmaz, aynı zamanda ayrışma, sert noktalar, aşırı soğutulmuş grafit ve diğer kusurlara neden olur. Bu nedenle, aşılayıcının parçacık boyutu mümkün olduğunca 2~5 mm arasında kontrol edilmelidir. Kuluçka etkisini sağlayın.
Proses kontrolünde, inokülasyon prosesi esas olarak inkübasyon tankında inoküle edilir, böylece bir döküm paketinin dökülmesi inkübasyon azalmadan temel olarak tamamlanabilir. Ancak nispeten büyük parçalar ve çift pota ile dökülen parçalar için gereksinimleri karşılayamaz. Bu nedenle, geç aşılama yöntemi benimsenmiştir: yani, yüzen silikon aşılama, döküm dökülmeden önce pota içinde gerçekleştirilir (aşı miktarı %0.1'dir), bu da aşılama düşüşünü azaltır veya yoktur ve aşılama etkisini iyileştirir.
2) Alaşımlama işlemi
Alaşımlama işlemi, gri dökme demirin mekanik özelliklerini iyileştirmek için sıradan dökme demire az miktarda alaşım elementi ekler. Eritme işleminin kontrolünde, alaşımların eklenmesi esas olarak müşterilerin su verilmesini istediği parçalar ve nispeten kalın kılavuz raylara sahip parçalar, eklenen ana alaşım elementleri ve ilave miktarı içindir.
Bu, CE değerindeki artıştan dolayı performansın düşmesini bir dereceye kadar sağlar ve su verilmiş parçalar için su verme sırasında sertleşebilirlik iyileştirilir. Söndürme derinliğini sağlayın.
Besleme ve ergitme işlemi sırasında bu aşamadaki anahtar kontrolün besleme sırası, hurda çelik, mekanik demir ve pik demiri öncelik sırasına göre beslemektir. Alaşım elementlerinin yanma kaybını azaltmak için, sonunda ferroalyaj eklenmelidir. Soğuk malzeme tamamen temizlendiğinde, sıcaklık 1450℃'ye yükseltilir. Bu A noktasıdır. 1450°C'den düşükse, yeniden karbonlaştırıcı veya ferroalyajın eksik çözünme riski vardır.
AB paragraflarında aşağıdaki işlemler yapılmalıdır:
- Sıcaklık ölçümü;
- cüruf mucking;
- Kimyasal bileşimin örneklenmesi ve analizi;
- Termal spektrometre ile geleneksel elementleri ve eser elementleri analiz edin;
- CW değerini ölçmek için üçgen test parçasını alın;
- Erimiş demiri çeşitli test sonuçlarına göre ayarladıktan sonra, 10 dakika boyunca güç sağlamaya devam edin ve ardından yeniden numune alın ve analiz edin. Tüm verilerin normal olduğunu doğruladıktan sonra, sıcaklığı yaklaşık 1500°C'ye, yani C noktasına yükseltmeye devam edin. CD bölümünde, erimiş demiri 5 ila 10 dakika bekletin ve ardından test etmek için bir üçgen test parçası alın. CW değeri. Sıcaklığı ölçtükten sonra ütüyü kılavuz çekmek için hazırlayın.
Üçgen test parçası kontrolü
Farklı kaliteler için, farklı üçgen test bloklarının beyaz ağız (CW) kontrol aralığını belirleyin ve fırının önündeki bileşim analizi ile birlikte erimiş demirin kalitesini belirleyin.
Sonuç
Yukarıda belirtilen gri dökme demir eritme teknolojisi, 8'dan 1996'e kadar 2003 yıl boyunca CSMF'de başarıyla uygulanmıştır. Dökümlerin CE'si, çekme mukavemeti indeksi veya fiziksel sertlik indeksi olsun, 3.6~3.9 öncül altında kontrol edilir ( özellikle bir kısmı Takım tezgahı parçalarının kılavuz rayının sertliği, dökümün kesme performansını büyük ölçüde artıran gereksinimleri karşılar.Bu teknolojinin nihai bir teknoloji olduğu kanıtlanmıştır ve kontrol noktaları aşağıdaki gibidir:
- 3.1 Malzemelerin kimyasal bileşiminin kontrolü
- 3.2 Yük oranının belirlenmesi
- 3.3 İz elementlerin kontrol teknolojisi
- 3.4 Aşılama işlemi sürecinin kontrolü
- 3.5 Alaşımlama işlemi
- 3.6 Eritme işleminin sıcaklık kontrolü
- 3.7 Üçgen test parçasının kontrolü
Lütfen yeniden basım için bu makalenin kaynağını ve adresini saklayın: Yüksek Mukavemetli Gri Dökme Demir Eritme Teknolojisi
Minhe Basınçlı Döküm Şirketi kaliteli ve yüksek performanslı Döküm Parçaları üretmeye ve sağlamaya adamıştır (metal döküm parça yelpazesi esas olarak şunları içerir: İnce Duvarlı Döküm,Sıcak Kamara Basınçlı Döküm,Soğuk Oda Döküm), Yuvarlak Servis (Döküm Servisi,Cnc İşleme,Kalıp yapımı,Yüzey İşleme).Herhangi bir özel Alüminyum döküm, magnezyum veya Zamak/çinko döküm ve diğer döküm gereksinimleri bizimle iletişime geçebilirsiniz.
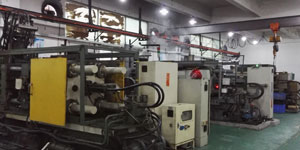
ISO9001 ve TS 16949 kontrolünde, tüm işlemler yüzlerce gelişmiş basınçlı döküm makinesi, 5 eksenli makine ve blasterlerden Ultra Sonic yıkama makinelerine kadar diğer tesisler aracılığıyla gerçekleştirilir. Müşterinin tasarımını gerçeğe dönüştürmek için deneyimli mühendisler, operatörler ve müfettişlerden oluşan ekip.
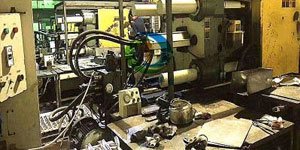
Dökümlerin sözleşmeli üreticisi. Yetenekler, 0.15 lbs'den başlayan soğuk oda alüminyum döküm parçaları içerir. 6 lbs'ye kadar, hızlı değişim kurulumu ve işleme. Katma değerli hizmetler arasında polisaj, titreşim, çapak alma, kumlama, boyama, kaplama, kaplama, montaj ve kalıplama yer alır. Çalışılan malzemeler arasında 360, 380, 383 ve 413 gibi alaşımlar bulunur.
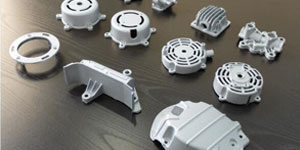
Çinko pres döküm tasarım yardımı/eşzamanlı mühendislik hizmetleri. Hassas çinko dökümlerin özel üreticisi. Minyatür dökümler, yüksek basınçlı dökümler, çok kızaklı kalıp dökümleri, geleneksel kalıp dökümleri, birim kalıp ve bağımsız kalıp dökümleri ve boşluklu sızdırmaz dökümler üretilebilir. Dökümler, +/- 24 inç toleransta 0.0005 inç'e kadar uzunluk ve genişliklerde üretilebilir.
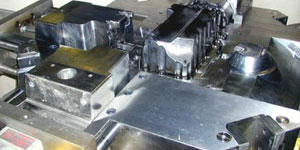
ISO 9001: 2015 sertifikalı döküm magnezyum üreticisi, Yetenekler arasında 200 ton sıcak odaya ve 3000 ton soğuk odaya kadar yüksek basınçlı magnezyum kalıp dökümü, takım tasarımı, cilalama, kalıplama, işleme, toz ve sıvı boyama, CMM özelliklerine sahip tam kalite güvencesi bulunur , montaj, paketleme ve teslimat.
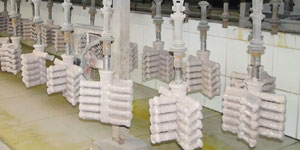
ITAF16949 sertifikalı. Ek Döküm Hizmeti Dahil yatırım dökümleri,kum dökümü,Yerçekimi Döküm, Kayıp Köpük Döküm,Savurma döküm,Vakumlu Döküm,Kalıcı Kalıp Döküm,.Yetenekler arasında EDI, mühendislik yardımı, katı modelleme ve ikincil işleme yer alır.
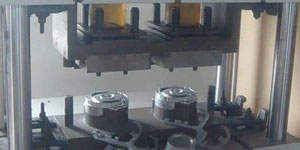
Döküm Endüstrileri Arabalar, Bisikletler, Uçaklar, Müzik aletleri, Deniz Araçları, Optik cihazlar, Sensörler, Modeller, Elektronik cihazlar, Muhafazalar, Saatler, Makineler, Motorlar, Mobilya, Mücevher, Jigler, Telekom, Aydınlatma, Tıbbi cihazlar, Fotoğraf cihazları, Robotlar, Heykeller, Ses ekipmanları, Spor ekipmanları, Aletler, Oyuncaklar ve daha fazlası.
Bundan sonra ne yapmanıza yardımcı olabiliriz?
∇ Ana Sayfaya Git Çin Döküm
→Döküm Parçaları-Ne yaptığımızı öğren.
→ Hakkında İlgili İpuçları Pres Döküm Hizmetleri
By Minghe Döküm Üreticisi |Kategoriler: Faydalı Makaleler |Malzeme Etiketler: Alüminyum Döküm, Çinko Döküm, Magnezyum Döküm, Titanyum Döküm, Paslanmaz Çelik Döküm, Pirinç Döküm,Bronz Döküm,Döküm Videosu,Tarihçe,Alüminyum Döküm |Yorumlar Kapalı